Parylene Coatings and Applications
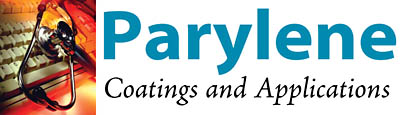
Parylene (poly paraxylylene) is a generic name for polymers that belong to a unique chemical family and are used as conformal coatings in protective applications. The coating process exposes product to the gas-phase monomer at low pressure. Through vacuum deposition, parylene condenses on the object's surface in a polycrystalline fashion, providing a coating that is truly conformal and pinhole free.
Compared to liquid processes, the effects of gravity and surface tension are negligible, so there is no bridging, thin-out, pinholes, puddling, run-off or sagging. The process takes place at room temperature so there is no thermal or mechanical stress on the product. Parylene is physically stable and chemically inert within its usable temperature range. It provides excellent protection from moisture, salt spray, corrosive vapors, solvents, airborne contaminants and other hostile environments. Parylene provides coatings with a friction coefficient as low as 0.25 to 0.30.
These coatings are formed by the polymerization of para-xylene, which is deposited on the substrate through vacuum deposition. Thus the coating is uniform, thin, stress free and has very good mechanical properties. The coating is applicable for substrates where protection is more important than decoration.

The parylenes are polymers of the p-xylenes and their substitutions, some of which are Parylene N, Parylene C and Parylene D. The basic member of the poly-p-xylylene series is Parylene N - a completely linear, highly crystalline material. The other commercially available members (C and D) originate from the same monomer and are modified by substitution of one or two aromatic hydrogens with chlorine atoms.
Parylene Deposition Process
The parylene polymers are deposited from the vapor phase by a process that is not line-of-site, and all sides of an object to be encapsulated are uniformly impinged by the gaseous monomer and uniformly coated. This characteristic is responsible for the truly conformal nature of the coating. The deposition process consists of three steps:
- Sublimation under vacuum at approximately 120 °C of the stable crystalline dimer di-p-xylylene, to produce vapors of this material.
- Pyrolysis of the vapors at approximately 650 °C to form gaseous p-xylylene, the reactive monomer.
- Deposition and simultaneous polymerization of the p-xylylene to form poly(p-xylylene) or parylene.
The parylene process involves several aspects. After proper cleaning, activation and masking, the product to be coated is placed in the deposition chamber. The product remains at room temperature during the coating process. Dimer is placed in the glass tube at the opposite end from the deposition chamber in an aluminum foil cup called a "boat". The coating thickness is determined by the volume of dimer placed in the boat.
An end cap is then placed over the tube and the process started. The vaporizer radiant heater cycles on and off with a pressure safety interlock to ensure safe operating limits; the dimer changes from a solid to a vapor and the molecules move down the tube by virtue of the reduced pressure at the opposite end.
The dimer moves into the pyrolysis zone, which is at 680 °C, and the high temperature cleaves the dimer into two divalent radical monomers. The monomer molecules enter the deposition chamber and re-form as a long chain polymer on all surfaces within the chamber (Figure 1).
Studies show each molecule makes an average of l0,000 collisions and, because of the short mean free path of the molecule vapor (less than l M.M.), the coating forms slowly and uniformly over surfaces with both sharp edges and deep crevices with no pin holes.
A cold trap is used between the deposition chamber and the vacuum pump. The cold trap use is twofold:
It prevents parylene molecules that have not deposited in the chamber from getting into the vacuum pump.
1. It prevents oil molecules from "back streaming" into the deposition chamber.
2. The deposition process provides the following features.
- Coating thicknesses from 0.10 micron to 76 microns can be applied in a single operation.
- Deposited at a typical rate of 5 microns per hour upon process equilibrium.
- No catalysts or solvents are required.
- A cold trap allows for liquid nitrogen or mechanical chiller cooling, preventing parylene from depositing in the vacuum system.

Important Parylene Features
Conformality and Thickness UniformityIn contrast with liquid coatings applied by spraying, dipping or brushing, parylene does not pull away from edges or exhibit meniscus forces. Compared to liquid coatings where flow between and beneath components tends to glue them to one another, parylene does not bridge even in apertures as narrow as 7 microns (0.25 mils) and has the ability to penetrate beneath and around closely spaced components. Because the buildup is consistent and uniform, physical and electrical protection can be achieved with a substantially thinner layer than conventional coatings, which often require heavier applications to overcome coating imperfections.
Another important advantage of parylene is the fact that it can be deposited in very thin layers: 0.1 to 50 microns (0.004 -2 mils), while the typical thickness of conventional coatings is within 25 to 250 microns (1-10 mils).
Stress Free
Since the polymerization of the film takes place on the substrate surface at room temperature, there is no thermal or mechanical stress introduced during application, hence original performance parameters of coated subjects are basically unaffected. Unlike conventional coatings, especially acrylic and silicone based, which can introduce stresses to the electrical components during the curing or drying cycles, parylene can be stretched up to 200% before breaking and retains the ability to remain flexible over a wide temperature range. For instance, in the coating of ferrites, the elasticity of parylene avoids any changes in the magnetostrictive properties of the ferrite material.
Electrical Properties
Overall, parylene's electrical properties are superior to those of conventional coatings: it has high dielectric strength and volume resistivity and low dissipation factor and dielectric constant. An important characteristic is the fact that its dielectric constant and dissipation factor are practically insensitive to increased frequency. Its extremely high dielectric strength combined with its electrical stability in various media provides unique insulating property. The dielectric constant and dielectric losses are low and unaffected by absorption of water vapor. Its volume and surface resistivities are advantageously high because of the purity, low affinity to moisture and in particular its freedom from trace ionic impurities present in conventional coatings.
Superior Barrier Properties
Parylene provides exceptional corrosion protection from moisture, salt spray, corrosive vapors and other hostile environments. Its water vapor transmission rate has been found to be significantly lower than most conventional coatings. With respect to migrating ionic species, parylene coatings have been proven to act as a barrier to extractable metals which otherwise will contaminate substrates.
Impressive Mechanical Strength
Since it has high tensile and yield strength, parylene is used for encapsulating microcircuits because it increases the pull strength of wire and lead bonds, face bonded chips and conductor bridges and, therefore, contributes significantly to device integrity. Since its specific gravity is low, the parylene layers are typically lighter than most other functional coatings.
Thermal Stability
Parylene coatings remain stable at continuous temperatures as high as 130 °C in air, or 220 °C in the absence of oxygen. It has good mechanical properties from -200 to 275 °C.
Chemical and Solvent Resistance
Due to its unique molecular structure, the parylene polymers are practically insoluble in all known organic solvents up to 150 °C and very resistant to most of the inorganic reagents including strong acids and alkali. They are also effective barriers to corrosive agents.
In contrast, some of the polymers used in conventional conformal coatings, especially the ones based on acrylics and silicones have relatively low to moderate chemical resistance and some, such as silicones, are permeable to corrosive chemicals.
Dry Film Lubricant
Inherent excellent dry lubricities, as indicated by coefficient of friction measurements, make parylene a valuable asset as a dry film lubricant, particularly as a coating for surgical instruments. Compared to fluoropolymers, parylene also has the ability to provide wear and abrasion resistance.
Sterilization
Due to their thermal and chemical resistance, parylene coatings can survive the conditions of many common sterilization techniques (e.g., autoclave, radiation, ethylene oxide).
Adhesion
In principle, its special chemical composition causes parylene to be more difficult to bond to various substrates versus the conventional coatings. However, after extensive R&D efforts we are able to develop special techniques that ensure a high degree of adhesion between parylene conformal coatings and the surfaces of the electronic and electrical devices.
Biocompatibility and Biostability
Biomedical applications are possible due to parylene's ability to offer very thin, pinhole-free, uniform and conformal coatings, which have resistance to many chemicals and are also compatible with bodily tissues and fluids. Parylene is effective in sealing the micro porosity of substrates that could otherwise trap and retain contaminants. Deposition of a thin layer of parylene over a cytotoxic surface can render it traumatic to cells. Parylene is not vulnerable to corrosive aqueous implantation environments; hence it is regarded as a likely candidate for implantation devices.
Repairability
Since it is so different in chemical composition, coating technique, applied thickness and surface characteristics from the conventional resin types, parylene presents a unique set of circuit repair issues as well as offers certain benefits. For example, acrylic-based coatings can be easily removed from circuit boards with proper solvents, using selective spot or overall dip exposure. However, this ease of repair is offset by the vulnerability of the acrylic material as well as of the material used to fabricate the circuit boards to potential solvent contaminants. Further, coating removal yields a contaminated solvent residue that is flammable and requires proper disposal. Also, the recoating of acrylic-coated boards must be done in a special booth that is equipped to handle organic volatiles.
Urethane coatings are not vulnerable to solvents, and their removal is generally accomplished by thermal softening followed by physical removal using special tools or by microblasting. However, caution must be exercised in the case of heating or burning used to remove them, because toxic fumes may be generated. Epoxy coatings present the same removal issues as the urethane coatings, and are even more difficult to remove because they are more compact and have even higher hardness.
Silicone coatings are relatively easier to remove because they are softer and are relatively vulnerable to some organic solvents. However, much attention has to be given to the silicone's known tendency to migrate and contaminate the adjacent manufacturing areas and negatively affect the bonding processes.
In contrast, parylene resists all known organic solvents, and its melting or burning temperatures generally exceed that of plastics that form the circuit's structure. Typically, parylene can be removed by the following techniques (in some cases helped by heat softening): mechanical abrasion or air microblasting with a very focused strong stream of particles, incision and suction, plasma etching, or by excimer laser emission
Particle Immobilization
Parylene assures circuit integrity, preventing mobility of loose solder, wire particles or other mobile debris left from manufacture. Pressed powder parts, ferrites, ceramics, corrosive metals, glass and epoxy particulates can be positively stabilized.
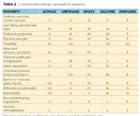
Comparison of Parylene with Other Coatings
Table 1 compares the physical properties of Parylene N, C and D. Table 2 compares the main properties of the conventional coatings: acrylic, urethane, epoxy, silicone and parylene in relation to the parameters that most affect the proper function of electronic and electrical devices. The rating used are: E= excellent, VG= very good, G= good, M= moderate, L= low.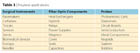
Parylene Applications
Due to their unique properties and excellence, the parylenes can be used in a number of places, but they are costly compared to other types of coatings. Some of the important parylene applications are shown in Table 3.
Medical
Protective coating of a biomedical surface may be required for a number of reasons, including physical isolation from moisture, chemicals and other substances, surface passivation, electrical insulation, biocompatibility, immobilization of microscopic particles and reduction of friction. In short, the coating must:
- resist water and ions, notably sodium;
- adhere to the probe surface;
- provide insulation along the interface;
- be as thin as possible;
- frequently withstand high electric fields;
- be nontoxic and sterilizable;
- be flexible and have a low coefficient of friction; and
- function reliably.
The choice of coating materials is dictated by many factors, including biocompatibility, mechanical characteristics, electrical properties and biostability in saline environments. For all these applications, an extremely consistent coating thickness is critical and the coating must have as little impact as possible on component dimensions as well as on its main features. The demand made on medical coatings varies greatly, depending on the form and function of the substrate; in most cases, these requirements cannot be met with conventional coatings.
Parylene is a vacuum-deposited polymer that can be applied to nearly any biomedical substrate. The coating is stable, causes minimal or no change in the component response characteristics and isolates surfaces electrically and chemically from body fluids, moisture and ionic contaminants. It is deposited with equal thickness on all surfaces, in crevices and on edges.
Since it is formed from a pure molecular precursor (a monomer gas), the parylene-based coatings have no contaminating inclusions. Because the conversion from monomeric gas to polymer film is direct, no solvents, plasticizers, catalysts or any other ingredients are used. The resulting film has very low thrombogenic properties and low potential to trigger an immune response. Parylene has been shown to be highly resistant to the potentially damaging effects of corrosive body fluids, electrolytes, chemicals, proteins, enzymes and lipids.
The film also forms an effective barrier against the passage of contaminants from a coated substrate to the body or surrounding environment. Unlike liquid coatings applied by spraying, dipping or brushing, parylene does not pull away from edges, bridge between adjacent surfaces or exhibit meniscus forces. And because buildup is consistent and uniform, physical and electrical protection can be achieved with a substantially thinner layer of parylene as compared to conventional coatings, which often require heavier applications to overcome coating imperfections. Since there is no cure cycle with parylene, substrates are not subject to cure forces, solvents, liquid-phase effects, or elevated temperatures. Because substrates are placed under vacuum prior and during coating process, any volatiles that might be present are extracted.
Catheters, Mandrels
Catheters, being molded parts, can be parylene coated to improve lubricity. This will help in reducing the chatter of insertion or removal that is experienced when using a non-coated catheter. Parylene also affords barrier protection against biofluids. Mandrels, being precise wire forms used in the production of catheters, are coated with parylene for the ease of releasability of the newly formed catheter from the forming mandrel.
Cardiac-Assisted Implant Devices
Because of parylene's excellent dielectric properties, not only are pace makers and implantable defibrillators protected against corrosive effects of biofluids, but the metal cases of these devices are also isolated electrically. Other applications include pressure sensors, medical instrumentation printed circuit boards, ultrasound transducers, guide wires, needles, epidural probes and elastomer products (silicone, latex gasket and seals), wherever lubricity and barrier protection is required.
Electronic and Electrical
Parylene has been successfully used as conformal coatings in many electronic and electrical applications: printed circuit boards; hybrid circuits, microelectronics; ferrite cores and bobbins; miniature servo motors; capacitors; small rotors and stators; pressure transducer thermistors; relays; memory heads; automotive sensors; memory cores; potentiometers; disk drives; implanted bioelectrodes; thermocouples; switches; semiconductors; and computer keypads. Other successful applications include such diverse end uses as optical devices, radiography equipment, digital displays, nuclear energy equipment, instruments and space equipment.
Circuit Boards
Parylene was developed over 30 years ago primarily to provide a conformal coating for printed circuit boards. Parylene films ranging from 0.25 to 1.5 mils in thickness provide a barrier, which is equivalent or superior to 2 to 6 mils of other conventional coatings. Because parylene is in a molecular state and builds from the surface up, board components are coated evenly and consistently, thus electrical protection can be achieved with a thinner layer than that of conventional coatings. The dielectric constant and dissipation factor are practically insensitive to changes in frequency. Given its resistance to humidity, barrier properties, physical and thermal properties and its unique molecular structure, parylene is practically insoluble in all known organic and inorganic solvents including strong acids and alkali. Parylene proves to be an effective barrier to corrosive agents and does not out-gas. It is an excellent choice when it comes to conformally coating printed circuit boards for military and aerospace applications.
Rubber
Because parylene is deposited as a gas at the molecular level, it yields a truly conformally coated part with like thickness on the flat surface area, over corners, and in, on and around the internal dimensions of holes. No matter the size or shape of the elastomer application, parylene film conforms to the surface features. With parylene film's surface adhesion and elasticity, the coating can handle substantial elongation of the elastomer part without any fracturing or breaking of the surface adhesion of the film from the substrate bond. Rubber keyboard applications using the parylene coating process will remove the elastomer tack but will also protect the keyboard against dirt, oils, petrochemicals and solvents while also protecting printed legends from wear. In addition, the appearance of the keyboard is also preserved. Rubber and silicone parts are usually coated in a horizontal chamber or tumbler. This exposes all surfaces to the parylene monomer. This proves to be cost effective, while offering superior quality. No fixturing is required, and because curing occurs before the film is deposited, the parts are not exposed to high temperatures and the integrity of the part is maintained.
Wire Wound Devices
Parylene was originally developed to protect printed circuit boards from salt spray and high-humidity applications. Several new markets and applications were found where the traditional spray or dip coatings were not able to perform to spec. One of these new application areas was the wire wound device market which includes magnets, wire-wound ferrite cores and powdered ferrite cores.
Parylene uses a vapor deposition process performed in a vacuum that builds from the surface outward. This produces a pinhole-free (pinhole-free @ .6 micrometer or higher) conformal layer of uniform thickness. Surface tension causing the pulling away of sharp edges, bridging or thin out when conventional coatings are used in the curing process does not occur with the parylene process. Along with a low-temperature no-cure process, parylene offers outstanding insulation and high dielectric constant properties over a wide range of frequencies. Parylene also eliminates abrasion damage to the wire in the winding process along with uniform coating thickness. Unlike the variance of thickness (bridging, shrinking, thin out and pinholes) with conventional liquid, spray or brushed on coatings, parylene gives a maximum winding window. Parylene does not impart magnetostrictive or permeability problems that may be encountered with conventional varnish impregnation. With parylene's low water vapor transmission properties it provides excellent corrosion protection. Again, because parylene is a batch process where many parts can be coated at a time in a tumble system, parylene offers a cost-effective solution for many applications, especially the least-expensive option for coating electronics.
MEMS
MEMS (Microelectromechanical System) represents the highest level of micro-integration yet devised. MEMS integrates motion, light, sound, molecular detection, radio waves and computation. All converge on an unusual chip array, many times smaller than a grain of sand.
Developments in the MEMS arena show that MEMS can be used as a DNA detector; it can sense if a DNA strand is defective. Some devices are so small that they could be injected into the human body. The day may come when micro-robots, or "nanobots," travel through the body to clear arteries and make repairs, borrowing a scene from the classic 1960s science fiction movie Fantastic Journey. MEMS could also find military uses suggested by science fiction writers like Dean Smith who tells of battles between earth nanobots and alien micro-machines in The Tenth Planet.
There are only a handful of MEMS products on the market, but we will see a large variety come to commercial fruition during the upcoming decade. Examples are accelerometers, used with virtually all modern automotive airbags, and micro-mirrors (MOEMS) used in some digital projectors.
Parylene with MEMS
Friction and Stiction
A common problem with the development of MEMS and MOEMS is the problem of friction or stiction. Friction is common to all mechanical products, however in MEMS, traditional lubricants are not practical. Stiction is a surface effect problem that is somewhat unique to micro mechanical devices. The tiny MEMS elements, once they make contact with one another, are held together by surface tension and atomic-level forces (similar to static electricity).
Parylene - a Friction, Stiction Solution
Many experts agree that a solution to the friction/stiction problem lies in an organic coating with low surface energy and, perhaps, hydrophobic properties. The coating would need to be very thin, and this is the realm for vacuum coating technology.
Given these parameters, a logical solution is parylene. First, it is important to say that only a limited amount of study has been done in this cutting-edge area of technology, but SCS is working with the industry to test several parylenes including a newer non-stick fluorinated product.
This class of polymer has been used for decades on a variety of applications, especially those involving the protection of electronic devices and circuitry. CVD is used to form an insulating thermoplastic coating with a high degree of chemical inertness, absence of pinholes and perfect conformity to the topography of the surface applied. Coefficients of friction range from 0.25 to 0.33 so that the lubricity is close to that of Teflon. In deposition, the parylene gas polymerizes spontaneously on the surface of coated objects that are at ambient temperature with no stresses induced initially or subsequently. There are no cure-related hydraulic or liquid surface tension forces in the process. The mean free path is only about 0.1 cm so that sides and small openings are coated. A typical rate of 0.2 m or less provides precise thickness control. Polymerization occurs in crevices, under devices, and on exposed surfaces at about the same rate to give a very uniform film. Parylene coating thickness can be as low as 100 Angstroms.
Parylene Issues
There could be some issues with parylene according to the few researchers who have experimented with the organic coatings on MEMS. Thin coatings gave good anti-stiction results before packaging, but control may be difficult. Anti-stiction performance was apparently good using standard parylene but sealing the hermetic package can cause degradation.
Two recommendations were given for parylene on MEMS devices: a well-controlled deposition process for very thin coatings and higher temperature stability to withstand ceramic packaging processes.
Conclusion
Vacuum-deposited parylene film can improve the surface properties of rubber substrates in ways that cannot be achieved with other materials or processes. Its application is controllable, and the process provides consistent, repeatable cost effective results. With the swings in defense spending, many former defense company engineers have entered the commercial sector, where demand for high-quality and low unit cost go hand in hand. Combine this with the expanding electronics market, in everything consumers buy, and the need for a high-quality conformal coating arises. With the increased demand comes an increase in the volume of conformal coating, and with competition, a decrease in price. Even the once touted "expensive" parylene has become competitive. Gone are the days of only one supplier, who demanded users purchase a license and pay royalties. Now, with three suppliers in the world with materials listed on the Q.P.L., competition and demand has lowered the price of raw material to about one half its original cost when Union Carbide had patent rights prior to 1986. Parylene job shops and many former in-house defense contractors have made the successful transition from the defense to the commercial and medical markets. The special demands placed on conformal coating of commercial electronic and medical products, such as true conformal coating, pinhole-free moisture barrier, high dielectric strength, solvent/reagent resistance and biomedical compatibility have made parylene the conformal coating of choice. Applications, ranging from the circuit board in a home flat iron to surgical instruments, meet and exceed their performance specifications by incorporating the use of parylene conformal coating.
As the demand for the use of parylene coating rises, the production and raw material will increase, and competition will drive cost down. One general manager of a leading parylene coating job shop predicts the market will grow 25% for every drop of $100.00 per pound of raw material.
Looking for a reprint of this article?
From high-res PDFs to custom plaques, order your copy today!