Polylactic Acid Polyols in Urethane Coatings

Polylactic acid (PLA) is a well-known bio-based thermoplastic. This versatile, renewable polymer is a premier example of the commercial success of a bio-based, sustainable material with an established and growing technology base.1 The polymer backbone of PLA is based on renewable carbon produced via the bacterial or yeast fermentation of sugars, derived from annually renewable agricultural sources. The fermentation process produces lactic acid, which is chemically converted to lactide and then polylactic acid via ring opening polymerization. It is used in a variety of applications such as compostable food service-ware and packaging, 3D printing filaments, hygiene products, compostable coffee capsules and tea bags, and nonwovens.2 PLA brings value to these applications beyond a sustainable, low-carbon footprint through performance attributes such as a high modulus, excellent solvent and grease resistance, food contact compliance, and where it can be industrially composted back to CO2 and water. Beyond compostability, PLA can also be both chemically and mechanically recycled into virgin polymer for new applications. These multiple after-use options combined with being made from renewable resources make PLA a leading biomaterial for bringing the concept of the circular economy into practice.
There is a breadth of physical properties that can be achieved by PLA and its compounds that are driven primarily by the control of the PLA molecular weight, degree of crystallinity, melting point and formulation additives. As a testament of the commercial success of PLA, in 2017, NatureWorks’ Blair manufacturing site reached a production milestone of making more than one-million cumulative metric tonnes of Ingeo™ PLA.
The fermentation process produces L-lactic acid (L-HLA), which is dehydrated into the cyclic lactic acid dimer known as lactide, 1, in Figure 1. During this dehydration process a small fraction of the L-lactic acid racemizes to D-lactic acid units and thus when cyclized, forms mixtures of L-, D- and meso-lactide, which is further rectified to produce polymerization grades of lactide for commercial use and for polymerization to PLA, 2. As shown in Figure 1, high-molecular-weight PLA is typically produced by the ring-opening polymerization (ROP) of lactide, which can be a selected mixture of D-, L- and meso-lactides. Poly(L-lactide) (PLLA) and poly(D-lactide) (PDLA) are highly crystalline thermoplastics with a melting point of about 175 °C. The substitution of about 20% of the L-lactic acid units in PLLA with D-lactic acid units reduces the crystallinity and makes it fully amorphous. In part, it is this ability to tailor the degree crystallinity of polylactides via control of the D-to-L ratio in the polymer microstructure that enables it to have a wide variety of physical properties and therefore bring performance benefits and value to different applications. Note that by convention, PLLA contains <2% D-lactic acid units (D-HLA), PDLA contains <2% L-HLA units and PDLLA or PLA is used to describe the ranges where >2% of the D or L HLA units are incorporated in the PLA composition. The control of the ratio of L-lactic acid to D-Lactic acid units of the PLA microstructure is analogous to how isotactic, syndiotactic and atactic polypropylene have different properties based on the polymer tacticity. Some typical physical properties of Ingeo PLA are shown in Table 1.3
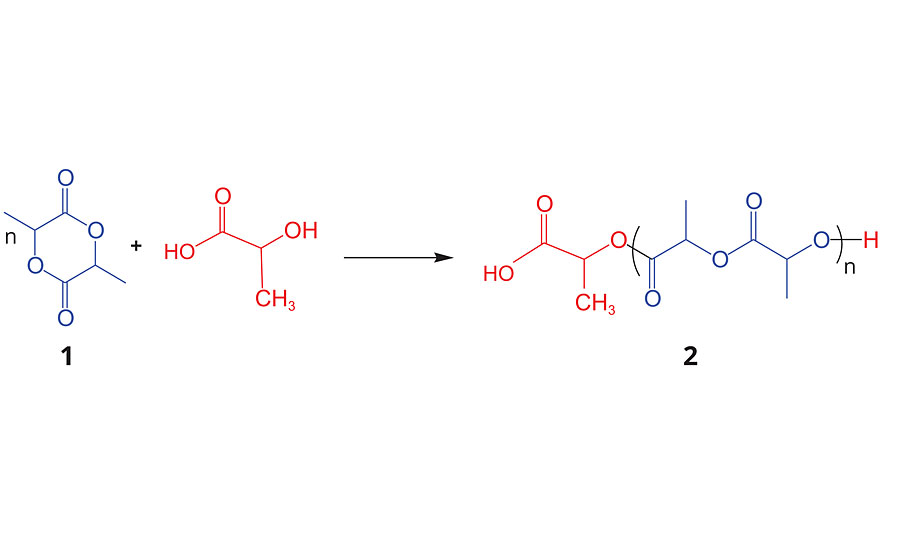
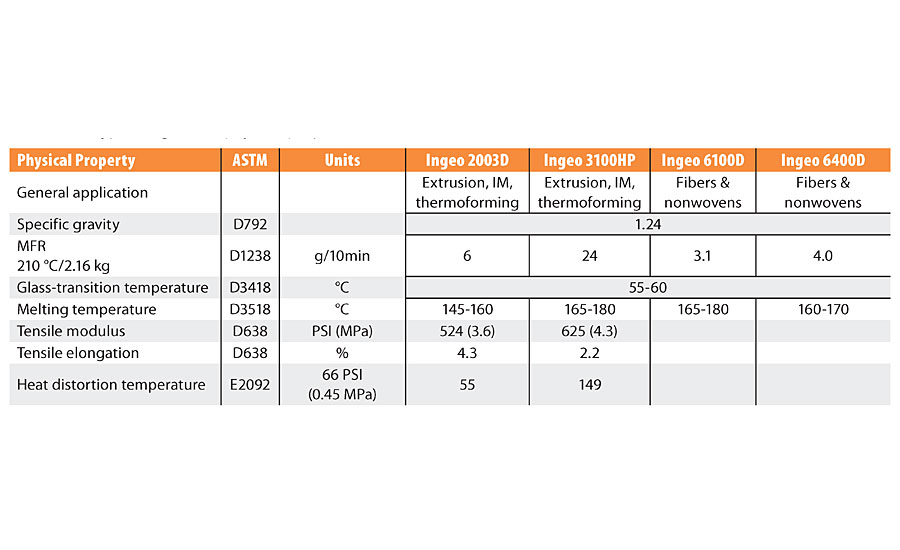
Given the commercial successes of thermoplastic PLA in the marketplace, NatureWorks has recently initiated the technology and application development of PLA for non-traditional markets such as coatings, adhesives and specialty derivatives. Leveraging the ROP chemistry shown in Figure 1, where the molecular weight and tacticity are controlled, it is possible to add the dimensions of initiator type and end groups to the available tool box to control the PLA microstructure and therefore the physical properties of the polymer. In this article, we will discuss recent advances in the technology and application development of functional PLA derivatives for reactive chemistries and, in particular, PLA polyols for urethane coatings.
Experimental
The PLA polyols were prepared by the ring-opening poly-merization of NatureWorks’ Vercet™ M700, meso-lactide using the initiators propylene glycol (PG), 1,6-hexanediol (1,6-HDO), 1,12-dodecanediol (1,12-DDO), or pentaerythritol (Penta) to produce the PLA polyols used in this study.
The molecular weights and hydroxyl values were controlled by manipulation of the molar ratio between the lactide and the initiator using a proprietary method to achieve a molecular weight target and to minimize the amount of residual lactide in the polyols. The PLA polyol hydroxyl values (OH value, reported in units of mg-KOH/g polyol) were measured using ASTM E1899-8 in dry acetonitrile. p-toluene sulfonyl isocyanate (PTSI) was used as the derivatizing reagent of the hydroxyl groups, and the excess PTSI is back titrated by tetrabutyl ammonium hydroxide.4 Polyol hydroxyl values (OH value) of 12, 25, 56 and 112 mg-KOH/g were targeted and, typically, the OH values were within 5 units of the target value. Full characterization data for the polyols are shown in Table 2.
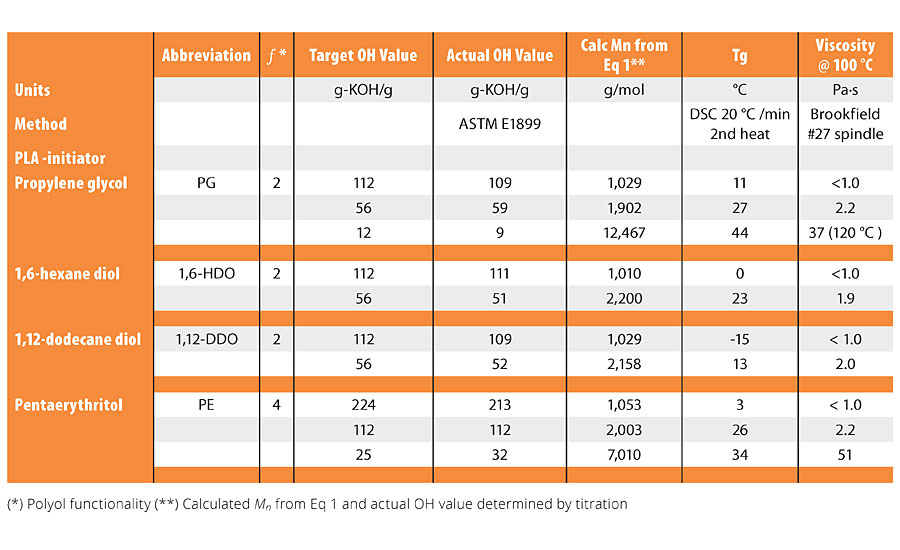
The PLA coating solutions were prepared in 2-butanone (MEK) and comprised a mixture of the polyol, isocyanate (NCO) and tin-based catalyst diluted to 40% solids. The multi-functional isocyanate used in these studies was a commercially available, oligomerized hexamethylene diisocyanate trimer (HMDI trimer) with a reported isocyanate value (NCO value) of 15.5% by weight of NCO groups or 271 g per NCO eq. The HMDI trimer was used as received, and any unused portion of the sample was blanketed with dry nitrogen before the bottle was re-sealed to maintain the desired level of active NCO groups. The coating formulations targeted an isocyanate to hydroxy equivalent ratio (NCO/OH) of 1.02 and used 50 part per million (ppm) of tin added as dibutyltin dilaurate (DBTDL). The coatings were prepared on isopropanol washed metal Q panels using a typical laboratory drawdown method. A Baker bar was used to form a coating with dry coating thickness of 50-60 µm. The solvent was allowed to evaporate from the coatings for 1 hr, and the coatings were thermally cured for 2 hrs at 100 °C. The coated test panels were conditioned for at least 24 hrs at room temperature (≈ 23 °C ) before mechanical tests were performed. ASTM test methods were employed to characterize the coatings for adhesion, MEK resistance, hardness and drop impact resistance. The methods used to characterize the coatings are listed in Table 3.
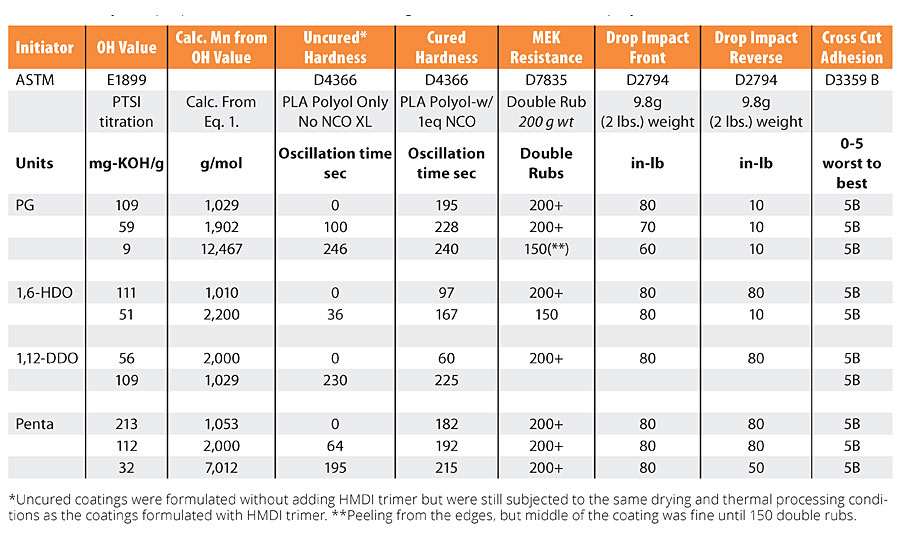
Results and Discussion
Synthesis of PLA Polyols
The polymerization of lactide can be achieved through the reaction of the lactide with an initiator molecule such as amines (–NH) and hydroxyl (–OH) groups. This ROP reaction yields PLA derivatives with a well-controlled degree of polymerization, microstructure and functionality.5-6 As shown in Figure 2, and has been reported previously, it is possible to make multi-functional PLA polyols by using commonly available hydroxy initiators. Figure 2 highlights the initiators described in this study, but other hydroxy compounds can be used.
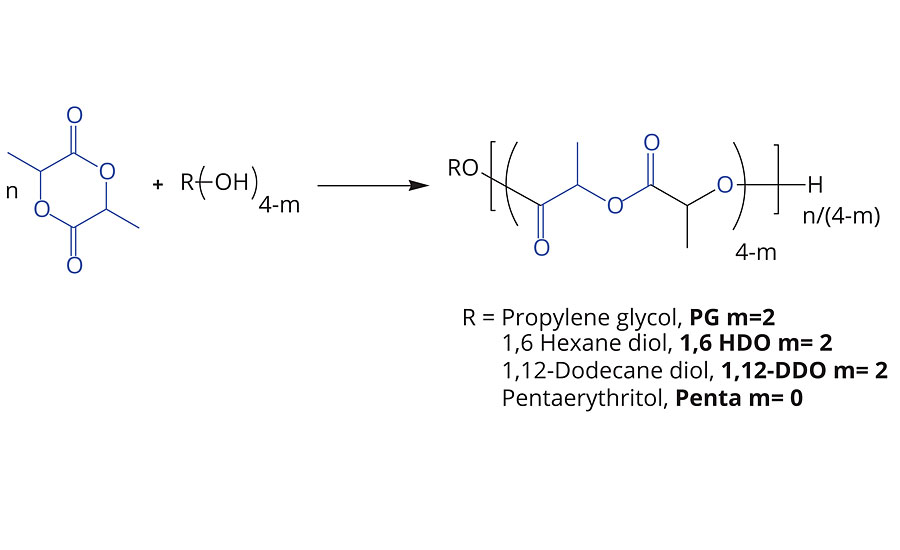
By controlling the molecular weight of the PLA oligomer to <10 kg/mol or a hydroxyl value of >12 mg-KOH/g for a difunctional polyol, the initiator becomes a significant contributor to the physical properties of the polyols such as viscosity, glass-transition temperature and solubility; while leaving the terminal secondary hydroxyl groups available for further reactions with functional groups such as isocyanates, anhydrides, caprolactone, glycolide or other comonomers.
PLA Urethanes
The PLA urethane network was formed from the reaction of the secondary hydroxyl groups of the PLA polyol and the isocyanate groups of the HMDI trimer. The reaction scheme is shown in Figure 3. The PLA polyols are crosslinked by the isocyanate and, as is known in urethane chemistry, the physical properties of the network and become a function of the type of polyol, or polyol blend, the isocyanate and the crosslink density.
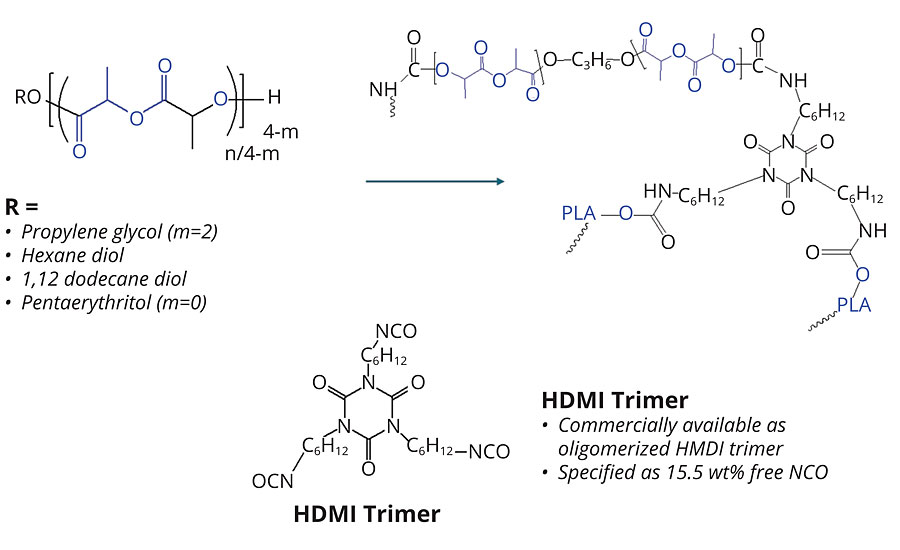
Infrared spectroscopy was used to determine rate and extent of reaction of the PLA polyols with the HMDI trimer. Using the normalized peak height for the signal from NCO groups of the HMDI trimer, between 2250 cm-1 and 2280 cm-1, to that of the PLA signal at 1450cm-1, it was possible to follow the rate and extent of the reaction at different temperatures. Figure 4 compares the change of the normalized peak heights for the NCO/PLA ratio as a function of time, temperature and catalyst concentration. As can be seen in Figure 4, there is a significant difference between the reaction rates at 100 °C and 80 °C, and with 10 and 50 ppm of tin catalyst. As expected, the IR data indicate the uncatalyzed reaction is extremely slow at 100 °C and remains incomplete even after 24 hrs.
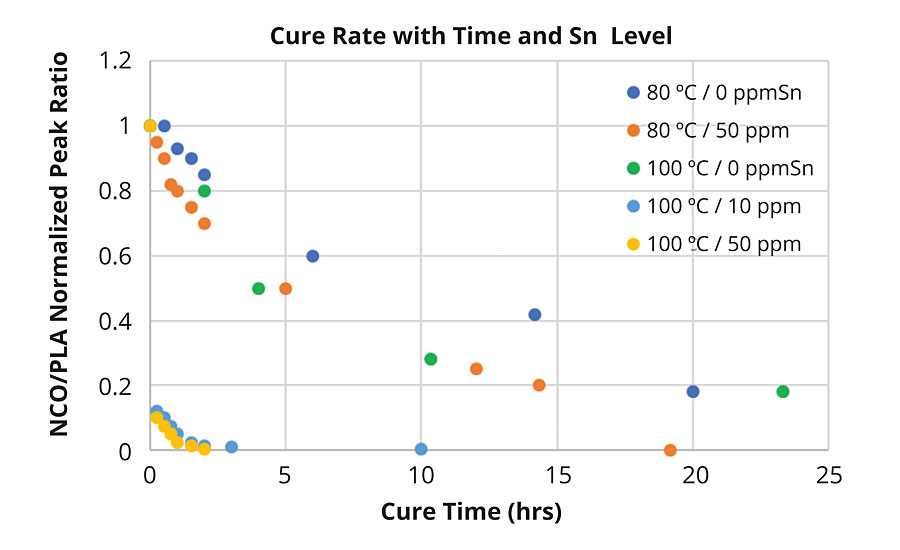
However, the addition of only 10 ppm of tin increased the reaction rate from essentially <20% to >99.5% complete after 2.5 hrs. The addition of 50 ppm tin-based catalyst did slightly increase this reaction rate, although it may be within the experimental error of the measurement. Knowing the reaction was completed within this period, a series of coated test panels were prepared and cured at 100 ºC using 50 ppm tin catalysts. The mechanical properties of the coatings were then characterized as a function of OH value, initiator and functionality.
Polyol Characterization
For the sake of consistency, in this article the polyol molecular weight will be referenced by the more commonly used industrial term of hydroxyl value (OH value) of the polyol, which is related to the number-average-molecular weight by Equation 1.
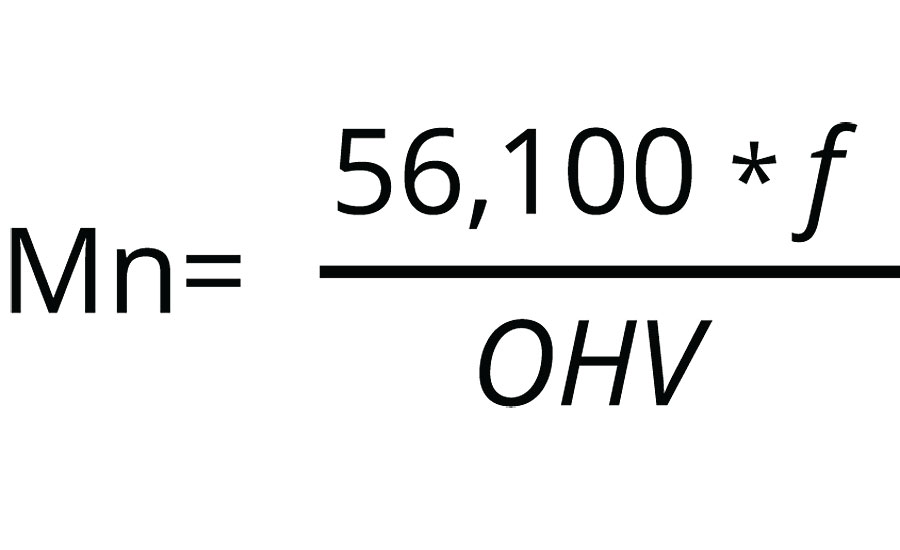
Where 56,100 is the molecular weight of KOH in mg/mol, ƒ is the number of hydroxy groups per polyol molecule, and OHV is the hydroxy value in the units of mg-KOH/g-polyol. Also, the terms cured and crosslinked refer to the coating after it has reacted with the isocyanate at a given reaction temperature, as described in the experimental section.
The physical properties of the PLA polyols are shown in Table 2. As noted, by the change in the glass transition temperature (Tg) versus the number of carbons in the initiator, there is a steady and systematic decrease in the Tg of the polyols as the hydroxyl value (OH value) increases from 12 to 112 mg-KOH/g, noting that OH value is inversely proportional to molecular weight.
Figure 5 graphically shows the relationship between Tg, molecular weight and the polyol initiator. Note that at a OH value of 12 or lower, corresponding to Mn ~ 9,000 g/mol or greater for a difunctional polyol, the Tg of the PLA polyols coalesces around that of a fully amorphous high-molecular-weight PLA at about 47-50 °C. This trend is consistent for the difunctional PLA polyols made with PG, 1,6-HDO and 1-12 HDO. However, at a given OH value, the polyol initiated with 1,12-DDO has a lower Tg than a polyol with a shorter initiator fragment such as 1,6-HDO and PG owing to the higher flexibility of the longer C12 segment compared to the shorter initiator segments. This trend, however, does not hold for polyols made with a branched initiator such as pentaerythritol, ƒ= 4. The decrease in the glass transition temperature with decreasing molecular weight is not as dramatic for the Penta PLA polyol. The higher Tg for the Penta polyol suggests there is an influence of the branched PLA polyols on the steric interactions of the polyol chains, decreasing chain mobility and thus increasing the Tg compared to a linear, difunctional PLA polyols with a similar OH value. Like the glass transition temperature, the viscosity of the polyols also decreases as the chain length of the initiator increases. As noted later in this article, these changes in polyol properties as a function of the initiator play an important role in the mechanical properties of the coatings and demonstrates the tailorable nature of the PLA polyols in the urethane network.7
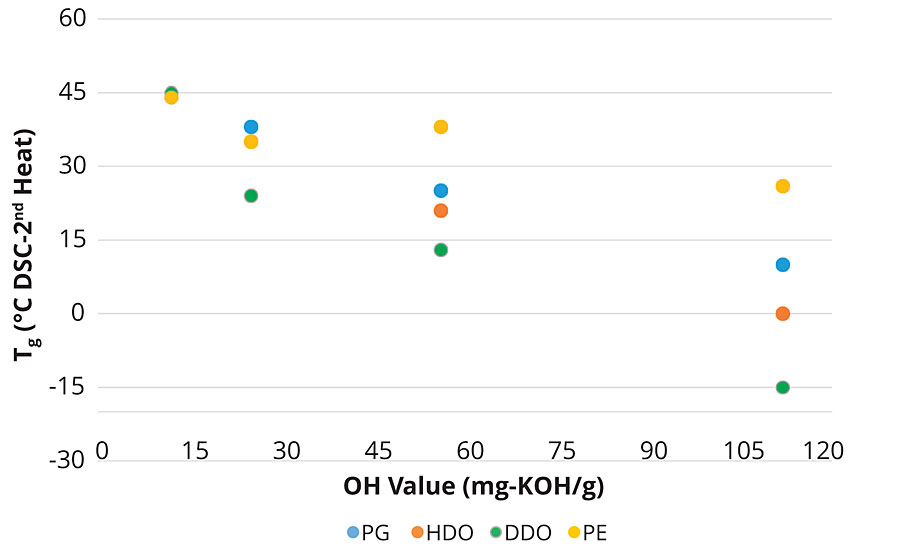
Coating Characterization
The cured coatings were characterized for adhesion, hardness, MEK double rub solvent resistance and drop impact testing. The testing was done in a manner consistent with common ASTM or ISO test methods. This investigation was focused mostly on the influence of the PLA polyol structure on the coating properties such as the influence of the initiator, degree of branching and molecular weight of the polyol. This study did not investigate additional variables such as the nature of the isocyanate, the isocyanate index, and functionality or the use of PLA copolymers or polyols blends. Future studies will investigate some of these variables in more detail. The coating properties are summarized in Table 3 and are discussed further in this article.
Adhesion
Adhesion of the coating to the test panels was tested by cross cut adhesion according to ASTM D3359 Method B. It was observed that cured PLA-urethane coatings had excellent adhesion to the Q panels. There were no detectable differences in the adhesion of these cured coatings by this test. All values for the cured coatings, regardless of nature of the PLA polyols used were 5B, that is, no part of the cross-cut area was damaged by the tape pull. However, when the coating was not cured, or under cured, the cross-cut adhesion values were 1B or less. With these results, the tape pull test became the laboratory default test to quickly determine if a crosslinking reaction had occurred, but the test did not provide more detailed resolution on the influence of the PLA structure on adhesion. Nonetheless, the adhesion value of 5B for the cured PLA urethane coatings confirms the PLA coatings had excellent adhesion to the metal panels.
Coating Solvent Resistance
The MEK solvent resistance was determined using ASTM D7835 (Solvent Resistance using a Mechanical Rubbing Machine). MEK is an aggressive test solvent used to evaluate the cure, adhesion and chemical resistance of a coating. The solvent test was done using a soft-scrub sponge saturated with MEK and a 1-lb static weight using an automatic wash tester that controls the oscillation rate of the sponge, and amount of solvent dispensed on the coating. The data summarized in Table 3 shows that the PLA urethane coatings had excellent solvent resistance to MEK. There are clearly indications that PLA urethane networks based on the lower polyol OH values did exhibit lower MEK solvent resistance. For example, as noted for the PG polyol series, the coating made with the 9 OH value had poorer MEK solvent resistance than the same coating made with 56 OH value, even though it still exhibited resistance to about 150 MEK double rubs. The relationship between MEK double rub resistance and OH value is partly related to the crosslink density since the lower the OH value, the lower the crosslink density and therefore the lower the MEK resistance. This is a reasonable assumption given that in the limit of no crosslinks, the polymer will dissolve in MEK. The relationship between crosslink density and polymer properties will be discussed later in the article. Nonetheless, given the excellent MEK resistance measured for these PLA urethane coatings they should also have excellent solvent resistance to other milder solvents and cleaners.
Coating Hardness
The cured PLA-urethane coatings were characterized by pendulum hardness according to ASTM D4366. Figure 6 compares the change in hardness of cured and uncured coatings as a function of OH value for the PG-initiated PLA polyols. As shown in Figure 6, there is a steady increase in the hardness of the coatings as the OH value of the polyol decreases from 112 to 12 mg-KOH/g, or as the Mn increases from about 1,000 to 10,000 g/mol. The increase in coating hardness is the result of two factors. First, as the OH value of the polyol decreases, the Tg of the uncured polyol increases, see Table 2, and when the Tg increases from below room temperature to about 45 °C, an increase in the coating hardness should be expected. In addition to the change in Tg, the formation of the crosslinked urethane network plays a significant role in the hardness of the coating. This is exemplified by comparing the change in hardness for the uncured coating based on PG polyol to the cured coating. Referring to Figure 6, when the PG PLA polyol, with a 112 OH value and a Tg of 10 °C, is part of the PLA urethane network, the hardness value increased from essentially 0 to 195 sec. For the same polyol, with a 56 OH value and a Tg = 25 °C, the coating hardness increased from 100 to 228 sec, and when the same polyol with a 12 OH value and a Tg = 44 °C is part of the PLA urethane network, the hardness was essentially within the standard error of the measurement. These data trends show that both crosslink density and the Tg of the polyol influence coating hardness. The influence of the crosslink density will become more apparent when we consider the performance properties of PLA polyols initiated with pentaerythritol.
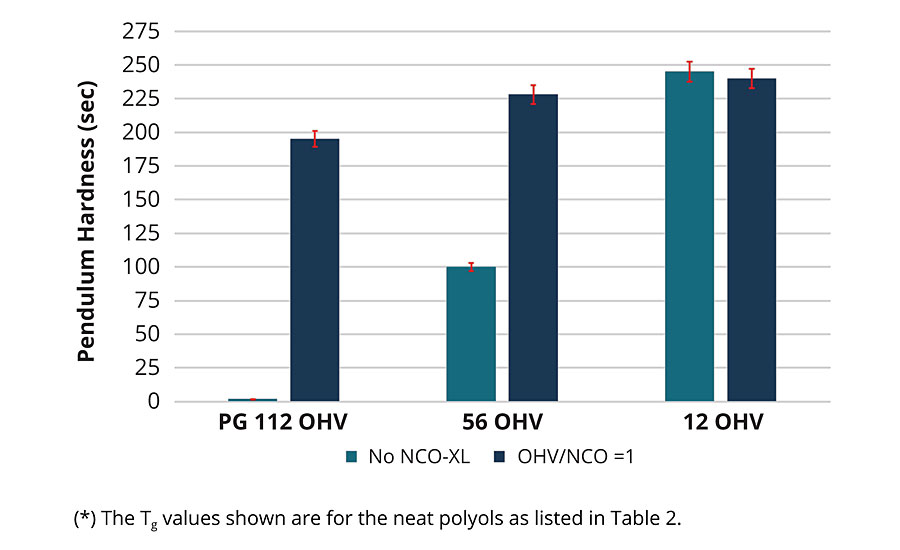
The influence of the initiator segment on the properties of the PLA urethane coating was investigated by studying the properties of cured coatings made with 56 and 112 OH values for PLA polyols made with PG, 1,6-HDO and 1,12-DDO, respectively. Figure 7 shows the expected trend that the PLA polyols with a 112 OH value has a greater change in coating hardness verses the 56 OH value. The longer the initiator segment, the softer the coating after crosslinking. Therefore, the PLA urethane coating made with the most flexible PLA polyol, 1,12-DDO, had the lowest coating hardness at a given OH value, and the 1,6-HDO and PG PLA polyols each increased the overall coating hardness. However, the tetrafunctional PLA polyol based on pentaerythritol did not show as much sensitivity in coating hardness as the difunctional polyols. It is important to note that 56 OH value of a difunctional polyol and 112 OHV of the tetrafunctional PLA have the same degree of polymerization and Mn ~ 2 kg/mol based on Eq 1. The trend in coating hardness again approximates the same trend as noted in the glass transition temperature and exemplifies that influence of the initiator segment on the coating properties of the PLA network.
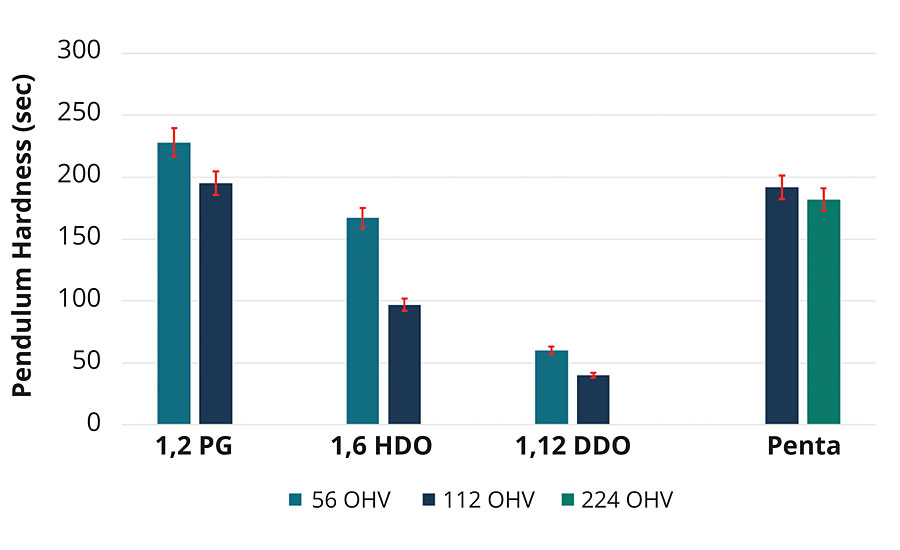
Drop Impact Results
Drop impact testing, ASTM D2794, is an aggressive toughness test that simultaneously evaluates adhesion and stress-strain properties of a coating by dropping a weighted ball on the front and back side of a coated panel. Therefore, the impact force is directly related to the weight and height from which the ball is dropped. By striking the front of the surface, aka frontside or direct impact, the coating undergoes a compressive deformation force at the impact site. Conversely, when the ball strikes the backside of the coated metal panel, the coating undergoes a tensile deformation stress. These different impact events test the coating’s stress-strain and adhesion properties at high deformation rates, and can cause the coating to fail by a variety of failure modes such as cracking, delamination, marring or any combination of these failure modes.
The drop impact results for the PLA coatings are summarized in Figure 8. The results highlight an excellent combination of the physical properties enabled by the PLA polyol initiator type and crosslink density. Take for example, the PLA urethanes made with 112 OH value polyols. These polyols will have the highest crosslink density of the series, and it was noted all of these coatings had excellent front side impact showing no damage or delamination at 80 in-lb (9 N·m) of direct impact force. However, the reverse side impact data for the PG polyol showed clear microcracking and delamination at even 10 in-lbs. (1.1 N·m). In contrast, the 112 OH value polyols based on 1,6-HDO, 1,12-DDO and Penta PLA polyol did not exhibit any reverse side impact damage at the max test condition of 80 in-lb force. As the OH value decreases to 56, the crosslink density decreases and therefore the network strength also decreases. As noted in the reverse impact strength data, the coatings made with the PG and 1,6-HDO polyol failed the reverse impact test, but coatings made with 1,12-DDO and Penta exhibited no damage at 80 in-lb. These data further indicate the influence of the initiator segment on the PLA urethane coating properties.

Influence of Crosslink Density
The performance data for the crosslinked PLA systems show promising results for the use of PLA polyols in urethane coatings. Of particular interest is the use of multi-functional PLA polyols such as the Penta-PLA with HMDI trimer. A very good combination of solvent, impact and hardness properties were noted for the 1-1 stoichiometric ratio of the Penta PLA polyol with the HMDI trimer which influences the crosslink density of the PLA urethane network.
The relationship between the physical properties of a crosslinked polymer and the crosslink density (XLD) or the average molecular weight between crosslinks was developed by Flory and Rehner.8 The equation, which now bears their name, describes the mathematical relationship for the mixing of a liquid and a solid, and the equilibrium swelling behavior of the solid. The degree of equilibrium swelling of the crosslinked polymer by that solvent is inversely related to the crosslink density. (The more crosslinks per polymer chain, the less the polymer network will swell). They found that this relationship between the change in crosslink density and swelling could be related to the elastic modulus of an elastomeric polymer network and hence its properties. Campbell used the same theory but modified and simplified the calculation to determine the XLD of a coated polymer network based on the stoichiometry of the reagents, the total functionality and hence the coating properties.9 Using the method described by Campbell, it is possible to estimate the XLD of the different PLA polyol-HMDI formulations evaluated in this study. Figure 9 shows the calculated crosslink density (XLD, mole XL/g polymer) versus the polyol hydroxyl number and PLA functionality. For these calculations, the functionality of the HMDI-trimer was assumed to be 3, and the reaction was assumed to 100% complete. These calculations enabled us to gain insight into how the properties of the coating are influenced by the stoichiometry between the PLA to HMDI trimer. We also include the calculated XLD for a glycerol-initiated PLA polyol with a functionality of 3 to complete the comparison of polyols with 2 and 4 equivalents of hydroxy groups per mole polyols with functionalities of 2, 3 and 4. However, it is possible to refine these calculation further by using a range of values that bracket the formulation parameters such as the extent of reaction, average functionality, and reaction stoichiometry.
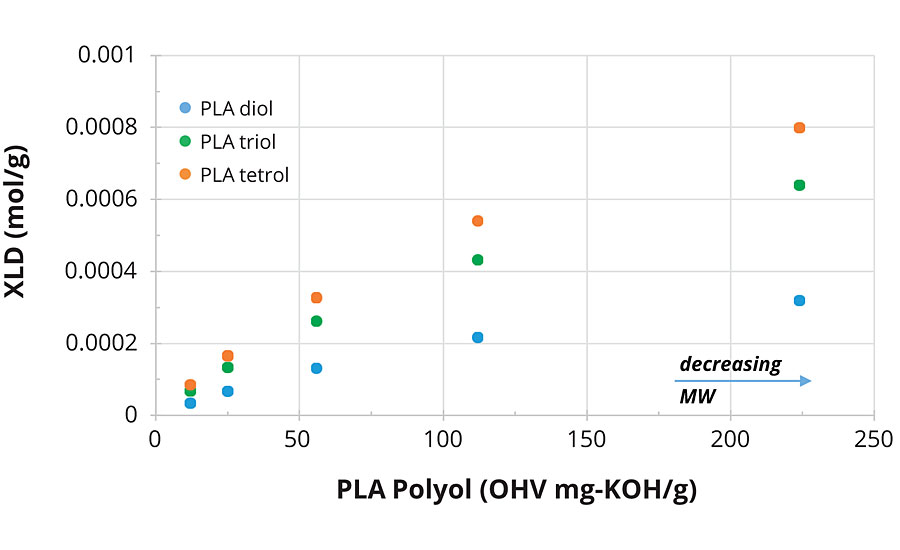
As noted in the coatings data, the PLA polyols with higher functionality and higher OH value should have a higher XLD increase, which can explain the observed impact on the properties such as hardness and solvent resistance. For example, the Penta-PLA polyol with OH value of 56 and 112 had better properties than PLA-based on PG diol. However, we also noted the influence of the initiator on the properties. The PLA polyols made with 1,6-HDO have similar coatings performance attributes as the Penta PLA at an OH value of 112 but poorer impact resistance than the Penta at 56 OH value.
Conclusions
Figure 10 provides a summary of the mechanical property trends for a PLA urethane coating as a function of PLA polyol type. For example, the 56 OH value PG-initiated polyol can make a coating with excellent adhesion, impact hardness and solvent resistance, but the impact resistance is lower. If this polyol were replaced by a polyol initiated with 1,12-DDO, the coating becomes softer, but the impact resistance improves. When the polyol was initiated by pentaerythritol as the initiator, all of the key properties of hardness, solvent and impact resistance remain high.
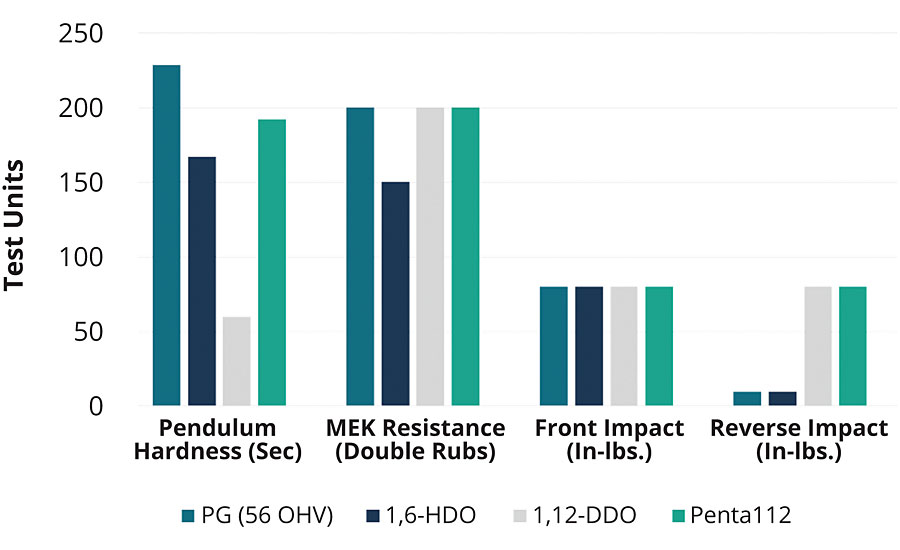
This article provides further insight in how PLA polyols expand the formulator’s toolbox for the development of coatings with improved key properties such as hardness, adhesion, solvent resistance and fracture toughness. Many of the PLA polyols discussed in this article are also compatible with common polyols such as certain adipates, polyethers and caprolactone polyols, and therefore further expands the coating formulation window. Knowing the influence of the PLA structure on the coating properties opens up the use of PLA polyols for the development of high-performance, bio-based urethane coatings that can bring value and sustainability for wood, paper and metal substrates.
References
1 Polylactic Acid, Synthesis, Structures, Properties, Processing and Applications, Auras, R.; Lim, LT.; Selke, S.E.M.; Tsuji, H., editors, Wiley Scientific, 2010, ISBN978-0-470-29366-9. See also Polylactic Acid PLA Biopolymer Technology and Application 1st ed., Sin, L.T., editor, Plastic by Design Library, 2012, ISBN 9781437744590.
2 NatureWorks LLC, Product and Application Brochures, see www.NatureWorksllc.com.
3 Ingeo™ Product Brochure and Physical Properties, see www.Natureworksllc.com.
4 Titration was conducted using a Metrohm automated titrated and the end point was determined potentiometrically. E1899-08 is also referenced as part of Metrohm Applications Bulletin 200/3e.
5 Idage, S.; Idage, B.; Rahman, I.; Sathe, V.; Metkar, S. Ring Opening Polymerization of Lactide: Kinetics and Modeling, J. Chem. Eng. Comm., 2019, 206(9) p. 1159.
6 Sin, L.T.; Rahmat, A.; Rahman, W.A. Handbook of Biopolymers and Biodegradable Plastics, Plastic by Design Library, 2013, pp.55-69. https://doi.org/10.1016/B978-1-4557-2834-3.00003-3.
7 Coggio, W.; Gehrung., M.; Tjosaas, M. Lactide Polyester Polyols in Polyurethane Coatings, presented at Coatings Trends and Technology Conference, Sept 10, 2019 Track 3.
8 Flory, P.J.; Rehner, J. J. Chem. Phys., 1943, 11, p.521.
9 Campbell, D.H. Calculation of Crosslink Density of Thermoset Polymers, A Simpler Method, Paint and Coatings Industry Magazine, 2018. July p. 33.
Looking for a reprint of this article?
From high-res PDFs to custom plaques, order your copy today!