Scrub Resistance of Latex Paints
Importance, Dependence on Raw Materials, Formulations, and Quality Characteristics of Architectural Coatings

Wall coatings are subject to erosion caused by scrubbing in passageways, e.g. in staircases, corridors, near doorways where moving people with clothes may cause slight abrasion of the coating, or when trying to remove minor dirt caused by everyday use with, for example, a sponge moistened with detergent. The coating's resistance to erosion caused by scrubbing is called “scrub resistance,” and the ability to scrub with no failure of the coating is called “scrubbability.” This property of latex paint is also required on various types of coatings, such as window frames, which are periodically washed with water and detergents. As a result of such scrubbing, which in the case of wet scrubbability (hence often referred to as wet-scrub resistance), the coating is thinned (thickness reduction as a result of wet abrasion) and a sheen/gloss change appears, revealing deeper layers of the coating, eventually revealing the substrate, known as failure.
FIGURE 1| Coatings after tests according to ASTM D2486 Method B (test coating and reference coating).
Scrub resistance depends on the composition of the coating, which in turn depends on the formulation of the latex paint, including pigment volume concentration (PVC), polymer dispersion and its film-forming properties, coalescing agent and other additives, fillers and their binder requirements, the ratio of PVC to CPVC (critical pigment volume concentration), and whether the coating is matte, semi-gloss, low sheen, or high gloss. The conclusion is that scrub resistance depends basically on all the ingredients of the formulation that combine together to form the paint, and in turn, the coating that is characterized by a specific scrubbability. That is why the process of determining the formulation and selection of raw materials is so important to ensure the appropriate level of scrub resistance, varied in terms of requirements depending on the application of the coating, market habits, and the region of the world in which the scrub resistance requirements and recipe formulation habits are often extremely different.
Morphology of Latex Coatings
Latex coatings are composed of all non-volatile components that remained after the evaporation of volatile components (water, coalescents, other volatile components from additives), and the coalescence of the polymer dispersion particles with other components of the coating (pigments, fillers) and non-evaporating additives, e.g. fungicides, surfactants. Depending on the porosity of the coating, it is filled mostly with Q>1 fillers (PVC>CPVC) or mostly with the binder Q<1 (PVC
Standardized Tests for Determining Scrub Resistance
Scrub resistance is a specific case of abrasion resistance, which usually occurs as wet-scrub resistance and applies to wall paints, mainly for interior and exterior. The principle of the test, regardless of the test method, consists in subjecting the coating obtained in a specific way to wet abrasion called scrub resistance (wet-scrub resistance), in a strictly standardized manner, and measuring the obtained results in a standardized manner in order to ensure adequate repeatability and reproducibility of the test. In the world of latex paints, there are several international standards for performing this test, however, locally many countries have introduced their own test methods over the last 30 years or more, , e.g. PN-C-81517:1992 (Polish standard). But despite the fact that some of themwere local standards, e.g. DIN 53778-2:1983 (German standard) and despite their withdrawal, they are still used not only locally, but also internationally.
In this article, I will focus on the four most important standards that define the scrub resistance test methods for wall latex paints, each of which is complementary and not a typical replacement. The methods referred to in this article are listed in Table 1, along with the dating of versions that have been described (the most current as of November 2023).
TABLE 1| Scrub resistance standards discussed in this article.
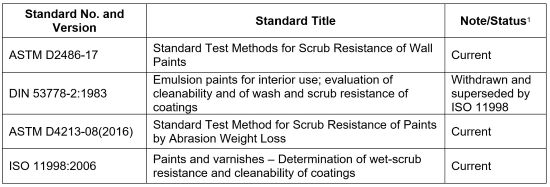
1As of November 2023.
The methods of testing scrub resistance differ from each other in the details of the test, however the principle remains the same. There are also differences in the ways of expressing the result. Basically, the scrub resistance test methods can be divided into two ways of expressing results¾cycles to failure and volumetric coating erosion. These differences come from the scrub pad, which can be non-woven or brush, which in turn can be made of natural or synthetic bristles. This is not the end of the key differences. The scrubbing medium, its aggressiveness, as well as the weight of the handle in which the scrubbing pad or brush is attached, the method of wetting the coating during the test, and the type of wetting medium, all make each of the tests different, not only in terms of the apparatus and parts used for the test, but also in terms of the aggressiveness of the test and therefore its suitability for various types of wall paint. The methods presented in Table 1 are characterized in terms of detailed testing and expression of results. In turn, Table 2 shows the details by which these methods differ from each other.
TABLE 2 | Comparison of different scrub resistance testing standards.
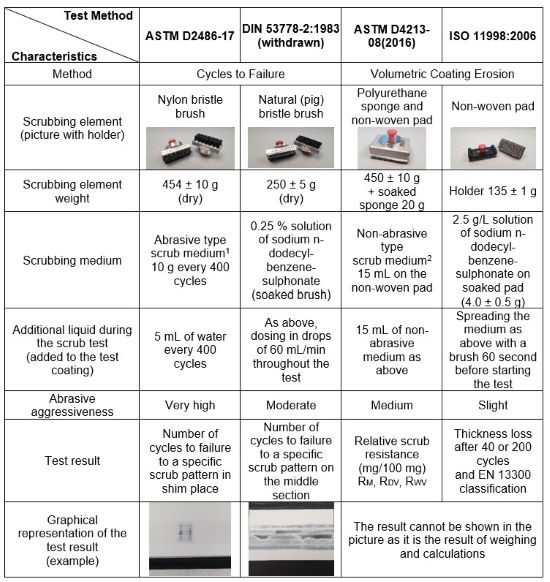
1 Suspension of silica, detergent, acetic acid, trisodium phosphate, ammonium hydroxide, preservative, and hydroxyethyl cellulose in water (e.g. Leneta SC-2 standardized abrasive scrub medium).
2 Suspension of detergent, acetic acid, trisodium phosphate, preservative, and hydroxyethyl cellulose in water (e.g. Leneta SC-1 standardized non-abrasive scrub medium).
Cycles to Failure
One of the most popular ways of expressing scrub resistance is cycles to failure, and the most common test method used worldwide is ASTM D2486.
ASTM D2486
The method of expressing the result as cycles to failure is one of the most popular, and the number-one ASTM D2486 standard is the method of determining scrub resistance, especially for high-quality coatings. This method involves performing a test on a coating obtained with an applicator with a gap of 7 mils, and conditioning it for 7 days in standard conditions of 73.5 °F ± 3.5 °F (23 °C ± 2 °C) and a relative humidity of 50% ± 5%. The coating is then subjected to scrubbing according to the method guidelines. Brushes with nylon bristles are soaked in water overnight before the test, and then 400 pre-scrubbing cycles are performed on the test coating before the final test is performed. This procedure is intended to condition the brushes before the actual scrubbing in order to avoid differences in the repeatability of subsequent scrubbing repetitions on a given day.
The test is performed using a washability apparatus performing 37 cycles per minute of back-and-forth movements, and an abrasive medium is used as the liquid, which additionally increases the severity of the test by abrasion caused not only by the movement of the brushes. During the test, there is a 1/2 inch wide and 10 mil thick shim under the coating, which causes the brush to scrub the area of the coating bulge, thus determining the location of the failure. The test is carried out until the substrate is exposed over the width of the shim and the pattern specified in the standard appears.
FIGURE 2 | ASTM D2486 brushes during subsequent weighing of scrub medium between 400 cycles.
The ASTM D2486 test is used to assess the scrubbing resistance of latex coatings, mainly in the PVC 25%-45% range, during the formulation and selection of raw materials, from binders to additives, in order to demonstrate their influence on the formation of coatings and their scrubbing resistance. This method is also the most popular scrubbability test performed to control the quality of coatings. ASTM D2486 specifies two test methods: A, cycles to failure, which evaluates the coating subjected to scrubbing; and B, percentage scrub resistance, in which a test coating and a reference coating are scrubbed, and the result is expressed as the percentage of scrub resistance of the test paint compared to the reference paint.
A cycles to failure result of 1,400 cycles or more in the ASTM D2486 test method means a very good scrubbability result. Latex coatings based on acrylic polymer latex are rated as very high scrub resistance if their result is approximately 2,000 cycles to failure.
DIN 53778-2
The DIN 53778-2 test method is a kind of historical standard, but still found in technical materials and characteristics of both raw materials in formulations and paint on the market, especially in German-speaking countries. This method is also based on the cycles-to-failure assessment and is dedicated mainly to coatings with slightly higher PVC (usually in the range of 45%-60%), which are tested after 28 days of conditioning in standardized scrubbing conditions using natural bristle brushes (pig bristle).
The difference between this standard and ASTM D2486 is very significant and consists of a different preparation of the brushes, which in the case of the German method are soaked and scrubbed in various stages (called leveling in the standard, including abrading the brush bristles on sandpaper before first use), and the test is carried out using a surfactant solution, in which the brushes are also soaked before the test and dosed onto the coating in drops throughout the test. The surfactant used does not cause additional abrasion, and the brushes are lighter compared to ASTM D2486. Scrubbing is carried out until abrasion is achieved, also defined as the pattern in the standard, but in the case of DIN 53778-2, it is practically along the entire length of the stroke in the rows wiped by the brush bristles.
FIGURE 3 | Apparatus prepared for scrubbing DIN 53778-2 with automatic surfactant feeding.
The DIN 53778-2 standard is officially withdrawn, as is DIN 53778-1, which specifies requirements for classifying the scrub resistance of latex paints in category W (wash resistance) as a minimum of 1,000 cycles to failure and in category S (scrub resistance), requiring a minimum of 5,000 cycles to failure.
Volumetric Coating Erosion
Another way of presenting scrub resistance results is to express the volumetric loss of the coating after scrubbability tests. This method is very popular in Europe to express the coating loss expressed in µm, however, the ASTM standard set also includes such a test method.
ASTM D4213
The ASTM D4213 method is the most extensive scrub resistance test and requires many operations before and during the test. This test involves scrubbing the tested coating and the calibration coating at the same time, and the test result consists of three components administered simultaneously:
- RM—milligrams of calibration film erosion per 100 mg of test film erosion.
- RDV—milligrams of calibration film erosion per 100 μL (displacement volume, that is, volume exclusive of air) of test film erosion.
- RWV—the number of mg of calibration film erosion per 100 μL of equivalent wet paint erosion..
Test coatings are applied to P121-10N panels using automatic drawdown using a 7 mil gap applicator and conditioned for 7 days, as in the case of ASTM D2486. Meanwhile, the solid content and weight per gallon required for calculations are determined and the coatings are trimmed as described in ASTM D4213 before testing. The cut-and-weighed coatings are placed on the scrubbing apparatus tray with the cut calibration coating, which is one of three paints with known scrub resistance, described as Type A, B, and C, where scrub resistance of Type A has been found to be approximately 35% of Type C, and Type C approximately 50% of Type D. These coatings are prepared in the laboratory and conditioned for 6 months before the actual test. This poses something of a challenge to be properly prepared to do it.
The scrubbing element is a holder in which a polyurethane sponge with a specific porosity protrudes about 0.25 in. is placed beyond the skirt, under which there is an abrasive pad of the same size as the sponge surface. The test is performed using a properly prepared abrasive pad with a non-abrasive medium applied, performing a total of 800 cycles, rotating the abrasive pad every 50 cycles for the first 200 cycles, and then every 100 cycles. After testing, the coatings are dried and weighed, and then RM, RDV, and RWV are calculated in relation to the calibration coating.
This method provides extremely extensive data for coatings with known scrub resistance, but requires quite complicated procedures regarding the coating itself and the proficiency in its implementation.
FIGURE 4 | Coating undergoing ASTM D4213 testing with reversing abrasive pad shown.
ISO 11998
European formulation habits regarding latex paints differ from the formulation rules used in the United States. European latex paints have much higher PVC, reaching even over 90% in the case of budget contractor's paints. However, you will typically find paint’s PVC 65%-80%, which makes the ASTM D2486 test method usually too aggressive to show differences between paints, especially in these higher PVC ranges. Therefore, the ISO 11998 method is used to test European paints, the principle of which is to condition the coating for 28 days under standardized scrubbing conditions for 40 or 200 cycles, as well as to determine the dry film density on a separate coating applied to the P121-10N panel (the dry film thickness must ensure no exposure of the substrate after the specified 40 or 200 cycles). The medium used is a surfactant in the form of an aqueous solution that is moistened with the coating and a non-woven pad attached to the holder of the scrubbing apparatus.
FIGURE 5 | Non-woven pad attached to the holder used for ISO 11998 test.
The test result indicated in ISO 11998 is the loss of mass per unit area (g/m2) calculated using the marked dry film density, the loss of coating thickness after a given 40 or 200 cycles, and classified according to EN 13300, which is an extremely important scrub resistance rating for European paint manufacturers.
European Scrub Resistance Classification
The European classification of latex paint parameters for interiors includes classes for basic parameters (gloss, grain size, hiding power), including scrub resistance expressed as thickness loss. This classification is used by all latex paint manufacturers in Europe, as well as in other countries outside the European Union, and is often treated by consumers as an indicator of the durability of the coating. The scrub resistance classification according to EN 13300 is presented in Table 3.
TABLE 3 | EN 13300 European scrub resistance classification.
Case Studies
To better illustrate the use of scrub resistance test methods, several examples of formulations and the impact of various raw materials, as well as formulation modifications for PVC, were prepared, presenting the use of the ASTM D2486 method as the most important scrub resistance testing procedure.
Latex paint formulations contain many raw materials, from latex binders, fillers, pigments, to various additives (dispersants, defoamers, thickeners, etc.). Each of the raw materials present in the formulation affects how resistant the coating is to various factors. A special role here is played by the raw materials responsible for forming the coating, i.e. the binder, coalescents, but also their quantity in the formulation (pigment volume concentration), as well as all types of surfactants. These raw materials may affect the deterioration of scrub resistance if their quantity is incorrect or if they are improperly selected, but with their participation, based on properly prepared case studies, it is possible to build formulations with increased scrub resistance, consciously using certain formulation treatments.
Ladder Comparison of Polymer Latex Dispersions
Polymer dispersions used to formulate latex paints differ in the composition of monomers, surfactants used, viscosity, pH, etc., but above all they differ in their impact on the binding of pigments and fillers in the formulation depending on their quantity. The professional expression of the relationship between pigments, fillers, and film-forming substances is called PVC (pigment volume concentration) and is used to characterize many parameters of prepared formulations. One of them is the dependence of PVC on scrub resistance, expressed in a ladder manner and depending on the type of polymer dispersion and the ingredients it must bind in the formulation. Figure 6 shows the relationship chart prepared for two styrene-acrylic polymer dispersions (A and B) with the same film formation temperature and formulations using the same amount and the same type of pigment in the form of titanium dioxide and calcium carbonate on the non-volatile parts of the binder for the characterization binding capacity for PVC in the range of 30%-80%.
FIGURE 6 | Ladder dependence of scrub resistance on PVC for two polymer dispersions.
As you can see in the chart using the ASTM D2486 test method, you can see the differences between the polymer dispersions used and the relationship between their scrub resistances, depending on PVC. It is also visible that in the case of high PVC (80%) the difference between polymer dispersions is invisible, although in the case of lower PVC, the differences they introduce in the quality of the result are clearly visible. This is why for high PVC ranges the test method is not recommended for use, as mentioned earlier.
Dispersing Agents
Dispersing additives are necessary to achieve the separation of pigment and filler particles and their stabilization, and are added at the grinding stage in the Cowles dissolver during mill-base production. Investigating to find the dosage that provides the lowest mill-base viscosity is the first step in dispersant selection. Determining this dose must also be correlated with its impact on the subsequent parameters of the paint and coatings, because the surfactant in the coating may affect its resistance to scrubbing. To obtain maximum performance, the dispersant dose can also be used to adjust scrubbability, as shown in Figure 7 on the example of the Darvan 7-N dispersant additive in a latex paint formulation based on Acronal ECO 6270 with a standard system of calcium carbonate fillers and titanium dioxide pigment. The presented graph clearly shows the distribution of the tendency to achieve the highest scrub resistance tested using the ASTM D2486 procedure.
FIGURE 7 | Scrub resistance depends on the amount of dispersant in the formulation.
Polymer Dispersions vs. Coalescing Agents
Figure 8 shows a comparison of scrub resistance made for a European latex paint formulation, in accordance with ISO 11998, and a presentation of the results with an indication of the various classes obtained according to EN 13300. The formulation was used to prepare paints using two styrene-acrylic polymer dispersions (marked as Latex A and Latex B) with similar MFFT (minimum film-forming temperature), to which various coalescents were added (TMPDMIB, myrifilm, DPnB glycol ether, and butyldiglycol) in doses ensuring forming film at approximately 0 °C (32 °F).
FIGURE 8 | Results of application studies of coalescents in various polymer dispersions.
The obtained scrub resistance results presented in Figure 8 show how much the obtained scrub resistance classes can be differentiated using coalescents, where for the same polymer dispersion a significantly better classification can be obtained compared to EN 13300. The presented case studies show that adjustment results can be consciously performed using appropriately selected coalescents, even for a seemingly inferior polymer dispersion.
Summary
In the methods of testing the scrub resistance of coatings, the most important are their appropriate selection, test performance, and interpretation of the results. You can often hear that scrub resistance is a parameter indicating whether the coating can be scrubbed with a brush or whether stains can be removed. There is some truth in this first part, because these are tests of resistance to wet abrasion and, in a quite specific way, unlike the typical abrasion tested with the Taber apparatus. On the other hand, good scrub resistance does not mean that the coating is stain resistant and easy to clean, because other methods are used for this assessment, and obtaining a high scrub resistance result using formulation operations and raw materials is completely different from designing easy-to-clean paint.
When it comes to test execution, it is very important to follow all the guidelines set out in the test methods to ensure reproducibility, and that the test is comparable. The reliability of scrub resistance tests is often very questionable due to failure to comply with the test conditions, use of low-quality consumables, lack of compatibility of the equipment, as well as the conditions in which the tests are carried out (drawdown method, temperature and humidity during sample conditioning, test execution).
And finally, when interpreting the results, there can be problems assessing whether a given result is really good. Are the cycles to failure or thickness-loss values actually good scrub resistance results, and what does this means in practice? The results of different paints cannot be compared between test methods, because 1,300 cycles to failure according to ASTM D2486 means something completely different than 2,000 cycles to failure according to DIN 53778-2.
I hope that this guide to scrub resistance test methods will be a kind of “knowledge in a nutshell”, and will contribute to building greater awareness of the main scrub resistance testing methods used by the paint industry around the world, the differences between them, and their importance and necessity. I also hope it will encourage formulators to perform tests correctly to ensure the reliability of the results, not only in quality control, but above all in the selection of raw materials for high-quality latex paint formulations.
Looking for a reprint of this article?
From high-res PDFs to custom plaques, order your copy today!