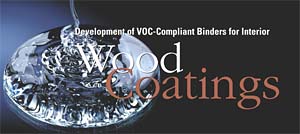

When applying conventional solventborne coating systems on an industrial coating line, organic solvents are released into the earth's atmosphere. To comply with European legislation, these emissions must be reduced by using expensive and complicated technical equipment and techniques such as solvent recovery, post-combustion, etc. Waterborne coatings contain very low quantities of solvents, or none at all. They allow for solvent-emission abatement by approximately 90%, provide a better working environment for the applicators and drastic pollution reduction. Furthermore, the liquid coatings are not flammable, offering increased workshop safety and reduced insurance costs (absence of spontaneous combustion). Finally, equipment can be washed with water instead of organic solvents. The wastewater can be conveniently treated so it poses no threat to the environment.

Crosslinking Technology
Polymer systems can be either crosslinked or non-crosslinked. Non-crosslinking resins contain long, unconnected polymer chains and are easily solvent-soluble. Crosslinked resins have long, attached polymer chains that form a ‘chain-link fence' type network. These systems are only slightly solvent-swellable, and have improved chemical and wear resistance.
There are many types of crosslinking systems for coatings dried at ambient temperature. An example of a two-pack system is Setalux 6520, a waterborne acrylic polyol dispersion with 3.2% OH (calculated on non-volatiles). This product, in combination with water-reducible polyisocyanates, gives coatings having good drying, water resistance and mechanical properties. However, there are some drawbacks associated with the use of isocyanate-based systems. An alternative system that offers the performance of a two-pack system without the use of isocyanates is the waterborne, all-acrylic (AA) system. All the components of the AA system have acrylic backbones. The system is based on an epoxy-functional acrylic dispersion and an amino-functional emulsion with an acrylic backbone. Besides being isocyanate-free, the all-acrylic system does not have the short potlife and foam formation during curing that is associated with waterborne two-component isocyanate systems.
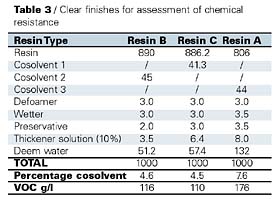
In this paper both types of technologies are investigated for their suitability as furniture finishes. The binders used in this study are shown in Table 1, their characteristics in Table 2. Table 3 contains clear-finish formulation examples.

Film Characterization of Finishes
For the first generation of binder developments (Binders A, B, C), we used Dynamical Mechanical Thermal Analysis (DMTA) to gain insight into the intrinsic properties of the binders. The Tg and crosslink densities of the film were determined by DMTA. The chemical resistance of the furniture finishes was determined using the DIN 68 861.
Tests carried out on simple, glossy, clear-finish formulations show significant improvement in chemical/stain resistance of the clearcoats compared to leading competitor products. With proper formulation and the use of suitable co-binders, the DIN 68 861 1B standard can be achieved as shown in Table 4, along with fast drying, and good initial hardness for scratch- and mar-resistant coatings.


Flooring-Finishing Systems
These binders, in combination with suitable air-drying polyurethanes, are exceptionally suited for flooring applications where a high degree of household chemical resistance, in addition to low wear, are paramount. Table 6 gives details of a flooring system.For the evaluation, three sample panels per system were prepared. Each Beech panel was coated with three layers, each layer averaging 45 microns dry film thickness (Table 7).
No significant differences in chemical resistance (DIN 68 861 1B) were observed with the flooring formulations when compared to our clear furniture formulation. This means that it is easy to blend other binders/materials into the system with no significant loss of performance. In addition, in comparison to the commercial reference, improvements in resistance to some chemicals/stains were noticeable (Table 8).

Novel Development Using Enhanced Crosslinking and Surfactant-Free Technology
Resin E is a new development using a combination of surfactant-free technology and novel crosslinking chemistries to further enhance the crosslink density. This technique gives exceptional film forming, chemical resistance, hardness with low MFT, and therefore significantly lower cosolvent demands. It is well documented that surfactant-free systems offer an additional advantage over surfactant-containing systems. They enable the resin manufacturer to develop binders that come even closer to the performance of conventional solventborne binders. There is no surfactant migration to the coating surface, which can result in a worsening of properties such as chemical resistance and mechanical properties. The environmental impact on the European industry will be twofold. A further reduction of the emission of volatile organic substances is possible since these binders offer high hardness combined with low MFT. A second benefit is that the use of reactive surfactants will have an environmental impact. There will be less leaking of surface-active materials into surface water. Furthermore, the technology does not contain alkyl phenolic moieties, and therefore has no endocrine disrupting potential (Table 9).




Formulation of Furniture Finish
A typical clearcoat formulation is shown in Table 14. The first step is to prepare the clear base as shown in Table 15 (Formulation 1A) with the amino emulsion ‘Resin G'. This clear base can also be used for the preparation of clear matte and pigmented topcoats. It is best to keep the clear base formulations as simple as possible. Several additives are, of course, essential for the preparation of the related paint. The preparation of the clear base can be a critical step, and care must be taken with the selection of the additives and with the order of addition.

Formulation Potlife
In an earlier presentation,6 the potlife was investigated and it was shown that there is only a small increase in viscosity in the first 24 hours. After 72 hours the formulation gelled. However, the gloss levels start to decline after 8 hours and, consequently, a working potlife of 8 hours is recommended for formulations containing hardener.
Conclusions
1. Our 1K furniture binders, which use a combination of gradient morphology, power feed and complementary crosslinking mechanisms, in combination with the correct additives, give interior coatings that meet the demands of the interior wood market with respect to the following:- Low-VOC coatings - less than 55g/l are possible;
- Chemical resistance - meets DIN NORM 68 861 1B, including some more difficult requests such as sweat resistance;
- Good early development of hardness - making these binders suitable for fast applications where the coating has to withstand early sanding and problems caused by stacking or handling;
- Excellent film clarity, low-haze coatings - similar to what is achieved with solventborne systems (commonly termed good "anfeuerung"), are possible with these new binders;
- In combination with commercially available PUR dispersions, one can formulate parquet lacquers that offer a high degree of abrasion resistance.

3. The non-isocyanate WB all-acrylic system can also be formulated at very low VOC (typical figures of 50g/l), thereby offering significant advantages to the manufacturer.

- Mixing of the two components is extremely easy, and can be done by hand.
- The potlife is considerably longer (> 8 hours).
- Resistance and mechanical properties obtained are comparable to NCO 2K systems.

References
1 Mestach, D. Double Liaison, 2000, No 517, 48-54.2 Mestach, D. Polym. Paint Col. J. 2000, Vol 190 No 4431, 28 (2 pp).
3 Akkerman, J.; Hall, R.; Mestach, D; and Vandevoorde, P. Proc. PRA 6th Nurnberg Congress ‘Creative Advances in Coatings Technology' (PRA, Teddington/Vincenz Verlag, Hannover), Nurnberg 2001, Paper 2, 17-32.
4 Hall, R.H.; Mangnus-Verhagen, N.; Weber, M.J.J. Proc. PRA 6th Nurnberg Congress ‘Creative Advances in Coatings Technology' (PRA, Teddington/Vincenz Verlag, Hannover), Nurnberg 2001, Paper 30, 403-16.
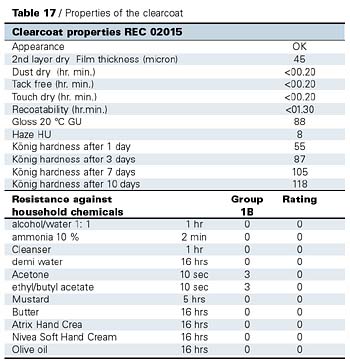
6 Vandevoorde, P.M.; and Brinkman, E. "Isocyanate Free Two Component Waterborne Coatings," Lecture presented at Forum de la Connaissance, November 26-27th 1996, Paris, France.

8 Brinkman, E. "Waterborne Two-Pack Isocyanate-Free Systems for Industrial Coatings," Proceedings 23rd Annual Conference in Organic Coatings, July 7-11th 1997, Athens, Greece.

10 Manning, E.; and Brinkman, E. "All-Acrylic Technology as an Alternative to Isocyanate-Free Polyurethane Systems," Polym. Paint Col. J., 2000, Vol. 190 No. 4426, 21-23.
For more information, contact Derrick Twene, Technical Service Manager, Wood; phone +31.164.276.454; e-mail Derrick. Twene@akzonobelresins.com.
This paper was presented at the 7th Nurnberg Congress, European Coatings Show, April 2003, Nurnberg, Germany.
Report Abusive Comment