The Wet Look That Lasts
In 1972, DuPont introduced Imron® polyurethane enamel, characterizing it as "the wet look that lasts" because of its gloss, chemical resistance and durability. In the 32 years since then, Imron has lived up to that appellation, and in the process has become the most well-known paint among the manufacturers, owners and painters of commercial vehicles. Its reputation has spread to other markets, most notably the aircraft industry, where it's a favorite with owners and manufacturers of single- and twin-engine planes. Indeed, when truck owners, aircraft owners and those in the refinish industry speak of polyurethane enamels, the first name that comes to mind is Imron.
While the term polyurethane enamel has many meanings to many suppliers and users, a polyurethane is any polymer that contains urethane chemical bonds. In the refinish business, this is achieved by the reaction of an isocyanate-containing activator with a polymeric binder.
The larger paint companies tend to use the term "urethane" to describe their most premium products. It is important to note, however, that some paint makers have capitalized on the polyurethane image, and use this term to describe inferior products. Thus, "polyurethane" does not always mean superior quality.
Imron Chemistry
Imron polyurethane binder uses a unique acrylic/polyester binder. The acrylic chemistry provides durability and hardness, and the polyester chemistry delivers chemical resistance. These two chemistries, combined with the flexibility of the urethane crosslink, provide an excellent balance of properties for the cost. Quality polyurethanes, being the best performing systems, give the longest paint cycles to fleet users.
Over the past four decades, Imron polyurethane enamel has evolved into a complete line of commercial finishes, including VOC-compliant single-stage and base/clear systems, as well as a product based on unique DuPont technology that is resistant to graffiti.
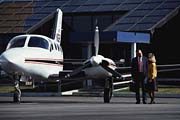
Truck Industry
With Imron, DuPont has been the primary topcoat supplier to the five heavy-duty manufacturers for the past 15 years. Dozens of other OEMs, including major van converters, bus manufacturers and truck bodybuilders, use Imron on their products. It's also the choice of thousands of fleets and commercial refinishers.A major reason for this popularity is not only its performance as a finish, but its performance in the paint shop in terms of productivity and economy. Standard Imron polyurethane enamel is an easy-to-use, single-stage finish that delivers exceptional gloss and DOI (distinctness of image) and outstanding durability. It is available in virtually any color. In fact, one mixing machine with 40 high-strength tints creates all color formulations for Imron 6000, Imron 5000 and Imron 2000. What's more, these systems are based on extensive color development for exceptional color-matching capabilities.
For the ultimate in glamour and durability, with VOC compliance, there is Imron 6000 polyurethane enamel. This base/clear system resists harsh environmental conditions like UV radiation and acid rain. It offers better hiding and more film build per pass for higher productivity. All of the thousands of colors have a maximum of 3.5 lb VOC per gallon.
The 5000 polyurethane enamel offers the highest productivity and performance with the lowest VOC. This single-stage finish also meets the country's toughest VOC regulations. It is available in 3.5 or 2.8 lb VOC, and features advanced UV screeners and light stabilizers to stand up to weathering and industrial chemicals. High-strength tints and a high-solids formulation cut material usage nearly in half. Less coating use translates to about half the time - Imron 5000 goes on in about half the time it takes for conventional urethanes.
Imron 2000 polyurethane enamel, while offering the same chemistry as 5000, is ideal for shops that don't have pressure pot equipment or prefer application methods like those used to spray original Imron. It is a versatile, user-friendly system that is easy to apply, and delivers a "no surprises" topcoat. It is applied with two separate coats, as opposed to the cross-coat technique recommended for 5000. And like 5000, Imron 2000 is ideal for in-kind repairs. That means it can be used on original equipment such as Kenworth, Freightliner, Peterbilt and Volvo heavy-duty trucks, all of which are factory-finished with Imron 5000.
Imron Clearcoat EZ-3460S provides outstanding cleanability, coupled with resistance to chemicals and graffiti. The chemical formulation for the two-component polyurethane clear is based on Teflon® technology. As a result, it offers exceptional cleanup properties while resisting dirt, road tar and tree sap, as well as graffiti. EZ-3460S was designed to use with the 6000 basecoat/clearcoat and the 5000 single-stage topcoats. When used over these products, it produces a durable clearcoat with excellent appearance on vertical surfaces.
EZ-3460S resists such compounds as hydrochloric acids and gasoline, as well as strong alkalines and other aggressive chemicals often used to remove graffiti. "With this clear, though, you normally can use less aggressive chemicals and processes to get rid of graffiti," says Irving Bell, DuPont's OEM/Fleet Product Platform manager. "And that reduces both the cost of the cleaner and the waste disposal costs." He notes that it also extends the repaint cycle, resulting in a significant saving in labor, material and vehicle downtime.
The latest iteration from DuPont's Performance Coatings laboratories is Imron Elite. This high-solids polyurethane topcoat, which is virtually free of hazardous air pollutants, has been adopted by five major heavy-duty truck manufacturers.
The manufacturers - Freightliner, Sterling Truck, Peterbilt, Kenworth and Mack - chose Imron Elite because it imparts unsurpassed gloss and resistance to chemicals, weathering, solvents and abrasion. The finishes utilize new dispersant-based color coat technology that, in addition to improved finish appearance and performance, increase productivity because of shorter flash time between the basecoat and clearcoat.
With Imron Elite, repair shops can easily recreate that exceptional factory finish, a finish that is smooth and glossy, with reduced orange peel. The system's two-component polyurethane technology also delivers the superior durability Imron is known for in low-VOC, low-HAPS, lead- and chrome-free formulations.
The Imron Elite system includes:
- DuPont Imron Elite SS Polyurethane Enamel Topcoat - A high-gloss, extremely durable single-stage for use on commercial vehicles, trucks and trailers, wherever superior performance and appearance are required. This air-dry urethane also may be force-dried for extra versatility.
- DuPont Imron Elite BC Polyurethane Enamel Basecoat - A high-hiding, air-dry basecoat that can cover in one cross-coat. Designed for use with Imron Elite Clearcoat, it provides unsurpassed gloss and resistance to chemicals, weathering, solvents and abrasion.
- DuPont Imron Elite 8840S Polyurethane Clearcoat - A high-gloss, extremely durable clear that resists yellowing and provides exceptional resistance to chemicals, solvents and environmental attack. This easy-to-use clear has good flow-out, excellent sag resistance, and is recommended for both air-dry and force-dry processes.
Repeated tests also prove that the Elite system has superior high-hiding capabilities and excellent sag resistance. In addition, lower viscosity colors make a superior Imron Elite finish even easier to apply with standard shop equipment, saving both time and money.
For more information on this Imron polyurethane enamel, visit the DuPont Performance Coatings website, www.performancecoatings.dupont.com, or call 1/800.GETDUPONT.
Looking for a reprint of this article?
From high-res PDFs to custom plaques, order your copy today!