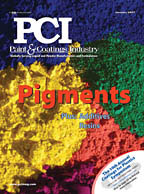
The isocyanate reaction between an isocyanate group and a hydroxyl group has been known since 1849 when Ann Wurtz obtained the first patent in this field (German Patent 71326). The polymer, containing a repetitive moiety that results from the reaction between an isocyanate group and a hydroxyl group, is a polyurethane. Its morphology depends on the structure and nature of the diol and the respective isocyanate.
Viable industrial solution waterborne polymeric materials, PolyUrethane Dispersions (further referred to as PUDs) and their synthesis on an industrial scale, have been known since the 70s. Their use in the coatings and adhesives industries as such, or in combination with other dispersions, made interest in them increase due to their particular advantages (typical PU properties) and one/two pack coating application.1
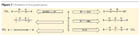
Isocyanate Reaction and the Building Blocks
Figure 1 summarizes the basic isocyanate reactions. The following are isocyanate reaction characteristics:- precise stoichiometric ratio is required;
- high-purity monomers and solvents are required;
- one polymer forming chemical reaction;
- randomly reacting functional groups;
- monomers disappear early in the polyaddition chain;
- molecular weight rises slowly and is high at high conversion degree; and
- broad molecular weight distribution until the very end of the reaction when all oligomers have reacted.
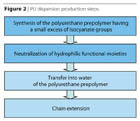
PU Basic Building Blocks
The selection of the PU building blocks is essential for the targeted coating properties.2- The isocyanate component constitutes the hard segment and must exhibit sufficient stability towards water. All isocyanates may be used for the synthesis of PUD, provided the right process is followed. It is important to emphasize that the reactivity of aromatic isocyanates is much higher than that exhibited by the aliphatic isocyanates during the early stage of water dispersion.
- The polyol constitutes the soft segment in the morphology of the final product. The nature of the polyol covers almost all known types of oligomers. Linear or slightly branched oligo-polyols are selected from polyethers, polyesters, polycarbonates, epoxy resins, hydroxyl acrylates, alkyds, hydroxyl polybutadienes, and fluoroalkyls. Short chain diols and triols are used to adjust the polymer branching and the polyurethane group content.
- The chain extender is the moiety introducing the urea valuable group in the polyurethane chain and is selected from the family of aliphatic amines. This choice is based on the understanding of the fact that the amine group is reacting at an extensively higher rate than the water with the isocyanate group. The choice is preferably made from the aliphatic, cyclic-aliphatic, amino polyethers, hydrazine and hydrazine derivatives.
- The internal emulsifiers are condensation monomers containing hydrophilic groups, which usually replace a small amount of the previous described building blocks, which contain ionic precursors or water-soluble segments in their molecule.
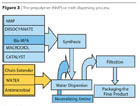
Polyurethane Dispersions:
State of the Art
The steps involved in the production of polyurethane dispersions are noted in Figure 2. The process of preparation3,4of high-molecular-weight polyur-ethanes is different only in the critical step, which is the high molecular weight build-up. This step, commonly known as the “chain extension” step, is actually dealing with two factors of high importance: the control of viscosity and the mastering of the extremely quick reaction of the isocyanate group and an amine.The steps involved in the production of polyurethane dispersions are noted in Figure 2. The process of preparation3,4of high-molecular-weight polyur-ethanes is different only in the critical step, which is the high molecular weight build-up. This step, commonly known as the “chain extension” step, is actually dealing with two factors of high importance: the control of viscosity and the mastering of the extremely quick reaction of the isocyanate group and an amine.
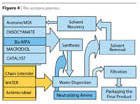
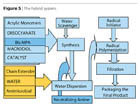
- The Solvent-Free Prepolymer Process: The fundamental of the process is the fact that the di-methylolpropionic acid (Bis-MPA) presented in a micronized form is soluble in the macromolecular diol at a temperature of about 50-120 ºC. However, the final molecular weight of the reactive prepolymer is low as the ratio of NCO/OH is about 2. Prepolymer neutralization, water transfer and chain extension are similar to the NMP process.
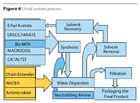
- The Ketimine and Ketazine Processes use blocked amines (bisketimine) or blocked hydrazine (ketazines), which, in the presence of water, form the amine group to further react to the isocyanate groups of the prepolymer. Similar processes use aldimines, aldazines or oxazolidines.
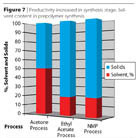
- The Hybrid System uses acrylic monomers replacing the solvent in the PUR prepolymer synthesis. After the water transfer phase, the monomer is polymerized, resulting in a hybrid polyurethane-acrylic imparting benefits of both polymer backbones. The resulting product is different from a physical blend as the polyurethane backbone is acting as a surfactant in a radical polymerization process where grafting is occurring (Figure 5).

- The Ethyl Acetate Process (Figure 6) may be regarded as a hybrid between the prepolymer process and the acetone process. However, the solvent is not water miscible as in the above processes, but forms an azeotrope with water (b.p. 70 °C, ethyl acetate 91.9%, water 8.1%). A better positioning for the ethyl acetate process is given in Figures 7 and 8.
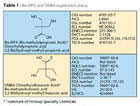
Anionic PUD Based on Hydrophilic Carboxyl Functional Monomers
Anionic PUDs are obtained by using bis(di-hydroxyl-functional) carboxylic acids, monomers having two primary hydroxyl groups that easily react with the isocyanate groups, and a tertiary carboxyl group, with low chemical reactivity due to sterical hindrance as an ionic precursor. Among these, the champion is the bis-methylolpropionic acid (Bis-MPA) (Table 1). With a lower importance as sales volume, but an overwhelming technological benefit, the bis-methylolbutyric acid (DMBA) is the second in range (Table 1). The latter gives the benefit of lower melting point and higher solubility in macrodiols and typical polyurethane solvents. Physical properties are noted in Table 2.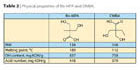
The present paper deals with the use of Bis-MPA in anionic PUDs by another approach, in an attempt to overcome the limitations of Bis-MPA. Basically the DMBA has a solubility of at least 20% higher than the Bis-MPA, a lower melting point and, therefore, it is much easier to be used in PUD manufacturing, but it is not registered in Europe.
Manufacturing problems are mainly related to the solubility drawbacks of α,α’-di-hydroxyl-functional carboxylic acids, which therefore are normally used in the form of small particles, normally not larger than 150 µm. In case the α,α’-di-hydroxyl-functional carboxylic acid contains larger particles, they may remain unreacted and must be removed by filtration. This gives rise to another problem, namely uncertainty regarding the exact amount of hydroxyl-functional acid built into the polyurethane chain.
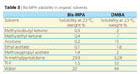
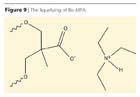
Experimental
The process is based on the observation that the ammonium salts of the Bis-MPA and any other α,α’-substituted acids having a tertiary carboxyl group are soluble in polyols, macrodiols and solvents and these blends are fluid at room temperature. In the process, the hydrophilic monomer is no longer used as containing a precursor ionic group, but as an ammonium salt, allowing a one-phase system at the very early stage of the prepolymer PUR formation (Figure 9).Components of the liquefied α,α’-di-hydroxyl-functional mono-carboxylic acids are given in Table 4.
The “liquefied Bis-MPA” may be produced in a reaction vessel equipped with a heating system, a stirring system, a water separator, a cooler and nitrogen inlet and stored prior to the PUD synthesis; or produced in the synthesis vessel where the PUD synthesis will be further accomplished, prior to the PUR prepolymer synthesis.
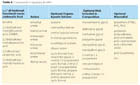
- Load at room temperature and under nitrogen blanket the diol or macrodiol and warm up to melt at 80-100 ºC and apply vacuum to dry. Reduce the vacuum with nitrogen flow. Load the solvent if required by the applied formulation.
- Charge the amine under mechanical stirring.
- Load the Bis-MPA under efficient stirring (in small portions).
- Heat the mixture to a temperature of 50-80 ºC under stirring and under nitrogen blanket until a clear solution is obtained.
The process as described allows a one-phase reaction, eliminating the long time required for the dissolution of Bis-MPA, or any acid as above described, by reaction with the di-isocyanate.
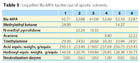
Liquefied Bis-MPA in Aprotic Solvents
In the examples given in Table 5, solvents such as N-methylpyrrolidone, methyl ethyl ketone, acetone, are used as typical PUD processes, (examples are given in parts by weight).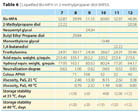
Liquefied Bis-MPA in Propane Diols
In addition, in Table 6 we present a few examples for liquefied Bis-MPA in 2-alkyl substituted propane diols (BEPD, NEO, MPD) and linear diol. More examples may be found on Perstorp website (www.perstorp.com), (examples are given in parts by weight).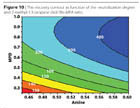
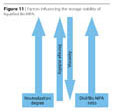
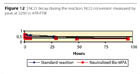
Isocyanate Group Reactivity with Liquefied Bis-MPA
The reactivity of the isocyanate group has been followed in ATR-FTIR by measuring the NCO peak at 2250 nm. The reaction needs no further catalyst to speed up when compared to the typical reaction of Bis-MPA (Figure 12). Figure 13 shows the decrease of the NCO group in the first 90 minutes of reaction. This makes possible the use of liquefied Bis-MPA as a chain extender. The reaction is easily exothermal, generally causing a temperature increase of about 20 ºC.
Formulations of PUD
Comprising Liquefied Bis-MPA
Further the examples of liquefied Bis-MPA have been tested in formulations of PUD according to the most applied industrial processes, the acetone process and the melt dispersion process, as well as in the solvent-free process. In the examples, formulations are given in parts by weight. All data is presented in the Appendix.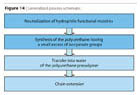
Conclusions
According to the experimental data presented in this paper, the hydrophilic monomer is no longer used as containing a precursor ionic group, but as an ammonium salt. This allows the easy dissolution of the hydrophilic monomer in the reaction blend and ensures a mono-phase system, which gives shorter reaction times, no crystallization hazards, and more uniform distribution of the hydrophilic moieties on the polymer chain.The presented examples of the liquefied Bis-MPA are completely compatible to the well-known industrial processes in concordance with the requirements of both themelt dispersion processand theacetone process. The liquefied Bis-MPA, as illustrated by examples, is suitable for the synthesis of PUR by the ethyl acetate process, resulting in virtually solvent-free PUDs, of similar kind as those produced by the acetone process. This method is preferred as the ethyl acetate gives a heterogeneous azeotrope, and the solvent may be easily recycled after dehydration.
Further, the use of liquefied Bis-MPA according to the method described above allows the manufacturing of PUR intended for PUDs completely free from any solvent when the dissolution of Bis-MPA is made in the macrodiol itself or in a suitable diol-amine combination or is used as chain extender. This eliminates the use of N-methylpyrrolididone and generates not only “virtual solvent-free PUDs” but solvent-free PUDs in the true meaning (Figure 14).
The liquefied Bis-MPA allows lower viscosity in the prepolymer. This may be explained by the fact that hydrogen bonds through the carboxyl group as in Figure 15 are not possible. The salt formation may contribute through electrostatic repulsion to a lower viscosity as increasing the space between prepolymer chains, as well as the amine is acting as solvent and spacer, thus reducing the viscosity build-up by H-bonds between urethane groups.
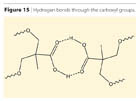
The dissolution of Bis-MPA neutralized with amine in solid diols results in liquid combinations easy to handle that need to be optimized in case they are intended to be storage stable for longer time periods. The use of liquefied Bis-MPA and other hydroxyl acids having tertiary carboxyl groups is an easy way to minimize problems related to the seeding and crystallization of PUDs.
The process differs from that commonly accepted by the fact that the ionization phase precedes the reaction of the isocyanate with the macro-diols and the hydrophilic monomers. This allows for the use of liquefied Bis-MPA and any other α-substituted hydroxyl acids for use as chain extenders in the same way as 1,4-butane diol is presently used.
Report Abusive Comment