When to Use a Leveling and Wetting Agent
If a coating formulation effectively wets the coating substrate and dries or cures without coating defects, leveling and wetting agents will not improve the coating formulation. Following are situations where a leveling and wetting agent should be tried.¥ If the coating formulation will not effectively wet the surface, or if defects occur as the coating cures.
- If a coating works effectively in a controlled laboratory environment but does not perform in the field because of difficult-to-control application conditions. A wetting and leveling agent can help ensure the coating will perform, even on dirty surfaces or surfaces with defects.
- If solventborne, high-VOC formulations are being reformulated to waterborne, high-solids, or 100%-resin systems such as UV-curable or powder coatings. When reformulating an existing coating to reduce or eliminate the VOC level, the reformulated coating often has a higher surface tension. These reformulated coatings may require leveling and wetting agents to ensure the coatings wet the surface and dry or cure without defects.
Types of Leveling and Wetting Agents
Determining whether to try a leveling and wetting agent is fairly straightforward - consider them if there are coating problems. The next question is what types of leveling and wetting agents to try and at what concentration.There are predominantly two types of surfactant chemistries used as leveling and wetting agents in coatings formulations. These agents are hydrocarbon surfactants and fluorocarbon surfactants. The difference between these two types of surfactants can be identified in Figure 1, which shows a typical hydrocarbon and fluorocarbon surfactant. The surface tension reducing part of a hydrocarbon surfactant consists primarily of hydrogen and carbon, while in a fluorocarbon surfactant it consists primarily of fluorine and carbon.
Both hydrocarbon and fluorocarbon surfactants are available in anionic, nonionic and cationic chemistries. Hydrocarbon surfactants are generally less expensive on a per-pound basis than fluorocarbon surfactants, and hydrocarbon surfactants are available with a variety of functional groups. Fluorocarbon surfactants, on the other hand, will result in a coating with a much lower surface tension. Fluorocarbon surfactants are also more efficient than hydrocarbon surfactants - requiring a lower concentration to provide an effect. Fluorocarbon surfactants can be tailored to function in all types of coating systems including solventborne and waterborne coatings, high-solids coatings, and powder coatings.
Trying a Hydrocarbon Surfactant
Because hydrocarbon surfactants are less expensive, it makes economic sense to try them first in the coating formulation. The table gives some general rules on what type of hydrocarbon surfactants to try in a waterborne system. A good starting point concentration is 0.1 weight % hydrocarbon surfactant. Figure 2 shows the relationship between the surface tension of a coating and the concentration of the surfactant. It also shows how the surface tension will level off as the concentration of surfactant is increased. The concentration should be adjusted to the level where the surface tension begins to level off. A hydrocarbon surfactant will typically result in a coating with a minimum surface tension on the order of 28-35 dynes per centimeter.In the comparison of a hydrocarbon and a fluorocarbon surfactant shown in Figure 2, a concentration of approximately 0.01% active fluorosurfactant (3M(tm) Fluorad(tm) FC-129) lowers the surface tension of an aqueous-based system to less than 20 dynes per centimeter. In contrast, a concentration of 0.1% hydrocarbon surfactant lowers the system's surface tension to slightly more than 30 dynes per centimeter.
Should the hydrocarbon surfactants tested fail to solve the coating problem, one of the following conditions may exist.
- The surface tension of the coating, though lower than the surface tension of the coating without the hydrocarbon surfactant, may still be too high.
- The hydrocarbon surfactant may not be the lowest surface tension component in the system. For example, if a silicone defoamer is in the formulation, surface tension gradients may occur during the drying or curing process that the hydrocarbon surfactant cannot resolve.
- Should high concentrations of the hydrocarbon surfactant be needed to sufficiently lower the surface tension - which is typically the case with hydrocarbon surfactants - the moisture sensitivity of the coating may have increased to intolerable levels.
Trying a Fluorocarbon Surfactant
After trying hydrocarbon surfactants, should any or all of the above conditions exist, the next step is to formulate with a fluorocarbon surfactant. Fluorocarbon surfactants can typically reduce the surface tension of coating formulations to 20 dynes per centimeter or less. The lower surface tension should maximize the initial wetting ability of the coating and minimize coating defects that occur because of surface tension gradients. When choosing the appropriate fluorocarbon surfactant to try in a particular coating formulation, the rules in the Table below also will apply. Because fluorocarbon surfactants are much more efficient, a starting point concentration of 0.01 weight % is recommended in waterborne formulations and 0.2 weight % in solventborne formulations.
Using a Hydrocarbon and Fluorocarbon Surfactant Together
Should the coating still not deliver good wetting and leveling properties even after minimizing its surface tension with a fluorocarbon surfactant, one of the following conditions may exist. First, consider the viscosity of the coating. If the viscosity is so high that the coating cannot be uniformly applied, the lower surface tension may not help. The coating may have to be reformulated to lower its viscosity. Second, consider the substrate the coating is being applied to. If the substrate has an extremely low surface energy, just lowering the surface tension of the coating may not be enough to ensure good wetting. In order for a coating to wet the surface of a substrate the following conditions must exist.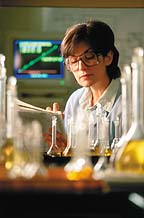
Conclusion
If your coating formulations perform effectively, and without coating defects, you don't need to consider leveling and wetting agents. However, if you are experiencing coating problems, consider trying either a hydrocarbon or a fluorocarbon surfactant or the combination of both types of surfactants. By experimenting with the various surfactants and adjusting their concentration, you should be able to develop coatings - even low-VOC coatings - that will perform on any type of surface.Sidebar 1: The Effects Of Fluorocarbon Surfactants On Recoatability
Because fluorocarbon surfactants dramatically reduce the surface tension of coatings, formulators often ask, do coatings that contain fluorochemicals result in a low-surface-energy, difficult-to-recoat surface? The answer to this question is, in most cases, no. The surface that results from a coating containing fluorocarbon surfactants typically does not have an unusually low surface energy. Fluorocarbon surfactants lower the surface tension of the liquid coating by aligning their fluorocarbon tails at the air/coating interface, but as the coating dries the fluorocarbon tail usually realigns away from the surface. Recoatability tests conducted on a variety of coating types containing fluorochemicals have shown the following.- Particularly in room-temperature drying or curing systems, it is unlikely a recoatability problem will occur, especially if a fluorocarbon surfactant is used in the recoat formulation.
- The few recoatability problems that exist with oven-cured systems have been resolved by using a different fluorocarbon surfactant in the recoat formulation.

Report Abusive Comment