

Figure 1. MDF production and consumption are growing, providing the potential for an increased use of powder coatings in this field. (EU: Europe; G: Germany. Source: EPF.)
In recent years, the development of ultra-low bake (ULB) and ultraviolet (UV) powder coatings for these substrates has allowed a dramatic reduction or even elimination of these traditional systems, resulting in new benefits for manufacturers. The woodworking industry in particular has increasingly begun taking advantage of UV and ULB technology to switch to powder coatings. As a result, new powder formulations are being developed that fulfill the needs of the growing MDF coating market (see Figure 1). The number of MDF powder coating lines has been increasing for several years, and this trend seems destined to continue in the future.
Generally speaking, powder coatings are “solventless” and do not contain or emit volatile organic compounds (VOCs). This characteristic makes them inherently user-friendly and easy to recycle (no waste treatment is required). UV and ULB powders place an extremely low thermal load on the substrate and can be handled immediately after curing. Unlike with liquid coatings, it is often possible to reduce or even eliminate intermediate sanding steps.
The use of ULB/UV powder coatings permits a greater freedom of board design (for example, allowing curvilinear shapes and seamless edges), while offering the flexibility of colors and textures not available in foils or laminates. Furthermore, these coatings allow a reduction in costly processes such as edge banding.
However, achieving a high-quality finish with this new technology requires choosing the right MDF type and powder, as well as the correct technical support and curing line.
MDF Suitability
Medium density fiberboard is an engineered wood composite used widely in the woodworking industry. It is manufactured by a dry process and available in thicknesses from 1.8 to 60 mm. The typical density is between 650 to 800 kg/m3.The choice of MDF type is as important as any other parameter because it can critically affect the coating performance. Characteristics such as “coatability,” deep routing, sanding, resistance to edge cracking, conductivity and degassing are all affected by the kind of wood, fiber, pretreatment, glue resin, additives and pressing process used to create the MDF substrate. There is no one “right quality” of MDF for powder application, but some types are more suitable than others. In general, the higher grades work best because they are more consistent than the lower grades. MDF suppliers usually can recommend a suitable choice.
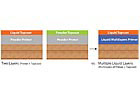
Figure 2. A two-layer ULB or UV solution is recommended to obtain smooth finishes.
ULB and UV Powder Coatings
ULB and UV powder coatings are specially formulated to allow a fast, low-temperature cure, which minimizes the thermal stress to the MDF. They are available in a range of finishes, including textured/smooth finishes (with a high or low gloss), clearcoats (smooth and textured) and pigmented or clear sandable primers.ULB and UV fine-textured finishes can be obtained in a variety of colors and can be used in a one-layer application on even the most complex shapes to achieve the same look as multiple coats of a liquid finish. However, a two-layer solution is recommended to obtain smooth finishes (see Figure 2).
Powder primers are available both in UV and ULB systems. They are easy to sand and offer excellent adhesion with the topcoat. Usually, a UV powder is recommended as a topcoat because of its smooth finish and high hardness, which makes it more scratch and chemical resistant than ULB powders. ULB powders also tend to exhibit more orange peel on the surface.
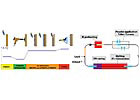
Figure 3. An overview of the UV powder coating process.
UV Powder Coating Process
The process of coating substrates with UV powder is divided into four different steps: preheat, powder application, melting and leveling, and curing (see Figure 3).The preheating step can be skipped, depending on the conductivity and porosity of the substrate. Substrates with good conductivity will be inherently suitable for powder application, and there will be no need to apply a liquid primer or preheat the substrate. The temperature at the substrate’s surface should never exceed 130°C (266°F).
The powder is applied at room temperature with automatic spray equipment (corona and/or tribo guns) and is then passed through a convection or convection plus infrared (IR) oven for melting (generally two minutes at 120°C/248°F).
After the powder has been melted, it is exposed to UV lights with a suitable wavelength (between 100 and 450 nm) and intensity to initiate the polymerization.
When the photoinitiators in the coating are exposed to UV light, they cleave into free radicals that then initiate addition polymerization within the unsaturated groups of the binder system. The whole reaction is completed in a few seconds.
ULB Powder Coating Process
Generally, ULB powder coatings use a standard powder coating chemistry. Since they are primarily used for interior applications, they are commonly formulated in an epoxy polyester binder system. The choice of the catalyst in these formulations is critical for low bake applications, as the board temperature cannot exceed 140°C (284°F).The primary advantage of the ULB powder process is that it doesn’t differ from that of normal thermosetting powders. It consists of a preheating stage (or primer application if required) and powder application (at ambient temperature), followed by melting/curing in a convection and/or IR oven. The processing time takes between 10 and 15 minutes.
During the installation of a ULB line it is important to consider the configuration of the IR lamps used to melt and polymerize the powder. Heat must be applied homogeneously to the entire board to avoid degassing problems or undercuring.
Current research efforts are focused on achieving high-performance ULB products with superior mechanical and chemical properties, ever-shorter curing schedules and compliance with furniture standards even under severe conditions.
UV or ULB: Which is Better?
The choice of whether to use UV or ULB powders primarily depends on the requirements of the application. Generally, ULB powders are recommended for lower-performance end uses (e.g., TV stands shelves, etc.) as they meet the furniture standards for “general use.” Also, compared to UV powder coatings, ULB powders offer a broader color range and a lower cost per square foot coated. Some colors, such as deep yellows, are difficult to cure with UV light, and there are also difficulties in curing very thick coatings. Moreover, while ULB powders can be used successfully on complex 3D shapes, hidden areas will remain uncured when using UV powders.UV powders are generally recommended where high performance is needed. In offices and kitchens, furniture generally must meet the standard for severe usage. The heating cycle used to melt a UV powder is milder and, unlike that of a ULB powder, separate from the curing process. This inherent latency means that smooth finishes are much easier to obtain. Consequently, the choice of the right MDF (in order to reduce deformation of the board and edge cracking) is less critical for UV powders, allowing the use of a lower-cost substrate. The next generation of UV powder offers superior mechanical and chemical properties.
This article was written by the following individuals: Ernesto Marelli (011.33.477.9670.00 or ernesto.marelli@fra.dupont.com), R&D project leader at DuPont Powder Coatings France S.A.S.; Paul Dinning (Paul.Dinning-1@gbr.dupont.com), R&D project leader, and Steven Hobbs (Steven.Hobbs@gbr.dupont.com), technology supervisor at DuPont Powder Coatings UK; Oriol Aixala, R&D project leader, and Helene Bolm (Helene.Bolm@swe.dupont.com), technology supervisor, at DuPont Powder Coatings Scandinavia; Dr. Carlos Rodriguez Santamarta (Carlos.Rodriguez-Santamarta@esp.dupont.com), technology manager for DuPont Powder Coatings Europe; and Dr. Volker Rekowski (Volker.Rekowski@deu.dupont.com), global quality manager for DuPont Powder Coatings.
For more information about powder coatings, visit www.alesta.dupont.com.
Report Abusive Comment