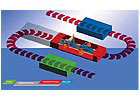
Figure 1. The new integrated technology can reduce the overall length of painting lines, the number of process steps involved and the cycle times.
Automotive coatings fall within an extremely wide range of specifications set by automobile manufacturers. To meet the high surface finishing standards demanded by the automotive industry, coatings carefully matched for compatibility are applied in several layers. Although every automotive manufacturer has different materials specifications, the finshing lines in which cathodic electrocoats, color layers and clearcoats are applied to vehicle bodies have become longer and increasingly complex. From the starting point, where bodies-in-white enter the painting process, to the end where the painted bodies enter the final assembly stage, the painting line can be more than a mile long. Nevertheless, having delivered successful results for years, each of the steps in the traditional process is now considered firmly established. The disadvantage of this process, however, is the high cost required to achieve maximum processing reliability, along with all the required materials and quality characteristics.
Searching for a more ecologically sustainable and cost-efficient solution, researchers at BASF Coatings asked whether the traditional coating process, proven in millions of applications, could be improved. Next, they asked if it was possible to create an innovative system that offers significant cost-cutting and ecological benefits, and can meet the constantly tightening volatile organic compound (VOC) emission standards around the world. The answer was “yes.” A new system technology developed through these efforts can streamline automotive production line coating - in particular, the overall length of painting lines, the number of process steps involved and the cycle times (see Figure 1). The technology eliminates an entire coating layer and yet can be seamlessly integrated into existing plants.
Reducing Costs and Emissions
Early attempts at paint line optimization sought to streamline the standard process in general. The sequence of the individual process steps was analyzed. The basic premises of the process chain, and their variations among automobile manufacturers, were closely studied. System-specific feasibility analyses and process studies led specialists to take a hard look at the primer stage as an area in which significant savings could be achieved.One problem is that the electrocoat (e-coat) that underlies the primer layer is light-sensitive. In conventional paint systems, the unique structure of the primer protects the e-coat by absorbing any remaining ultraviolet (UV) light that penetrates through the clearcoat and the basecoat. Eliminating or changing the primer allows this residual UV light to attack the e-coat and impair adhesion, causing the paint finish or the e-coat film to separate partially from the substrate. In field tests and laboratory simulations of three- to four-year weathering, this loss of adhesion occurred over large areas.
Nevertheless, eliminating the primer remained a promising approach to reducing costs in the painting process. The knowledge gained in previous tests and studies, and the simple question “what does the primer actually do,” led researchers to the idea of cutting out the primer and the process steps needed to apply it, while maintaining its critical functionality. To retain this functionality, the properties of the primer had to be integrated into the other components of the paint system. The result was a new integrated process technology that can be incorporated into existing lines.
Eliminating the primer not only eliminates expensive processes and system technology, but it also eliminates related solvent emissions. As a result, the new technology can make a significant contribution to meeting the more stringent requirements of the future.
Integrating the Coating Steps
Primers are traditionally applied by spraying. They even out irregularities and offer additional protection from corrosion and stone chips. Primers are also highly efficient in protecting the e-coat from the effects of UV radiation. Their ability to fill in irregularities, as well as their sandability, is an important property. The color of a primer is also important for the basecoat and clearcoat layers that go over it. Properly matched primers allow the subsequent basecoats to be thinner. Because of their multiple functions, the formulation of primers is an expensive and demanding task.In general, the application of primers begins with a manual and/or automated cleaning process. Then the primer is applied by means of electrostatically assisted high-rotation “bells” and robots equipped with nozzles that atomize the paint pneumatically. When waterborne or solventborne primers are used, the vehicle body moves to the flash-off zone and the baking oven after leaving the paint booth. After leaving the oven, the vehicle passes through the inspection, sanding and correction zones, and any necessary reworking is performed. The surface is then cleaned again, and the body enters the topcoat application area. With the new integrated system, the current practice of finesse sanding and the quality inspection stage are eliminated. In addition, the so-called “conveyor accumulator,” where vehicles await the next step after priming, is no longer needed.
A complete profitability analysis of the primer stage, then, must cover not only the application process, but also all the booth cleaning work that is required in a primer application booth. The frequency of booth cleaning, as well as the cost of the recovery of the overspray from the booth water is a function of the transfer efficiency of the application process - i.e., the ratio of sprayed product that ends up on the body to the amount that ends up as overspray. Seen as a whole, the primer application process generates a substantial share of costs.
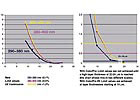
Figure 2. In combination, the two advanced basecoat layers perform all the functions normally associated with primers, from ensuring protection against stone chipping to providing a base for an excellent overall finish.
Retaining UV Protection
As already noted, protecting the e-coat from the damaging effects of UV radiation is essential. Because of its high energy content, UV radiation is able to attack macromolecular materials and coatings through the formation of “free radicals,” leading to adhesion failure and embrittlement. Normally, such damage does not occur in the e-coat unless the high-energy radiation is able to penetrate the overlying layers. Therefore, if the primer is to be eliminated, the other layers applied over the e-coat must absorb the UV light.Researchers decided to pursue a system strategy with the new technology. This decision was based on previous experience with coordinated combinations of light stabilizers in metallic paints (involving durability, color stability, gloss retention and resistance to cracking for more than 10 years).
Transferring the UV absorption function to the clearcoat proved to be possible only to a limited extent because, beginning at a specific level in the nano range, the clearcoat loses its transparency and colorless properties and takes on an undesirable green or yellow cast. For this reason, an approach using two advanced, water-based basecoats as a system seemed to make the most sense. In combination, the two basecoat layers perform all the functions normally associated with primers, from ensuring protection against stone chipping to providing a base for an excellent overall finish (see Figure 2).
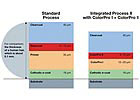
Figure 3. In the new integrated system, the primer is eliminated. Then, in place of the traditional basecoat, one layer of advanced basecoat (which absorbs UV radiation) is applied in the first step, and a second layer of advanced basecoat is applied in a second step.
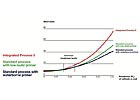
Figure 4. The new technology covers substrate roughness better than conventional processes.
Advantages of the Integrated Technology
The new technology enables the elimination of the entire primer application section of a coating line - along with the associated cleaning, sanding, dust extraction, water treatment, waste disposal and pre- and post-treatment operations - while retaining all of the primer’s functions, including absorbing UV radiation, covering sanding marks and substrate textures (see Figure 4), preventing delamination after aging and stone chips (see Figure 5), and preventing other damage from reaching the substrate. The result is a much shorter coating line. For example, with the new technology, the length of the conveyor line can be reduced by 17%. The new technology also offers cost savings over the conventional process by providing a high first-through capability and high efficiency. Further, the technology permits the same paint formulation for OEM manufacturers and add-on parts manufacturers, delivers a finish nearly identical to that of conventionally applied coatings, and allows unrestricted repairability.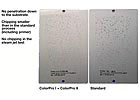
Figure 5. The new technology provides better protection against stone chips compared to conventional processes.
The system can be applied with existing electrostatic equipment and, in general, is fully compatible with two-component clearcoats.
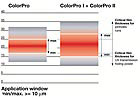
Figure 6. The system consisting of the two advanced basecoats can be varied for optimum performance for any given set of requirements.
Continuing Development
Extensive studies involving UV exposure of automotive coatings in different climates and over varying periods of time revealed major differences among colors in their ability to absorb UV radiation. Dark colors are inherently UV-absorbing, but many currently popular colors - in particular, silver - allow varying amounts of UV radiation to pass through the coating. The advanced basecoat system was matched in such a way that, for some colors, it is now possible to achieve UV protection with a single coat of basecoat - in other words, with only one layer that combines the properties of both advanced basecoats. With more difficult colors, however, maximum functionality and reliability still requires both system components in combination. These variations can only be determined through extensive laboratory tests, climatic and aging simulations, and application tests - all of which have to be carried out for every color.The system consisting of the two advanced basecoats can be varied for optimum performance for any given set of requirements (see Figure 6). Researchers continue to investigate system-based approaches to deliver further improvements in automotive finishes. The latest results from system modifications show that the brief infrared flash time between the two advanced basecoat applications can be eliminated, and that the combination of the advanced basecoats is only necessary for certain colors. Among future objectives is the adjustment of all coating components, from electrocoats to clearcoats, to create a fully integrated system encompassing the entire paint process. In the meantime, however, any coatings currently on the market can be used with the components in the new integrated technology.
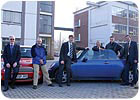
BASF Coatings and BMW Group employees worked together closely to realize the project at the MINI plant in Oxford, UK. The BASF team included (from left): Michael Richert (material development), Ralf Kebschull (applications specialist), Dr. Jorge Wellmann (launch leader), Dr. Achim Gast (BMW Group account manager), Paul Kelly (technical service Oxford plant), and Kevin Hayes (BMW Group UK account manager).
Through these advances, the shortening of the application line, cost savings and a general simplification of the painting process can now be realized in other automotive facilities. In addition, with the reduction in VOCs, the new technology demonstrates that eco-efficiency can be achieved in automotive paint operations without any negative impact on manufacturing technology, quality or design freedom.
Report Abusive Comment