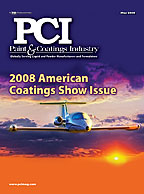
Corrosion is a terrible waste of energy. During the last decade there has been increased awareness of how the coming energy crisis will affect industry. Buyers of protective coatings will soon find they have less money for painting after adjusting for rising energy costs. The following paper explains how advanced maintenance programs, developed by the airline industry, can reduce energy waste and lower costs for complete life coating systems.
The Problem
On January 2, 2008, oil reached a record price of $100 per barrel. Oil, coal and natural gas are fossil fuels and produce 85% of the world’s energy needs. Currently, the United States uses 20 million barrels of oil per day. This represents 25% of the world’s oil production. When fossil fuels are converted into energy they produce carbon dioxide, a green house gas. Each year, 6.1 billion metric tons of carbon dioxide are added to the atmosphere. Greenhouse gases prevent sunlight from being reflected back into space, causing global warming, severe climate changes, rising sea levels and diminished land usage patterns. For the foreseeable future, experts agree that no combination of alternative technologies will replace the worlds’ dependence on fossil fuels. Corrosion costs the U.S. economy over $500 billion per year in direct and indirect costs. This represents 6% of the Gross Domestic Product valued at $8.79 trillion. Using a simple comparison, corrosion costs the United States over 5 billion barrels per year.Advanced Maintenance Technologies
In the early 1960s, the crash rate for jet aircraft was alarmingly high. In an attempt to reduce crash numbers American Airlines’ senior management, with the approval of the FAA, began intensive engineering studies on in-service aircraft. The studies proved that the major assumption that every component in first-generation jet aircraft had a specific “lifetime” of reliable service, after which it had to be repaired or replaced in order to prevent catastrophic failures, proved wrong in virtually every specific case.Many of the discoveries made by the airline revolutionized the maintenance discipline for physical assets. This has been the basis for a new generation of highly efficient maintenance programs including Predictive and Reliability Centered Maintenance (RCM). The following is a discussion on how Predictive and RCM maintenance programs can be adapted to protective coatings.
Predictive and RCM Programs
Currently, industry recognizes four major maintenance classifications: reactive, preventative, predictive and reliability center maintenance (RCM).Reactive Maintenance:an asset is allowed to operate to failure before repairs or replacements are performed. The practical approach to painting is based on reactive maintenance. It is estimated that 55% of all industrial repairs and replacements are based on reactive maintenance.
Preventive Maintenance:repairs or replacements are scheduled at predetermined time intervals. Work is based on performance estimates and operational histories. Ideal/optimum maintenance painting is based on preventive maintenance. It is estimated that 31% of all industrial repairs and replacements are based on preventive maintenance.
Predictive Maintenance:maintenance is scheduled based on current asset condition. Predictive maintenance relies on the precise evaluation to detect minor changes in operational performance. Repairs or replacements are planned before major performance changes occur. It is estimated that 12% of all industrial repairs and replacements are based on predictive maintenance.
Reliability Centered Maintenance (RCM):This maintenance program utilizes preventive and predictive maintenance techniques with root cause analysis. RCM is based on accurate inspections to determine when a component has reached a predetermined unacceptable condition. At this point, repairs or replacements are performed to prevent a more costly failure from occurring. The identification of wear stressors, by root cause analysis, can aid facility owners in improving future maintenance operations through design changes or modifications. The following saving comparisons can be made:
• 0% – Reactive
• 25% to 35% – Preventive
• 45% to 55% – Predictive
• 60% to 80% – Reactive Centered Maintenance based on root cause analysis.
Maintenance is a proven way to reduce whole life corrosion damage. Traditionally, there are two standard approaches to maintenance painting. One is to begin touch up as soon as the topcoat begins to wear down. This is the ideal/optimum approach. The second is to schedule maintenance painting after visible rusting is found. This is the practical approach.
Protective Coatings NDT
Protective Coatings NDT is a highly efficient maintenance program that has been developed to provide continuous corrosion protection for equipment and steel structures throughout their complete service life. PC/NDT is based on the principals of non-destructive testing where fluorescence and black light illumination are used to locate surface defects. PC/NDT has the potential to remove the cost, production and technical barriers that prevent the coating industry from using predictive and RCM maintenance technologies.PC/NDT is formulated to fluoresce at 365 nanometers (nm); a slightly higher energy level than visible light on the Electromagnetic Energy Spectrum (EMS). Fluorescence produces an Enhanced Visual Signature (EVS) that produces a highly visible contrast between non-reactive (NR) substrates or standard NR coatings. EVS increases a worker’s ability to locate, define and repair coating defects found during the original application or later maintenance recoating. PC/NDT is the only quality control process that has an inspection rate comparable to the rate of modern spray applications. Line of sight inspections can be performed as fast as the hand can move a black light and as fast as the human eye can follow.
The average worker with 20/20 vision can usually locate a coating defect 50 microns in size in good lighting and given enough time for a thorough surface inspection. The same worker using NDT/EVS can locate a defect 10 microns in size or smaller even in low light or during production painting operations.
NDT/EVS inspections are the key to PC/NDT corrosion management programs. By integrating quality control into the original coating formulation, PC/NDT can provide more science than guesswork for determining exactly when and where maintenance is required. As the topcoat begins to wear away and defects are located by black light, maintenance is relatively inexpensive and much more effective.
The two major advantages for PC/NDT are the virtual elimination of catastrophic coating failure and crisis condition recoating. This is made possible by the ability of no-contact, black light inspections to scan large surface areas in short periods of time and detect minor changes in surface condition. In many cases, black light can replace traditional inspection tools for scheduling maintenance recoating. Additional advantages include:
- Increased equipment and structure life;
- Reduction in corrosion related repairs, downtime and replacement cost;
- Improved performance and operational readiness;
- Improved worker safety and morale;
- Reduced waste and disposal costs;
- Reduced VOCs and negative environmental impact;
- Improved remanufacturing and recycling potential;
- Lean Engineering: A reduced need to over-design products to resist corrosion;
- Reduced energy usage for corrosion control maintenance programs; and
- Surface Maintenance Technician. The savings produced by PC/NDT would allow facility owners to create a new job position. Surface maintenance technicians would monitor in-place coatings by black light and schedule maintenance based on predictive or RCM maintenance evaluations.
Conclusion
The Clean Air Acts of 1970 and 1990 were passed to help reduce pollution levels produced by industry and the private sector. These new regulations also had a serious effect on the coatings industry. Manufacturers were forced to reformulate proven products to lower VOC content. In the 21st Century, the coatings industry may be forced to change formulations again, this time, to save energy.Note, in 2007 no major airline accidents were reported in the United States.
For more information contact Jim Deardorff at jdeardorffsupct@yahoo.com; 660/646.6355.
Report Abusive Comment