Improving Corrosion Resistance of Powder Coating Systems for ACE Applications

Allnex has recently developed a generation of modified superdurable polyesters for powder coatings, demonstrating improved corrosion resistance for ACE applications. The binders based on these polyesters, hardened with b-hydroxyalkylamide, are expected to compensate observed performance gaps of novel environment-friendly anti-corrosive pre-treatment solutions like nano-ceramic systems, relative to current systems like zinc or iron phosphate on steel, and yellow chromate on aluminum surfaces.
The objective of this article is to illustrate our company’s findings that have improved corrosion resistance after salt-spray tests (ASTM B-117) on both pre-treated and untreated shot-blasted substrates for ACE applications. It will also cover the potential use for the same application of alternative binders based on triglycidyl-isocyanurate (TGIC- Araldite® PT 810) and blend of triglycidyltrimellitate and diglydicylterephthalate (PT 910-Araldite PT 910).
Introduction
Powder coating is an advanced, fast-growing technology that is widely recognized for its durability, gloss retention, weatherability, ability to apply up to 200 microns-high thickness, and unlimited range of colors, finishes, glosses and textures. All this, combined with its ability to prevent corrosion on metallic substrates (considering that corrosion has a global estimated annual direct cost of ca. $2.200 billion, which accounts for over 3% of the world’s GDP1), makes powder an important technology in the coatings world.
In addition to the points made above, powder coatings provide solvent-free finishing and almost 100%-recyclable processes, making them an important part of a sustainable or green building project that incorporates low VOC-emitting products.
Regulations and opinion leaders require, however, further improvements in environmental friendliness of powder coating producers and end users, including the processes and materials used in the different pre-treatment steps of the metal substrates. This, while continuing to comply with the guarantee and warranty level of corrosion protection as stipulated in existing accreditation systems.
It is indeed known that surface pre-treatment for corrosion protection of metal substrates has a strong impact, from an environmental perspective,2 as illustrated by the current wide-spread use:
- On steel: iron and (even more) zinc phosphate;
- On aluminum: yellow hexavalent chromium, which is associated with DNA damage and cancer, and is the main reason for legislation against anticorrosion coatings.3
The recent introduction in the market of more environmentally friendly pre-treatments, like nano-ceramics and titanium- or zirconium-based systems, has evolved in parallel with the need for better corrosion-resistant coatings that balance their lower efficiency, when used at the same extent and/or cost.2
While suppliers are continuing to improve the performances of their pre-treatments, Allnex is targeting to develop a new generation of cost-competitive resins able to further improve corrosion resistance of powder coatings for ACE applications.
This article will begin with a short review of the mechanisms of corrosion and the typical prevention and analysis methods, followed by a detailed overview of the experimental work that has led to the development of new superdurable polyester for ACE applications in combination with ß-hydroxy-alkyl-amide (ß-HAA), triglycidyl-isocyanurate (TGIC), and a blend of diglycidylterephthalate and triglycidyltrimellitate (PT 910). It will cover more general findings and our next steps of research and development.
Basics of the Mechanism of Corrosion
Corrosion is defined as an electrochemical deterioration of a metal due to the reaction with its environment involving the oxidation of a metal and the reduction of another material,4 which results in the breakdown in the metal (corrosion).
Factors influencing corrosion are:
- The presence of water, oxygen and ions, which reduce the ohmic resistance provided from the presence of a coating between the metallic substrate and the corrosive environment;5-6
- The adhesion to the substrate;
- The porosity and thickness of coating film;
- The cleanliness of the substrate from grease and rust.
Corrosion resistance of coatings is dependent on their barrier properties, and generally varies with the nature of the film-forming polymers and paint formulation used. It has been found that permeation of moisture and corrosive gases negatively affects the adhesion and, in many cases, results in corrosion of the substrate. Failures in coating adhesion also deteriorate the protective properties of coatings.
The barrier properties of polymer films towards water have been shown to be dependent on the sorption and the diffusion behavior of water. Sorption-desorption studies indeed show that moisture readily passes into the paint films, but that the rate of desorption varies according to the type of binder and pigmentation used.7,8
Permeation of gases through the film has been shown to involve three main processes:
- Dissolution of permeating species in the films at the high-pressure surface;
- Diffusion of dissolved gases through the film along a concentration gradient;
- Re-evaporation of gases from the low-pressure surface of the film.
For corrosion protection by the application of a surface coating to the substrates, four schemes are applied normally:
- Barrier coatings to separate the electrodes from the electrolytes;
- Addition of inhibitors/passivating partially soluble inhibitive pigments and/or additives;
- Addition of cathodic/sacrificial protection (example zinc, phosphates, borates, molybdates, zirconate-rich coatings);
- Improvement of adhesion to reduce water and oxygen permeation.
Methods to Improve Corrosion
Typical methods to improve corrosion resistance include the following.9
Substrate Pretreatments
- Conversion coatings, which act as a base for paints and at the same time provide corrosion protection. It is a slightly acidic aqueous solution (water-based) of chemicals. Iron or zinc phosphates are the most common chemicals in the formulation, although other chemical salts are also added to perform various functions. The metal is immersed in a tank containing the solution and, while immersed, the metal dissolves very slightly and the phosphate actually plates out onto the clean metal. The coating thickness is normally less than 100 nm. Both zinc and phosphate are considered to be environmentally unfriendly;
- Wash primers that passivate the surface and temporarily provide corrosion resistance; this to provide an adhesive base for the next coating. They are water-based formulations of phosphoric acid in solutions of vinylbutyral resin, alcohol and other ingredients such as zinc chromate and have a dry film thickness: 8-13 microns;
Electro Coating (in OEM and ACE Processes)
- This method employs an electric current to deposit an organic finish; a process that uniformly applies thin-film primers and one-coat finishes to metallic substrates. Four steps are involved in this process: a) substrate cleaning, b) conversion coating, c) sealing, d) drying-curing, and cooling. The coating thickness is dependent on the immersion time, the bath temperature, the process voltage and the bath chemistry;
Use of Main Primers
- Their functions are to protect the substrate from corrosion for at least 10 to 15 years. They ‘seal’ the surface so that the solvents or water of top coats will be able to evaporate away as they were designed to, and will create a barrier to oxygen, moisture and corrosive compounds at the metal surface. The most common binder chemistries are polyurethanes, epoxy, moisture-cured urethanes and fluoro polymers (mainly used in coil coatings).10 Additives that can be incorporated into primer coatings are: anti-corrosion pigments/corrosion inhibitors, active pigment corrosion inhibitors or passive pigment corrosion inhibitors.
It is important to remember that in ACE applications, coatings are required to keep both protective and aesthetic performances for a long time, but that degradation of aesthetics, like blistering and dripping of rust, is happening earlier than a serious degradation of the structural properties of the metallic substrate.11
Analysis Methods
Typical analysis methods done in order to check corrosion resistance are:
- Salt-Spray Test (ASTM B-117): A 5% sodium chloride solution is sprayed by means of a nozzle into a closed chamber to produce a static fog. The panels with an Andreas cross are suspended in this for a prescribed period of time, while the temperature is kept constant at 35 °C
- Controlled Humidity Test (ASTM D2247): Estimates the influence of moisture on corrosion. The samples are exposed to 100% relative humidity at 40 °C
- Filiform Corrosion Test (ASTM D2803): Scribed panels are placed in a corrosive atmosphere (salt spray for 4 to 24 hrs) or immersed in a salt solution and are exposed to humidity (25 °C and 85% relative humidity).
- Prohesion (ASTM G 85-A5): Scribed panels are placed in a weaker corrosive atmosphere alternative cycles at room temperature and at 35 °C.
- Electrochemical Tests like Electrochemical Impedance Spectroscopy (EIS) on intact or scribed panels have the advantage of continuously recording the variation of resistance and capacity, and are able to relate with corrosion mechanism, but need a skilled person in order to fully understand the results. Further electrochemical test methods include Potentiodynamic polarization as well as others.
An Important Market Need
Our company’s Powder Coating Resins Technology department is aiming to develop a solution to answer exactly this important market need: Introduce an environment-friendly powder coating solution that provides outstanding corrosion resistance even when applied on less-efficient anti-corrosion pre-treatments.
Although there will be intermediate offerings, the project’s ultimate goal remains the provision of powder coating resins able to substitute in terms of corrosion resistance performances, even when applied on solely shot-blasted panels, epoxy powder coatings and/or, the actual benchmark powder coatings applied on standard pre-treated substrates (initially iron-phosphate and in the future zinc-phosphate).
Moreover, the study will demonstrate that improvement of corrosion resistance performances on solely shot-blasted steel are clearly replicated when the same powder coatings are applied on iron or zinc-phosphate pre-treated panels.
Experimental Results
Table 1 summarizes the targets of the project. With the exception of the salt spray resistance, the other targets are typical application properties of superdurable offerings for ACE applications. Solely shot-blasted steel substrates were selected as the ultimate target, being more commonly available and the most stringent from a corrosion perspective.
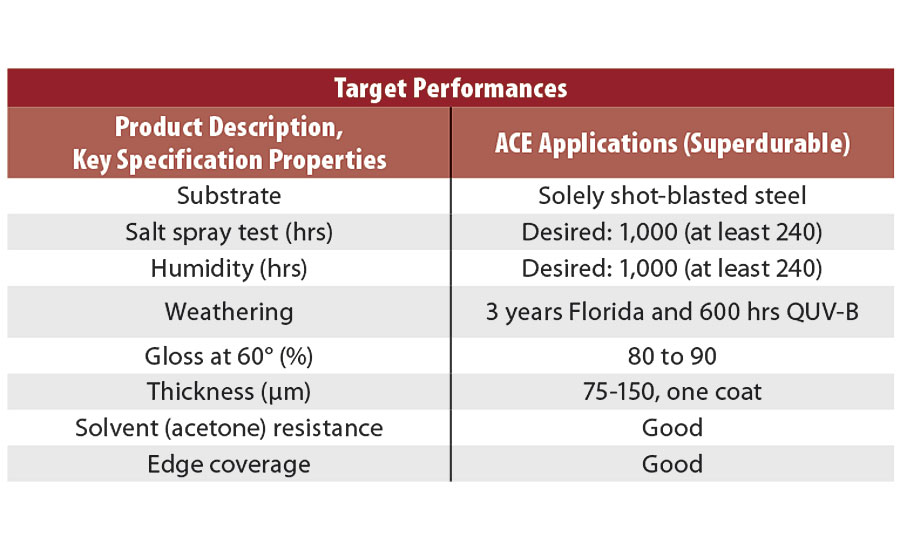
Superdurable Powder Coatings Based on ß-Hydroxy-Alkyl-Amide for ACE Applications
The powder coating formulation used for all the tests is shown in Table 2. It contains 65% of binder and is based on a polyester and ß-hydroxy-alkyl-amide hardener, with titanium dioxide only in the pigment-filler part. It’s exempt from any anti-corrosive pigments/additives.
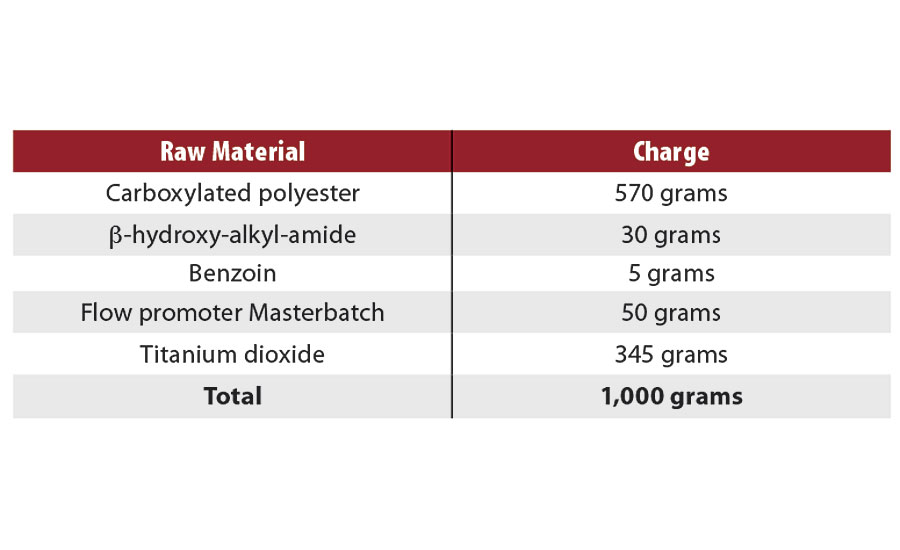
The reference grade used in this part of the study was a superdurable polyester from Allnex, today widely used in many ACE applications.
The new generation of polyester resins developed and presented in this article are targeting to:
1. Reduce the permeation of humidity and oxygen, with formation of ions at the coatings-substrate interface, through:
- Improvement of barrier performances;
- Increase of adhesion of the coating to the substrate: providing good wetting of substrate by coating system and reinforcing the wet adhesion of the polymer;
- Increase of coating stability to its environment, to hydrolysis and UV radiation, thermal stability.
2. Inhibit the corrosion through:
- Increase of inhibition/passivation performances, mainly with the help of additives.
Different polymeric structures were tested initially on their salt spray resistance and subsequently for all the other typical application performances. This work finally led to the development of a new ACE polyester for ß-hydroxy-alkyl-amide.
Table 3 and Figure 1 report the experimental results in terms of salt spray resistance after 500 hrs for the reference product and the new development grade.
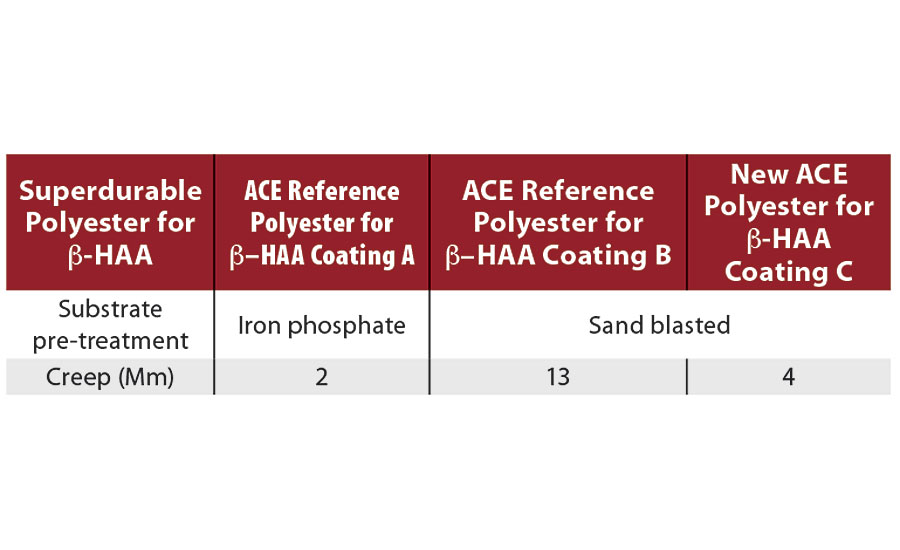
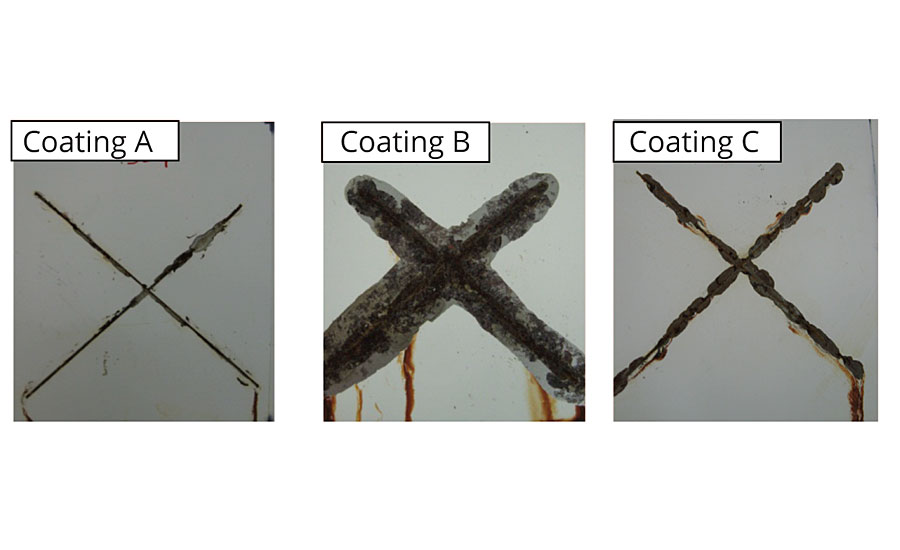
The improved creep performance of the new ACE polyester in comparison to the reference is evident when applied on the same non-pretreated substrate, while it is still slightly worse compared to when the coating based on the reference is applied on iron phosphate pre-treated panels. Similar promising results have been found with tests in a humidity chamber.
When looking at the other typical properties (Table 4), and again in comparison to the reference, the viscosity of the new ACE polyester is reduced, while, when comparing the powder coatings, gel-time and flow are much longer. The lower reactivity doesn’t impact the chemical resistance, which is demonstrated from the comparable solvent resistance (acetone test) result.
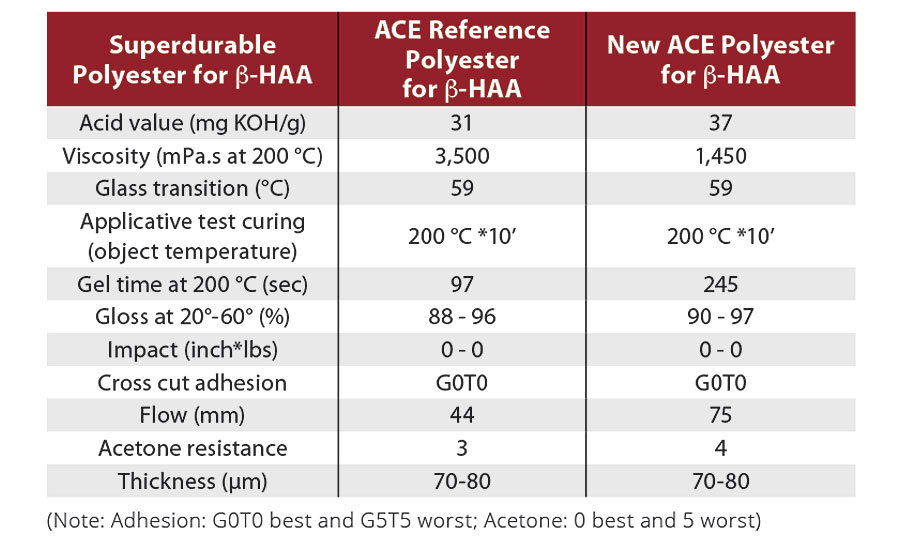
A similar level of improvement has been confirmed on the more demanding brown powder coating applied on solely shot-blasted panels, as reported in Table 5 and Figure 2.
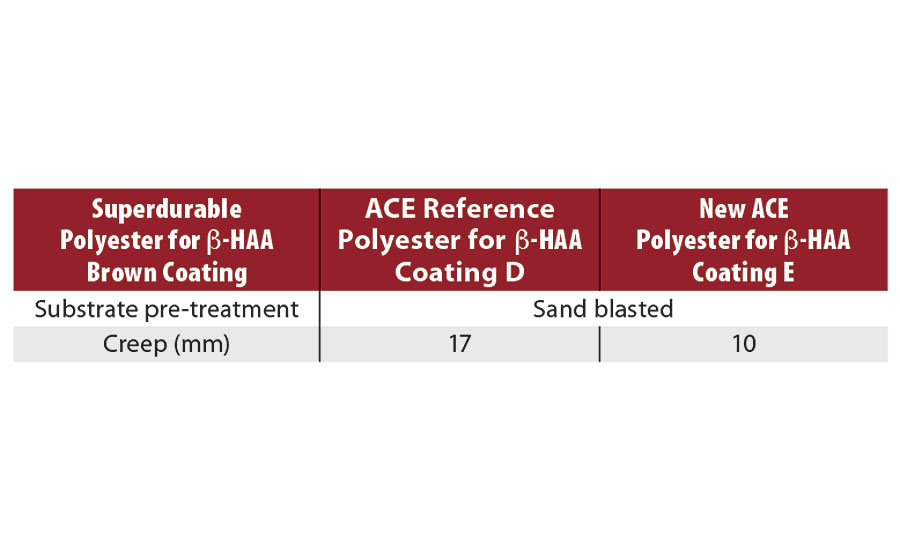
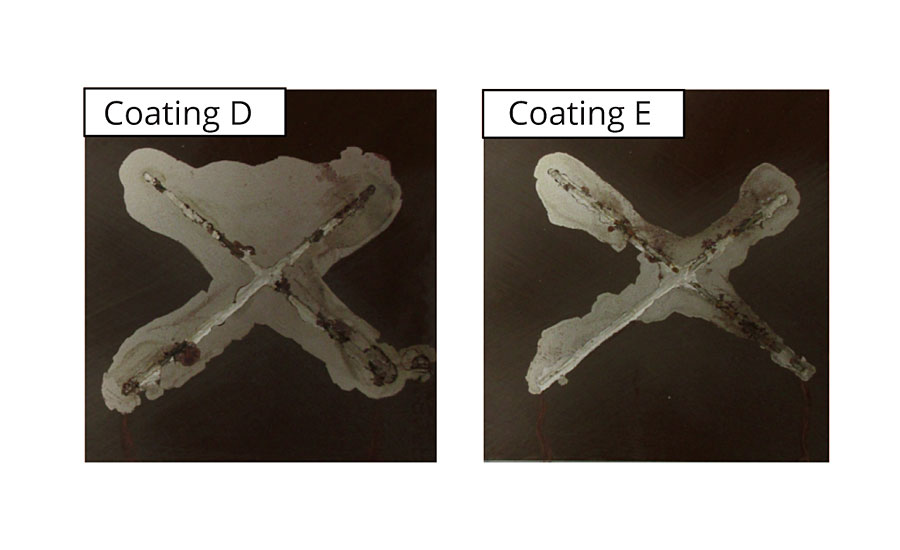
Preliminary outdoor durability results of the new ACE polyester are in line with the expectation and similar to the reference, as reported in Figure 3.
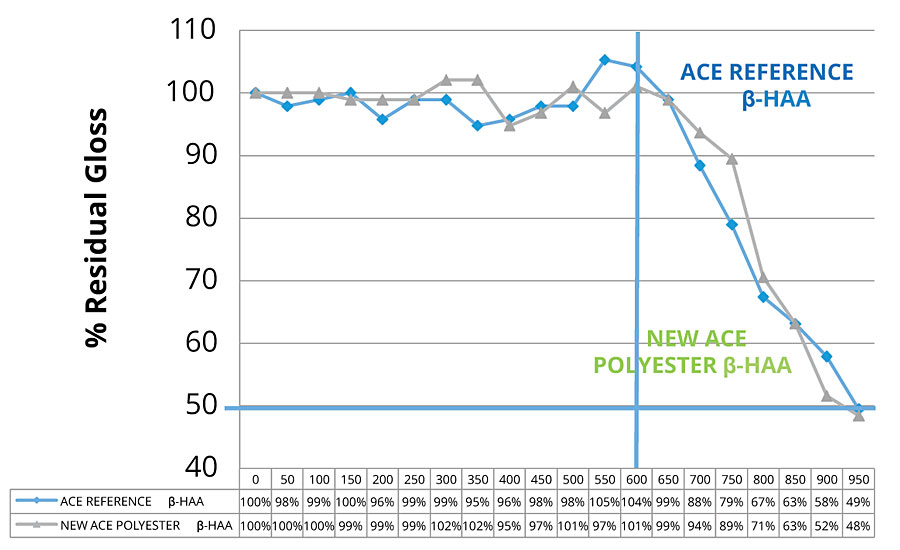
Superdurable Powder Coatings Based on Triglycidyl-Isocyanurate for ACE Applications
These results, and interest in the different markets like Asia and America where ß-hydroxy-alkyl-amide is not the reference hardener, have encouraged us to extend the investigation to the combination with TGIC.
The powder coating formulation studied is shown in Table 6, with 70% of binder content based on a polyester resin and triglycidyl-isocyanurate.
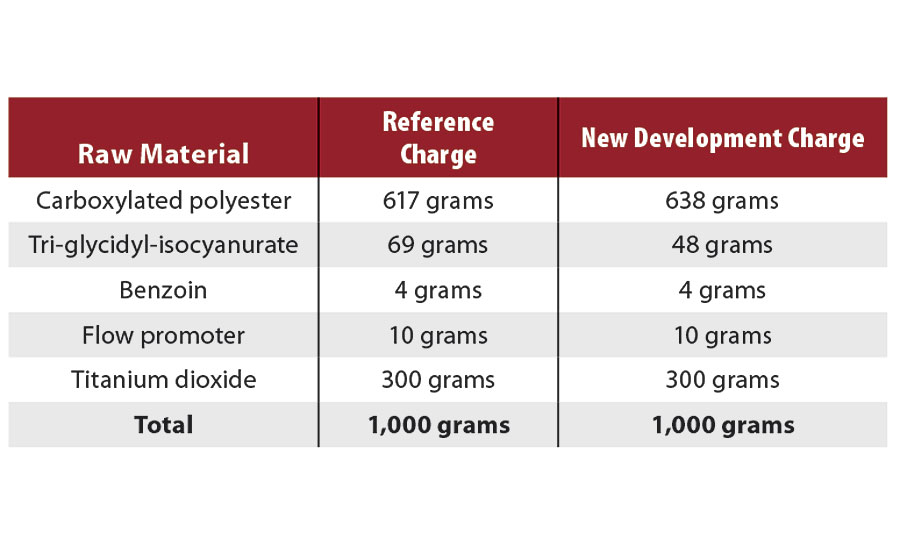
The reference grade is a well-introduced polyester resin for ACE applications in the American market. In similarity with the research work for ß-hydroxy-alkyl-amide applications, several modifications of the resins’ polymeric structures have been developed and tested in terms of corrosion resistance and other typical properties, this leading to the development of two new ACE polyesters for TGIC.
Table 7 and Figure 4 report the experimental results in terms of salt spray resistance after 500 hrs. The Allnex polyesters v1 and v2 clearly showed that the new ACE polyesters represent a significant improvement in comparison to the reference in salt spray resistance. The new ACE polyesters for TGIC also demonstrated appropriate application performances (Table 8).
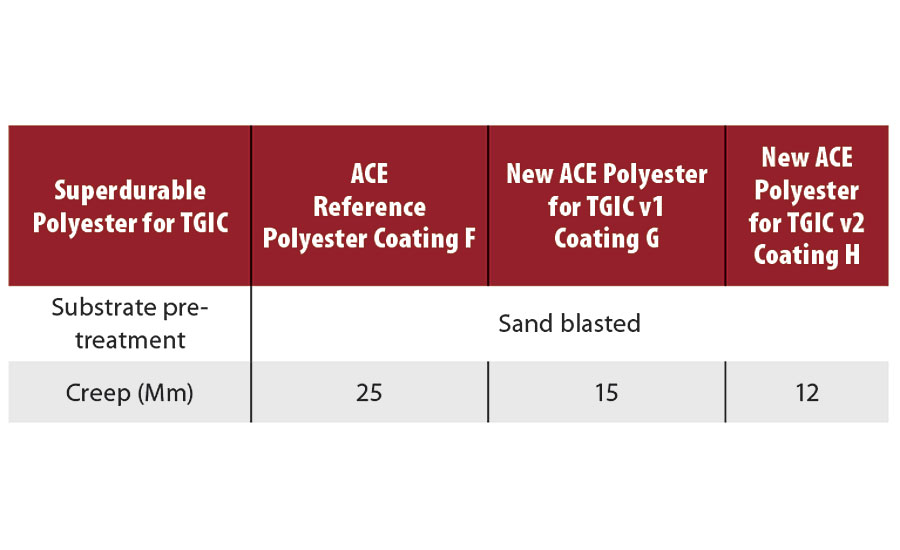
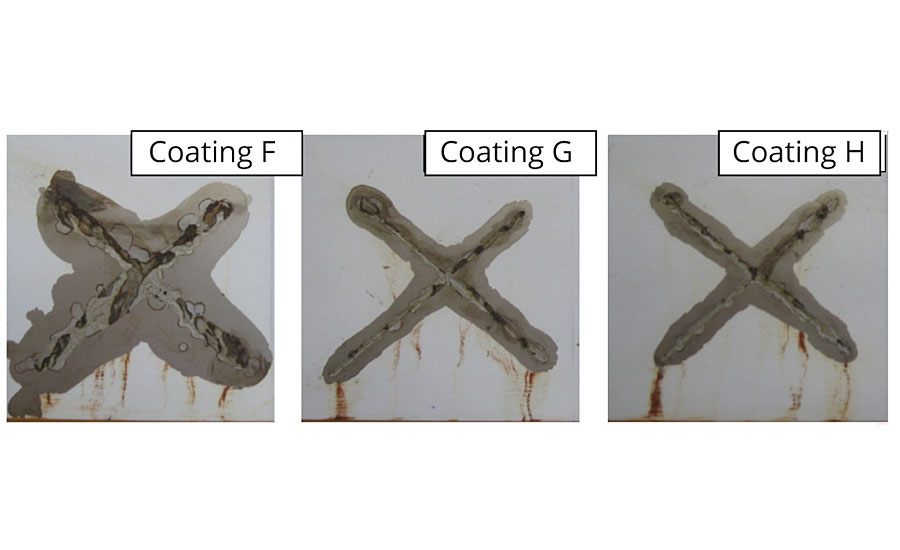

Here too, in spite of the longer gel-time, when combined with TGIC, new ACE polyester for TGIC v1 and v2 provide very similar performances vs the ACE reference polyester, including accelerated outdoor durability, as reported in Figure 5. New ACE polyester v1 is preferred vs v2 due to the better solvent resistance linked to the higher viscosity of the resin.
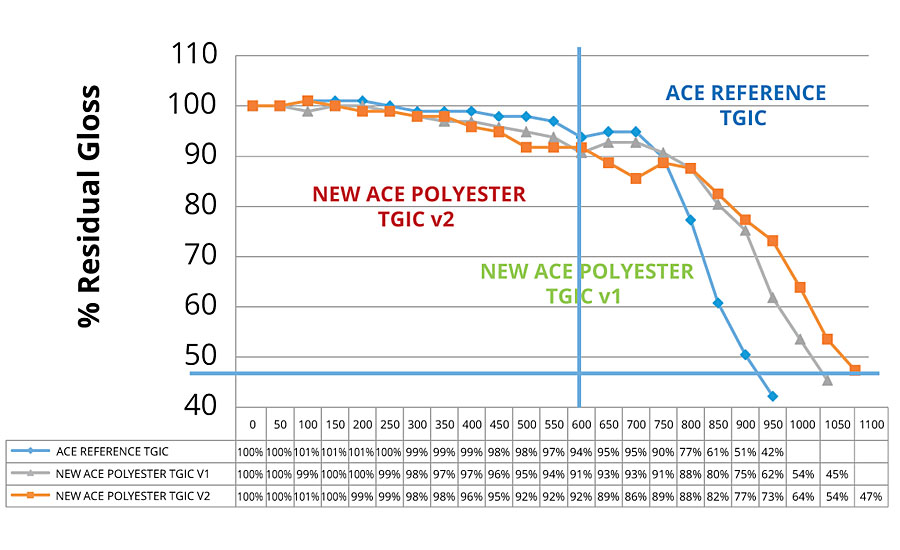
Superdurable Powder Coatings Based on Blend of Diglycidyl-Terephthalate and Triglycidyl-Trimellitate for ACE Applications
A second area of interest in Europe is powder coating systems based on superdurable polyester in combination with PT 910.
The powder coating formulation used in all the tests was based on a 93 to 7 ratio between polyester and PT 910, with a 71% binder content in presence of titanium dioxide as the only pigment (Table 9). The reference is an Allnex superdurable carboxylated polyester used in combination with the same hardener.
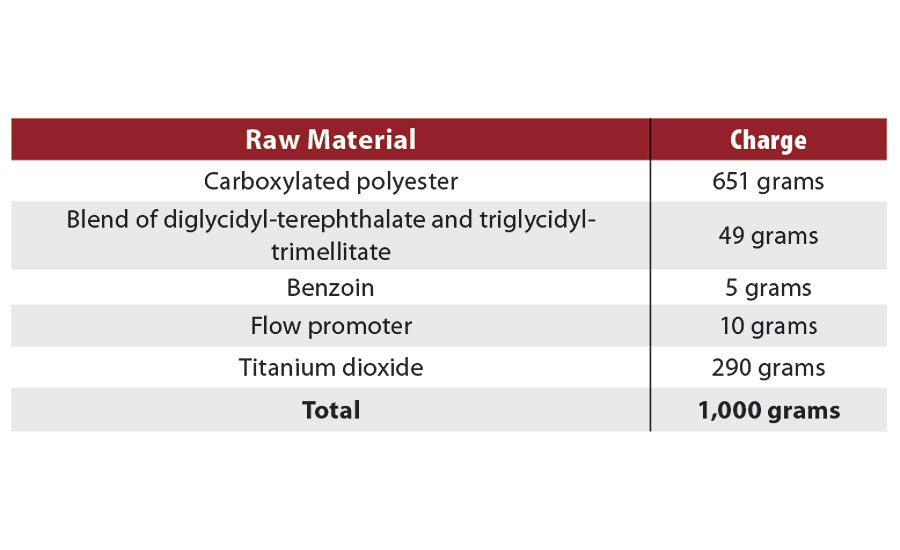
The research for this application targeted lower curing (160 °C), which was difficult to achieve on solely shot-blasted steel. For this reason, zinc-phosphate pre-treated panels were used.
The research has led today to a new polyester for PT 910 based on different modifications in the additives, which offers results much better in comparison to the reference.
Table 10 and Figure 6 report the experimental results in term of salt spray resistance after 1,500 hrs for the Allnex polyester reference product and the new development. The new ACE polyester for PT 910, in spite of the shorter gel-time, demonstrates good flow and typical application performance in general (Table 11).
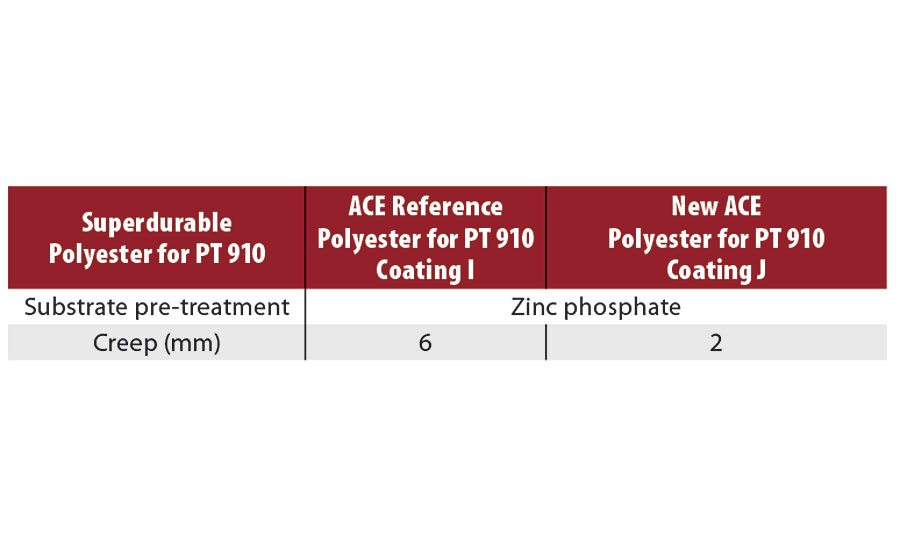
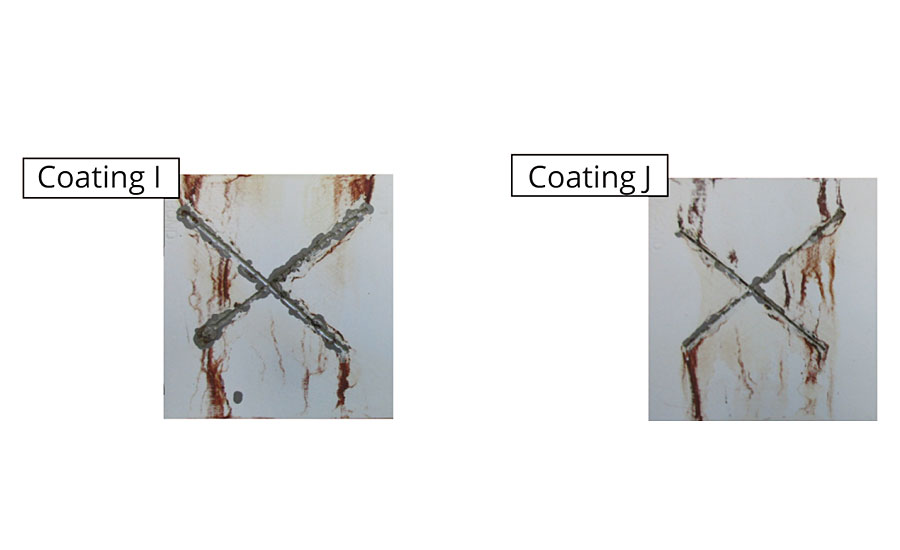
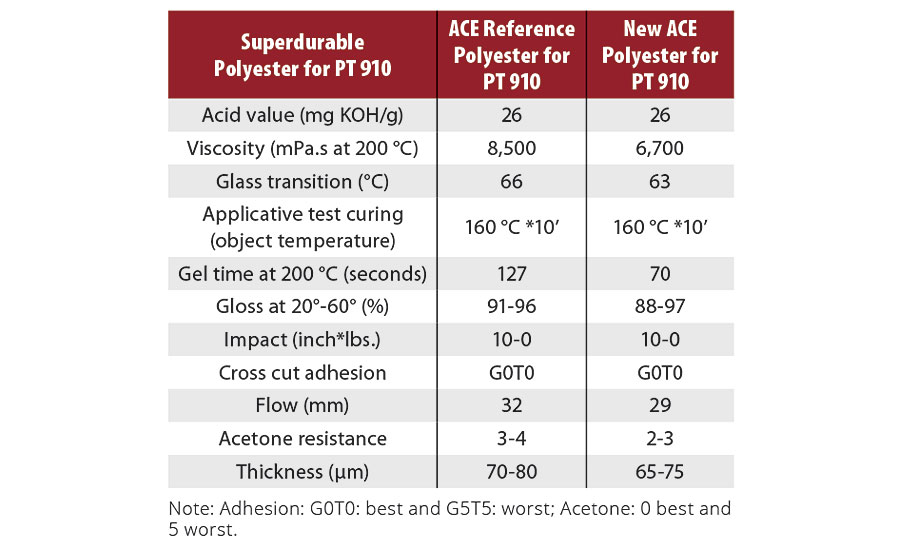
Application on Iron and Zinc Phosphate Pre-Treated Substrate Based on ß-Hydroxy-Alkylamide and Triglycidyl-Isocyanurate
In the case of powder coatings based on ß-HAA and TGIC, which started from solely sand-blasted steel panels, the investigation was extended to pre-treated substrates, and for this reason, like for PT 910 salt spray resistance, test times were increased to 1,000-1,250 hrs in the case of iron-phosphate, and 1,500-2,000 hrs in the case of zinc-phosphate pre-treatment respectively.
The observed results shown in Tables 12-15 confirm the improvement for both combinations with ß-HAA and TGIC, compared to their respective references.
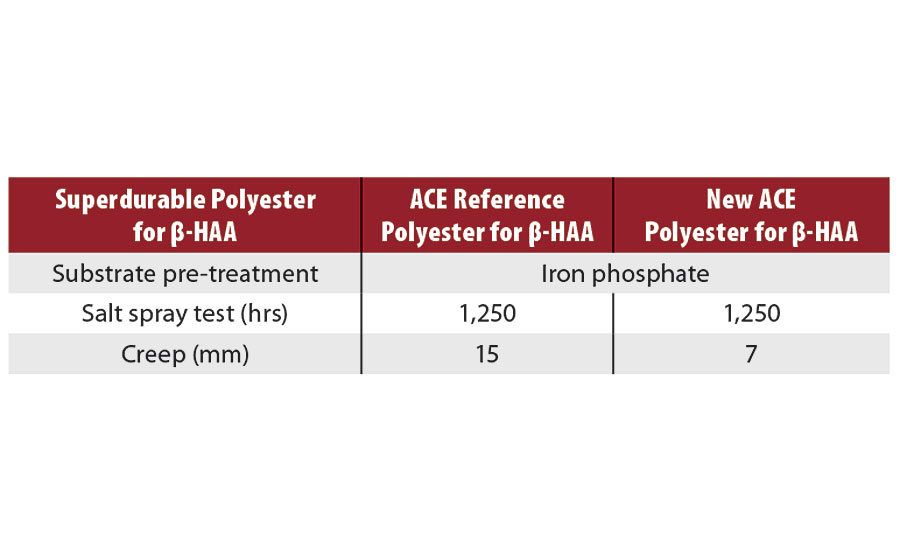
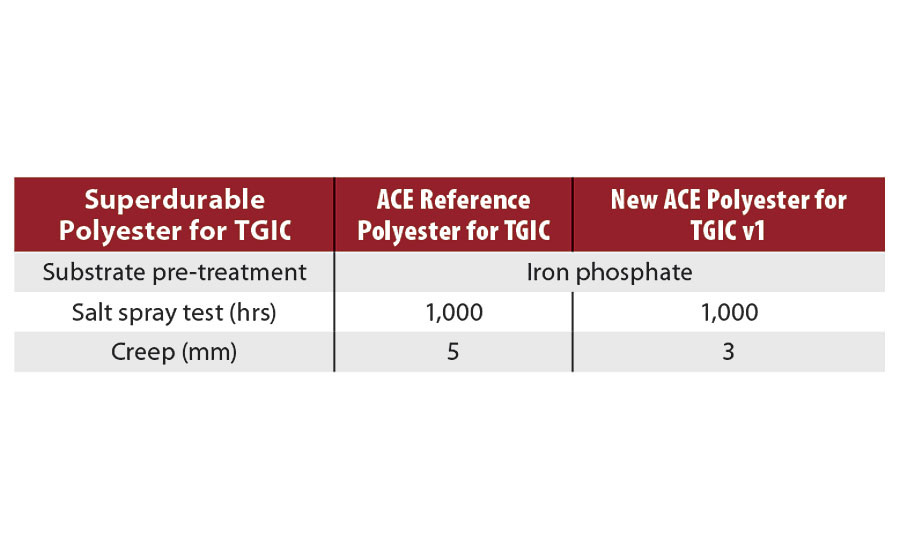

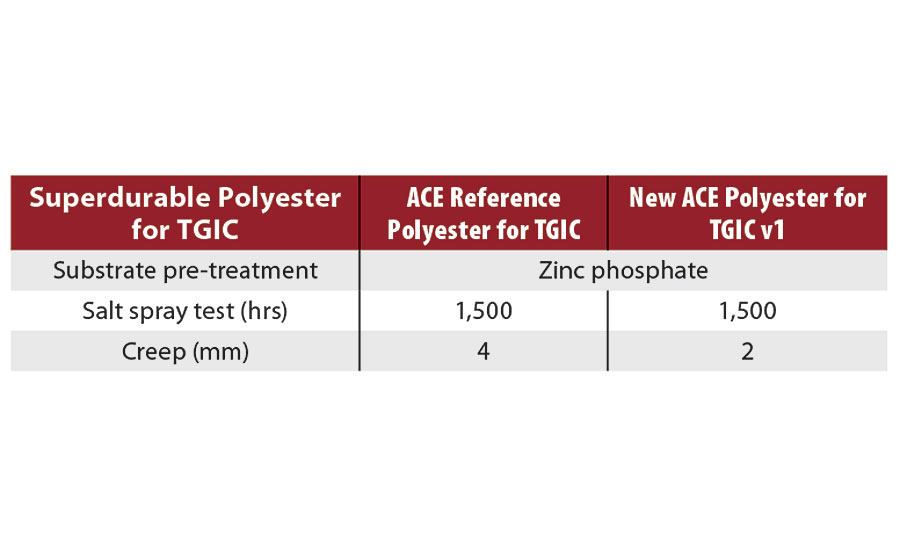
The same coatings have been tested for acetic salt spray resistance on non-chromate aluminum substrates, and in this case the results are good, with no corrosion initially observed for all the involved coatings, but without being able, until today, to better discriminate these results.
Powder coatings based on ß-hydroxy-alkylamide were analyzed with electrochemical impedance spectroscopy on both scribed and non-scribed panels. The results have not been conclusive. Powder coatings demonstrate to maintain a very high impedance level of ca. 1010 ohm/cm2 even after 2,800 hrs of testing.
Further Findings
In conclusion, another interesting finding is related to the effect of the curing temperature, as reported in Table 16. The higher the curing temperature, the better the salt spray resistance. This is in line with the results of other studies that state that the crosslinking density appears to affect ionic conductivity of the film and reduces the permeability of water and ions through the coating film, leading to a structure more resistant to corrosion.5,6
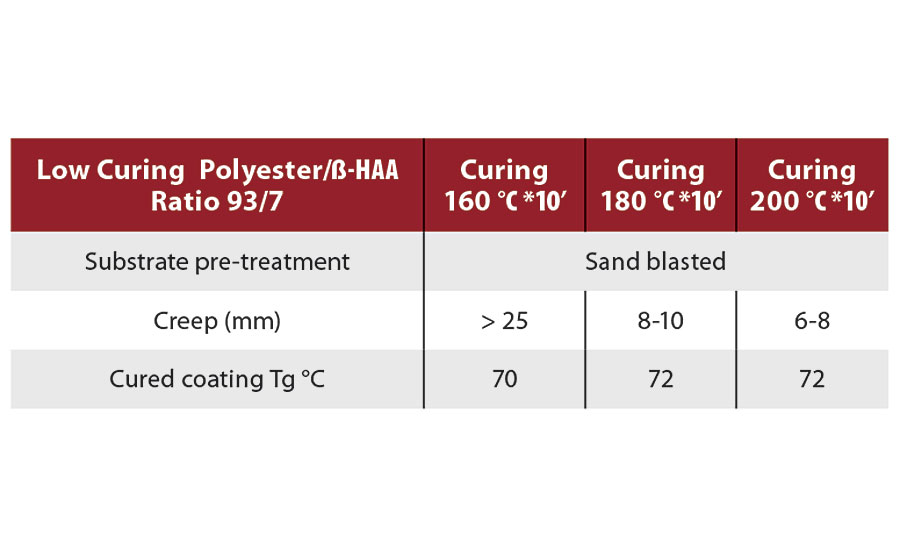
What is new from the study results is that this is valid even on powder coatings expected to be already fully cured, like a low-bake binder based on polyester and ß-hydroxy-alkyl-amide and cured already at 160 °C for 10’ object temperature.
Conclusion
Salt spray corrosion resistance provided from powder coatings for ACE applications can be improved by new superdurable polyesters for ß-hydroxy-alkyl-amide, triglycidyl-isocyanurate and the blend of diglycidylterephthalate with triglycidyltrimellitate developed by Allnex.
The improvements are evidenced both on standard pre-treated and un-treated substrates, and with white and colored coatings.
These new developments are targeting better adhesion and barrier properties, which are considered the best manner by which polyester can reduce the corrosion speed.
The ultimate target is still the removal of pre-treatments at all. More studies and tests including acetic salt spray and cyclic corrosion are planned in that respect.
References
1 AkzoNobel & UoM’s Corrosion & Protection Center Partner to Develop Corrosion Protection Solutions SpecialChem - Feb 20, 2012;
2 Challener, C. Corrosion Protection with Coatings: Facing the Challenge, CoatingsTech, Feb. 2012, 42-46.
3 Salam, A.; Makhlouf, H. Casting out Chromium, European Coating Journal, March 2012 (16-20).
4 Corrosion Inhibitors for Waterborne Alkyds Technology: Halox® October 2007.
5 Mafi, R.; Mirabedini, S.M.; Naderi, R.; Attar, MM. Effect of Curing Characterization on the Corrosion Performance of Polyester and Polyester/Epoxy Powder Coatings, Corrosion Science 50 (2008) 3280-3286.
6 Radhakrishnan, S.; Sonawane, N.; Siju, C.R. Epoxy Powder Coatings Containing Polyaniline for Enhanced Corrosion Protection, Progress in Organic Coatings 64 (2009) 383-386.
7 Paul, S. Surface Coatings, John Wiley and Sons 1985;
8 Supper, E.; Krassnitzer, M.; Feola, R. (LCR): New Waterborne Resins for Corrosion Protection 2002.
9 Gordon Bradley, specialchem4coatings.com: How to Prevent Corrosion in Industrial Coatings Market.
10 Van Liempt, H. Keeping a Clean Profile, European Coating Journal, March 2012, 22-25.
11 Fedrizzi, L.; Stenico, M.; Deflorian, F.; Maschio, S.; Bonora, P.L. Effect of Powder Painting Procedures on the Filiform Corrosion of Aluminum Profiles Progress in Organic Coatings 59 (2007) 230-238.
Disclaimer: Allnex Group companies (“Allnex”) decline any liability with respect to the use made by anyone of the information contained herein. The information contained herein represents Allnex’s best knowledge thereon without constituting any express or implied guarantee or warranty of any kind (including, but not limited to, regarding the accuracy, the completeness or relevance of the data set out herein). Nothing contained herein shall be construed as conferring any license or right under any patent or other intellectual property rights of Allnex or of any third party. The information relating to the products is given for information purposes only. No guarantee or warranty is provided that the product and/or information is adapted for any specific use, performance or result and that product and/or information do not infringe any Allnex and/or third party intellectual property rights. The user should perform its own tests to determine the suitability for a particular purpose. The final choice of use of a product and/or information as well as the investigation of any possible violation of intellectual property rights of Allnex and/or third parties remains the sole responsibility of the user. ©2016 Allnex Belgium SA. All Rights Reserved.
Looking for a reprint of this article?
From high-res PDFs to custom plaques, order your copy today!