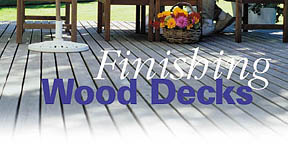
For optimal long-term performance, a wood deck should be maintained with a finish after construction. The horizontal surface, foot traffic, pooling of water, and full exposure to sun and rain make deck finishing more demanding than other wood finishing (e.g., exterior walls and interior floors). A full range of both penetrating and film-forming finishes are available, but the penetrating finishes provide better overall performance and provide easier refinishing.1
The primary function of any wood finish is to protect the wood surface from natural weathering processes (sunlight and water), and to help maintain its appearance. How well the finish accomplishes this function depends on how the finish was formulated, particularly the type and amount of polymer (resin or binder), pigment (including extenders), solvent system, and additives used. Of these components, the type and amount of polymer and pigment most directly affect the mechanical properties and durability of the finish. Other factors that affect the durability of a finish include application technique, time between refinishing, extent to which the surface is sheltered from the weather, and local climate conditions.
Available Finishes - Penetrating Finishes
The advantage of a penetrating finish over one that forms a film is that the wood can breathe, and the finish cannot flake, crack or peel. Such treatments reduce water absorption, and retard the growth of decay and staining microorganisms. Penetrating finishes can be used as a pretreatment for other finishes or as a natural finish for wood. There are three types of penetrating finish: water repellents, water-repellent preservatives and solventborne semi-transparent stains.Water Repellent and Water-Repellent Preservatives
The difference between a water repellent (WR) and a water-repellent preservative (WRP) is the inclusion of a mildewcide in the WRP. Mildewcides inhibit mildew growth on the surface, and provide moderate protection against decay in aboveground use. The WRPs are not intended for use in wood that is in contact with the ground and should not be confused with the preservatives used to pressure treat wood. The WRPs provide short-term aboveground protection against decay for untreated wood, and for sections of the wood that either did not take the preservative treatment (heartwood) or for the interior of large cross-sections that were exposed by cutting or drilling. The addition of the mildewcide also prevents mold and mildew growth on wood treated with waterborne preservatives, such as chromated copper arsenate (CCA). Wood treated with CCA does not resist mildew fungi. The WR and WRP finishes contain a water repellent, such as wax, and a binder, but do not contain pigments. The binder, which amounts to 10–20% of the formulation, consists of drying oils (linseed or tung oil) or a varnish binder. These oils or varnishes penetrate the wood surface and cure to partially seal the wood surface. They also help bind the mildewcide and make the wood surface water repellant. The WRPs that are formulated with nondrying oils that act as solvents (such as paraffin oil) are also available. These oils penetrate the wood, but do not dry. They protect the wood from degradation and mildew attack, as do other types of WRPs. Because the oils do not dry, the deck surface may remain oily until the finish absorbs. This usually takes several days, but depends on the application rate and porosity of the wood.
Penetrating finishes are extremely effective in stopping the adsorption of liquid water, thereby decreasing dimensional changes in the wood. Less dimensional change results in decreased splitting, cracking, warping, and twisting, and less stress on fasteners; therefore, less nail pull-out. These finishes enhance the appearance and service life of both naturally decay-resistant wood species and species pressure treated with wood preservatives.
Several commercial wood treatments are using a WR treatment combined with CCA treatment for 5/4 radial-edged decking. This lumber is marketed under brand names such as Ultrawood, Wolman Extra, MELCO and Weathershield. With this dual treatment, wood is more resistant to weathering. Although the WR should thoroughly penetrate and saturate the wood, it is still advisable to treat the ends that are cut during construction with a WRP. Of the treated wood currently available, these treatments should improve the wood characteristics and extend the product’s service life, particularly with sustained maintenance using a WRP.
Semi-Transparent Stains
When pigments are added to WRP solutions or to similar transparent wood finishes, the mixture is classified as a semi-transparent stain. Addition of pigment provides color and greatly increases the durability of the finish compared with that of the WRP. Semi-transparent stains permit much of the wood grain to show through. The solventborne semi-transparent stains penetrate into the wood without forming a continuous layer and, consequently, will not blister or peel even if excessive moisture enters the wood. The pigment protects the wood surface from sunlight, thus increasing service life. The binder in the solventborne oil-based, semi-transparent stain absorbs into the wood surface, just as it does with the WRP, and there is no film formation. The durability of a stain system is a function of its pigment volume concentration, resin type and content, preservative, water repellent, wood species and the surface characteristics and quality of material applied to the wood surface. If the decking material was given a factory-applied WR or if it was recently finished with a WRP, a semi-transparent stain may not absorb properly. In these situations, the wood should be allowed to weather for two to three months before finishing. This is the only situation in which it is beneficial to wait this long before finishing the wood with a penetrating stain. Lumber should not be left unfinished for six months to one year as indicated by some product literature, or as recommended by some paint and lumber suppliers. A short drying period may sometimes be necessary.
Film-Forming Finishes
Film-forming finishes cover a range of finishes from waterborne, latex-based, semi-transparent stains to paints, and include both oil-based and latex solid-color stains (also called opaque, full-bodied, or hiding stains). Almost all of these products are unsuitable for use on wood decks. The only exception is good-quality paint, but even that can fail prematurely and cause decay in the wood. On structures that are fully exposed to the weather, such as decks, paint tends to trap moisture and can actually increase the decay hazard. The paint seal breaks at the joints between different pieces of wood. These cracks permit water to enter the wood and become trapped by the paint film. This leads to decay of untreated wood, and the paint peels at these joints. Proper pressure treatment with a preservative can eliminate the decay risk. However, it is best to avoid the use of film-forming finishes on lumber that is fully exposed to the weather, even if the lumber has been pressure treated.
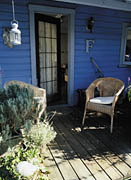
Conditions that Affect the Finish - Weathering Wood
Weathering of wood is a photochemical degradation of the surface caused by the combined effects of water, the ultraviolet (UV) radiation in sunlight and abrasion by wind-blown sand. Weathering should not to be confused with decay. Photochemical degradation is manifested by an initial color change, followed by the loosening of wood fibers and gradual erosion of the wood surface. Rain washes the degraded wood materials from the surface. Rain and/or changes in humidity cause dimensional changes in the wood that accelerate this erosion process. In softwoods, erosion is more rapid in the less dense earlywood rather than in latewood, which leads to an uneven surface. However, surface erosion proceeds slowly. The erosion rate for solid softwoods, exposed horizontally in temperate zones, is on the order of 5/16–5/8 in. (7–14 mm) per century, and depends mainly on the intensity of UV radiation and the wood species.Weathering is a surface deterioration and, therefore, directly affects finish performance. A film-forming finish applied to the eroded and roughened surface of weathered wood may not adhere properly; exposure of wood for only a few weeks is sufficient to cause this loss of adhesion.
Wood finishes also undergo photochemical degradation, but the mode of degradation is different for penetrating finishes (stains and water repellents) than for film-forming finishes (paint).
The weathering of penetrating finishes, such as semi-transparent stains and WRPs, is similar to unfinished wood. The surface of the wood degrades, but at a slower rate than unfinished wood. If the finish contains a pigment (semi-transparent stain), it partially blocks the sunlight. As the wood surface and the finish undergo simultaneous degradation, the pigment particles no longer bond. As the pigment erodes from the surface, the degradation of the wood increases. To avoid excessive wood degradation, timely refinishing is essential. The surface should be refinished when pigment loss is evident. The subsequent finish should absorb into the wood. Finishing too early leads to inadequate absorption and film formation. Finishing too late allows excessive wood degradation.
Pigments in film-forming finishes (e.g., paints) block the damaging UV radiation and protect the wood surface. The degradation of the film occurs on the surface of the film and results in slow finish erosion. This is the most benign mode of paint degradation because, as the primer coat begins to show, another top-coat can be applied.
When painted wood of a deck is fully exposed to the weather, another type of degradation occurs. This degradation mode involves checking, cracking, and peeling, and can occur with other film-forming finishes as well. When paint has peeled, the surface of the wood is completely vulnerable to weathering. Paint peeling is the most serious mode of paint degradation and is likely to occur on painted decks.
Preservative Treatment
Finish characteristics of preservative-treated wood are primarily dependent on wood species and grain orientation (flat or vertical grain) of the lumber. Preservative-treated lumber is not graded according to grain orientation. Therefore, lumber from a species group like Southern Pine generally contain wide bands of latewood, which can create finish problems. Stain penetration is poor on these latewood bands, and early finish failure is more likely to occur, particularly in structures that are fully exposed to the weather.Waterborne preservative treatments do not adversely affect the finishing characteristics of the wood. In fact, CCA treatment actually enhances the durability of semi-transparent stains and similar finishes. CCA contains chromium oxides that bond to the wood after treatment. These chromium oxides decrease photodegradation of the wood surface, and can increase the durability of semi-transparent stains two to three times.1 It should be noted that ammoniacal copper zinc arsenate and copper oxide/quaternary ammonium compounds do not contain chromium oxides; therefore, stain performance on this type of treated lumber will be similar to that on untreated wood given similar finish coverage and exposure conditions.
Other preservative pressure treatments for wood, including creosote and pentachlorophenol in light or heavy oils are intended for use on retaining walls, railroad crossties, and other heavy industrial applications. They should not be used on wood decks. Penta in heavy oil and creosote will not hold paint, so the lumber does not absorb semi-transparent stains well. Penta in light oil or solvent can be finished after it weathers for a year or two.
Moisture Content
The main consideration in finishing pressure-treated lumber is the moisture content of the wood. In some cases, the lumber may still be wet from the pressure treatment when it is delivered to the job site, particularly during cool or wet weather. If the wood is still wet, it must be allowed to dry before finishing so that the surface moisture content is less than 20%. The rate of drying depends on weather conditions; under warm, summer conditions, about two to three weeks should be sufficient. For the best finish performance, the wood should have a moisture content that is typical of what it will have during its service life. This is about 12% for most areas of the United States.2Methods for Finishing New Decks
The first finish on wood, whether it is a deck or any structure, is the most important. This finish should be applied as soon as the wood surface is dry. If the first finish is not applied properly, there is often little that can be done to correct problems that develop later. The choice between a penetrating and a film-forming finish should be given considerable study, because it is necessary to continue with that type of finish in the future. If a penetrating finish is to be used, the next decision is whether to use a semi-transparent stain or a WRP. The service life of WRPs is about one year on the exposed surfaces; however, WRPs are extremely easy to reapply to decks. They absorb readily into the end grain of lumber and can stop the wood from absorbing water into the end grain much longer than one year. Because they are not pigmented, problems with uneven wear and lap marks are eliminated. Lap marks occur during finishing when the finish that is being applied to an area laps over an adjacent area that has already been finished. This yields areas that have two coats of finish, whereas the surrounding area has only one coat.To avoid lap marks in applying semi-transparent stains, brush the stain on only two or three boards, being careful to keep the edge of the stain along the edge of the board. Stain the entire length of these boards. If a second coat is desired, it must be applied while the first coat is still wet (within 30 to 45 min), or it will not absorb. If the first coat has dried, it seals the surface and the second coat cannot be absorbed. Brush the stain onto the adjacent two or three boards, being careful to avoid lapping stain on the boards previously stained.
If you are unsure whether to stain or to use a WRP, apply the WRP on the deck first. It is possible to switch to a semi-transparent stain when the deck needs to be refinished. Even if the deck has been maintained with a WRP for many years, the semi-transparent stain will perform satisfactorily, because it penetrates the wood and will not fail by peeling, as can film-forming finishes.
The easiest finish to maintain on a deck is a WRP. The next best is a semi-transparent, oil-based stain. Film-forming finishes, such as paints, are prone to fail by peeling and are not recommended. The WRP requires frequent application, but the ease of refinishing compensates for the additional applications.
Conclusion
Long-term performance of horizontal wood structures exposed to the environment and foot traffic is improved if maintained with a finish after construction. The role of the finish is to protect the surface from the natural weathering processes. Lumber should be finished as soon as moisture content conditions permit; additional weathering beyond necessary for drying will not improve finish performance. The surface should be refinished when some pigment loss is evident. Premature and delayed finishing can lead to inadequate absorption or excessive wood degradation, respectively. Ease of finishing should be considered in selection process. Film-forming finishes, such as paints, are generally not recommended for horizontal exposures because water can be trapped and actually improve the conditions for decay fungi.This article was originally prepared as a paper by the Joint Coatings/Forest Products Committee Treated Wood Task Group. Chairman: Alan Ross, Kop-Coat Inc., Pittsburgh.
For more information on wood finishing, contact Alan Ross by e-mail at ASRoss@Kop-Coat.com; call 412/826.3387.
Report Abusive Comment