Trends in UV-Cure Coating Formulations, Production Coating Methods and Apparatus
for Polymeric Film and Sheet High-Volume Consumer Product Categories

Two years into the worldwide Great Depression, which began in the United States on October 29, 1929, Plexiglas™ and Lucite™ - polymethyl methacrylate (PMMA) - were invented in two different companies’ laboratories on two different continents.
Polyethylene was first discovered by two chemists at ICI in England by accident in 1933. After five years of R&D efforts, commercialization became possible.
In the middle of the Great Depression era, circa ~1935, BASF first produced polystyrene, and RCA Victor introduced vinyl-based phonograph records – having twice the groove density of shellac records with far superior sound quality. This aided the growth of the entire music industry from phonograph records and record playing devices, making available a wide array of recorded audio music venues to consumers, raising their spirts worldwide.
Nylon was invented and patented by DuPont in 1935, with an explosion in popularity of women’s nylon stockings – producing an immediate success.
In 1938, chemist Roy Plunkett, also of DuPont, discovered Teflon – now commonly found in nearly all household kitchenware and commercial bakeware.
In 1941, polyethylene terephthalate (PET) was discovered in Great Britain.
In 1948, acrylonitrile butadiene styrene (ABS) was created with its subsequent incorporation into countless number of molded components, subcomponents and devices.
In 1950, DuPont commercialized polyester.
The 1950s saw initial research of photopolymer UV and EB+ chemistries, driven by marking and coding applications for cans, components, labels and packaging. Initial methods and apparatus were of flexography, gravure, offset and screen printing. Use of inkjet printing had to wait until the 1970s for computers and the precursor of dot matrix printers to allow for the scope of inkjet printing using solvent-based and/or UV-energy-cure inks to first emerge.
In 1951, chemists J. Paul Hogan and Robert L. Banks of Phillips successfully polymerized propylene to create polypropylene.
In 1953, chemists Daniel Fox at General Electric and Hermann Schnell at Bayer AG invented a new form of polycarbonate resin thermoplastic – Lexan™ and Makrolon® respectively – both of which the author has electroless plated and conformal coated. Nearly all wireless devices – mobile, smart phones, notebook and/or tablet computer enclosures are made from polycarbonate or polycarbonate-base alloys.
1954 brought the invention of expanded or foamed polystyrene – Styrofoam™ – used in countless packaging, cups and as building insulation.
In the early 1960s, high-density polyethylene bottles were introduced, essentially replacing glass in soft drink packaging.
In 1965, chemist Stepahanie Kwolek developed a light, highly resistive and durable plastic aromatic polyamide or Aramid, woven into fibers – commercially known as Kevlar®.
In the 1980s, polyester film stock replaced cellulose acetate for photographic film, computer storage, reel-to-reel audio and video tape.
In 1983, ICI and Bayer introduced polyether ether ketone (PEEK), polyphenylene sulphide (PPS) and polyether sulphone (PES), all of which the author has electroless plated and conformal coated.
In 1987, BASF introduced polyacetylene with double the electrical conductivity of copper.
In 1988, the first polymer monetary bank notes were issued in Australia.
In 1990, ICI introduced Biopol – the first biodegradable plastic produced on a commercial scale (Figure 1).
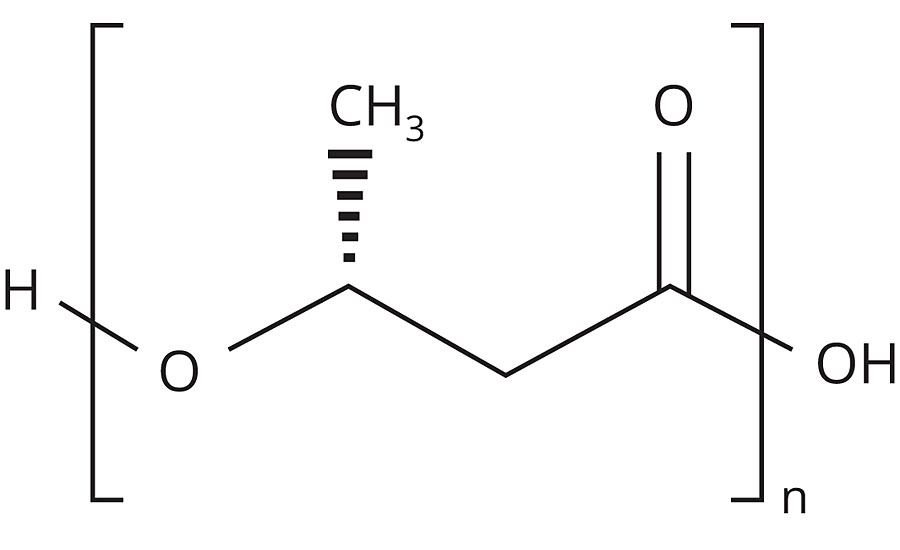
Polymer Materials
Polymer materials may be fabricated using one or more of the methods listed in Table 1.
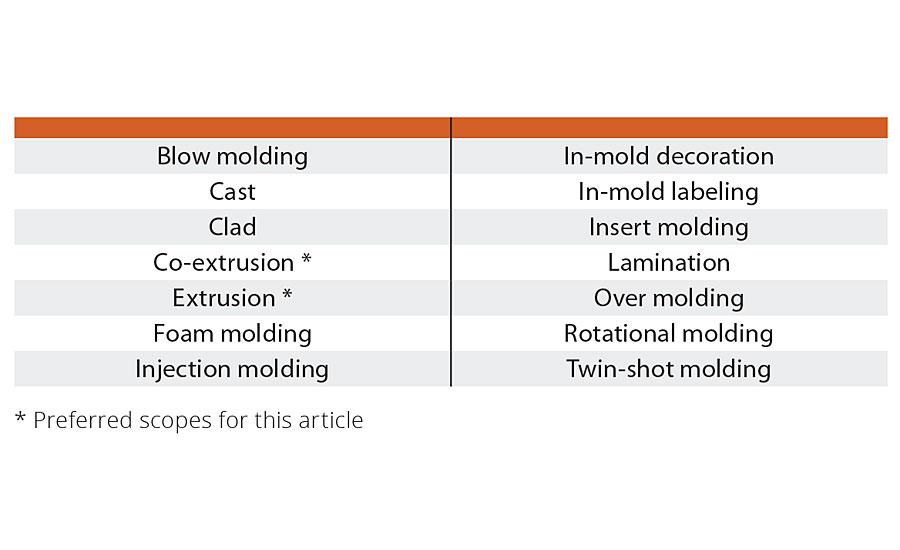
Extruded plastic is of a high-volume method and apparatus where one or a plurality of plastic materials are melted and formed in a continuous profile with the heat of friction from the extrusion process along with profile heating through various forms of dies. Once sufficiently cooled below a plastic’s glass transition temperature (Tg), outcome yields a continuous two- or three-dimensional profile shape, creating an entirely new scope of uses for plastics (Figure 2).
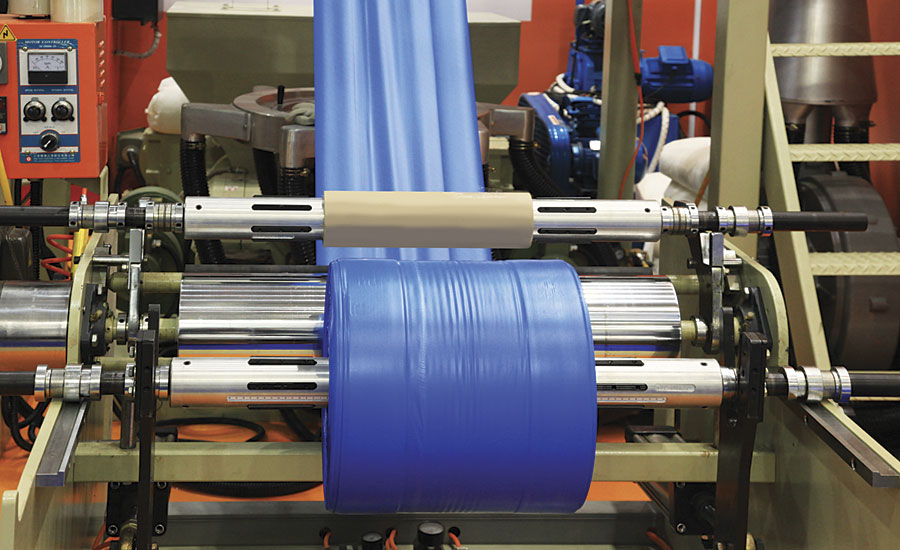
In the early 20th century, the first extrusion apparatus were for rubbers – reprocessing of waste rubber and for uniformly mixing additives into rubbers. The first thermoplastic extrusion apparatus for rubber was by Paul Troester of Hamburg, Germany, followed by Roberto Colombo of LMP, who is credited with developing the first twin-screw extrusion apparatus in Italy.
Common uses for extruded plastics include but are not limited to deck railing, fencing, film and/or sheet, piping, tubing, weather stripping and wire insulation.
Plastic’s various co-extrusion and extrusion methods and apparatus are characterized by:
- Blown film – very thin polymer film for packaging or continuous web sheet outcome;
- Coating – where a secondary heated resin is applied via pressure rollers onto moving extruded web outcome;
- Co-extrusion – where a plurality of extruders feed a single die to create a multiple layer outcome;
- Compound extrusion – where a plurality of polymers and/or additives produce a homogenous outcome;
- Extrusion coating – where a thin polymer layer is added upon film, foil and/or paper web outcome;
- Film extrusion – where polymer is a continuous two-dimension extrusion of less than 0.030” (0.76 mm) thickness but greater thickness than that of blown film outcome;
- Extrusion lamination – where hot extruded polymer resin acts as the bonding medium to a second web – sans adhesive-use outcome;
- Sheet extrusion – where polymer is a continuous two-dimensional extrusion greater than or equal to 0.030” (0.76 mm) thickness and a curfed outcome;
- Tubing extrusion – where method and apparatus allow for a continuous portal in the drawn direction outcome.
The most commonly available polymer film/sheet substrate materials are listed in Table 2. Pursuant to the scope of this article, cast, co-extruded and/or extruded polymer film/sheet and/or materials may be manufactured by a variety of options for end user-desired specifications use intentions, such as:
- Clear
- Laminate
- Opaque
- Pigmented/colorants
- Effect pigments
- Translucent
- Transparent.
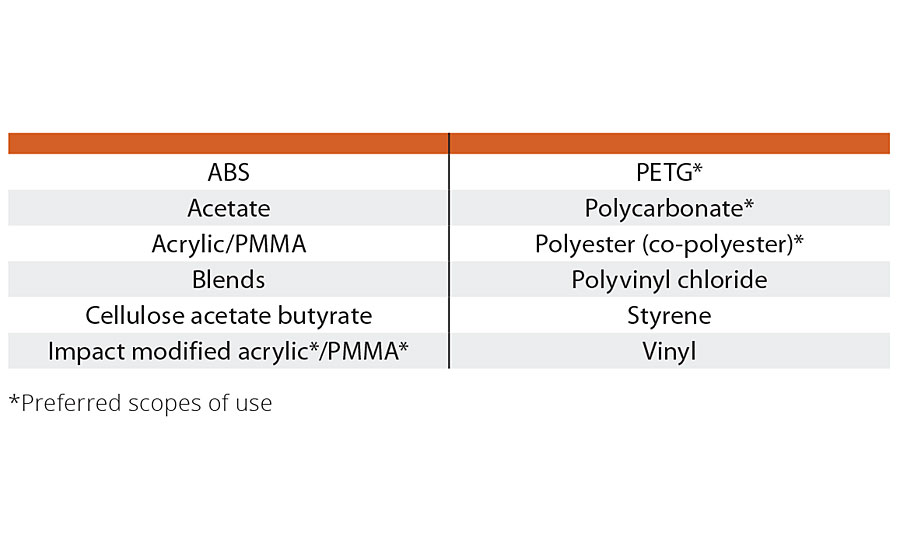
Just as one size does not fit all, cast, co-extruded and/or extruded polymer film/sheet chromatic and/or indicia methods may consist of:
- Conformal coating
- Embossing
- Lamination
- Physical vapor deposition - PVD
- Plating-on-plastics - POP
- Printing
- Resin-based.
In addition, cast, co-extruded and/or extruded polymer film/sheet methods and apparatus for various fabrication final geometries may consist of:
- Flat – two-dimensional
- Bendable – three-dimensional simple
- Formable – three-dimensional complex and/or deep draw
- Moldable – three-dimensional complex.
Furthermore, cast, co-extruded and/or extruded polymer film/sheet materials, methods and apparatus for applied chromatics and/or indicia – selective or full bleed for consumer and/or industrial use may consist of:
- Adhesives
- Coatings
- Inks
- Overprint varnishes.
Formulation materials, methods and apparatus for UV/EB+/IR use may be:
- Aqueous* – dry
- Aqueous/alcohol* – dry
- Solvent* – dry
- 100% solids – UV cure.
- Mixed dry/cure systems available
Just as consumers seek the greatest values for their retail purchases, point-of-sale retailers (especially Big-Box retailers in every major country) use their massive buying power, national or worldwide locations and logistics to drive down pricing to generate new sales dollars and increase brand loyalty from consumers, while maintaining their targeted financial EBITDA – earnings before interest, taxes, depreciation and amortization – in other words, profits.
Tried-and-true materials, fabrication and/or manufacturing processes of the past may not have the capability to achieve the targeted costs, volumes, time to market and/or consumer trend product outcomes desired.
Every fabrication, manufacturing and/or process operation is specific to the exact combination of materials, methods and apparatus incorporated for the desired or intended outcomes – while at the lowest costs and highest reliabilities that are production process attainable.
For example, a solvent-based coating or ink material is going to be priced below its water-based equivalent simply because of much lower weight solids of solvent-based materials. Alcohol-based formulations generally have weight solids between solvent-based and water-based coating and/or ink formulations.
Then one needs to address the precise method of application – which generally involves losses due to component geometries as well as the transfer efficiencies of the application method chosen specific to the material transfer medium of choice – aqueous, aqueous/alcohol, solvent or 100% solids. Lowest material price may not be a true reflection of lowest methods and apparatus cost outcome.
More notably, processing energy, losses, space and/or time requirements incurred for a wet film state transitioning into a dry film state is a highly complex challenge – and perhaps one not so readily apparent. Every wet film, particularly of a horizontal surface and/or any wet film surface subject to heated and moving air flow – which is de-rigueur for accelerated tunnel and/or batch oven drying of a wet film into a completely dry film state creates a rich debris-filled processing environment with subsequent processing losses, sometimes as high as 50% – generally all of which are economically nonrecoverable, thus increasing the COG (cost of goods).
Incorporation of new materials, methods and apparatus can have significant bottom line, production efficiency and through-put impacts, often resulting in novel and/or new fabrication, manufacturing and/or processing outcomes, replacing former tried and true materials, fabrication and/or manufacturing processes. Such is witnessed through the scope of decoration and/or indicia applied upon polymer film/sheet for high-volume and/or high-value consumer and industrial products of the metrics and dynamics presented herein.
Method and Apparatus for UV & EB+ Energy Cure
Coatings and Adhesives
- Curtain coat
- Dip (immersion) coat
- Flow coat*
- Roll coat*
- Spray coat
* Preferred embodiments
Of the above-noted coating and adhesive methods and apparatus specific to polymer film/sheet, it is assumed a full bleed or 100% coverage is the desired scope. Incorporation of selective application is possible through use of selective methods and apparatus, removable tape and/or masking equipment that may be employed.
Curtain coating is commonly used when conformal coating a low-profile, three-dimensional surface – such as embossing or added surface components.
Dip or immersion coating may be employed where polymer film/sheet may be of a vertical method and/or apparatus, such as large cast sheets or of web film such as in fabricating color light filters used in lighting for live broadcasting, filming, theatrical and/or musical stage productions.
Flow coating is employed where highest purity and/or light transmittance is required – such that only the applied coating touches the polymer film/sheet – high-end optical and/or medical environments.
Roll coating is employed where high coating precision, tolerance and low thickness is desired through pressure of the transfer roller and/or material application.
Spray coating is generally not engaged due to limitations due to dry spray from atomization, nonuniformity, overspray, processing time, spray footprint and/or transfer efficiency losses.
Incorporating UV & EB+ energy cure materials to any of the above five methods and apparatus provide combined features and/or advantages of:
- 100% material transfer use;*
- Ability to coat 1st and/or 2nd surfaces in one continuous processing operation;*
- Allows for immediate on-line and/or in-line monitoring and real time QC;
- Elimination of batch and/or tunnel-heated forced air drying and energy costs;
- Elimination of final dimensional variations;
- Elimination of induced curling and/or warping due to solvents and/or cosolvents;
- Elimination of wet to dry film debris issues and losses;*
- Maximum film/sheet process throughput;*
- Minimize processing line space requirements;
- Near-zero airborne VOC emissions;*
- Near-100% elimination of hazardous waste disposal costs and cradle-to-grave liability;*
- Reduction of overall carbon footprint.
*With the exception of spray coating
Adhesives and Inks
- Digital printing
- Flexographic printing
- Gravure printing
- Lithographic printing
- Offset printing
- Pad printing
- Screen printing.
Of the above noted adhesives and inks methods and apparatus specific to polymer film/sheet, it is assumed a full-bleed or 100% coverage of adhesives, white for opacity, chromatics and/or selective indicia in one or a plurality of colors for 1st, 2nd or combined polymer film/sheet surfaces to the desired scope intended.
Digital printing allows for near-unlimited options for adhesives, chromatics and/or indicia without the need for any secondary method and/or apparatus. Furthermore, polymer film/sheet finished dimensions are limited only by the apparatus printing width, length of the polymer film/sheet and Z-axis apparatus processing capability – web and/or sheet format.
Flexographic printing allows for adhesives, chromatics and/or indicia specific to polymer film/sheet dimensions up to the secondary method and/or apparatus width of the press, circumference of the roller and capability of Z-axis apparatus processing capability – web and/or sheet format.
Gravure printing allows for adhesives, chromatics and/or indicia specific to polymer film/sheet dimensions up to the secondary method and/or apparatus width of the press, circumference of the roller and capability of Z-axis apparatus processing capability – web and/or sheet format.
Lithographic printing allows for adhesives, chromatics and/or indicia specific to polymer film/sheet dimensions up to the secondary method and/or apparatus width of the press, circumference of the roller and capability of Z-axis apparatus processing capability – web and/or sheet format.
Offset printing allows for adhesives, chromatics and/or indicia specific to polymer film/sheet dimensions up to the method and/or apparatus width of the press, circumference of the roller and capability of Z-axis apparatus processing capability – web and/or sheet format.
Pad printing allows for adhesives, chromatic and/or indicia specific to polymer film/sheet dimensions up to the method and/or apparatus limitation of the pad print cup diameter, number of ink stations and/or if single or dual-printing scope – generally of a sheeted format.
Screen printing allows for adhesives, chromatic and/or indicia specific to polymer film/sheet dimensions up to the method and/or apparatus screen size, screen mesh and number of color stations – web and/ or sheet format.
Incorporating UV & EB+ energy cure materials to any of these seven methods and apparatus provide combined features and/or advantages of:
- 100% material transfer use;
- Ability to coat 1st and/or 2nd surfaces in one continuous processing operation;
- Allows for immediate on-line and/or in-line monitoring and real time QC;
- Elimination of final dimensional variations;
- Elimination of induced curling and/or warping due to solvents and/or co-solvents;
- Elimination of batch and/or tunnel forced hot air dry and associated energy costs;
- Elimination of wet to dry film debris issues and losses;
- Maximum film/sheet process throughput;
- Minimize processing line space requirements;
- Near-zero airborne VOC emissions;
- Near-100% elimination of hazardous waste disposal costs and cradle-to-grave liability;
- Reduction of overall carbon footprint.
Overprint Varnishes
- Coating
- Printing
Overprint varnish (OPV), by definition, is the addition of a protective coating upon already printed surfaces without limitation – similar to da Vinci’s oglio cotto. The scope of overprint varnish materials, method and apparatus is also for adding gloss to uncoated and/or unprinted substrate surfaces.
A limited degree of protection from abrasion, chemicals, marring and/or scratch resistance may also be achieved through incorporation of overprint varnish.
While an OPV may be of aqueous, aqueous/alcohol, solvent and/or 100% solids UV material formulations, the preferred embodiment is for UV 100%-solids materials to take full advantage of combined materials, method and apparatus to achieve uniform and controllable applied thicknesses far below one micron, measured in bcm - billions of cubic microns.
OPV methods and apparatus traditionally use anilox print rollers, having greater than 1,000 cells per linear inch for varnish transfer to substrate surfaces. Advances in methods and apparatus now present newer and more advanced roller coating scopes, such that OPV materials, method and apparatus may employ coating and/or printing ranges of use for high-volume and/or high-value consumer products.
While traditional OPV formulations offer a limited degree of abrasion, chemical, marring and/or scratch resistance, current OPV material formulations have two major use limitations:
Substrate surfaces, especially of applied darker chromatics and/or indicia upon industry-wide fiberboard packaging are readily malleable such that the protective OPVs and the underlying applied chromatics and/or indicia are readily abraded, marred and/or entirely scratched away from the fiberboard substrates – resulting in cosmetic packaging defects, similar to what is termed “box burn” in decorative conformal coating and/or foils use upon molded plastics.
OPVs by nature, not being malleable, will be unable to address scopes of use where polymer film/sheet are elongated through forming operations, lamination and/or in-mold decoration where three-dimensional outcome geometries are desired, due to OPV delamination, fracture and/or separation from elongated polymeric substrate surfaces.
New OPV UV-energy-cure technologies are coming to market addressing current OPV material and/or method limitations - having chemical, functional, mechanical and/or physical combined features and/or advantages improvements in:
- Abrasion resistance
- Chemical resistance
- Cross-hatch adhesion
- Formability
- Gloss levels
- Pencil hardness
- Scratch and/or mar resistance
- Solvent rub resistance.
Materials, method and apparatus venues of applied chromatics and/or indicia upon cast, co-extruded and/or extruded polymer film/sheet substrates:
- Clear – first or second surfaces
- Laminate – first surfaces
- Opaque – first surfaces
- Translucent – first or second surfaces
- Transparent – first or second surfaces.
Each of the above five outcomes may be readily attainable without limitation through incorporation of new OPV UV-energy-cure coating technologies applied upon cast polymer sheet, co-extruded and/or extruded polymer film and/or sheet.
Materials, methods and apparatus of UV-energy cure:
- UV-A 400-315 nm ~black light
- UV-B 315-280 nm ~biological hazard
- UV-C 280-200 nm ~germicidal.
UV energy cure of UV-B and UV-C wavelengths have sufficient excitation energy to be employed by all three major UV polymer crosslinking technologies:
- Anionic
- Cationic
- Free radical.
Electron beam or EB+ energy cure is of beta radiation – b, very high-kinetic-energy electrons, generated, accelerated and target focused via induction mechanisms to crosslink polymers. EB+ is also common of hospital, medical and/or pharmaceutical environments for the purpose of pathogen sterilization.
Crosslinking polymerization should not be confused with chain polymerization, where polymerization is of monomer additions at the end(s) of growing polymer chains. Note that UV energy cure may also engage chain polymerization in conjunction with polymer crosslinking.
Anionic polymerization was engaged by the author as an organic chemistry Ph.D. candidate using strong and highly unstable lithium metal ligand groups rather than conventional electron transfer mechanisms. It may be considered a living (on-going) polymerization process, continuing until impurities, increased viscosity, monomer concentrations and/or polymer crosslinking density essentially terminate the reaction mechanisms.
Cationic polymerization involves cycloaliphatic epoxies and/or a plurality of other cationic monomers, crosslinking through the mechanism of a weak Lewis acid generated by photo initiators and is also considered a living polymerization mechanism.* (*Preferred embodiment for the scope of this article.)
EB+ or electron beam may be engaged to decompose photoinitiators in generating weak Lewis acids.
Free radical polymerization involves generation of free radicals - C·, through photoinitiators reacting with carbon alkene double bond C=C monomers to polymerize. Unlike anionic and cationic polymerization, free radicals can only be generated by photon excitation and immediately cease once the UV excitation energy source terminates.
EB+ or electron beam may also be employed in opening C=C bonds without photoinitiators. Research promulgates mixed systems combining free-radical and cationic polymerization.
Examples
Household and commercial kitchen and/or laundry major appliances traditionally incorporate brushed, polished and/or oxidized stainless steels and/or cold rolled galvanized steels with applied conventional conformal industrial coatings in a variety of chromatics and/or texture effects upon formable sheet metal operations for cosmetic, functional and/or brand marketing purposes.
Household and commercial kitchen and/or laundry major appliance sheet metal forming, bending, stamping and/or fabricating operations for galvanized formable steels and stainless steels are truly massive in size and scope. Suppliers of galvanized sheet metal deliver rolls and/or sheets free of surface defects and imperfections – cosmetically flawless galvanized sheet metal ready for appliance-forming operations, including post-forming application of decorative and/or functional industrial coatings of specified chromatics and/or effect pigments desired (Figure 3).
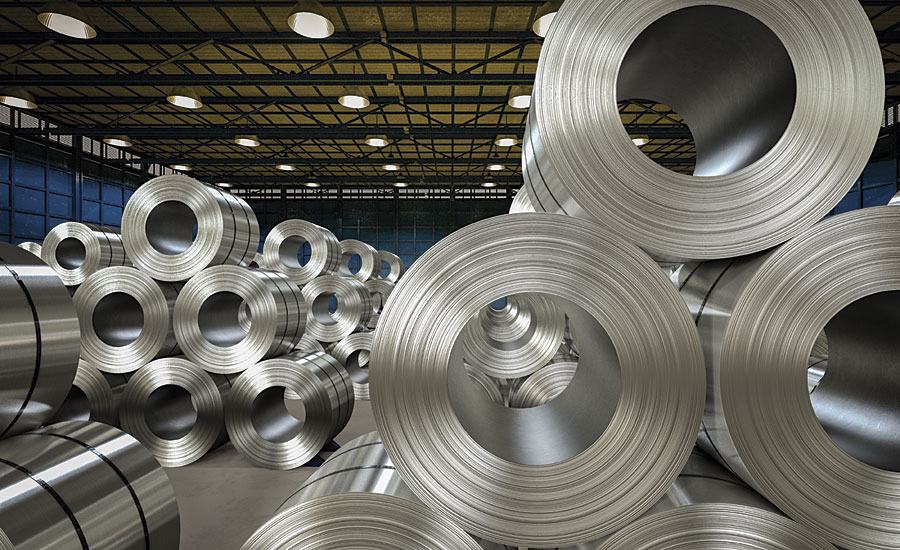
Since galvanized cold rolled steels are decorated after conventional sheet metal-forming operations, significant care and cost is undertaken by sheet metal-forming operations to minimize surface defects imparted during forming and handling, so as to not telegraph processing and/or handling defects through the applied conventional industrial coatings, and become visible upon the final decorated appliance surface, resulting in a nonrecoverable four-, five- or six-sided sheet metal substrate housing and/or sub-component, i.e. – scrap.
Stainless steel appliance surfaces - brushed, oxidized and/or polished while generally not engaging of a secondary conformal coating other than an OPV for fingerprint protection, none-the-less require absolutely flawless material surfaces to be maintained throughout far-more challenging stainless sheet metal jigs, tooling, forming, handling and fabricating operations of four-, five- and/or six-sided stainless steel sheet metal substrate housings and/or subcomponents (Figure 4). Pure stainless steels may be readily recycled allowing some economic loss recovery.
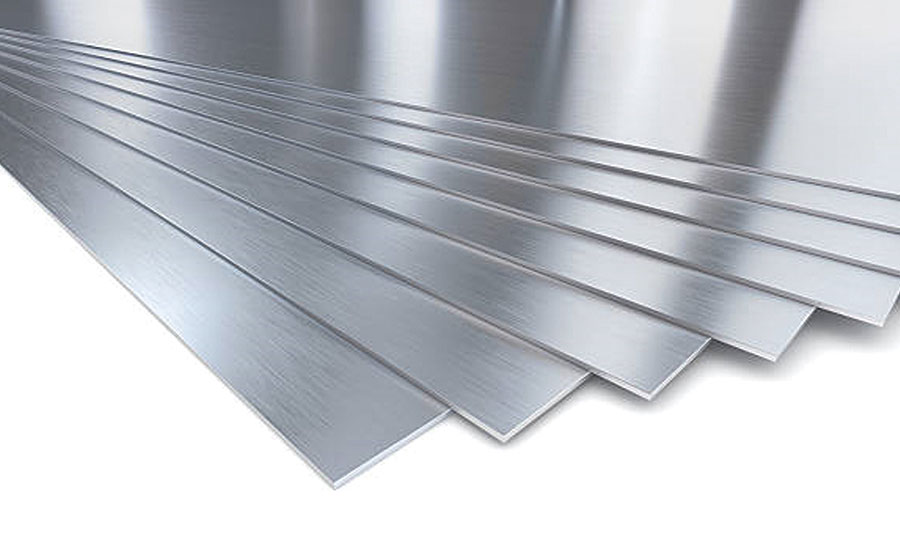
Major appliance sheet metal department managers and/or sheet metal contract manufacturing businesses use conventional materials, methods and apparatus for kitchen and laundry appliance forming, industrial coating decoration and/or fabrication.
In the February, 2018 issue of PCI Magazine, features and benefits from incorporation of decorative and/or functional cationic precoating of deep draw steels with manufacturing, fabrication and/or assembly operations for major appliances was presented. Herein is presented another new and novel alternative material, method and apparatus scope to incorporate polymeric film/sheet engaging first and or second surface chromatics and/or indicia design without limitation through the range of cationic UV energy cure coatings upon polymer film/sheet first surface protection without limitation.
Any appliance OEM and/or sheet metal contract manufacturer engaging cationic UV energy cure coatings upon polymer film/sheet for incorporation upon kitchen and/or laundry appliances can benefit from two new features and/or advantages – coating and/or printing of chromatics and or/indicia are without limitation – design, color, chromatic, volume, etc. What cannot one print or coat upon a polymeric surface of design, chromatics and/or indicia? Second and perhaps more significant is that sheet metal-forming operations only need to produce clean and dimensionally stable steel components and/or subcomponents. Appliance decoration and/or indicia are done through assembly – in-house or out-sourced, as cosmetic and/or indicia polymeric film/sheet become an assembly line operation, such as through incorporating a dedicated work cell, without limitation. A true dream come true for formable sheet metal operators and management.
Another benefit involves healthcare. According to the Centers for Disease Control and Prevention or CDC, in 2011, one person in seven admitted to a hospital in the United States acquired an infection simply from being in a pathogen-rich environment of a hospital – regardless of the scope of the hospitalization (Figure 5). Infections caused by antibiotic-resistant bacteria alone killed 23,000 people in 2011, made two million persons sick and cost $35 billion in lost productivity due to sick days within the United States. Of these one-in-seven persons acquiring a hospital infection (HAI) – in 2011 totaling 722,000 persons – 75,000 patients succumbed to HAIs from any one of five major classes of pathogens. Today this early mortality number likely exceeds 100,000 patient deaths annually – just within the United States, much less than worldwide HAI mortality rates.
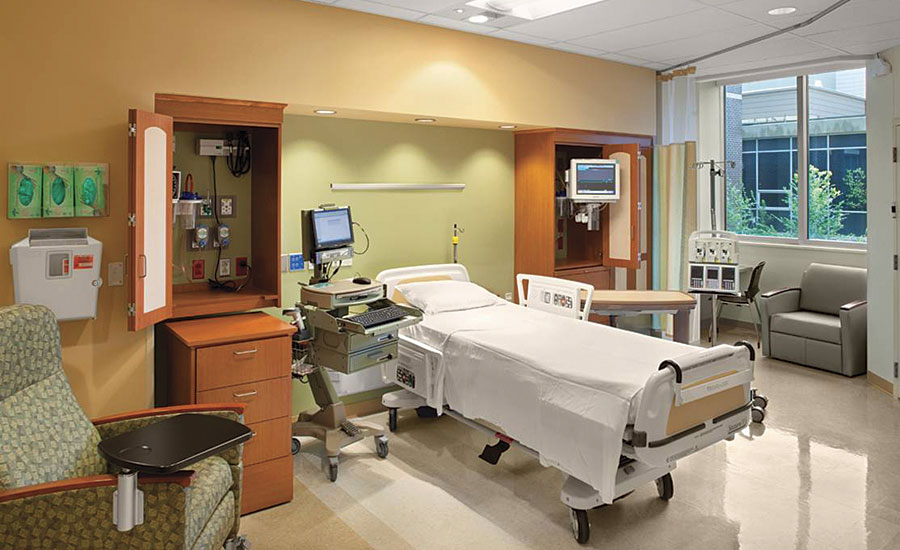
HAIs have become health insurer’s, hospitals’ and government’s number-one health care cost, with average HAI hospital stays of an additional seven to 10 days often in acute or critical care. Recalcitrant pathogens of (but not limited to) CDI, HAI, MSRA and VRE domains can be found in dental, emergency room, hospital, laboratory, medical, surgical and trauma center environments with cross-communication of pathogens leading to increasing mortalities.
One novel remedy for reduction in HAI recalcitrant pathogens is the incorporation of pathogen deterrents directly upon first and second surfaces of the billions of formed polymer film/sheet disposable components, devices and/or medical procedure kit enclosures and/or packages used throughout dental, emergency room, hospital, medical, surgical and/or trauma center environments. Irrespective of EB+ irradiation sterilization and/or high-temperature sterilization methods – doctors, patients, staff and/or visitors all have one common element – all touch and/or handle physical objects including (but not limited to) charts, computer keyboards and/or touch screens, body fluids, blood, door handles, draping, exchange monies, foods, lavatories, light switches, mobile devices, patients, sterile environs, telephones and/or wastes, thus cross-communicating pathogens within and throughout pathogen-rich healthcare environs.
Presidential Executive Order 13676 of September 18, 2014 – Combating Antibiotic-Resistant Bacteria – establishes a Task Force headed by Secretaries of Defense, Agriculture and HHS with representatives from 10 Federal Agencies.
Use of cationic UV energy cure formulations containing pathogen deterrents upon polymeric film/sheet allows for pathogen deterrents to be communicated of efficacy CFU/mL R values of 6+ with efficacy contact times under 30 seconds without limitation of planktonic, monolayer and biofilm bacteria as well as gram-negative and gram-positive bacteria, as a barrier to pathogen cross-contamination while rendering the pathogens deterred and/or dead.
Conclusion
UV-cure cationic coatings present viable and attractive options to OEMs, polymer coaters, extruders, contract coaters and/or thermoformers to improve functional and/or physical properties for formed polymer film/sheet as well as an effective delivery transport mechanism for new pathogen inhibition and biocidal efficacy technologies.
Author Note:
The author wishes to thank UV Specialties, LLC of St. Charles, Illinois, and Mr. Dewey Mason, Technical Director, for his contributions.
Looking for a reprint of this article?
From high-res PDFs to custom plaques, order your copy today!