
Definition of Nanotechnology
Everyone is familiar with the term "atom" meaning the smallest indivisible part of matter that the Greek philosopher Democrit could think about. He came to the philosophical conclusion that atoms must exist by dividing matter into smaller and smaller parts that ultimately would lead to the smallest part that all matter is made of. If one picks up these thoughts today it is surprising that the change in size going from macroscopic matter to atoms is always accompanied by a change in properties. For example, the colours of metals change drastically when reducing the size of an individual unit of metal. If the size of gold particles is reduced to approximately 5 nm, the metal colour turns into an intensive red that, for example, has been used in former times to colour glass windows of churches. So only by changing the size does the physical property of colour change as well. The dimension needed to cause such a change in colour is in the area of a few 10-9 m or, in other words, in the range of a few nanometers. This change in physical properties is attributed to a change in the electronic properties of matter. Electrons are confined in a smaller space, causing these changes to occur. Nanotechnology deals with those electronic effects. Matter reduced in at least one dimension to a size less than 100 nm can be considered nanomaterial. At the same time, the surface area of nanomaterial is enhanced by orders of magnitude so that surface effects become a critical aspect in nanotechnology. Stabilization of individual units as well as the surface activity become important when using nanomaterials. Assuming a dense packing of atoms, almost 60% of all atoms are located on the surface of 2-nm particles. Even for 10-nm particles it is still around 20%, as can be seen in Figure 1.
Only well-dispersed individual units of nanomatter behave like nanomaterial in the best way. Even slight aggregation can cause the loss of all nanoeffects. For that reason, pre-dispersed nanoparticle master batches are an ideal way to utilize nanomaterials in coatings. By using only small amounts of the active ingredient and by achieving very high active ingredient contents in the master batch, nanoadditives are the smart way to introduce new or enhanced coating properties.

Nanotechnology in Coatings
There is a huge potential for nanotechnology in different areas of our daily life. One of the most mature areas where nanotechnology is applied today is in the field of plastics and coatings. The main reasons to apply a coating to a substrate can be for the intended decorative or protective effects. The protective need for surface coatings includes the need for protection against all types of environmental effects such as UV, humidity and oxygen, mechanical attack, and so forth. For those demands, technical solutions have been developed over time based mainly on organic and polymeric chemistry. Today more and more nanotechnology is being focused on by coatings manufacturers in order to achieve comparable, improved or even new effects in coatings. For example, by using certain nanosized oxides well dispersed into the coating formulation, the mechanical properties of these coatings can be improved significantly. Especially nanosized alumina and silica is of interest because high-gloss, high-transparent coatings can be achieved by using nanosized fillers instead of micron-sized materials. Figure 2 shows a TEM image of nanosized alumina made by gas phase synthesis. The material is dispersed at concentrations of more than 50% in different media. Due to the nature of the particles, the viscosity of those dispersions is very low since there is no tendency for bridging flocculation, as for example in materials made by flame pyrolysis. When incorporating a small amount of nanoalumina in a UV-curable coating system, the resistance against mechanical scratching can be increased significantly. In Figure 3, the increase in haze due to scratches formed on the coated surface is measured as an indicator for scratch resistance.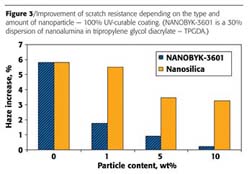
Without the organo siloxane the effect of scratch resistance cannot be achieved in all systems. Sometimes the appearance after scratching is worse (e.g., system 3 changes from 2 to 3). By adding a small amount of only 0.1% BYK-UV 3500, the effectivity of the nanoalumina can be enhanced significantly, leading to an improved appearance after scratching in seven out of eight coating systems.
Currently, the focus on the use of nanomaterials in coatings is in several other areas besides scratch resistance, including UV stabilization, anti-microbial activity, IR absorbance, or conductivity/anti-static properties. Inorganic UV absorbers are used more and more in coatings. Here, three different materials are under intensive development: nanosized titania, nanosized ZnO and nanosized cerium dioxide.
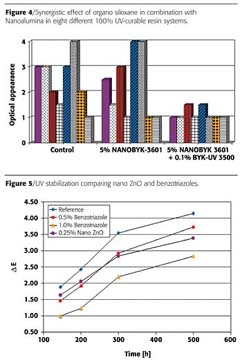
Compared to ZnO, the last of the three inorganic UV absorbers, titania has a higher absorption coefficient but is more transparent in the near UV-A region. ZnO very effectively blocks radiation below 400 nm while being less expensive compared to the two other oxides. In Figure 5, the stabilization effect of ZnO is compared to benzotriazole in a styrene-unsaturated polyester coating cured by radical polymerization. Due to the high amount of polystyrene, yellowing occurs even after moderate irradiation with UV-A light.
After 150 hours, the reference shifted by almost 2 units in the DE value mainly caused by a shift in the b-value, which is equal to a yellowing process. Benzotriazole (BT), at a level of 1%, can reduce this shift to 1, while 0.25% ZnO and 0.5% BT show equal effectivity. After 500 hours the ZnO is out-performing twice the amount of BT. These results are still preliminary but indicate already the advantages of inorganic nanosized UV absorbers. Due to the nanosize of the particles, the gloss and the colour of the coating is not affected when adding less than 2% of, for example, ZnO. Even with initially equally good performance of the inorganic and organic UV absorbers, especially over a long lifetime, the inorganic will out-perform the organic absorbers simply because it does not decompose by photochemical reaction induced by UV light.
Summary
In the short and midterm future, nanotechnology will influence our life more and more. Simply by changing the size of currently existing materials, new, improved or enhanced properties occur that can be taken advantage of. One area where nanotechnology is moving very fast into products is the field of nanocomposites and mainly in coatings. Improving the protective nature of coatings or creating new properties in coatings by adding small amounts of nanoadditives will be the future of nanotechnology in this area. Industry is taking the lead in this current area of R&D, including the environmental and health aspects of nanotechnology. A sustainable and safe use of nanotechnology will help to use existing resources in an even more responsible way.This paper was presented at the Nano and Hybrid Coatings conference sponsored by The Paint Research Association, January 2005, Manchester, UK. Conference proceedings are obtainable by contacting Janet Saraty, Conference Administrator, at j.saraty@pra.org.uk.
Report Abusive Comment