Improved Block Resistance in Low-VOC Acrylic Topcoats Without Fluorinated Additives

Coating manufacturers are continually working to improve their products. This is achieved by either improving the performance of the cured coating, or by reducing the time it takes for a coating to return to service after application. One of the key properties that allows a coating to return to service quickly is the rapid development of block resistance, which is the ability of a coating to resist adhering to, or developing blemishes due to contact with another object. Block resistance is an important property for most coatings applications that spans many market segments, including architectural, institutional, cabinetry, and industrial paints. Block resistance is one of the many performance requirements demanded of paint consumers today, which drives paint manufacturers and raw material suppliers alike to find the best balance of properties for their market, with the fewest compromises. In this article, we will discuss the role of latex in delivering on this goal with a new approach to near-zero-VOC coatings with same-day block resistance, without a reliance on fluorosurfactants.
Background
Block resistance is defined as the ability for a film to resist either self-adhesion or adhesion to another substrate. Block resistance is a particularly important attribute around windows, doors, cabinets, when stacking painted parts, or wherever a coating is in contact with some other object. In each of these situations, there is an opportunity for the paint film to adhere to either itself or another substrate, and if the adhesion is too strong, it can cause delamination or tearing when the door is opened, or when the parts are separated. Traditionally the block resistance of a film builds as a function of time. Since this property increases over time, it is also important that a coating has strong block resistance from an early point in time after application. For many paint manufacturers, films must be able to pass a block resistance test after an overnight cure, but as technology advances, manufacturers are looking to decrease that initial cure time as much as possible.
Currently there are a variety of approaches to designing a coating system that has strong block resistance including considerations such as pigment volume concentration (PVC), glass transition temperature (Tg), and using wax additives and fluorochemical additives. While they all can help a manufacturer achieve the goal of increased block resistance, they may also bring in varying degrees of negative impacts on other properties.
A common technique to create a paint film with strong block resistance is by having a high PVC in the coating formulation. Inorganic pigment particles are very hard relative to the binder, and are typically insensitive to temperature, which effectively hardens the final film and aids block resistance. Unfortunately, as the PVC is increased, the gloss tends to be lower. This may not be an issue if there is no target sheen, but in systems that are targeting a high-gloss, semi-gloss, or even satin finish, increasing PVC is not a viable solution. In addition to gloss implications, higher levels of pigment will generally lower the durability of a coating film, especially in the context of abrasion, durability, and water resistance.
Another common technique to create a paint film with strong block resistance is by utilizing a binder with a high Tg. Much like with an increased PVC, this directly increases the hardness of a film at all temperatures that allow a paint film to resist blocking. The primary drawback of higher Tg binders is that they become more difficult to coalesce. Therefore, for higher Tg binders to coalesce at low temperatures, if not room temperature, a coalescent must be added. If a standard volatile organic compound (VOC) coalescent is used, then the formulator must be aware of any VOC regulations that may be applicable. If the target VOC is reached and the formula is still not coalesced, then a low-VOC coalescent can be incorporated. In small amounts this is a great solution, but if high levels of low-VOC coalescent are utilized, it may permanently soften the film, canceling out any benefits that were gained by increasing the Tg of the binder. In addition to VOC concerns, it should be noted that increasing the Tg of a binder is not trivial. It involves, at the very least, changing the monomer ratio within the polymer backbone, if not changing the monomers themselves. While this does not necessarily have an impact on final properties, it can have unintended consequences, so any binder change should be accompanied by an investigation into its effects on important performance properties. Lastly, high-Tg binders can have durability issues outside in colder temperatures where they can struggle to flex with the substrate they are applied onto as the outside temperature fluctuates. This is primarily an issue with wood substrates but can occur on any substrate with dimensional instability.
When neither of the previous approaches is appropriate for the application, formulators will commonly turn to additives. The first common additives added for block resistance are waxes. Wax additives preferentially migrate to the air/liquid interface of a film while the film is drying. This allows the film to have a different morphology or composition on the surface than in the bulk of the film, so a harder wax can impart improved block resistance.
Finally, another common additive that is used to formulate coatings with strong block resistance are fluorochemical additives. Much like waxes, fluorochemicals generally migrate to the air interface of a film during drying, but unlike waxes, they impart block resistance by the nature of their chemical structure. The fluorine atoms of the compounds prevent anything from adhering to them, whether that is a similar film or another substrate. While there may be other changes to coating properties, especially surface properties, fluorochemicals typically do not have a strong effect on durability or other common film characteristics. However, due to increased scrutiny and regulation, fluorochemical additives have become a less desirable solution.
PFAS Regulations
In the regulatory context, there are several acronyms that are commonly used to describe fluorochemicals. Per or poly-fluorinated alkyl substances, or PFAS, are compounds that have multiple fluorine atoms attached to an alkyl chain. Two PFAS compounds of particular interest are perfluorooctanoic acid (PFOA) and perfluorooctanesulfonic acid (PFOS). PFOA and PFOS are the focus of particular regulatory concern due to their mobility and inability to break down readily in the environment, as well as their potential risk to human health.1 While PFOA and PFOS are not typically used in waterborne coating formulations, some fluorinated additives in coatings, such as fluorosurfactants, can fall under broad regulatory definitions for PFAS.
With PFAS uses coming under increasing scrutiny by EPA, the United States, and international agencies in Canada, the European Union, and elsewhere, there has been increasing pressure to identify alternatives to PFAS, especially in consumer-facing products. Replacement of PFAS chemicals in formulated products presents a significant technical challenge due to the unique attributes of fluorinated additives, including their durability and resistance to degradation. Nevertheless, in some cases, alternatives to PFAS additives with comparable performance attributes have been identified, presenting an opportunity for customers seeking to avoid additional regulatory obligations.
Polymer Optimization
With new complications regarding the use of fluorosurfactants, alternate strategies are needed to achieve improved block resistance. The solution that EPS has found is through polymer optimization.
Particle morphology describes how a polymer particle is structured. A latex polymer could be composed of a single stage, meaning that the entire polymer is made up of the same monomer composition. By utilizing different synthetic strategies, particles can also be created in non-homogeneous ways that allow for different monomer mixtures that possess different properties to be present within the same latex particle. This can result in polymers with multiple domains that can be organized into complex morphologies, that when designed for a specific purpose can be a powerful tool for controlling end-use properties.
Introducing cross-linking moieties is another technique to optimize polymers that can improve block resistance. These cross-linking components can increase the hardness of a film post-cure, without raising the overall VOC of a paint, and can impart both intra-particle and inter-particle crosslinking. This allows a polymer to have a higher hardness and higher molecular weights than can be achieved just by changing the monomer ratios alone. This technique can also be combined with particle morphology to create even more complex structures. Finally, other specialty monomers can be incorporated into a resin that promote adhesion, flexibility, hardness, and coalescence demand, among other performance properties.
Comparing Fluorosurfactant-Containing Polymers to Optimized Polymers
To determine if an optimized polymer can meet the level of block resistance performance that a polymer-containing fluorosurfactant (FS) has, two polymers were developed. One was made utilizing a fluorosurfactant additive, referred to as “Polymer with FS,” while the other was optimized in the absence of fluorosurfactant, referred to as “Optimized.” Both were all-acrylic self-crosslinking latexes with a minimum film-forming temperature of 21 °C (a temperature that is compatible with <50 g/L VOC formulations). Both polymers were formulated into the same semi-gloss white formulation shown in Table 1. A similar, clear base formula was also tested in each binder system and tinted with 12 oz/gal yellow iron oxide color dispersion. Tests were chosen both to test the effect of the polymer on block resistance and other standard coating properties, with an emphasis on surface properties, due to fluorosurfactants generally being surface active.
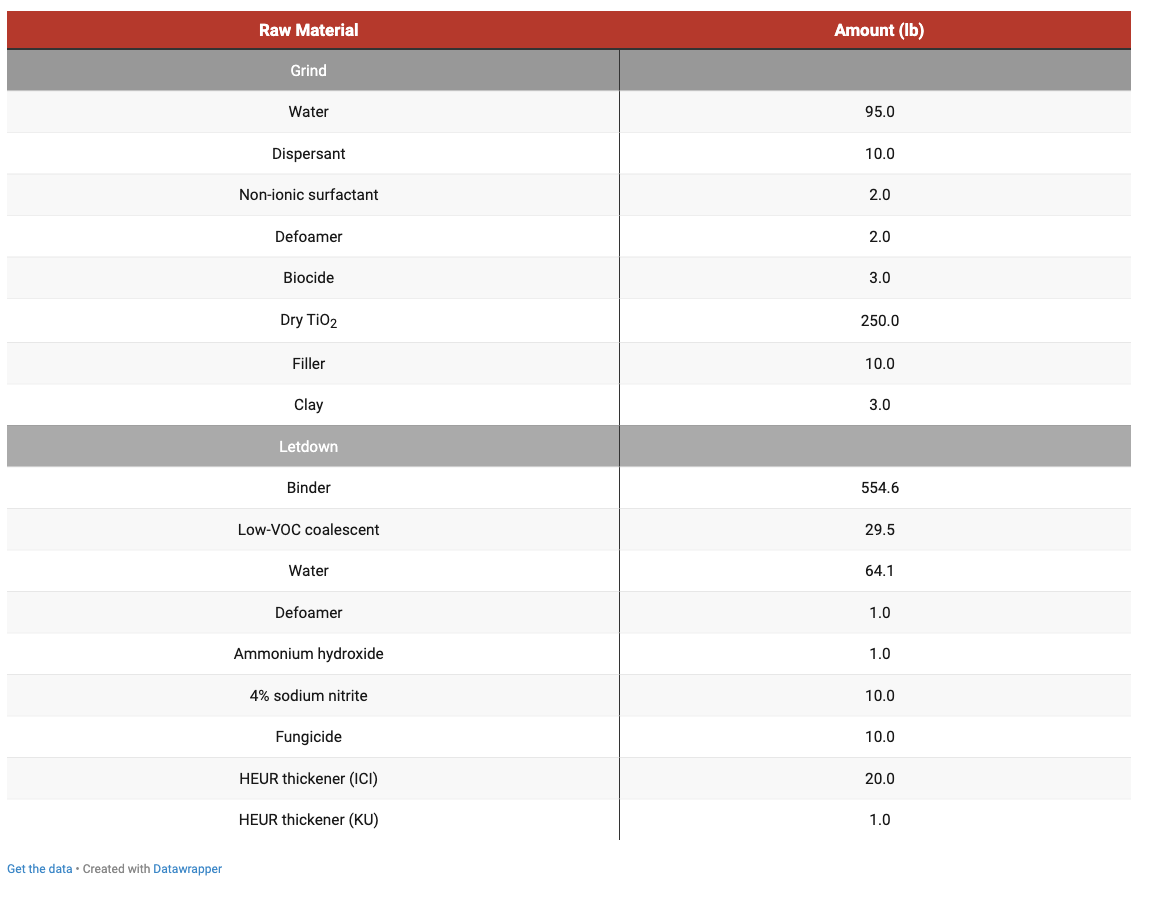
Block Resistance
ASTM D4946 was utilized at various cure times to quantify the block resistance of the two systems. In addition to the semi-gloss (SG) white formulation, both polymers were formulated into a modified-SG, clear tinted-with-yellow oxide colorant (YOX). This formulation was evaluated as a highly tinted system with a low PVC, which allows for greater differentiation for block resistance testing.
As is demonstrated in Figure 1, in a SG white, both the Polymer with FS and the Optimized Polymer achieve at least a passing score of at least 4 after a 4-hour cure. However, the Optimized Polymer has improved upon the performance of the Polymer with FS, with a block-resistance rating of at least 8 at all time points, including at 1-hour cure time. In the SG yellow-oxide formulation, the Polymer with FS only passes after 7 days of curing, whereas the Optimized Polymer passes after 4 hours. Overall, the Optimized Polymer is easily able to meet and surpass the block resistance performance of the Polymer with FS.
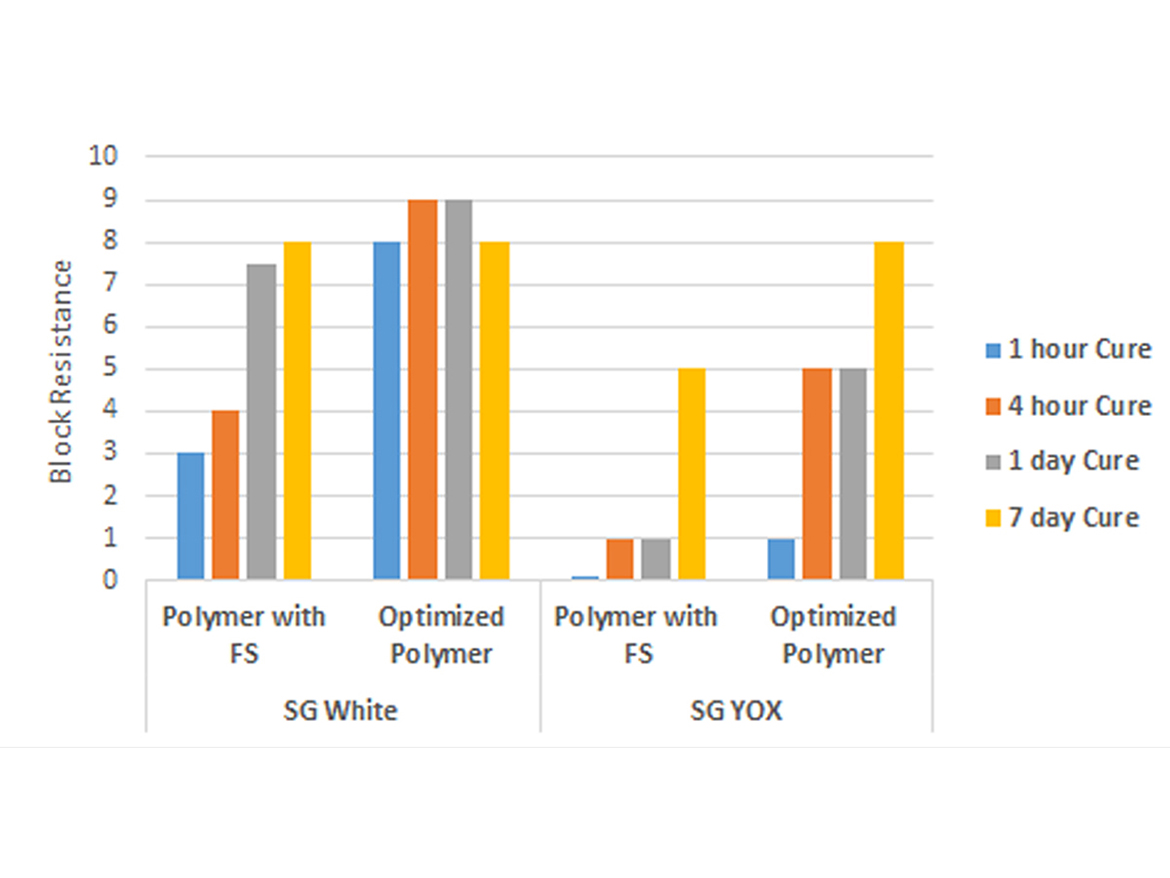
Tack Resistance
Another important surface property that is related to block resistance is tack resistance. Generally, films that do well in block resistance do well in tack resistance, but this relationship is not always guaranteed. This test was performed on a high-gloss (HG) modification to the SG-white formulation, as well as a HG clear formulation modification tinted with red, yellow-oxide, or black colorant at 12 oz/gal. Films were allowed to cure for 24 hours at 70 °F and 50% relative humidity. Once cured, a cotton ball was sandwiched between the film and a 500-g weight for 60 minutes at 120 °F. After the 60 minutes, the weight was removed and the remaining system was allowed to cool for 30 minutes. After this cooling period, the cotton ball was removed in one motion, and the remaining cotton was rated qualitatively. The results can be seen in Figure 2.
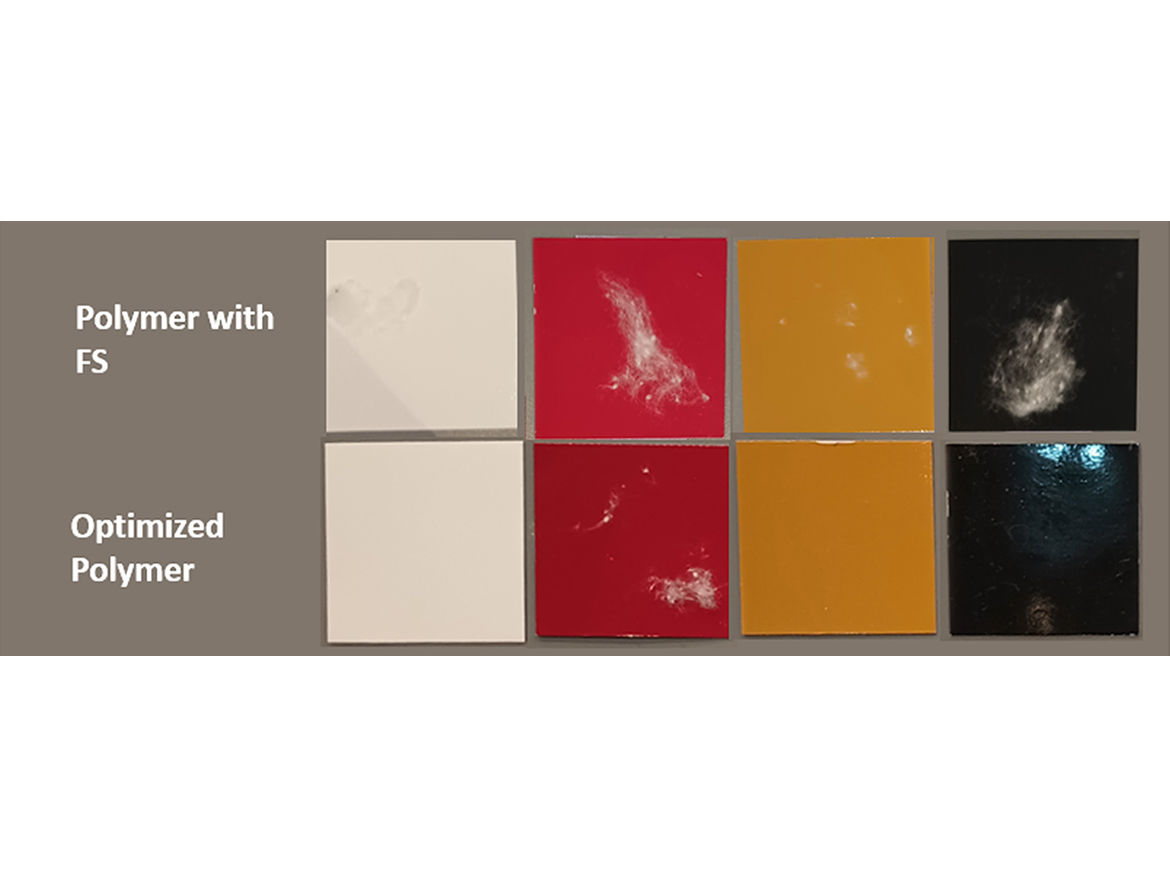
While both polymers perform well in this test, the Optimized Polymer performs significantly better than the Polymer with FS, particularly in the red and black organic pigments.
Interior Durability
Two tests were selected to test interior durability: a high-traffic durability test and a washability test. The high-traffic durability test simulates a coating applied in a high-contact area such as near a light switch or door. A coating is allowed to cure for 7 days, after which a lotion is then applied to half the panel for 2 hours, and then removed. A mineral oil and carpet dirt stain or a rusty water stain is then applied for 2 hours, after which is wiped away. Once the stains are removed, the panel is subjected to 100 cycles of a sponge and a non-abrasive scrub media. The dE from the initial film color is reported in Figure 3 and can be observed in Figure 4.
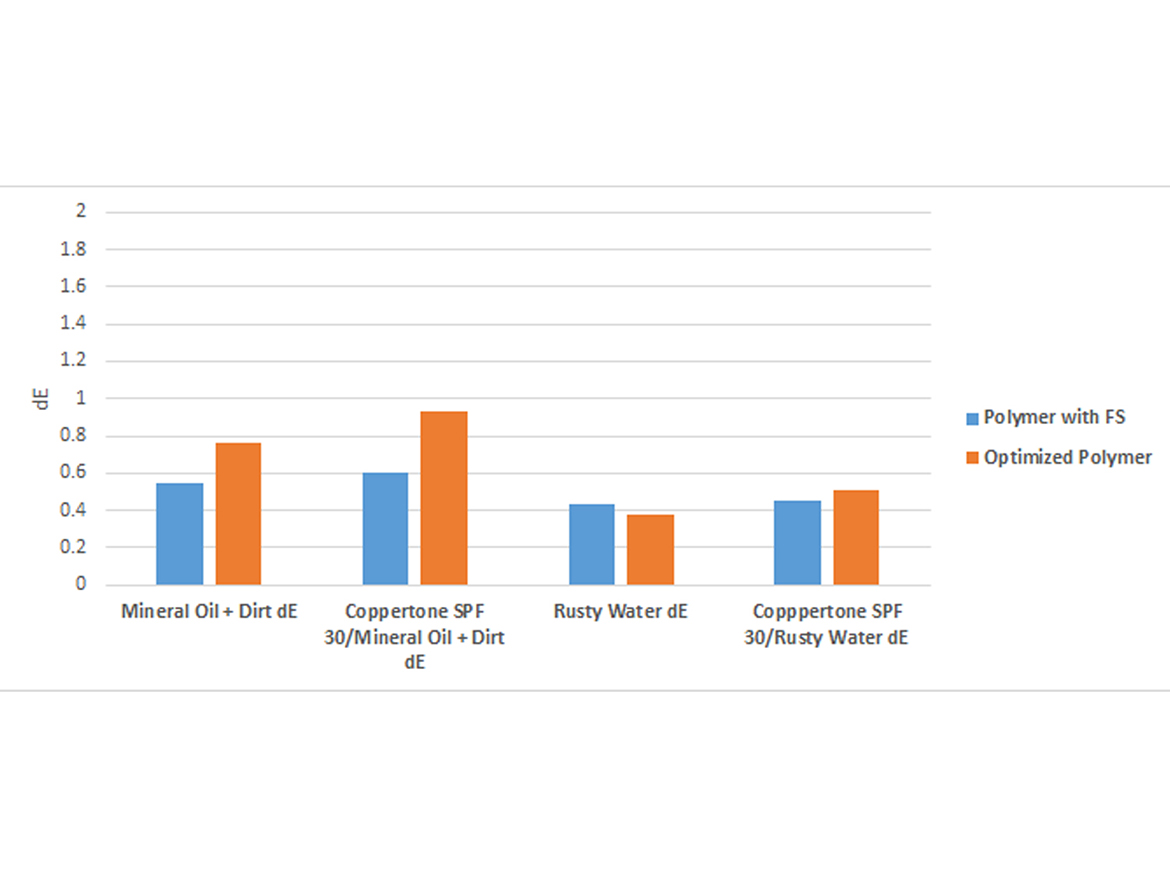
The Polymer with FS and the Optimized Polymer demonstrate minimal differences between the dEs of the various media, and are within 0.5 units. The washability test captures how well the film can be cleaned after a common household stain is applied and left for a moderate period. A modified ASTM D4828 was utilized with pencil, lipstick, crayon, washable marker, coffee, wine, mustard, tomato sauce, and pen as the stains and allowed to sit on the coating for 4 hours. The results can be seen in Figure 5.
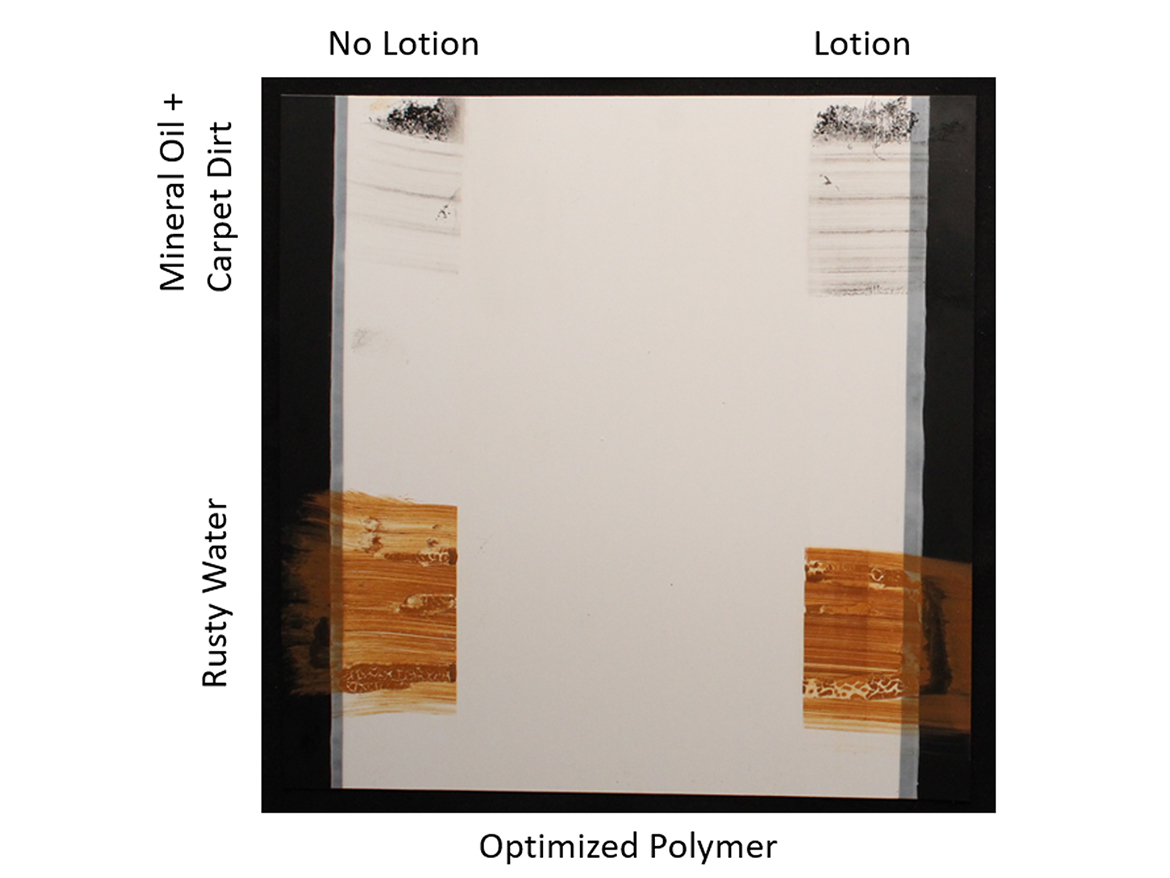
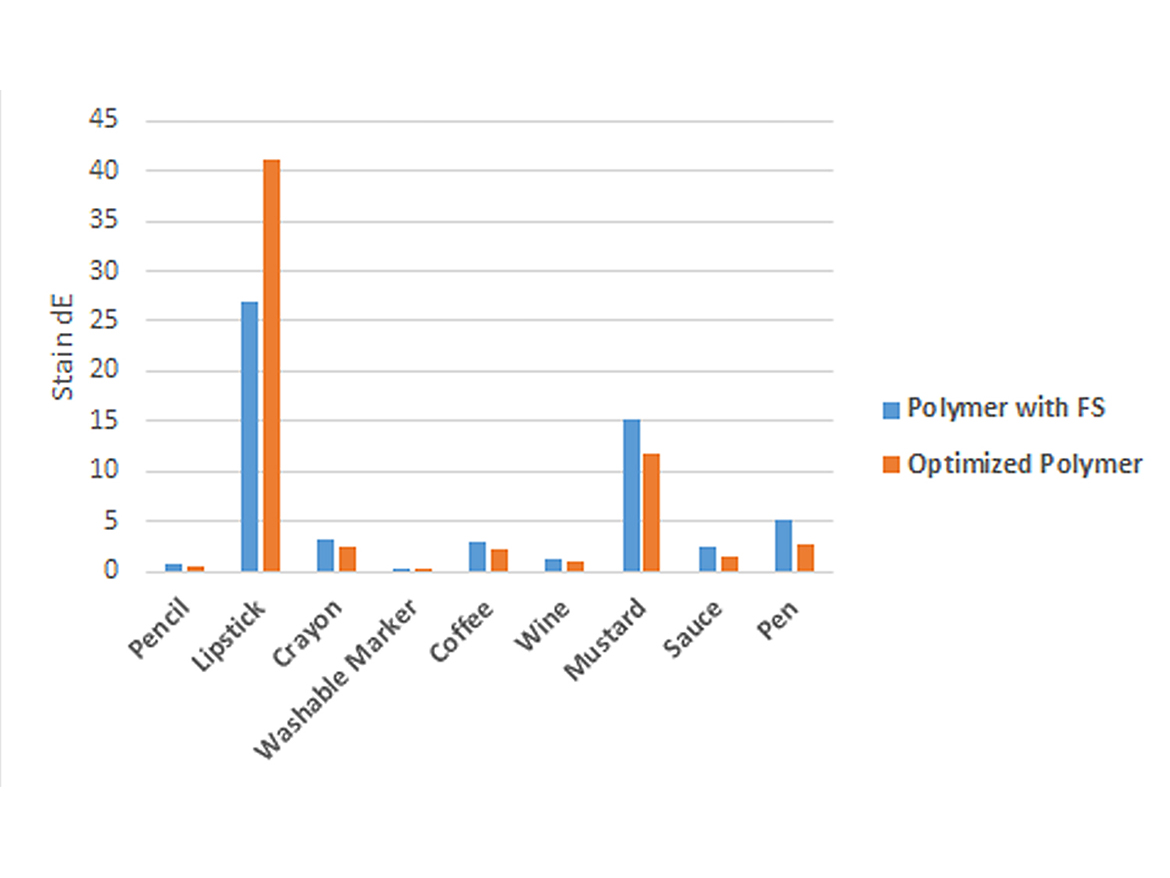
The Optimized Polymer performs marginally better than the Polymer with FS in all categories, except lipstick. However, both polymers struggle for removing lipstick, resulting in a high dE in both cases and an overall visually apparent residue.
Exterior Durability
Three methods were chosen to test exterior durability: cyclic QUVA, Florida exposure, and California exposure. Cyclic QUVA is an accelerated weathering test that can provide results that correlate with true exterior exposures without having to wait for months or years. The method utilized was ASTM G154 cycle 1, and the results can be seen in Figure 6.
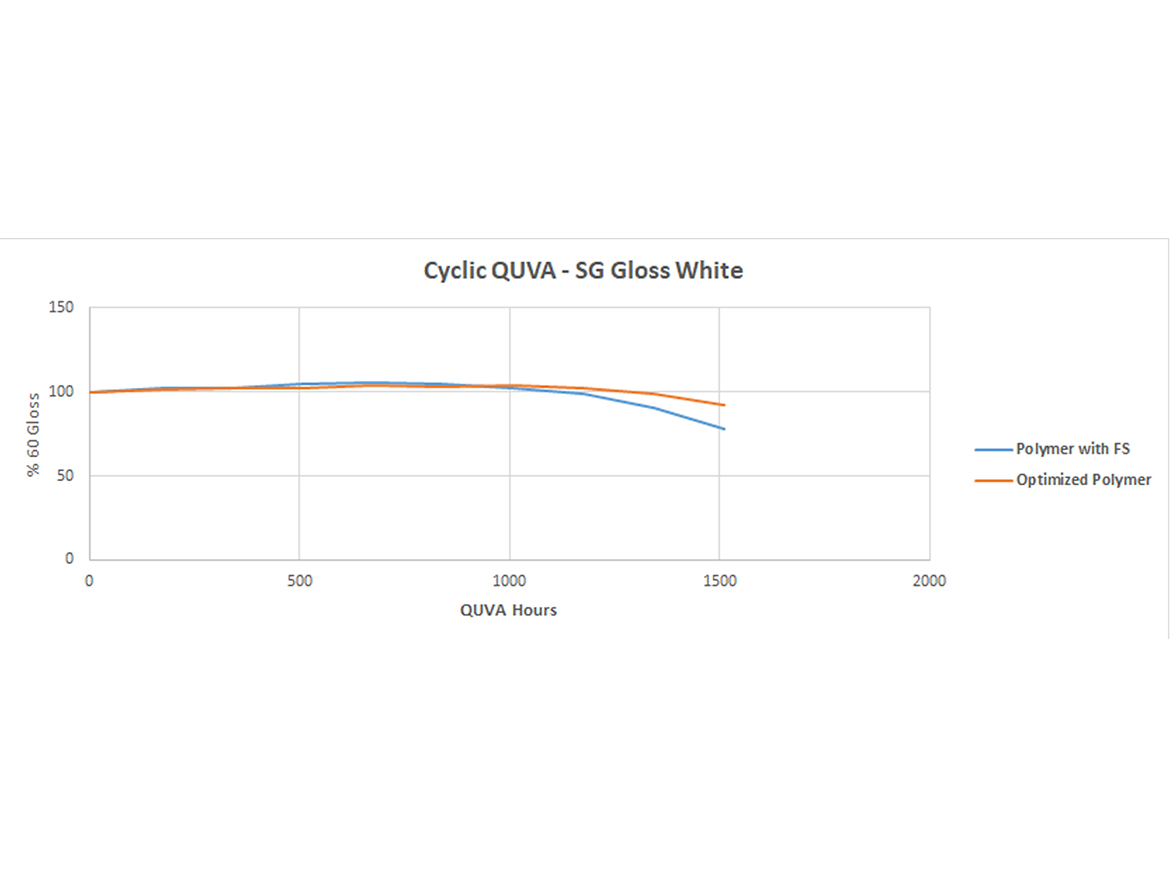
While there is a slight variation past 1,000 hours, the two polymers generally have equivalent performance. A Florida exterior exposure is a real-world test in an environment that emphasizes gloss retention. Coatings are generally subjected to a very-humid and wet environment with a large amount of UV exposure. The coatings were painted onto primed aluminum along with a modified clear formulation tinted with either yellow oxide or black and exposed in Fort Myers for nine months. Percent gloss retention was observed and reported in Figure 7.
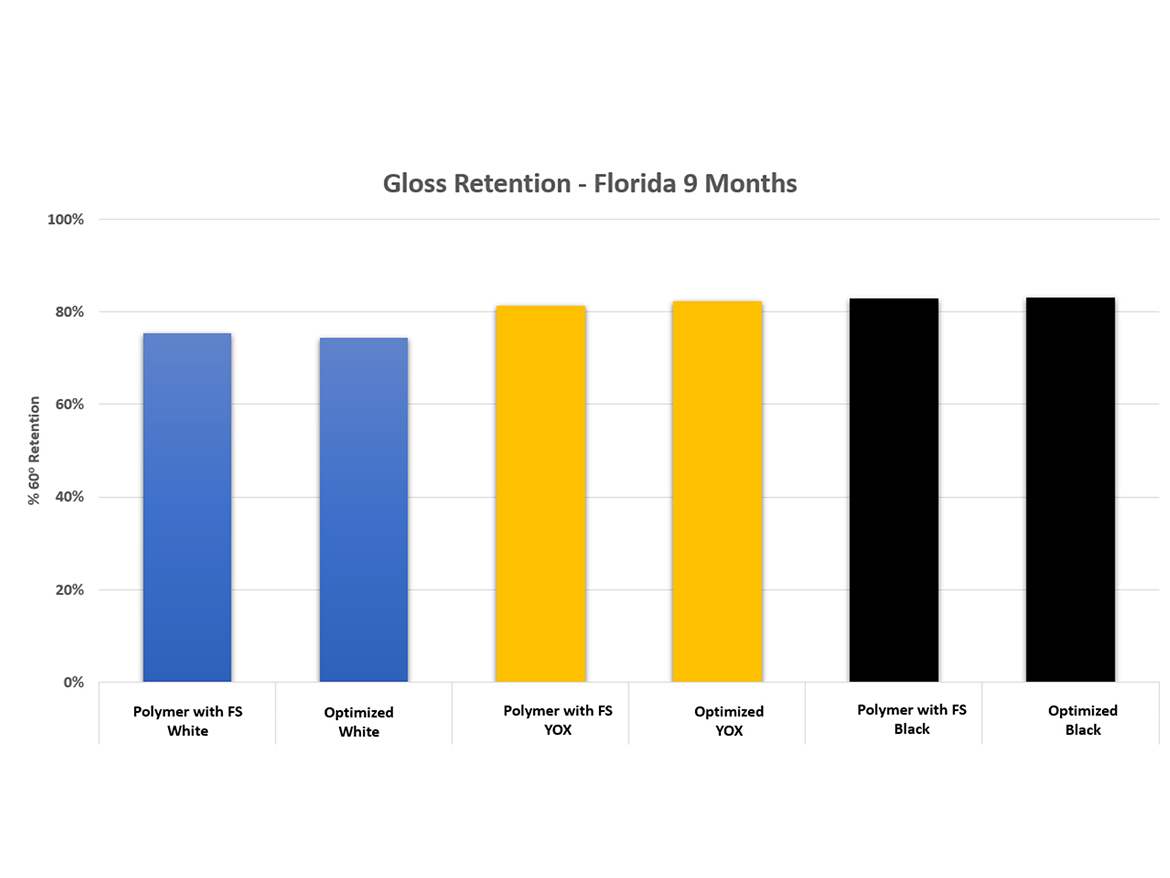
As predicted by cyclic QUVA, both the Polymer with FS and the Optimized Polymer have equivalent performance in all colors at 9 months. Lastly, our Los Angeles test location is a challenging exposure environment, specifically due to the severe smog, dirt, and dry-heat. As such, panels exposed in this environment demonstrate their dirt pickup performance rapidly. This emphasizes the need for coatings that resist dirt accumulation. The coatings were applied to an aluminum panel alongside a modified-SG-clear formulation tinted with a yellow-oxide tint. Then they were exposed outside for 12 months and rated qualitatively. The results are shown in Figures 8 and 9.
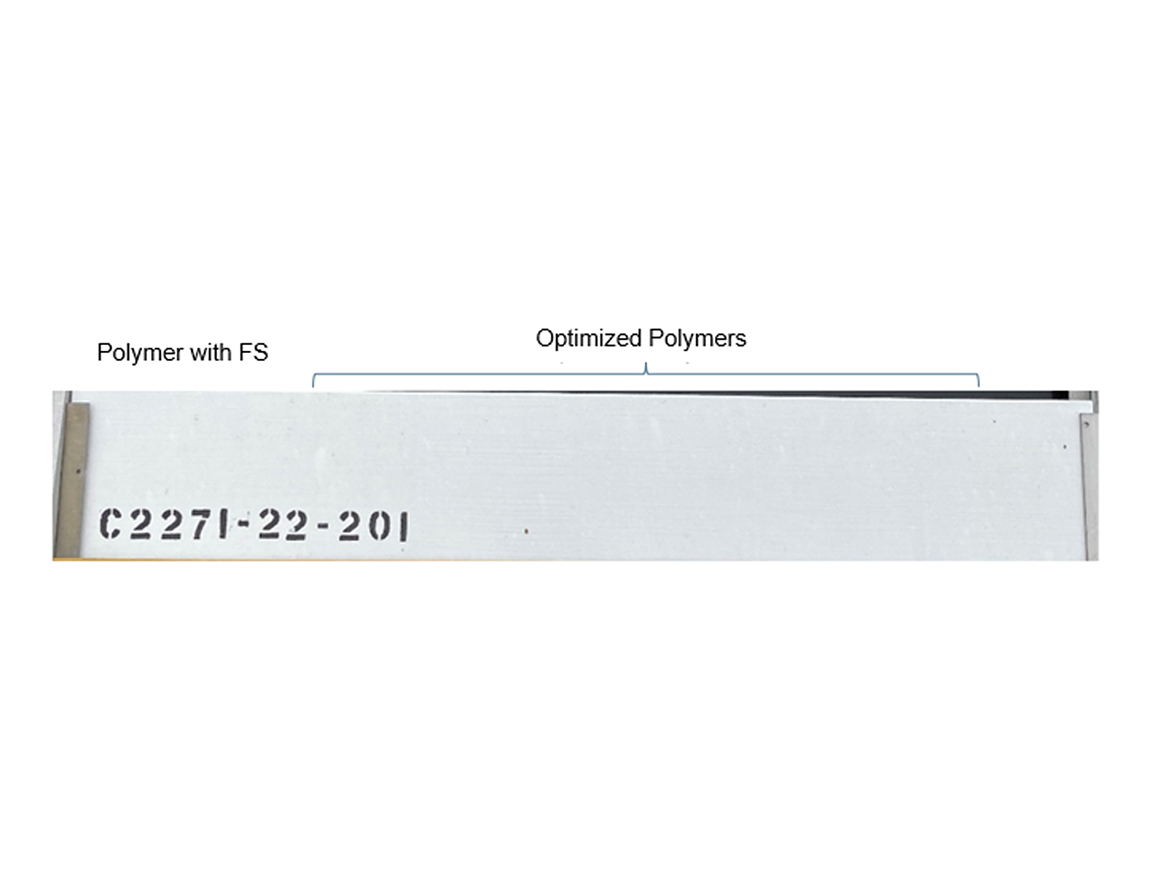
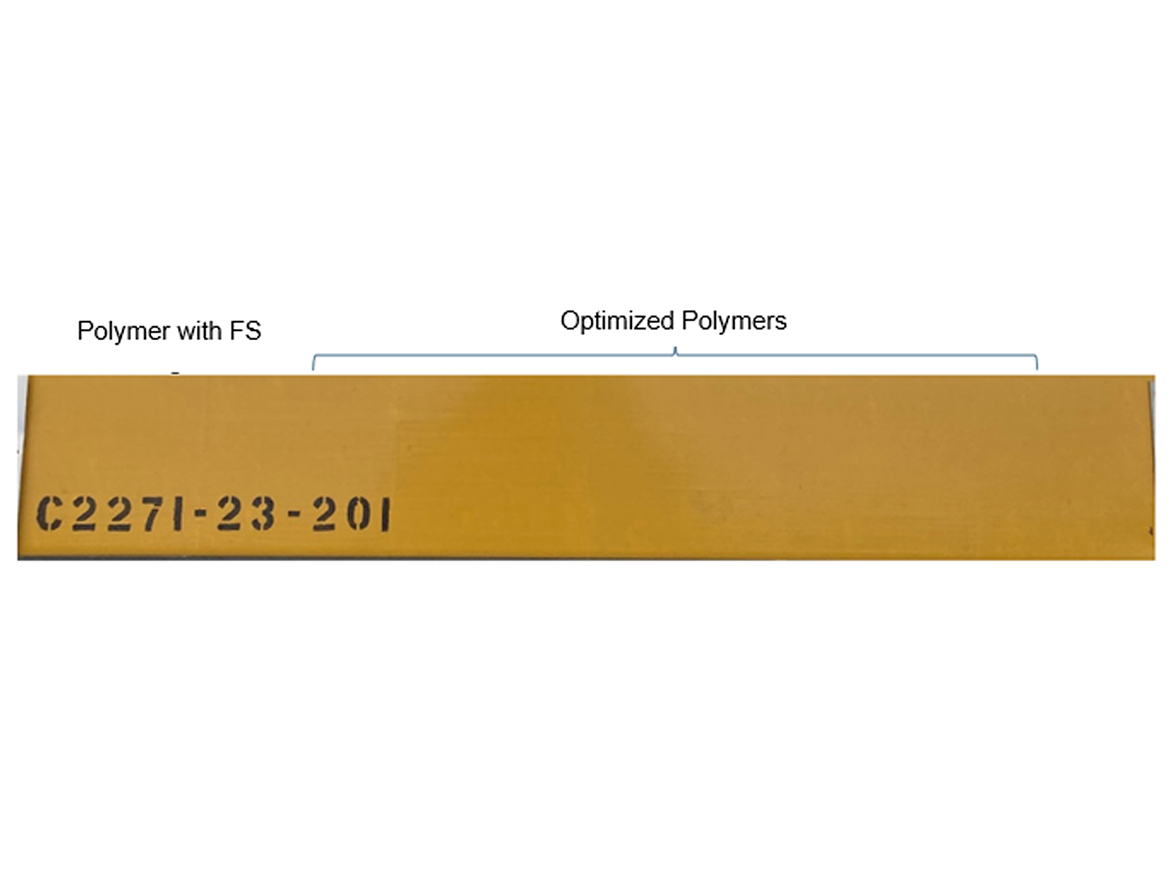
As demonstrated in Figures 8 and 9, there is no distinguishable difference between the DPUR performance of the Polymer with FS or the Optimized Polymer in either color.
Conclusion
Rapid return to service has become an important selling point for various commercial coatings. Performance expectations for low-VOC coatings has grown to not only expect excellent block, but to achieve that block in only a few hours of dry time. Previously, low-VOC coatings utilized fluorosurfactants as an additive to enhance the block resistance. However, due to increased scrutiny on PFAS compounds, a different approach is preferred. By utilizing a variety of polymer optimizations, removal of fluorosurfactant additives from formulations is possible without sacrificing other key properties. The study and experimentation, presented in part above, has contributed to the development of new product offerings that meet the high-performance block requirements demanded by the coatings industry today.
For more information, click here.
Acknowledgements
Ashley Rodgers and her team for synthesis support, Paul Baukema for his product stewardship insights. Jacob Bolton, Charles Myers and Dr. Patrick Lutz for application support.
References
1 PFAS Strategic Roadmap: EPA’s Commitments to Action 2021-2024. The United States Environmental Protection Agency. 2021. https://www.epa.gov/system/files/documents/2021-10/pfas-roadmap_final-508.pdf
Looking for a reprint of this article?
From high-res PDFs to custom plaques, order your copy today!