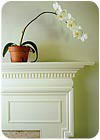
Medium-density fiber-board (MDF) is composed of selected wood fibers pressed together with a combination of resins and adhesives to form compact, dense and homogenous panels. Despite certain disadvantages - including density differences between the heart and surface of the board, fibers present after routing, inconsistencies between boards and manufacturers, lower strength than natural wood and limits to board thickness - MDF is extremely versatile, adaptable and flexible in many applications. It can also be designed, routed, cut and perforated in any direction, shape or form. For these reasons, it is often used as a substitute for solid wood panels in the furniture industry. Design options in the MDF finishing industry are expected to expand even further, while introducing significant cost, environmental and process benefits.
Finishing professionals who work with MDF have traditionally relied almost exclusively on liquid paint processes. However, many conventional liquid paint processes face drawbacks such as volatile organic compound (VOC) emissions and expensive waste treatment; a significant investment in time, energy, labor and space for drying or curing and then sanding multiple liquid coats at each stage; and wasted product lost to the spray cabinet, down the drain and to the environment.
An alternative finish came from the metal finishing industry, which long ago discovered that powder coatings provide significant process and environmental benefits. These benefits include zero VOC emissions and, with today’s advanced powders and processes, the ability to coat complex 3D shapes and heat-sensitive substrates.
Powder Coating Advantages
Undoubtedly, the transition to powder coatings requires some outlay in new equipment, along with a new approach to finishing. However, the technology’s many advantages can far outweigh the costs and efforts of the transition. These advantages include:- Environment: Powder coatings contain none of the VOC pollutants found in liquid paints. Additionally, the recycling capabilities of powder coatings in use provide recovery values in excess of >95%; these capabilities also reduce waste treatment costs.
- Versatility: Although less resistant than polyvinyl chloride (PVC)/MDF laminate composites, powder coatings, unlike laminates, can be used on edges, borders, indents and odd-shaped panels. Powder coatings can also be used to encapsulate panels - an application that is impossible with plastic laminates.
- Productivity: One-pass application using a fully automated, continuous process is possible, compared with the three to six passes necessary for liquid paints. By eliminating several coating passes, manufacturers save on the labor and production costs of spraying, inter-coat sanding, drying and curing, while reducing the time required for the entire coating cycle from hours or days to minutes. This is particularly true for applications that use vertical processes, which allow simultaneous application to both sides of a panel.
- Application costs: Powder coatings cost about the same as plastic laminate processes but less than liquid paint processes due to the ease of automation of application processes, including increased productivity, reduced labor and reduced waste treatment costs.
- Resistance: In just one pass, a 2.8 to 4.5 mils thick coating is achieved that protects the moisture-sensitive MDF substrate. Powder coatings are typically more flexible than liquid paints, and are also more abrasion, chemical and corrosion resistant.
Like liquid paints, powder coatings come in a wide range of colors and finishes. Unlike PVC sheets, powder coatings can be purchased in small lots to allow for design flexibility.
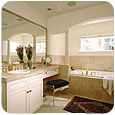
Powder coatings manufacturers have developed MDF-specific powder coatings that offer low-melt-point and high-performance finishes.
Meeting the Challenges of the MDF Market
Over a number of years, innovative advances in powder coatings technology have been developed through close working relationships with MDF manufacturers and processing equipment suppliers. These advances have resulted in a range of products, services and solutions that allow the MDF finishing industry to choose from a variety of powder coating technologies and to develop new products for the future.For the powder to electrostatically coat the substrate evenly, the MDF board must be conductive - simple with metal and conductive substrates, but not so with fiberboard and other non-metallic substrates. The other challenge is that conventional powders have to be melted at temperatures that threaten to damage the MDF substrate’s integrity.
Recognizing the benefits that powder coatings could bring to the MDF industry, MDF manufacturers have identified high-performance wood fibers, additives and resins, allowing them to manufacture heat-resistant MDF products that are sufficiently conductive for the electrostatic spray process. Powder coatings manufacturers have likewise developed MDF-specific powder coatings that offer low-melt-point and high-performance finishes.
Preparing MDF Prior to Powder Coating
The preparation of MDF prior to the application of the powder coating finish is simple. First, the MDF panels are sanded; sometimes they are also pretreated, as for liquid paints. The panels are then preheated for 5-15 minutes to encourage the moisture content to migrate to the surface, which makes the MDF sufficiently conductive to attract and hold the electrostatically charged powder coating particles. Preheating also ensures outgassing of elements that would cause problems during coating.The heated panels are then powder coated using a one-pass application, after which they are heated to melt the particles into a continuous coating that physically “locks in” to the substrate, thereby ensuring excellent adhesion and durability. The subsequent curing and polymerization of the coating depends on the type of coating used. Thermocure materials polymerize at relatively low temperatures using convection heat, infrared radiation or, ideally, a combination of the two. Lower-melt-point products are available that polymerize through exposure to UV light.
With the right substrate preparation and today’s advanced powder coating materials, finishing professionals working with MDF can use powder coatings to optimize their processes and products.
Report Abusive Comment