UV Protection and Coatings for Plastics in the Automobile Industry
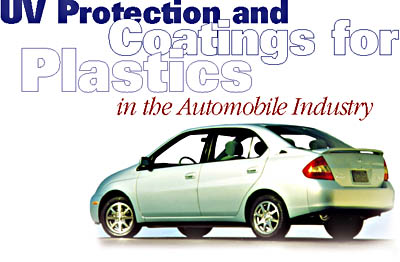
Since Henry Ford launched his famous Model T, the development of automobile and transport engineering has experienced true quantum leaps. Because of the variety of possible forms, safety considerations and the significant weight savings, the automotive industry is increasingly using plastic components. On average, today's car consists of 14% of various types of plastic. The organic material is, however, subject to a natural aging process that makes the addition of stabilizers necessary. Exposure to sunlight accelerates the process. Often, such plastic components are treated with a topcoat. However, due to undesired migration, the concentration of stabilizer in the plastic and coating decreases over time. The plastic, as well as the coating, is then no longer sufficiently protected. This article describes the mechanism of migration and explains possible methods of delaying it.

Plastics
Plastics are found in the car as cable insulation, interior covering, dashboards, tanks or under the hood. Increasingly, auto body components are also being made of plastic. Some of these are uncoated or appear in the same shade as the rest of the auto body. Some pilot projects even describe auto bodies made entirely of plastic.The material itself is subject to a natural aging process, which begins as early as manufacture, due to extreme processing conditions that occur at times. To delay the degradation as long as possible, so-called process and long-term stabilizers are added. If the component is exposed to the elements without protection, degradation is further accelerated. In addition to the compulsory long-term stabilization, the polymer also needs an additional UV-stabilization package.

Coatings
The UV stabilization is an indispensable element of the plastic coating in the automobile exterior. In ideal circumstances, these are multi-layer systems. The coating of plastics begins with the application of a primer, which has a binding effect on the basecoat, that is then applied over the primer. Finally, a clearcoat containing the light stabilizers for UV protection seals the coating system.
This, however, exacerbates the problem of migration1: the organic substrate makes it possible for the stabilizers to migrate into the plastic and also permits the migration of the plastic stabilizers to the top surface of the coating. With a decrease in the concentration of UV protector in the paint surface, the protective function of the coating, by definition, also decreases. Plastic stabilizers migrating upwards from the substrate cause yellowing in the topcoat or, in the worst case, can even lead to complete loss of adhesion.

Polymer Stabilizer Packages
Every stabilizer has a specific temperature range in which it develops its optimum protective effect. For this reason, a mix of different stabilizers is added to the polymers - so-called stabilizer packages. They generally consist of primary and secondary antioxidants, and ensure sufficient protection of the polymer (see Figure 1).The most important primary antioxidants are the sterically hindered phenols. They are suitable as long-term stabilizers in almost all cases. Despite their many benefits, they have one undesirable side effect. As a result of UV radiation and subsequent photolytic degradation, they develop deeply colored quinoid structures which lead to a yellowing of the plastic (see Figure 2).2
As protection against the often high temperatures during further processing, secondary antioxidants such as phosphites, phosphonites or HALS are also used.
Coating Stabilizer Packages
Two groups of stabilizers have been developed for coatings and are suitable for protecting both plastics and the coatings themselves: UV absorbers and sterically hindered amines (also called HALS = Hindered Amine Light Stabilizers).3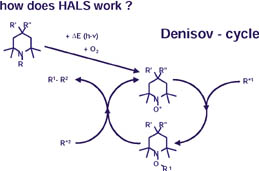
UV Absorbers
Most UV absorbers function according to similar mechanisms. The physical absorption process protects both the deeper sections of the coating and the substrate from the high-energy fractions of sunlight. These are absorbed and lead to isomerization, causing the molecule to transform into an excited structure. When the molecule reverts to its original condition, the absorber releases the energy into the environment as thermal energy. The relevant UV absorbers in coatings include 2-hydroxybenzophenones, oxalanilides, 2-hydroxyphenylbenzotriazoles and 2-hydroxy-phenyltriazines.
According to the Lambert-Beer Law, the absorption of a medium depends, among other things, on the UV-absorber concentration and on the distance traveled within it by the light. The concentration and the thickness of the coating may, therefore, not be permitted to fall short of a certain minimum limit in order to guarantee protection of the substrate through absorption. The deeper the UV ray penetrates the coating, the greater the absorption or the effect of the UV absorber. Due to the very short distance the UV ray is able to travel to the immediate surface of the coating, the protective effect of the UV absorber is at its lowest at this point (see Figure 3).

Sterically Hindered Amines (HALS)
With UV protectors of the hindered amine light stabilizer type, stabilization results from the trapping of the intermediately developed radicals. All UV protectors of this type are based on a single chemical structure: tetramethyl-piperidine. They differ only in terms of the substituents at the nitrogen atom (R) or on the opposite ring side (R' and R'').They operate as UV protectors by combining with oxygen when exposed to light to form stable nitroxide radicals. The latter trap the radicals, which have developed from the polymer through exposure to UV rays. The most important feature of the nitroxide radicals is their regeneration capacity. Thus, a cyclical reaction is possible, which can repeat hundreds of times until the HALS itself has been degraded (see Figure 4). Radical chain reactions, which attack the coating and the substrate, are thus prevented.
HALS, in contrast to UV absorbers, protect chemically rather than physically. Consequently, their effectiveness depends on optimum dispersal in the binding agent. The necessary quantity of HALS is therefore based on the solids content in the binding agent.
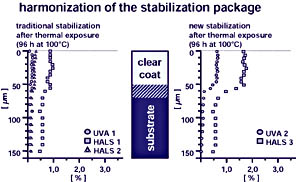
Migration Processes
Migration is the undesired movement of the stabilizers between the coating layers and the substrate. Whether migration proceeds from the upper layer to the substrate or vice-versa -- negative effects occur in both cases. Among other things, the stabilizing properties of the coating may be lost or a degradation of the plastic may occur. The speed of migration depends on a variety of factors, including the temperature, solubility of the additives, concentration differences, the thickness of the coating or the mobility of the additive.2While migration cannot be completely prevented, it can be effectively delayed and controlled by the following.
- Harmonization of plastics and coating stabilizers
- Use of "non-migrating" stabilizers
- Migration barriers
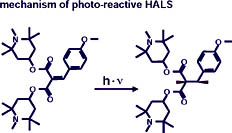
Detection through Microtome Technology
The microtome technique is a modern method of tracing migration. Working from the outside, it separates coatings into thin layers thus permitting a detailed analysis of the protective layers. Depending on the hardness and brittleness of the material to be examined, suitable setting of the microtome permits sections of as little as 2 mm to be cut. In order to obtain intact and usable sections, the plastic samples are generally somewhat thicker. Subsequently the sections, which can be up to 7 x 9 cm, are placed in test tubes, mixed with an extraction agent and left in an ultrasonic bath for 10 hours. Afterwards, the concentration of the additive in each individual layer can be determined by HPLC (UV absorber) or gas-chromatographic means (HALS and UV-absorber).Methods of Reducing Migration
Harmonization of Plastics and Coating StabilizerHALS stabilize both the plastic and the coating. In the protective coating, the HALS operate together with a suitable UV absorber as light stabilizers. In plastics, on the other hand, they are often needed for process stabilization.
Whereas it was common up to now for each manufacturer to use the stabilizer of his choice, the latest studies from Clariant prove the benefit of using identical stabilizers in the protective coating and the plastic. Otherwise the additive concentration in the protective layer drops significantly due to the extremely high level of migration, causing stabilization to become ineffective. The adhesive properties of the coating decrease, the component is subject to rapid discoloration and loss of gloss.
The contrasting results achieved through the use of the same HALS in plastic and protective layer -- the clearcoat -- are shown in Figure 6. Here, too, a migration process occurs under the specified experimental conditions. However, the concentration profile confirms a significantly slower migration process. The use of the same additive therefore leads to a reduced alteration of concentration between plastic and protective layer. The concentration profile presented in Figure 6 is also comparable to the profile in multi-layer systems on a metal substrate. For this reason, greater weathering resistance can also be expected.1
This new process, however, demands close cooperation between the manufacturers of coatings and the suppliers of plastics. This is because the same stabilizers can only be used following consultation. Apart from the increased stability, the laborious process of manufacturing multi-layer systems can be avoided, considerably reducing production costs. However, the process cannot be universally applied. Further points also remain troubling such as the considerable logistic requirements due to the wide spectrum of colors or the realization of metallic shades.
Use of "Non-Migrating" HALS
Various possibilities exist for directly preventing the migration of HALS. Oligomer HALS, for example, are so large that they adhere to the surrounding polymer matrix and migrate very little. A further variant is graftable HALS. These are chemically linked directly to the binding agent and are therefore not capable of any migration. Very special perspectives are offered by the new photo-reactive HALS Sanduvor PR-31.
With this product, the first photo-reactive HALS (see Figure 7) have been developed. The malonic acid derivative not only exhibits the typical functional groups of the HALS, it also contains a UV absorbing system of conjugated double bonds, which also involves an olefinic double bond. The latter is split under UV light, causing the loss of the UV absorbing effect of the molecule. At the same time, the HALS molecule is chemically attached to the binding agent thus preventing migration. The HALS molecule is also fixed in place where the UV rays are greatest: at the upper surface of the coating. With decreasing strength of the UV rays, these HALS are, of course, capable of migrating into the deeper layers of the clearcoat, but can no longer bloom. As soon as Sanduvor PR-31 has migrated toward the surface, it is photochemically attached to the binding agent through the increased UV radiation. Thus the deeper regions of the clear coat have a reservoir effect for the surface and the proportion of HALS molecules fixed in the surface region increases with time. Overall, Sanduvor PR-31 guarantees not only lasting protection in the surface area but also excellent value, particularly with components subject to strong UV exposure.
Migration Barriers
So-called migration barriers block the migration of the additive. Basecoats and primers can have a hindering effect, especially when filled with disc-shaped pigments and extenders. Furthermore, the solubility of additives in the basecoat binder significantly influences the additive concentration in the top clearcoat and, consequently, the migration capacity. But each multi-layer system leads to a different migration speed.
A higher crosslink density of the polymer matrix may contribute to the reduction of the additive migration speed as well. With increased crosslink density, the gaps in the polymer matrix become smaller, holding back larger additives. This variant is, however, of only limited success as excessive crosslink density leads to embrittlement of the coating.
Conclusion
Plastic components are having a determining influence on modern automobile construction and will be a decisive factor in shaping the car of the future due to their manifold advantages. As a result, the development of efficient and cost-cutting coating systems for this special substrate is becoming increasingly important. The most significant finding is that plastic and protective coatings beneficially contain identical stabilizers. The migration process is considerably retarded as a result and the expensive application of a multi-layer system becomes unnecessary. However, close cooperation between plastics supplier and coating manufacturer was highly appreciated.This article was originally presented at the Fourth International Coatings for Plastics Symposium, June 4-6, 2001, in Troy, MI.
For more information on coatings for plastics, contact Gerd Faoro, Pigments and Additives Division, Polymer Additives BL, Boite Postale 149, 68331 Huningue, Cedex, France;
phone 0033-389-89-6172; fax 0033-389-89-6195; e-mail Gerd.Faoro@clariant.com; or Circle Number 132.
References
1 "Distribution of Stabilizers in Multi-Layer-Coatings and Plastic Coatings,"3rd International Coatings for Plastic Symposium, Troy, MI, June 2000.2 "Potential Reasons for Yellowing of Coatings over Plastic Substrates," 4th International Coatings for Plastic Symposium, Troy, MI, June 2000.
3 "Protecting UV-absorbing Clear Coats from Sunburn," Polymers Paint Colour Journal, February 2000.
Looking for a reprint of this article?
From high-res PDFs to custom plaques, order your copy today!