
MDF boards enter the preheat oven in the DVUV, LLC plant in Cleveland, Ohio.
When manufacturers that had been powder coating metal began to powder coat wood, it wasn't as easy as they thought it was going to be.
Wooden kitchen cabinets did not behave anything like steel cabinet doors might. The wood cracked and warped. The fibers were raised on its surface. The wood outgassed, heated nonuniformly and in general did not conduct heat very well. The problem was made even more complex when wooden boards were shaped and routed into all sorts of decorative, difficult-to-control shapes and sizes.
It was an all too common story: Great-looking test parts were made from simple squares of board, but when the same process and powder coating was used on the actual part, the finish was uneven, undercured and unacceptable. Part of the problem was in the process heating approach.
To powder coat heat-sensitive materials such as wood, it became clear that a different approach was needed. One process heating systems designer went back to the drawing board to develop an oven designed specifically for powder coating wood.
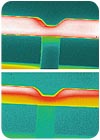
Thermal imaging showed that convection (top) had a more gentle heating effect that did not heat the surface as effectively but heated through the board, or its core, at the same time it heated the surface. Infrared heating (bottom) caused a more rapid increase in temperature, especially on the surface of the board nearest the heat source.
Pressed for Powder
Powder coaters primarily are interested in finding a way to effectively powder coat medium-density fiberboard (MDF). MDF is the mainstay of the kitchen and bath cabinet market as well as for ready-to-assemble and contract furniture. Although MDF is an engineered product (composed of resins, adhesives and other materials pressed together), it varies to some extent from supplier to supplier. The solution had to be flexible enough to account for the variations among board manufacturers.The manufacturers of powder-coated boards were looking for a solution that allowed faster process times as well. Using thermal imaging equipment provided by Flir Corp., Portland, Ore., lab engineers at the process heating equipment manufacturer studied the effects of both infrared and convection heating on wood panels. A series of cross-hatched test boards were developed to study the effects of heating edges and boards of varying thickness and geometry.
The tests revealed that each method had a markedly different effect on the way the MDF responded. Not surprisingly, the ordinary effects of each technology were evidenced. Infrared heating caused a more rapid increase in temperature, especially on the surface of the board nearest the heat source. Convection had a more gentle heating effect that, while more forgiving to the board's shape and size, did not heat the surface as effectively. But the convection process heated through the board, or its "core," at the same time it heated the surface. It became clear to the engineers that while each heating method had advantages, they also had limitations for processing powder-coated boards.
An infrared solution alone had a high probability of scorching some parts of the board and underheating other parts. Another problem with straight infrared was that it heated the surface more rapidly than the core and did not allow sufficient time for the board to outgas. Trapped moisture, volatiles and air would cause problems during the curing process, creating surface defects on the panels. Further testing also showed the board surface cooled dramatically, especially on the edges and in the routed surfaces. This was a particular concern because uniform heating is necessary at various steps in the powder coating process.
To properly powder coat an MDF part, it first needs to be preheated. Preheating the board does a few things:
- Allows the board outgas before the coating is applied.
- Allows moisture in the wood (typically in the 4 to 7 percent range) to render the surface conductive enough to attract the powder coating. Powder is applied electrostatically by charging the powder particles at the tip of the spray gun. The charged particles are drawn to the grounded part surface. With metal parts, this happens easily. But with wood, it is difficult to develop enough attraction without some moisture in the board. (In fact, some board manufacturers have taken to preconditioning boards in large, environmentally controlled rooms to ensure proper moisture content.)
- Allows powder to stick better to the surface. The fast-moving powder particle actually melts a bit on impact - a process referred to as impact fusion. The fused particle is more tightly bound to the panel than a powder particle clinging on by static electricity alone.
The benefit of controlling film thickness and coverage of applied powder is a functional concern and a cosmetic one. Functionally, thicker films may offer more wear resistance than a film that is too thin. Conversely, film that is too thick may be difficult to cure all the way through. But variations in film thickness also affect visual qualities such as the gloss of the coating and how smooth the final coating will appear.
Proper preheating is key to good-looking, properly functioning coatings. And a key to uniform film thickness is uniformity of board temperature. Although the powder booth may be only a few feet away from the preheat oven, the part cools during the trip. In practice, there often is a minute or two of transit time. By the time the part arrives in front of the powder guns, variations in temperature are more extreme than they were in the oven. That is why careful control of the preheating environment is a must for powder coating wood.
Experiments were conducted using a wide selection of infrared sources. Both gas-powered and electric units were tested as well as sources ranging from medium to very short-wave designs. Testing showed that for curing powder coatings on MDF, the best overall performance came from medium-wave infrared panel heaters. The heaters were selected to provide easy maintenance and protection against dirt and contamination from materials in their construction.
Although the infrared sources were capable of reaching surface temperatures around 1,200°F (649°C), experimentation indicated that they would be run at lower temperatures. The controls system utilizes PID temperature controls and zero-cross SCR technology to provide needed process control around tight, repeatable tolerances. The controls architecture also provides the operator the ability to run stored recipe profiles tailored around different products and different powder coating materials.
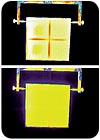
A test panel with a routed cross hatch in it is removed from a gas-fired convection oven (left) Infrared thermography reveals as much as 40°F temperature variation. The same test part heated less than half as long in a specially designed hybrid oven for wood (right) produces almost no temperature gradient.
Hybrid Infrared/Convection
The nature of hybrid infrared/convection ovens is different than if infrared is used as a traditional boost or gel oven. In this hybrid design, the infrared and convection work together rather than independently to provide greater speed and greater uniformity.These process benefits attracted DVUV, LLC, a furniture manufacturer and custom coater in Cleveland, Ohio. For DVUV, the process heating equipment manufacturer supplied a hybrid system consisting of a 1.5 min preheat cycle and a 1.5 min melt/flow cycle before a UV curing chamber. Compared to processes requiring as much as 8 min each for these steps, the hybrid oven provided better performance in a smaller footprint. Boards come through the system more than 10 min faster, so there is less work in process and fewer hangers to buy and clean.
Mike Knoblauch, president of DVUV, was drawn to UV powder coating his product because of his concern over the effects of higher temperatures. "The core of the wood is degraded with heat," Knoblauch explains. "Keeping the core temperatures down and controlling the temperature of the board is critical to integrity of our product."
Some early concerns over the relative operating costs of hybrid ovens vs. conventional designs also tipped the scales in favor of hybrid technology. In operation, the ovens are efficient and the benefits of having a large air mass heated with convection allows the infrared temperature controllers to operate smoothly when it comes to changes in the system such as changes in the line loading or ambient air temperature. The convection acts as a buffer to keep the infrared system from cycling as much as in infrared-only designs.
Powder coating wood promises to open new markets for manufacturers and suppliers of equipment and coatings. The advantages powder has offered other manufacturers for decades finally are available to new markets. Many problems will undoubtedly need to be solved as new applications arise, but the innovative use of process heating technologies can help overcome these obstacles.
Editor's note: This article is reprinted with permission from Process Heating magazine.
For more information about Nutro's hybrid ovens, call (440) 572-3800 or visit www.nutro.com.
For information on reprints of this article, contact Jill DeVries at devriesj@bnpmedia.com.
Report Abusive Comment