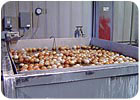
Powder coatings on aircraft engine parts almost fully dissolved in the new chemical stripper. A light rinse in a hot water bath was the only additional cleaning needed.
Four basic stripping methods are typically used to remove cured powder coatings: mechanical, thermal, thermomechanical and chemical. Each method has advantages and disadvantages that must be considered in making a selection. Recently, a new chemical process has been developed that offers quick coating removal at ambient temperatures and is safe for workers and the environment. With this new process, today’s finishing professionals have a new option for powder coating removal.
Conventional Methods
MechanicalMechanical removal uses blasting media such as sand, water, dry ice, glass beads, steel or plastic. The media is shot at the surface under pressure, and the abrasion resulting from the impact removes the coating. Aggressive blasting media can remove the coatings quickly but can leave the surface rough. More gentle blasting methods can preserve the surface profile but are slower.
Mechanical removal is usually the most inexpensive method of coating removal since it requires simple equipment; however, since each part has to be blasted individually, it is typically much slower than other processes, so labor costs can be high. Irregularly shaped parts can be a problem because they take a long time to blast and they can trap blasting media, which can cause coating failures. The surface of any part must also be cleaned with solvents or an alkaline wash before blasting, or any contamination that is on the surface can be embedded in the surface and cause coating failures.
Thermal
Thermal removal methods use high temperatures to remove the coatings. The three types of thermal removal are bake-off, burn-off and fluidized bed.
Bake-off stripping systems are batch processes in which parts, hangars or racks are loaded into an oven that is operated at 644-752°F (340-400°C) - the temperature range in which most powder coatings will degrade and eventually ignite. Parts usually require three to six hours for complete cleaning, but the oven can process many parts in one cycle. This process leaves residual ash on the parts that must be removed in a separate washing stage to prevent contamination of the next coating process.
Burn-off stripping systems operate at much higher temperatures, from 1004-1202°F (540-650°C). At these temperatures, the coating ignites quickly and is burned away from the part. Normally this method is used as part of an inline process operating at up to 6 ft/minute, and coatings can be removed in as little as 4 minutes. Water is used to extinguish the fire and remove the ash so that the parts are clean when they leave the process. The drawback is that high temperatures can damage or warp parts, so this process is generally only used for hangars or racks.
Fluidized bed stripping systems use inert media such as sand or oxides to transfer heat. Natural gas or propane is burned in a chamber below the media, and the heat produced is blown through the media, causing it to be heated and held in suspension just like a fluidized powder hopper. Hangars or products are lowered into the 806°F (430°C) fluidized media, where the coating breaks down and the ash is removed by the abrasive action of the media. The parts do not require additional cleaning after processing. This type of system can be used in batch or inline applications.
Regardless of the process used, the key to thermal stripping is that parts and hangars must be resistant to high temperatures. All three thermal processes produce combustion byproducts such as volatile organic compounds (VOCs) that require afterburners in the exhaust system to be properly destroyed. This equipment can be expensive and can consume a lot of energy; however, when the equipment is operated correctly, thermal processes release almost no contaminants into the environment.
Thermomechanical
Thermochemical stripping methods use temperature and a chemical reaction to remove the coating from the part. This method is often called “molten salt,” and it can strip parts and hangars in only a few seconds. It is used inline, and a water spray is used to remove the chemicals and residue from the parts or hangars. The operating temperature is about 806-896°F (430-480°C).
Chemical
Chemical stripping methods can use either hot or cold chemistries in a batch-type process. Hot strippers are usually caustic and operate near 176°F (80°C). The coating will dissolve or swell and might fall off into the chemical bath or need to be removed with a water spray. Hot strippers can evaporate fairly quickly, which can result in rapid chemical consumption. The caustic materials can also burn skin and eyes quickly, so they present a significant worker hazard.
Traditional cold chemical strippers often contain methylene chloride, phenols and other hazardous solvents. They work very quickly but are highly toxic and can burn workers within seconds of exposure. Both the used stripper and the rinse water used to clean parts are considered a hazardous waste.
Chemical stripping is relatively fast and economical, and the equipment is usually simple. However, due to the environmental, safety and disposal issues, this method is not often used anymore.
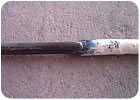
The new stripper was used to remove polyester- and epoxy-based powder coatings from a hook. The stripper removed all of the accumulated coatings after a 24-hour dwell time at an average temperature of 81°F (27°C).
An Environmentally Compliant Alternative
A growing resistance to hazardous chemicals in the 1980s prompted a number of researchers to look for alternative technologies for coatings removal. As a result of these development efforts, environmentally compliant products are now used to strip about half of the worldwide commercial airline fleet, including planes at companies such as Singapore, Quantas and United Airlines. Environmentally acceptable chemical stripping processes are also being used to address other applications where chemicals could not historically be used because of environmental issues or worker safety.More recently, researchers have begun focusing specifically on powder coating removal chemicals and processes. One solution that has emerged through these efforts is an alkaline, diphase liquid originally developed for removing coatings and carbon from engine parts in dip tank applications. The product has an oil upper layer to reduce evaporation. It contains no free hydroxides, phenols, chromates or chlorinated solvents and is safe on steel, aluminum, titanium, magnesium and most other metals. The product can be heated to 149-189°F (65-87°C) or used at room temperature.
With the new stripper, parts typically can be stripped in 15-60 minutes, and production hooks and racks normally can be stripped in 12-36 hours at 70°F (21°C), depending on the coating thickness and uniformity. (The type of powder coating being removed will also have some effect on stripping times, but the coating thickness is the biggest factor.) Solids can be removed by filtering the stripper with a bag- or sock-type filter. Most of the pigment will usually remain in suspension.
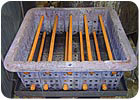
A crane-lifted bucket contains coated parts prior to stripping.
To test the stripper’s performance, the stripper was used to remove polyester- and epoxy-based powder coatings from a hook. The stripper removed all of the accumulated coatings after a 24-hour dwell time at an average temperature of 81°F (27°C). This result was typical of the performance that researchers saw in similar applications.
The stripper was also tested in a dip tank to remove coatings from aircraft engine parts. The tank containing the stripper was heated to 149°F (65°C), and the parts were immersed for 15-20 minutes. A variety of dipping mechanisms and baskets were used to accommodate the different sized parts, from heavy, crane-lifted buckets to simple pails with holes drilled in them. The tank was filtered continuously while in operation to capture loosened paint; the agitation caused by the filtration also helped speed the stripping. The powder coatings almost fully dissolved in the stripper, so the parts came out of the stripping bath almost clean. A light rinse in a hot water bath was the only additional cleaning needed. (A pressurized water spray also could have been used to clean the parts.)
Due to the effectiveness of the dip tank process, a similar system is being installed in a new powder coating plant that will open in 2007 near Houston, TX. The company builds accessories that are used in the automotive aftermarket. All parts are coated with a polyester powder coat. At the company’s existing plant, powder accumulates on the hooks until it falls off and causes defects on the parts. The company needs a fast and efficient system for cleaning the hooks and removing defective coatings from parts.
A dip tank containing the environmentally compliant stripper with a filter system will be built that can accommodate the largest parts, which are 2 meters long. The tank will probably be unheated since the removal times of 30-40 minutes are fast enough to prevent defective parts from accumulating. The tank will also be used at night to clean the hooks, which will help reduce overall defects.
A New Stripping Option
Many different methods can be used to remove powder coatings. Each finishing operation must consider what will be the most cost-effective and efficient process for their specific application. Following are some questions that can help determine the best process:- How fast must the coatings be removed?
- Is the process being used to clean parts or hangars/racks, or both?
- Should the process be in-line or batch?
- Will post-strip cleaning be required?
- Will the parts be damaged by the process?
- What are the environmental or health restrictions?
Report Abusive Comment