
Successful job shops in the USA and Europe have some things in common. For one, it's difficult to succeed in today's economy without offering value-added services. Of course, companies can get their parts coated to specifications, but they also may want packaging, machining, printing and other services to limit transport and contracting. In France, there is a job shop that not only has exceptional coating capabilities but also offers the kind of extra service that adds value for its customers' customers.
Located in western France in the city of Fougeres, Société Fougeraise de Peinture Industrielle (SFPI) has six lines at this location to provide a range of coatings on different substrates and product sizes. With the different lines and coatings, SFPI has the flexibility to provide exceptional quality, and they are giving their customers a valuable service that makes them an important supplier and a strong ally in business.
SFPI employs 120 people at the Fougeres site. SFPI also has a coating facility in LeMans. Its coating business includes aluminum extrusion for building materials (about 60%), automotive parts (20%) and general industrial product (15%). It handles about one million square meters a year (10,760,000 square feet) of product to be coated.
Line number one is a powder line designed for small service orders and prototypes. A very important part of its business, prototyping allows SFPI to test an application on different shapes and with different powders to prove the process before introducing it into one of the two high-volume powder lines. Architectural aluminum is racked horizontally and pretreated in an in-line washer. Application is manual, providing flexible application and fast color change for small volumes.
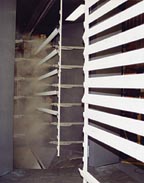
Horizontal and vertical racking
For high-volume production of powder coated architectural aluminum, SFPI uses two lines: one that racks parts horizontally and one that runs them vertically. Parts that are coated on the horizontal line are prepared in a dip wash system. After they are preracked, the parts are run through the dip system, which uses an overhead hoist to move parts through pretreatment stages for cleaning and chromating the surface prior to racking on the coating line.The ITW Gema (Indianapolis) Magic Cylinder powder booth uses automation and a smooth-walled, cylinder design to provide consistent coverage and fast color change. The round, plastic booth is designed to minimize powder accumulation on the walls and floor. The plastic booth walls provide a low level of electrostatic attraction and simple cleaning. The shape of the booth, extraction system, and feed center contribute to the simplicity and speed of the color change. Easy-access design allows an operator to quickly perform the simplified manual cleaning procedures from outside the booth cabin.
Along with the seamless, sandwich-wall, booth cabin construction, the seamless ductwork minimizes the risk of color contamination. The mono-cyclone has a built-in sieve that screens out contaminates.
The integrated feed center uses PLC intelligence to automate cleaning by pulsing compressed air over the gun exterior and throughout the powder path, including suction tubes, pumps, powder hose and gun. The feed center allows the operators to spray powder directly from the powder manufacturer's original shipping container. The combined features of the system provide SFPI with 10-minute color changes going from one reclaim color to another, with no cross contamination, and using only one operator.
The spray system uses 12 automatic guns mounted on a short-stroke vertical reciprocator with no manual reinforcement. Parts pass through the booth on load bars using a power-and-free conveyor system.
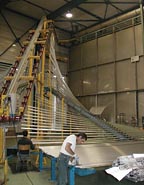
Vertically inclined
The third powder coating system is designed for application on vertically racked architectural aluminum. Vertical systems are common enough in the US for liquid systems, but there are not many designed for powder coating. These systems are much more common in Europe.The ingenuity and practical nature of this system cannot be overstated. It starts with the loading system where rows of parts are hooked to the rail and lifted from their horizontal position into the vertical position by the conveyor. This provides fast loading with very little labor and excellent rack density. The parts are then conveyed through the multistage washer to be cleaned and chromated.
After the parts are washed and pretreated, they pass through a dry-off oven and head to the two powder booths. The booths use plastic sheeting for walls to facilitate color change. Two sheets of plastic are used to form a "v" shape with the powder extraction duct in the center. The plastic sheet is fed from a roll and passes through a series of retainer bars to a take-up roller. When a color change is made, the plastic is indexed from a feed roller to a take-up roller to remove the powder-laden plastic and replace it with a clean sheet of plastic. Parts pass in front of the spray guns, and oversprayed powder is captured in the "v" shaped by the plastic sheets.
Eighteen powder guns are used for application in each of the two booths. They are mounted on a horizontal gun bar with four horizontal rows in a staggered pattern. The guns move up and down on a long-stroke vertical reciprocator. The system is capable of running parts up to 7.5 meters (24.5 feet) long. The reclaim system uses a cyclone for powder separation and recovery.
After the parts exit the coating booth, an operator attaches an alligator clip to the bottom of each part with a chain that connects them in a line. The chain and clip system prevents the parts from swinging into one another as they travel through the oven. The cure oven uses an infrared preheat section to sinter the powder so that it cannot be blown off in the convection portion of the oven.
When parts exit the cure oven, they are cooled and then lowered back into the horizontal position using the same technique as the load area in reverse. They are quickly packaged into crates and sent to the storage area.
The automated storage system stacks the parts into a racking system until they are ready to be shipped to the customer's site. Retrieval of a crate of parts from the storage system is initiated from a computerized panel that allows one operator to pull out the appropriate part in the color and quantity needed and load it onto a waiting truck.
The automated system provides SFPI with advantages in productivity and control of their stock, and provides additional service that adds value for its customers, says Armel Reminiac, SFPI's president.
The liquid side of the business
The liquid coating systems used at SFPI are designed for application on plastic substrates. Similar to powder coating, they use a small manual coating line to run prototypes. Processes for new products or colors can be developed on the prototype line before they make design decisions and build up for production runs.The two production lines are designed for robotic application of color coat and clearcoat on plastic. Both lines are totally enclosed to prevent dirt from getting on parts after they are cleaned. Most of the volume on these two lines is devoted to coating cell phone covers. Each skid of molded cell phone covers has a color standard attached for visual color match.
On the first line, the parts are hung from vertically positioned racks. A strip of molded plastic is attached to the rack frame to hold the parts in place. The racks have 21 strips, each of which holds three cell phone covers, for a total of 63 parts per rack.
Three booths are used in the coating system. All application is done by an HVLP spray gun mounted on a robotic arm. A primer is applied in the first booth, followed by a color coat, and finally a clearcoat. The total film build on the cell phone covers is 70 to 80 microns (3 mils). All of the coatings on the first line are thermosetting paints.
The newest line uses automation and robotic arms to apply the same coatings as the other liquid production system, but parts are run through in the horizontal position on a floor-mounted conveyor. With no overhead conveyor and a totally enclosed process, the new system is virtually dirt-free.
In addition to thermally cured products, the system also uses some UV clearcoats. The UV clearcoats provide very fast cure at very low temperatures, and the coatings are very low in VOCs. UV is used as much as possible, but some colors are sensitive to the UV light and may cause discoloration, so the thermally cured clearcoat is still used for certain colors.
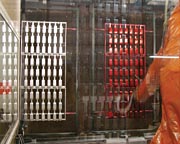
Quality is critical
Quality is a critical part of SFPI's business, and they strictly adhere to the European QUALICOAT standards. The QUALICOAT standards establish minimum requirements for plants, coating materials and finished products. They are designed to provide high-quality coating on products used in architectural applications. It requires them to treat all products used for architectural products according to the written specification.The specifications include product performance testing and work specifications. Every run in the facility must be subjected to a battery of finished film tests, including appearance, gloss, film thickness, adhesion and impact. Tested panels are retained for two years. The approved source is then able to use a quality label to show that it meets the standard.
Considering the volumes that it coats and the standards that it must meet, it is no wonder that this custom coater is in demand in Europe. Using several systems for both liquid and powder, they are able to react to customer needs and accommodate fast turnaround times, small orders, large orders and special requests. This is just the kind of service that the market demands of a custom coater these days.
SIDEBAR:
Tales From the Land of Dickens and Flaubert
We had planned to write only a single article about our recent trip to Europe with a group of DuPont Star Coaters to visit custom coaters and see what types of products and processes they were running. But we met so many interesting people and saw such unique processes that we decided one article couldn't adequately tell the whole story. So in upcoming issues, we will share more stories about our trek through Europe.In this issue, we have a case study of one of those custom coaters, Société Fougeraise de Peinture Industrielle. This was our first visit to a coating facility in France and it was well worth the trip. SFPI does both liquid and powder coating, and it has a unique operation.
In upcoming issues we will talk about some batch systems that we saw running architectural aluminum in France and in London. They had some unique setups and produced a lot of volume from a small lines. We will also take a look at powder coating on plastic parts.
One of the highlights of the trip was a lunch in Belgium. When we started out that morning, we were told that we would meet the inventor of powder coating. Some of us had heard of Pieter G. de Lange, and we were intrigued by the prospect of meeting him.
When we arrived at our first stop, the DuPont sales office in Hasselt, Belgium, we learned that de Lange had been held up in traffic. We had a brief discussion about the powder market in Europe and then left for our first tour of the day, Thermo-Clean, a very large facility that provides rack-stripping services for coaters. We then went on to our next tour, a large coater of aluminum called Alural. We will also have a story on this facility. After this tour, we went to lunch, disappointed about failing to meet up with the man who had started the thermoset powder market.
When we arrived, we learned that de Lange had at last arrived and would be joining us for lunch. He shared his story with us, and we will share it with you in our February issue.
While working for Teodur Coatings (now Teodur Powder Coatings, a division of DuPont) in The Netherlands, de Lange was challenged with finding a low-VOC coating. He came up with powder coatings, exceeding everyone's expectations. Working with existing electrostatic technology from Sames, he was able to apply the first thermal setting powder in Europe in 1960. We want to share this important part of the coatings industry's history with our readers, as well as insights and observations from the inventor himself.
And speaking of history, Industrial Paint & Powder turns 80 years old in 2004. Beginning in January, and running throughout the year, we will reprint portions of the magazine beginning with the first issue in 1924. You'll read about the companies, the technologies, the events and the newsmakers that helped shape the modern coatings industry, as well as the world in which we live. So join us in each issue as we celebrate 80 interesting years of history-our history, and yours.
Report Abusive Comment