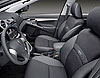
Two-component (2K) polyurethane (PUR) soft-touch coatings have been used to coat plastics in the automotive industry for over a decade. Due to the inherent traits of polyurethanes, the coating formulations exhibit high scratch and abrasion resistance while maintaining low gloss. VOC regulations have guided a shift in chemistry for soft-touch coatings toward waterborne. Soft-touch coatings are now obtainable with low VOC, resulting in minimal fogging of the automobile windshield.
In recent years, soft-touch coatings have been plagued by the concept of cream resistance. Research has shown that hand creams and sun tan lotions at elevated temperatures can not only soften the coating but also migrate through the coating and into the plastic, causing adhesion loss at the coating to plastic interface. With ever-changing automotive and general industrial product specifications, a need still exists to improve the adhesion, resistance and haptic (soft feeling) properties of soft-touch coatings for plastics.
Introduction
The use of plastic has grown exponentially over the past decade. The positives to using plastic as a substrate are that it has low cost, durability and light weight. Because of these positives, plastic is used in a wide variety of applications ranging from automobiles to children’s toys. The negatives to using plastic are that it yellows after long-term weathering; can easily be scratched and damaged by chemicals; and the cold, smooth surface does not invoke a sense of luxury. These points have motivated raw material suppliers and coating manufacturers to invent products that not only protect the plastic surface but also improve the image of plastics by giving it a soft, velvety feel. These coatings have been generally branded with the term soft-touch coatings.One of the biggest markets to date utilizing soft-touch coatings is the automotive industry. Automotive companies have been applying soft-touch coatings to car interiors since the early 1990s. Therefore, specifications for interior coatings are well known in the coatings industry and are often used as benchmarking tools. Automakers are continually looking for coatings that exhibit great appearance, excellent resistance properties, rapid cure, ease of application, lower cost and are environmentally friendly. A goal of continuous improvement for the automaker translates into harder-to-fulfill specifications for the coatings manufacturer.
First-generation soft-feel coatings were solventborne, which yielded a very soft feel and good chemical resistance. One of the biggest drawbacks to solventborne systems is the VOC level. Governmental regulations regarding the allowable amount of VOCs used at plant sites continue to be more stringent. These requirements have pushed coaters to search for more environmentally friendly technologies. Therefore, the coatings industry has seen soft-touch coatings shift toward 2K waterborne chemistry, utilizing polyurethane dispersions (PUDs).
By utilizing waterborne two-component polyurethane resins, the formulator can achieve a variety of softness and resistance levels. A typical waterborne soft touch formulation consists of a OH-functional PUR dispersion, a non-functional polyurethane dispersion, and a water-dispersible isocyanate. Choosing the best combination of resins to achieve the most highly resistant and non-yellowing coating that still maintains the softest feel has proven to be a very arduous task. Complexity surrounding the optimum formulation is further heightened by ever more challenging product specifications.
Bayer MaterialScience has been working successfully on significantly improving the performance of water-dispersible resins for soft-feel coatings. This work explores improvements made to these resins with the goal of achieving improved adhesion resistance, haptic and application properties. It was found that choosing a particular functional and non-functional polyol combination is important when trying to improve properties such as thermal yellowing, hydrolytic stability and cream resistance.
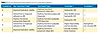
Materials and Methods
The experimental work was divided into two segments. The first segment evaluated the effects of resin choice on hydrolytic stability, yellowing resistance and cream resistance.For hydrolytic stability testing, specimens were subjected to an environment set at 90 °C with 90% humidity. The cross-hatch adhesion and pencil hardness testing were conducted immediately following the test, at 72 hours, and at 240 hours. For yellowing resistance testing, films were aged for 72 hours at 90 °C and for 24 hours at 120 °C.
The second experimental segment utilized results of segment one to devise a matrix. The matrix consisted of different functional polyols, non-functional dispersions and isocyanates at different blend amounts. These formulations were evaluated for suntan lotion/DEET resistance, perspiration resistance and grease staining resistance. This segment discusses five formulations that performed the best (Table 1).
Commercial additives used were: BYK® 346 (BYK-Chemie) for flow and wetting; Disperbyk® 191 (BYK-Chemie) for pigment wetting utilized in generated pigment pastes; Tego® Foamex 805 (Evonik Industries) used as a defoamer; Bayferrox 318M (Lanxess) used in black pigment paste; and OK 412 (Degussa) silica used in pigment paste to generate soft feel. Butyl carbitol, Proglyde DMM, n-butyl acetate and mineral spirits were solvents utilized in the formulations.
Coatings were applied to a polycarbonate/acrylonitrile butadiene (PC/ABS) blended substrate. The coated panels were cured by flashing off the water and solvents at room temperature for 20 minutes and then baking for 40 minutes at 80 °C. The panels were aged for two weeks at room temperature before any testing was undertaken. The aging is to ensure that final film properties are achieved.
Cream resistance properties for soft-touch coatings were evaluated using a test method that involved combining ingredients from suntan lotion and insect repellent. The solution was applied to a coated panel, baked for 1 hour at 80 °C, and then evaluated for visual and scratch assessment. Perspiration resistance was tested by applying synthetic perspiration to a coated panel, baked at 80 °C for 24 hours, and then evaluated for adhesion, scratch and visual assessment. Grease staining resistance was tested by applying beef tallow and an alcohol-based hair dressing product separately to a coated panel, baked at 80 °C for one week, and then evaluated for adhesion and dry-rub testing.

Discussion and Results
A soft-touch coating formulation tends to get its haptic properties from the combination of a soft binder and small particles in the micrometer range such as special matting agents. Additionally, it is possible to use additives like wax or silicone to achieve a certain surface slip.1 Waterborne soft-touch coatings are achieved by combining flexible polyurethane dispersions of high molecular weight with flexible hydroxyfunctional prepolymers and crosslinking them with flexible, water-dispersible polyisocyanates. In the early days of soft-touch coatings, the specifications for chemical resistance were relatively lenient, so it was easy for the coatings formulator to meet the specifications. Formulators then discovered that various creams, especially suntan lotions, caused the coating to soften and scratch off. Studies have confirmed that the failure is due to ingredients in the creams softening the film, penetrating through the coating and attacking the plastic substrate, resulting in adhesion loss.2With the soft-touch coating failure causing dismay among consumers, automakers increased the specification requirements. The next generation of soft-touch coatings was designed to increase the barrier resistance of the creams while maintaining a soft feel. In order to achieve increased barrier resistance, the formulator was forced to choose harder, less-flexible polyols. Coaters had a hard time selling these new soft-touch coatings to the automakers because altering the soft feel coating to pass the more stringent auto specifications caused the coating to feel less soft. Over time, automakers realized that they would have to become more tolerant of the new feel for the coatings to meet their requirements. Original equipment manufacturers (OEMs) continue to try and achieve ever-increasing paint chemical resistance specifications while maintaining the softest feel possible.
The goal for the described work was broken into two segments. The first segment was to identify functional and non-functional polyols that resulted in formulations with improved hydrolytic stability, yellowing resistance and cream resistance. The second segment goal was to utilize information learned in segment one to devise a matrix of formulation combinations to achieve the formulation with the best suntan lotion/insect repellant resistance, perspiration resistance, and grease staining resistance while maintaining the softest feel.
Segment One
The first testing round was completed to see if improvements made to the non-functional polyurethane dispersions and polyol dispersions used in soft-touch formulations would result in improved hydrolytic stability, yellowing resistance and cream resistance.

The trend of non-functional dispersions utilized in Figure 1 and Figure 2 was from soft to hard. As the hardness level of the non-functional polyol rose, the formulation exhibited higher hydrolytic stability. The formulation containing the solvent-free anionic dispersion is considered to be the first-generation flexible non-functional polyol for two-component waterborne formulations. This formulation demonstrated a significant pencil hardness loss and a small degree of adhesion loss. The second generation utilized the improved hydrolytic stability formulation, which showed much improvement for pencil hardness and adhesion. However, this formulation was not able to pass more recent auto specifications that combine suntan lotion and DEET resistance. A need still existed for further improved hydrolytic stability. The bottom four products listed in both Figure 1 and Figure 2 are the new and improved products for hydrolytic stability. All four products demonstrated higher degrees of hydrolytic resistance when compared to the first two products. However, the formulation containing the product labeled improved haptics and scratch resistance exhibited as good or better adhesion and pencil hardness that continued to improve over time.




Utilizing information obtained in Segment One, several combinations of functional polyols, non-functional PUDs and water-dispersible isocyanates were evaluated. The results of the evaluation can be found in Table 2.
Formulations 1A-1E passed the perspiration resistance test. Formulation 1B performed the best for grease staining resistance, while Formulations 1A, 1C and 1D passed the test but did not perform as good as Formulation 1B.
None of the tested formulations passed the sunscreen/insect repellant resistance test. However, formulations 1B and 1D were very close to passing. Using a five-finger scratch tester loaded with an 8.5 N load, the hemispherical tip caused only a very slight indentation in Formulation 1B and slight indentation in Formulation 1D.
Conclusion
Solventborne, two-component soft-touch coatings have long been used in the automotive and general industrial markets. However, governmental regulations have forced companies to lower their VOC output at the plant sites, and trends show that the allowable levels will continue to decrease. Furthermore, car manufacturers want to lower their overall interior emissions. Many regions of the world are responding to these regulations by switching their soft-touch coating chemistry to waterborne formulations.The coatings industry tends to use automotive specifications to benchmark the quality of the coatings. Early generations of soft-touch two-component waterborne coatings were able to meet automotive specifications for resistance properties and maintain a soft feel. As the specifications became more difficult, the formulators were forced to incorporate harder polyols into the formulation causing the resultant film to be less soft. The automotive market continues to search for a soft-touch formulation that meets ever more stringent requirements while maintaining a soft feel. In response to the search, new polyol and non-functional polyurethane dispersions with improved overall resistance and haptic properties have recently been developed by BayerMaterial Science.
Choosing the proper combination of functional and non-functional dispersions, coupled with the right polyisocyanate, can yield a formulation that is more hydrolytically stable, more cream resistant and exhibits reduced thermal yellowing. Two formulations performed the best for suntan lotion/insect repellant, perspiration, and grease staining resistance. Formulation 1B was designated as the formula that performed the best overall. The feel of Formulation 1B was not the typical grabby, velvety soft feel. It displayed more of a smoother, suede soft feel.
The hardest automotive specification resistance test to pass is the suntan/insect repellent test. Even though Formulations 1B and 1D exhibited minor changes after testing, the results were very encouraging warranting further evaluation of these formulations.
Acknowledgements
Contributions by Uwe Klippert, Dorris Grillo, and John Zern.For more information see www.bayermaterialscience.com.
This paper was presented at the 11th Annual International Coatings for Plastics Symposium, April 2008, Chicago, IL.
Report Abusive Comment