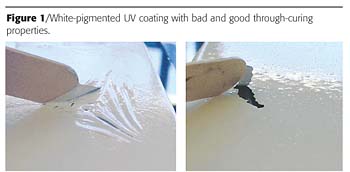
This paper provides an overview of several ideas for producing pigmented, UV-polymerized films with both good through-curing properties and excellent hiding power. The presentation discusses the right choice of pigments as well as different methods of processing a pigmented UV coating.
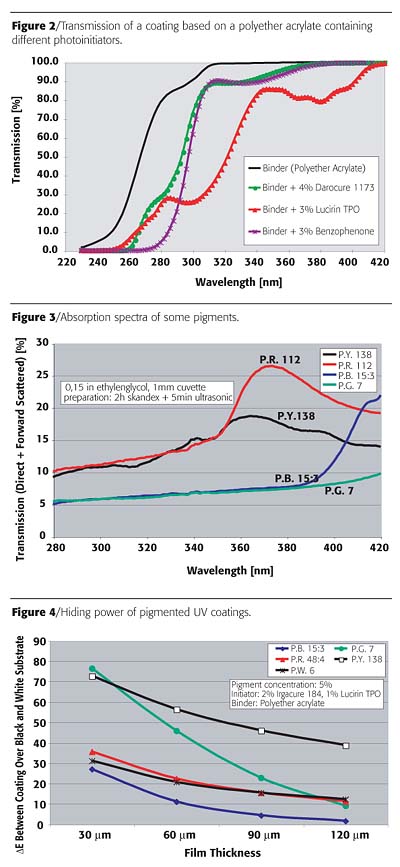
UV Monocure
In principle, UV coatings are formulated by combining an unsaturated binder with reactive diluents and a photoinitiator. The exposure to UV light cleaves the photoinitiator into radicals, which start the radical polymerization.The ideal way to cure colored UV coatings would be to find pigments that absorb in the visible light range (400 nm - 700 nm), thus providing good hiding power. At the same time, the coating should be transparent for the UV light to initiate the polymerization at the bottom of the film. In this case, the curing mechanism of radical polymerization induced by UV light is sufficient to change the liquid coating to a solid film.
Unfortunately, many pigments exhibit insufficient transparency in the UV region. Thus, not enough photons are able to reach into deeper layers of the film. Consequently, the rate of radical formation is too low. The result is a film that is polymerized at the surface but not at the bottom (Figure 1).
For white-pigmented UV coatings, developing the class of acylphosphine oxides as photoinitiators, as done by BASF AG, is a solution for this problem. Acylphosphine oxides absorb UV light between 380 - 410 nm. In this range, titanium dioxide is transparent, which enables the photons to reach the photoinitiator at the bottom of the film. The anatase form of titanium dioxide is especially suitable for UV-curing systems. Thus, white-pigmented UV coatings can be formulated with good hiding power and good through-curing properties.
Unfortunately, the majority of colored pigments don't exhibit this desired transparency in the relevant UV area. The competition between pigments and the photoinitiators for the UV light very often leads to insufficient through-curing properties. The result can be a coating that polymerizes at the surface but not at the bottom.
In order to achieve optimal curing properties, the photoinitiator has to be chosen accurately. Figure 2 shows the transmission of a coating based on a polyether acrylate containing different photoinitiators.
Due to the absorbance of acylphosphine oxides (Lucirin® TPO) in the range of 380 - 410 nm, the use of these acylphosphine oxides increases the usable UV wavelength area and leads to improved through-curing properties. Since the binder absorbs almost all energy below 300 nm, short-wavelength-absorbing photoinitiators act primarily at the surface of the film. Acylphosphine oxides are the preferred initiators to cure pigmented UV coatings due to their absorption characteristics.
The absorption spectra of certain pigments (Figure 3) can explain some basic curing properties:
Red: Relatively high transmission between 380 - 420 nm, but a high concentration of pigment is necessary in order to achieve good hiding power. As a consequence, UV absorption is increased and the coatings are difficult to cure.
Blue: Blue pigments are characterized by a high transmission in the relevant UV area and high hiding power. Thus, relatively good curing properties can be achieved.
Yellow: Yellow pigments have a low transmission level in the UV area. Additionally, these pigments have poor hiding power. Through-curing properties are usually poor.
Green: The green pigments have the lowest transmission level. Thus, green-pigmented UV coatings with good hiding power are minimally curable.
The absorption spectra of a pigment doesn't allow an exact prediction concerning the curing properties of a UV coating since the hiding power of the film has to be considered. Consequently, the pigment concentration also plays an important role. In our trials, the maximum pigment concentration that allowed acceptable film curing at a thickness of 30µm was determined. Therefore, the pigmented UV coatings were formulated with increasing pigment concentrations. These coatings were applied on a substrate (aluminum + adhesion primer) at a thickness of 30 µm, and the adhesion after curing was measured by cross cut. The maximum pigment concentration, which can be used in order to achieve good adhesion, was determined. The adhesion was used as a measurement for the through-curing properties.
The substrate we used had white and black spots, much like a chessboard. With the application of just one layer (30µm), the coating had only limited hiding power (high figure for the delta E). In the next step, we applied a second layer (2x30 µm = 60 µm) to increase the hiding power - this was done a total of four times (4x30 µm = 120 µm). It is not possible to cure a film thickness of 120 µm in just one step due to the limited through-curing. If we had a coating with perfect hiding power (i.e., an opaque coating) there would be no difference in color if the substrate was black or white. When the coating is not opaque there is a difference. This is why we applied the same coating in the same way over this black/white substrate. The results confirm the practical experience. Green and yellow pigments are much more difficult to cure with a satisfying hiding power compared to blue- or white-pigmented UV coatings (Figure 4).
In order to achieve a certain color shade, several combinations of pigments can be used. In the example of blue pigments, a method was developed that allows the determination of the most suitable pigment.
The pigmented UV coatings were applied on a black and a white substrate at a film thickness of 30 µm. The pigment concentration, which led to a DE = 5 between both films, was determined in order to have a comparable hiding power (Figure 5).
Only the P.B. 60, which is an Indantrone blue pigment, exhibits comparable values for both, the maximum pigment concentration and the concentration leading to DE=5. For the P.B. 16 as well as for the P.B. 15:3, which are phthalocyanine pigments, the maximum curable pigment concentration is below the concentration, which is necessary to achieve good hiding power. The row in front gives the maximum pigment concentration, which permits one to cure a film thickness of 30 µm. If the row in front is not as high as the row behind, then that means the cured film is not opaque, or, in other words, the delta E is higher than 5. When the row in front is of the same high number as the row in back, the delta E is 5. If the row in front is even higher, then the hiding power is stronger and the coating shows an opaque appearance. Therefore, the Indantrone P.B. 60 pigment would be preferred in UV coatings.
The UV energy emitted by the UV lamps has to match the absorbance of the photoinitiator. Compared to a conventional mercury lamp, gallium- and iron-doped mercury lamps emit UV energy in a longer wavelength region. Thus these lamps lead to improved through-curing properties in combination with Lucirin TPO, a photoinitiator for low-yellowing, white-pigmented UV-curable coatings, printing inks and clearcoats.
UV lamps emitting only UV-A and UV-V are also available as so called "sun-tanning lamps." Unfortunately these lamps cannot induce the polymerization of a UV coating under conventional circumstances due to strong oxygen inhibition. Under inert atmosphere - and thus in the absence of oxygen - such lamps are useful to cure UV coatings. The UV-A lamp used in the following trial was a Philips HB 406 sun-tanning lamp with a total power of 400 W. In order to reduce the oxygen inhibition, the coatings have been cured in an atmosphere of carbon dioxide. This process - curing of UV coatings under an atmosphere of carbon dioxide - is patented by BASF AG and licensed under the trademark Larolux™ that is owned by BASF AG.
A significant increase in maximum curable thickness of the coating was observed by using the UV-A lamps. The curable thickness of the coating cured with a conventional mercury lamp led to a maximum of ca. 70 µm. With the UV-A lamp, a significantly higher curable film thickness was measured. This is probably due to the higher penetration of UV-A light into the film (Figure 6).

UV Dual Cure
Another approach to cure pigmented UV coatings is to combine the UV technology with a second curing mechanism. The formulation of dual-cure systems, where the photoinitiated radical polymerization is combined with a polyaddition reaction, offers a solution. Hydroxyl-functional acrylic esters are combined with polyisocyanates, where the UV curing leads to very rapid curing at the surface, whereas the reaction between the OH groups of the UV binder with polyisocyanate leads to a lower crosslinked, but solid, film at the bottom (Figure 7).Since the polyaddition reaction is not as fast as UV polymerization, the full performance of these films can be achieved only after some hours or days. Nevertheless, depending on the processing parameters (temperature, film thickness, ratio between functional groups, etc), such coatings can be handled directly after the UV exposure but may have a rather short potlife.
Both functionalities, the unsaturated acrylic group and the NCO group, can be combined in one molecule. This allows the formulation of dual-cure coatings where the UV/NCO binder can be combined with polyols to formulate polyurethane coatings with the benefit of polymerizing the surface of the film using UV light (Figure 8).
As mentioned above, dual cure means the combination of two independent curing mechanisms. Thus, not only the combination of polymerization and polyaddition can be considered by formulating dual-cure coatings. The combination of physical drying and UV curing is a second approach. Therefore, UV dispersions can be used together with pigments. The photo-induced polymerization of such coatings will generate a gradient of double bond conversion. At the surface of the coating the combination of physical drying and UV curing will lead to a high resistance. Although in deeper layers the radical polymerization is minimized, good adhesion is provided due to the physical drying.
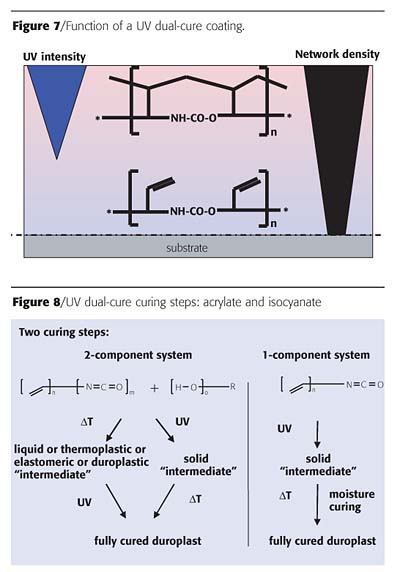
Conclusion
In this paper, an overview of different approaches to provide full-hiding, colored UV coatings is presented. The most convenient way to provide colored UV coatings is to use an UV monocure system, including pigment that is able to absorb the visible light (responsible for full hiding power) but not the relevant UV light (good curing properties). To optimize the utilization of pigments in UV coatings, BASF AG started a project to investigate pigments with respect to their behavior in UV coatings. The target was to offer a solution to formulate pigmented UV coatings with both optimal hiding power and satisfying through-curing properties. The UV monocure technology, however, has limitations in full hiding power and through-curing properties in certain color shades.The dual-cure combination of radiation curing and a second curing mechanism has been developed to overcome the limitations of the monocure system. The dual-cure system will generate new applications and higher market share for UV coatings in the future.
Report Abusive Comment