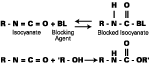
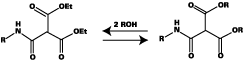
Background
The chemistry of blocking and unblocking is well understood,2-3 with the main blocking agents [e-capralactam (ECAP), methylethylketoxime (MEKO), and DMP] reacting by way of equilibrium between free isocyanate and blocked isocyanate (see Figure 1). Increasing temperature moves the equilibrium to the left, releasing isocyanate groups, which then react with active hydrogen species to generate urethane bonds.In contrast, it is generally accepted that diethyl malonate (DEM) blocked isocyanates react by way of transesterification, rather than liberation of isocyanate (see Figure 2). The final reaction product differs from that formed from a conventional blocked isocyanate in the following ways: a stoichiometry of 1:2 (nco:oh) is theoretically achievable; and a carbamate (urethane) bond is not formed in the crosslinking reaction.
Furthermore, the transesterification reaction can take place at lower temperature than normal stoving conditions. This is both an advantage and a disadvantage. The reduced temperature cure is desirable but since the reaction can also take place slowly at ambient temperature, the stability of 1K formulations based on DEM-blocked isocyanates is poorer than those derived from other blocked isocyanates. The stability can be improved by incorporating a volatile monofunctional alcohol, which competes with polyol in the transesterification reaction and prevents crosslinking from taking place during storage. Key features of the main blocking agent are shown in Table 1.
Combinations of blocking agents are used to achieve a two-stage cure or achieve high build coatings by imparting some crosslinking at a relatively low temperature and thus reduce the tendency of the film to flow when the higher temperature is reached. Since DEM and DMP have similar peak unblocking temperatures, the combination of these blocking agents does not, at first sight, have any advantage. However, the different chemistries involved may mean that coatings produced from such combinations have different (ideally enhanced) properties than coatings produced from either DEM or DMP blocked isocyanates.
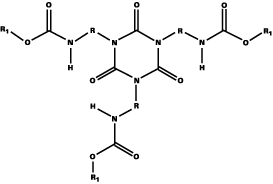
Discussion
As noted, the optimum ratio of OH:NCO in a diethyl malonate blocked isocyanate is greater than 1:1. To establish the optimum ratio of OH:NCO, an isocyanate blocked entirely with diethyl malonate (Trixene BI 7963 was cured with acrylic polyol (Crodaplast AC589BN). Reaction was catalyzed by DBTL and the substrate was a primed steel panel. The results are shown in Table 2. Stoving was for 30 min. at the indicated temperature.To establish the optimum ratio it was necessary to run below 120 DEG C. Table 2 indicates that cure temperature and stoichiometry influence the cured film properties for a DEM-blocked isocyanate, with better properties shown at the higher ratio. It is also reasonable to expect a longer cure time to improve film properties. It must be noted that the optimum stoichiometry may vary with the structure of the polyol and isocyanate, due to steric hindrance around the blocking group and the active hydrogen compound. However, since the same polyol was to be used for all the subsequent work in this article, the ratio of 1.6:1.0 was chosen.
A significant implication of the study of optimum ratios is that blocked isocyanates containing DEM are potentially more cost-effective than a conventional blocked isocyanate, since less blocked isocyanate would be required to fully react with all the active hydrogen sites on the polyol.
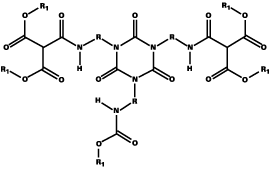
Combinations with DMP
As well as the problem of the transesterification reaction occurring in the formulation, leading to reduced stability relative to conventional blocked isocyanates, DEM-blocked isocyanates have a tendency to solidify. This is particularly so in the case of DEM-blocked HDI trimer. In preliminary experiments to combine experiments to investigate the combination of DEM with DMP, simple blends of blocked HDI trimer were made; however the tendency to solidify remained. It was only when the two blocking agents were reacted with HDI trimer in the same reaction that the blocked isocyanate remained liquid. This improved behavior is due to the incorporation of hybrid-blocked isocyanate, where a proportion of the trimer molecules are blocked with both DEM and DMP (as well as a proportion, which are blocked with either DEM or DMP). This is in contrast to a straight blend where the trimer molecules are only blocked with either DEM or DMP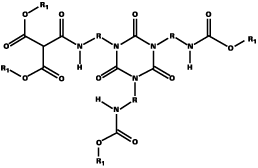

Formulations
In order for the cost effectiveness of the hybrid blocked isocyanates to be useful, it is important to establish that the coating properties had not been detrimentally affected. The results are illustrated in Tables 3-6. It has been demonstrated above that the optimum ratio of OH:NCO is around 1.6:1.0 for the polyol used in this study and an all DEM-blocked isocyanate. For a hybrid DEM/DMP-blocked isocyanate with a 1:1 ratio of DEM/DMP the optimum ratio of OH:NCO is therefore 1.3:1. In all the formulations shown, a 1.3:1 ratio of OH to NCO has been used; this means that only 77% of the molar equivalent of a hybrid blocked isocyanate is required compared with a conventional blocked isocyanate. Key measures used to assess performance included the following.- Artificial weathering performance (assessed by QUV yellowing and gloss)
- Resistance to yellowing on overbake
- Acid etch resistance
- Adhesion
Clearcoat formulations prepared for this work are shown in Table 3. Results of the coating tests are shown in Table 4.
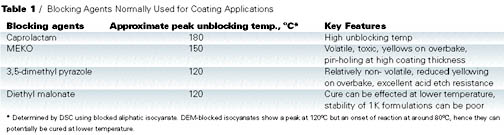
Artificial Weathering Performance (QUV)
Clearcoat formulations were prepared and coated over a white basecoat and stoved at 140 DEG C for 30 min. The samples were placed in a QUV accelerated weathering cabinet (4 hr. condensation cycle at 50 DEG C, 4 hr. UV cycle at 60 DEG C - UVB) and the color and gloss of the panels determined.
In all cases there was no loss of gloss on weathering over 2,000 hrs., and the yellowing behavior of DMP, DEM, and hybrid were all better than MEKO.
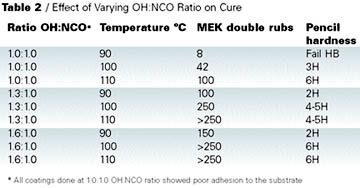
Resistance to Yellowing on Overbake
This test simulates a breakdown on a paint line; the resistance to yellowing is one of the key advantages of DMP-blocked isocyanates compared with MEKO-blocked isocyanates. A coating was applied to a primed steel panel over a white basecoat, cured at 140 DEG C for 30 min. and then cured for a further 30 min. at 150 deg C. The appearance was noted before and after baking. The coating based on MEKO-blocked isocyanate showed significant yellowing, whereas all other coatings remained as clear.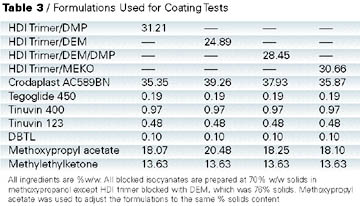
Acid Etch Resistance
Improved acid etch resistance is another advantage that DMP has over MEKO-blocked isocyanates. In this test 10% sulphuric acid (six drops) was placed on a cured coating and the panel heated. The temperature at which the coating started to mark was recorded. Table 4 shows that DMP outperforms all the other blocking agents, with the hybrid giving similar performance to MEKO.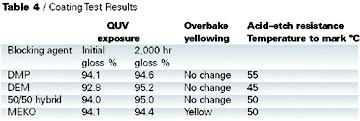
Adhesion
Adhesion test results are shown in Table 5. Cross-cut adhesion was tested on the coated panels and found to be acceptable for all the blocked isocyanates. However, when the adhesion was tested on a simulated repair, DMP-blocked isocyanate performed the least well (Table 6). In this test, a clearcoat was applied wet on wet to a basecoat, which was then cured at 140 deg C for 30 min. A fresh basecoat and clearcoat were applied on top of the cured coating and cured at 140 deg C for 30 min. Crosscut adhesion was re-tested. Close inspection of the failure confirmed that the original cured basecoat/clearcoat was intact and the adhesion failure occurred between the freshly applied basecoat and the previously baked clearcoat.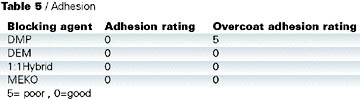
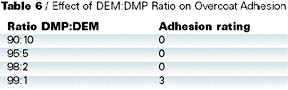
Conclusions
The combination of diethyl malonate and dimethylpyrazole as blocking agents gives formulators the flexibility to develop coatings to respond to a number of needs. At higher levels of DEM the cost-effectiveness is optimum, while at the same time having better in-can stability than isocyanates blocked entirely with DEM; yet at lower levels of DEM, the already good properties achieved by DMP-blocked isocyanates are enhanced by improvement to overcoat adhesion. Production quantities of the hybrid blocked isocyanate resins have been prepared and are available under Baxenden Chemicals Ltd.'s Trixene trade name. This chemistry is continuing to evolve and exciting developments in blocked isocyanate chemistry can be anticipated.
Acknowledgements
The assistance of Louise Bolton, Peter Hargreaves, Severine Michon and Ian Rimmer of Baxenden Chemicals is gratefully acknowledged. c
Crodaplast is a product of Cray Valley Ltd.
Tegoglide is a product of Th Goldschmidt.
Tinuvin is a product of Ciba Specialties.
For more information on isocyanates, contact Baxenden Chemicals Ltd., Paragon Works, Baxenden, nr Accrington, Lancashire, England BB5 2SL; phone +44/1254.872278; fax +44/1254.871247; visit www.baxchem.co.uk; or e-mail mail@baxchem.co.uk. Baxenden is represented in the midwestern U.S. by Archway Sales Inc., 4155 Manchester Ave., St. Louis, MO 63110; phone 314/533.4662; fax 314/533.3386; or e-mail rbeckmann@archwaysales.com; the West Coast is covered by Tri-Iso Inc., 480 N. Indian Hill Blvd., Suite 2A, Claremont, CA 91711; phone 909/626.4855; fax 909/621.9119; or e-mail service@tri-iso.com.
References
1 Wicks, Z. Progress in Organic Coatings 9 (1981) 3-28Wicks, Z. Progress in Organic Coatings 3 (1975) 73-99.
2 Wicks, Papas and Jones. Organic Coatings Science and Technology 2nd edition p 200 - Wiley Interscience 1999.
3 Thomas, R.O., ed. Waterborne and Solvent-Based Surface Coating Resins and Their Applications, p 149. SITA Technology, 1998.
Report Abusive Comment