

At higher pigment levels the appearance of powder coatings becomes worse. High pigment levels are required to reach a desired hiding power, especially in thin-layer applications. The difference in appearance between a standard and a highly filled system can be seen in Figure 1.
Resins are developed based on a special concept, the HiTone concept, to overcome flow and appearance problems at higher pigment levels. The purpose of this study is to achieve a better pigment affinity of resins without compromising on important properties like flow, gloss and hiding power. As already mentioned, the pigment affinity can be improved by using the HiTone concept. This paper discusses the effect of the solution found on the properties of pigmented powder coatings. Besides the appearance, it is expected that the extrusion and milling behaviour of powder coatings with a higher pigment level will be affected. The effect of high-filled systems on milling behaviour is also discussed.
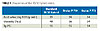
Experimental
A standard 70/30 hybrid resin and two 70/30 hybrid resins based on the HiTone concept (Uralac® P 770 and Uralac P 772) were synthesized. Uralac P 772 is a faster-curing version of Uralac P 770. Furthermore, a standard 60/40 hybrid resin and a 60/40 hybrid resin based on the HiTone concept (Uralac P 760) were synthesized.
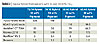
Powder coatings were prepared by extrusion of the formulations using a Prism TSE 16 PC twin extruder with 16 mm diameter screws and L/D 14. The extrusion temperature was set at 120 °C, the extrusion speed at 200 rpm, and the torque was kept between 75 - 90%. After extrusion, the extruded material was ground by a Retch ZM 100 centrifugal mill and sieved through a Retch Vibro sieve with a mesh of 90 µm. Finally, the powder coatings were sprayed electrostatically onto steel panels (Q-panel S 46) with a GEMA PG1 spraying gun and placed vertically in a UT 6120 hot-air oven from Heraeus. Coatings with a layer thickness of 60 µm were used for evaluation.
Evaluation
Flow was visually evaluated on coated panels and compared to PCI standards. In addition, the flow was evaluated with a white light interferometer from Veeco. This device is able to rapidly measure a 3D scan of a large surface area (e.g., 2x2 mm2 with a single scan) with a height resolution of a few nanometers and a lateral resolution of 600 nanometers. By using an automatic XY table and appropriate “stitching” software, the interferometer was able to measure even much larger samples (e.g., 10x2 mm2).Coating flexibility was tested via reverse impact, according to test method ASTM D 2794. Coated steel panels were subjected to an impact of 160 inch-pound on the back of the panel. Also ALMg3 panels were coated and cured for 10 minutes in a BYK-Gardner gradient oven between 150 - 250 °C. These panels were subjected to an impact of 160 inch-pound. Gloss and haze were measured at 20° and 60° with the BYK Gardner reflector meter, according to the standard ASTM D 523.
Heat resistance was determined by placing a cured panel in the oven at 240 °C for 10 minutes and 220 °C for one hour. Colour differences between an untreated panel and the treated panel were evaluated.
Salt spray tests were conducted on a cured panel with a vertical scratch of 1 mm, according to ASTM D 2803. The cured panel was placed in salt spray equipment for 500 hrs. After 500 hrs, the average creepage from scratch was measured. The powder and coating Tgs were determined by differential scanning calorimetry (DSC) at a heating rate of 5 °C/min.

Results
HazeHaze values are an indication of the appearance. In general, if the haze value is low the appearance is good; if the haze value is high the appearance is bad. Haze values of the final coatings were measured by the BYK Gardner reflector meter. Haze measurement results are shown in Figure 2 for different pigment concentrations. A comparison between standard resins and the new, developed resins, Uralac P 770, P 772 and P 760, was made.
The standard resins showed low haze values up to a concentration of 40-45 wt%. Above a concentration of 45 wt% pigment, an increase in haze was shown. Conversely, Uralac P 770, P 772 and P 760 showed much lower haze values up to a concentration of 55 wt% pigment versus the references.
Summarizing the above-mentioned experimental results, it can be stated that compared to standard resins, HiTone resins can be much higher filled with titanium dioxide without compromising haze properties.
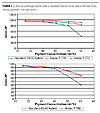
Gloss is also an indication of the appearance. In general, a high gloss value indicates a good appearance. Gloss values were measured by the BYK Gardner reflector meter. Figure 3 shows a comparison of the gloss values between standard resins and the HiTone resins (P 770, P 772 and P 760) at different pigment concentrations. In this figure, gloss 20° is plotted as a function of the pigment concentration.
As can be seen, coating gloss, based on standard resins, starts to decrease at a pigment concentration of 40 wt%. On the other hand, gloss decrease at higher pigment loadings was much less for systems based on the HiTone resins. The results on gloss and haze indicate that the pigment affinity of HiTone resins is much better than the pigment affinity of standard resins.
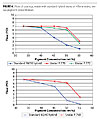
Flow depends on many factors. In general, flow will improve if the reactivity of the system is lowered. Also other parameters such as viscosity and surface tension can influence flow. It is expected that flow will improve at higher pigment levels if the pigment affinity of the resin is improved. Flow results at different pigment concentrations are shown in Figure 4. A comparison was made between standard resins and HiTone resins. The flow was measured by comparing standardized PCI panels with coated panels made with HiTone resins or standard resins.
The flow at lower pigment concentrations was comparable, but at higher pigment concentrations differences in flow were observed. HiTone resins showed better flow than standard resins at higher pigment concentrations. This indicates that the improved pigment affinity of HiTone resins improves the flow properties, especially at higher pigment loadings.

As can be seen from Figure 5 the Uralac P 770 levels better than the standard resin at a pigment concentration of 50 wt%. According to the flow results, HiTone polyesters showed a better flow at higher pigment levels than standard polyesters. It is clearly demonstrated that the use of the HiTone concept improves the flow ability of highly filled systems.
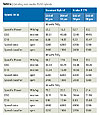
To determine the influence of high-filled systems on the specific power consumption during grinding, grinding experiments were performed on an industrial scale. The specific power consumption is expressed by the required electrical power per kg of product to mill the product to a defined particle size. For the grinding experiments Uralac P 770 was tested over the full range of pigment concentrations. Also Uralac P 760 with 50 wt% pigment was tested. Because smaller particle sizes are needed for thin-layer applications, the difference in specific power consumption between a particle size distribution (PSD) of an average size D50 of 30 µm and 50 µm was determined. The experiments were performed on an air classifier mill ACM10 of Hosokawa. Limiting conditions during grinding were the maximum power consumption of the grinding motor and the classifier motor and the maximum pressure drop over the system. The effects of these conditions were especially observed during grinding of the highest pigment loaded systems to the smallest particle size. To overcome this, the speed of the grinding disk and the classifier were adjusted. The most relevant test results obtained are given in Tables 4 and 5.
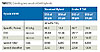
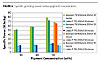
From Figure 6 the general conclusion may be drawn that with higher pigment loading rates a tougher milling behaviour is observed, especially in combination with a small PSD. Nevertheless, the tougher milling behaviour is independent of the polyester type used and is directly related to the increased pigment content. It can be concluded that the milling behaviour of HiTone resins is not different compared to standard resins.

Other Coating Properties
As already mentioned, the purpose of this study is to improve the pigment affinity of polyester resins without compromising on important properties. Haze, gloss, flow and milling behaviour have been discussed. The results of tests done to determine other properties are presented in Table 6. A comparison was made between a standard 70/30 hybrid, Uralac P 770 and Uralac P 772, and a comparison was made between a standard 60/40 hybrid and Uralac P 760. Only the results with 33 wt% and 50 wt% TiO2 are indicated.The impact resistance was measured on a gradient panel, which was cured in a gradient of 150-250 °C for 10 minutes. The temperature at which the coating starts to have a good impact is shown in Table 6.
From the results given in Table 6 it is clear that properties like chemical resistance, heat stability, powder stability and salt spray resistance are not affected by using the HiTone concept. Also powder Tg and coating Tg are comparable. The standard curing HiTone resins (Uralac P 770, Uralac P 760) are a little bit slower than the standard hybrid resins but for fast-curing 70/30 hybrid systems Uralac P 772 can be used.
Conclusions and Discussion
In this paper, the use of resins with improved pigment affinity has been described. Excellent results are achieved by using the HiTone concept. Properties of coatings made with HiTone resins Uralac P 770, P 772 and P 760 have been discussed. These resins have been filled up to 50 wt% pigment while maintaining properties like flow, haze and gloss. Performance on other important coating properties such as powder stability, flexibility, heat and chemical resistance, powder and coating Tg has not been affected.Furthermore, the milling behaviour of HiTone resins has been discussed. Hitone resins with a low and high pigment amount have been milled to a D50 of 30 and 50 µm. A comparison has been made with standard polyesters. HiTone resins showed no difference in milling behaviour compared to standard resins.
To conclude, with HiTone resins a much higher pigment loading rate can be reached than conventionally possible, whilst retaining high aesthetic and mechanical properties. The good results enable a broader formulation and application window. Possible application areas are for example, thin layers, domestic appliances and white goods, high-filled primers, ceiling tiles, heat ventilation and airco, metal housing, metal furniture and many others. n
This paper was presented at The Waterborne Symposium sponsored by The University of Southern Mississippi School of Polymers and High Performance Materials and The Southern Society for Coatings Technology, 2008, New Orleans, LA.
For more information, visit www.dsmpowdercoatingresins.com.
Report Abusive Comment