The Impact of Insoluble Cellulose Fibrils
on the Rheology of Water-Based Acrylic Satin Paint Upon Tinting

It is commonly known that waterborne formulations still suffer from several issues, and it is not always possible to obtain the same performance as with solventborne systems. One of the typical challenges with waterborne systems is related to the behavior of rheology modifiers in the presence of surfactants as well as under extreme pH conditions. The common rheology modifiers can be divided roughly into two categories, associative and non-associative. The former is typically sensitive to the presence of surfactants, and this is often seen after the tinting of the base paint. In most cases, the viscosity of the paint reduces as a consequence of disturbance in the associative network due to the surfactant’s presence in the tinting paste.
Microfibrillated cellulose (MFC) is a multi-functional additive for coatings, adhesives and sealants, with a pronounced effect in improving rheology, stabilization and surface properties. MFC is suitable for a wide variety of polar organic and waterborne systems, enabling the control of viscosity and modification of thixotropy of various water and polar solvent-based systems. The high inertness, compatibility and stability of MFC allows the development of stable and robust formulations, even under demanding conditions. In addition, MFC offers solutions for formulators for improved anti-settling, anti-syneresis and anti-cracking of coatings formulations.
The compatibility and rheological behavior of microfibrillated cellulose has previously been studied in water-based acrylic and epoxy systems. 1,2 The results from these studies showed that MFC dispersed very well into the resins and showed good compatibility. In addition, the viscosity and sag resistance increased with increasing concentration of MFC. Furthermore, the dispersions were heat stable in terms of sedimentation and retention of rheological properties.
The unique rheological properties of MFC lead also to better control of the formulations by controlling the flow of the particles. It has been shown that MFC can prevent the coffee-ring effect during the drying process of films, leading to a better distribution of particles and pigments. 3 This opens up possibilities for increased effectiveness and better color development of pigments and fillers, such as titanium dioxide.
Microfibrillated Cellulose
MFC was first introduced back in the 1980s. 4 Over the years its potential and possible uses have been reported extensively, ranging from use as a thickener in cosmetics to an oxygen barrier in food packaging. 5 Until the beginning of 2010 the research and small-scale production of MFC was conducted mainly at universities and small pilot facilities. Borregaard launched the world’s first commercial production facility of MFC, opening a 1,000 dry MT Exilva ® factory in 2016. 6
MFC consists of long and thin cellulose fibrils that form a three-dimensional network. The secret behind the unique properties is the extremely large surface area, combined with numerous hydroxyl groups on the surface of the fibrils. The interaction of MFC is based on physical as well as on chemical interaction in the formulation. The main characteristics of this unique fibril structure resembles a hybrid of water-soluble polymers and insoluble additives. MFC has high viscosity and yield stress, is shear thinning and has high water holding capacity. The insoluble nature of the cellulose fibrils also leads to excellent stability and compatibility. MFC is stable at a wide pH range (1-13) and is compatible with common water-miscible organic solvents as well as with surfactants.
Compared to common polymer solutions in water, the rheological properties of MFC suspensions are quite different. First of all, the viscosity does not reach a plateau at low shear as it normally does in polymer solutions. This can be seen in Figure 1, which shows that the viscosity of MFC suspension increases as the shear rate decreases. Instead, the viscosity of hydroxyethyl cellulose (HEC) solution reaches a plateau around the shear rate of 0.1 s -1 . This means that the viscosity at rest is much higher for MFC, nearly 100 times higher. This will give considerably better stability under storage, especially in terms of syneresis and settling. At higher shear rates, HEC solution and MFC suspension have comparable shear thinning, which helps in pumping, spraying, mixing and application of the formulation.

Due to the high viscosity at low shear rates and exceptional shear thinning behavior, MFC can also be used as a thickener in products that are intended to be applied by spraying. MFC secures high stability during storage and allows the spraying of very thick suspensions since the viscosity decreases during the spraying. However, when the product has been applied and no forces are applied, the viscosity recovers quickly, and the product remains where it impacts the surface without sagging (Figure 2). In addition to anti-sagging, the use of MFC leads to a non-dripping effect, which is often desired in coatings.
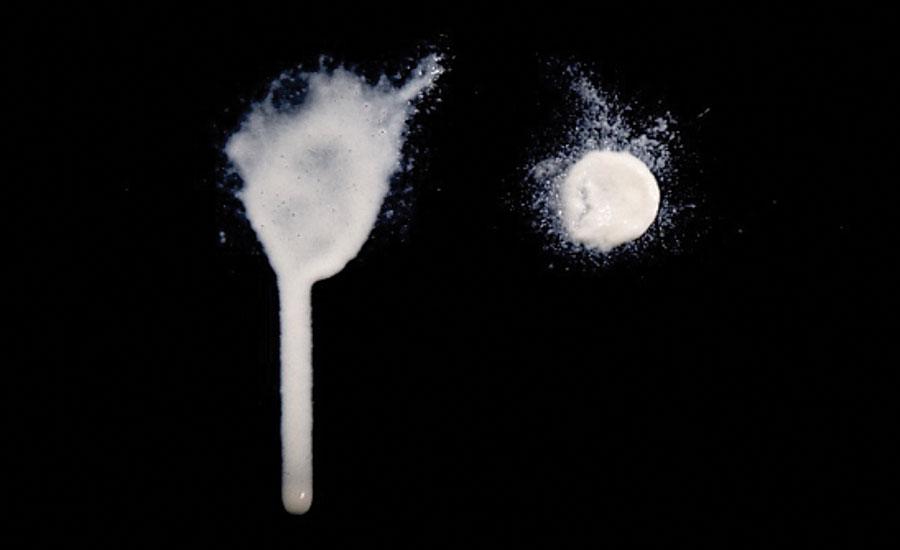
Materials and Methods
Commercially available MFC was used in this study, MFC (Exilva F 01-V), containing 10 wt% MFC in water (manufactured by Borregaard). The following universal colorants were used for tinting: 808-9907 lamp black, 808-7214 phthalo blue and 808-1045 red iron oxide. Sag resistance (tinted) was determined according to ASTM D4440, flow and levelling (tinted) according to ASTM D4062, gloss (tinted) according to ASTM D523, scrub resistance according to ASTM D2486 and block resistance according to ASTM D4946. The rheology was measured with an Anton Paar rheometer using a bob and cup measuring geometry.
Effect of MFC on the Loss of Viscosity and Color Float of an Acrylic Coating Upon Tinting
The effect of MFC on film properties as well its ability to prevent loss on tinting and color float was studied with an acrylic deep base formulation (Table 1). The formulation was based on an acrylic binder, with either non-ionic urethane modifier (HEUR) as a thickener or MFC as a functional additive. In both cases, HEUR thickener was used to adjust the high-shear viscosity. The base paint was tinted with three different colorants, 8 ounces per gallon.
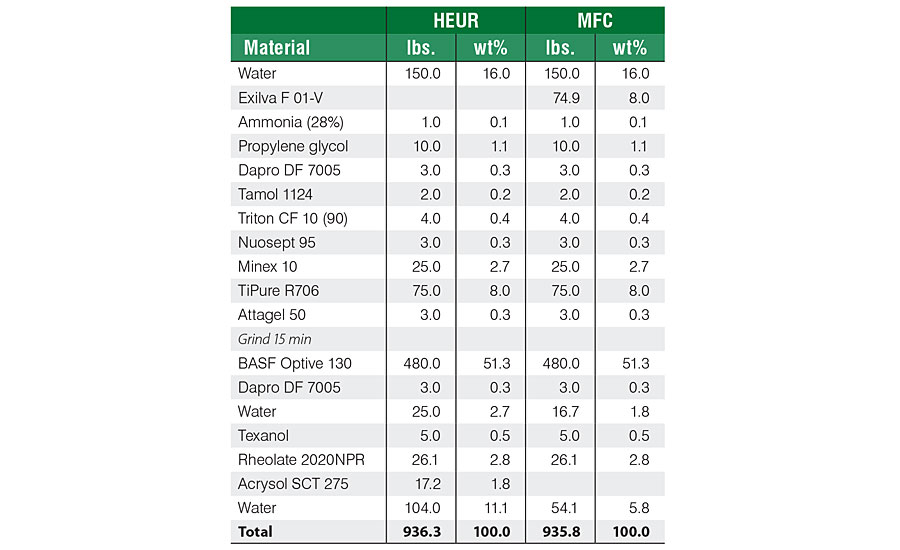
The effect of MFC on viscosity retention after tinting with 808-9907 lamp black (8 ounces per gallon) can be clearly seen from Figure 3. The viscosity of the HEUR-based formulation drops 12.6%, whereas the formulation based on MFC only 4.0%. The difference can be explained by the physical nature of the MFC fibrils. The thickening effect of MFC is based on the physical interaction with the fibrils as well as on the hydrogen bonding with the other components in the system. Therefore, the network is not affected by the presence of surfactants or other hydrophobic compounds.

A major difference was also noticed on the sagging (Table 2). The high viscosity at rest and relatively fast viscosity recovery of MFC resulted in a sag resistance rating of 24 according to ASTM D4400, whereas the formulation based on HEUR resulted in a sag rating of 4. Color acceptance was at a similar level for both formulations. Color float was slightly lower for MFC. A strong effect on gloss was noticed when MFC was used as a rheology modifier. The gloss for the HEUR-based formulation was 37.2 (60°), whereas for the MFC-based formulation it was 10.1. As the levelling for both formulations was at a similar level, 9 for HEUR and 8 for MFC (ASTM D4062), the loss on gloss is thought to be related to the physical structure of the MFC fibrils, leading to a matting effect. This also means that MFC can be used to formulate smooth-surface flat paints at higher dosage levels. Both formulations showed good scrub resistance, MFC resulting in a slightly higher resistance (1,351 vs 1,278).
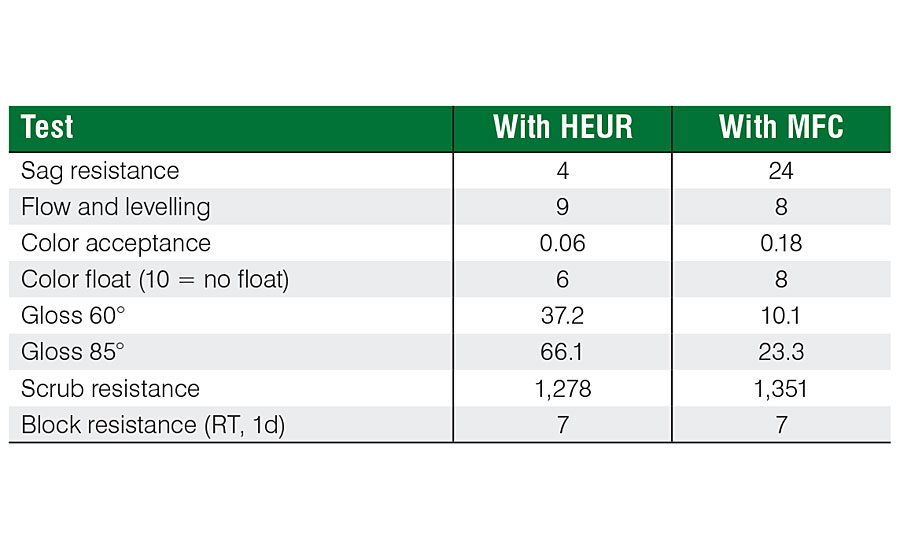
The effect of colorants was further studied with phthalo blue and red iron oxide (Table 3). The same trend was observed also with these colorants. MFC effectively prevented the loss on viscosity after tinting, whereas the formulation based on HEUR resulted in a significant drop in viscosity (Figure 4).
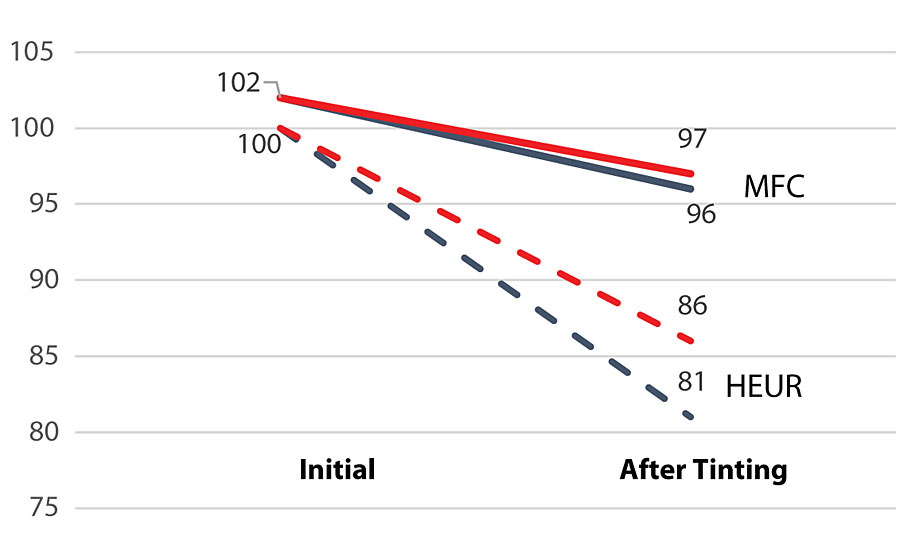
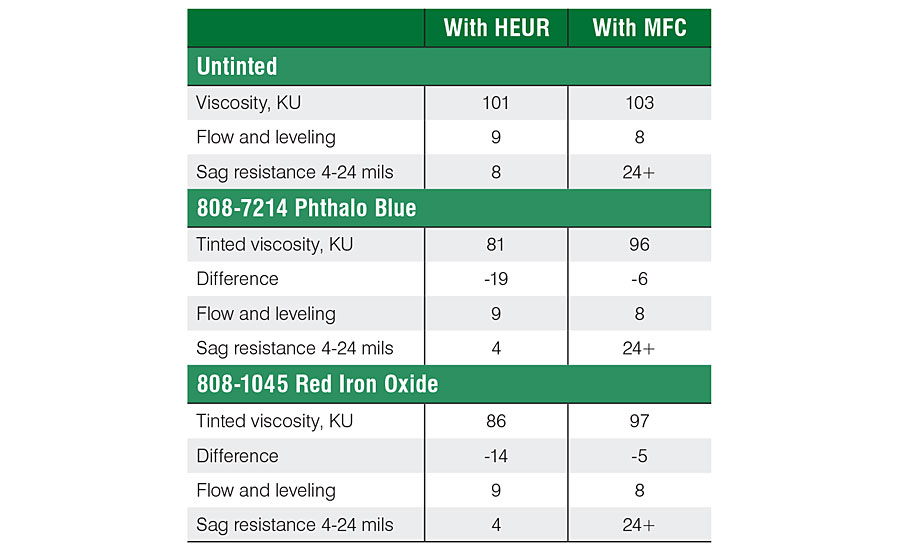
The behavior of the tinted paints was further studied with a rheometer. First the untinted paints were analyzed in order to have the reference values. The untinted paint, based on MFC, showed high viscosity at rest, combined with strong high-shear thinning behavior (Figure 5). The viscosity at rest was 10 times higher for the formulation based on MFC when compared to the formulation based on HEUR. At the high-shear area, viscosity of the MFC-based formulation was half of the HEUR-based formulation. The shear curve results were well in line with the sag resistance values (Tab. 3).

After tinting the paint with 808-9907 lamp black (8 ounces per gallon), a dramatic drop at the low-shear area viscosity was observed with the formulation based on HEUR. The viscosity at the low-shear area dropped from around 10 Pa.s to 1 Pa.s, whereas the viscosity of the formulation based on MFC remained nearly the same (Figure 6).
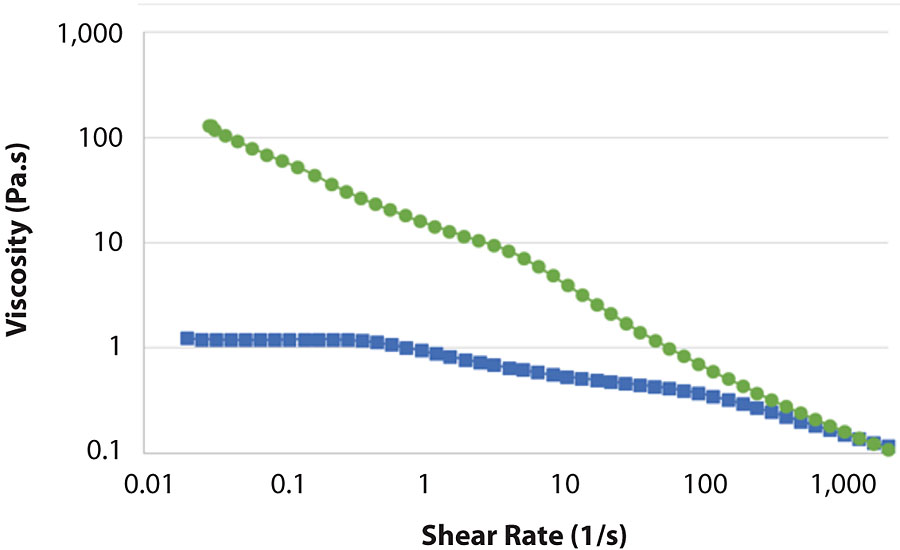
The paint tinted with blue colorant behaved almost identically with the paint tinted with lamp black (Figure 7). A difference was observed when the paint was tinted with 808-1045 red iron oxide (Figure 8). Again, the formulation based on MFC behaved nearly the same as the untinted paint. The formulation based on HEUR showed less drop in viscosity than with black and blue colorants. This correlates well with the KU results (Tab. 3). However, the viscosity of the MFC-based formulation was still 20 times higher at rest.
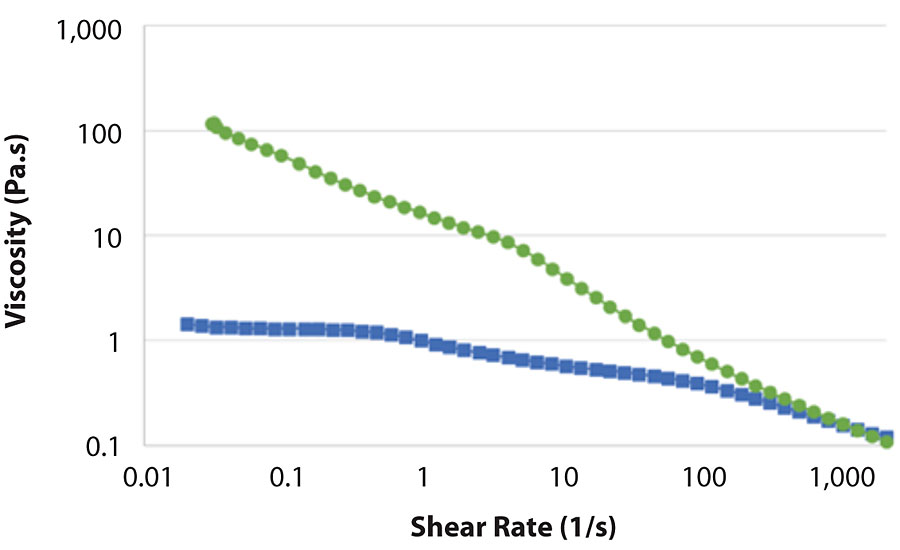

Conclusions
The effect of MFC on the rheology of coating formulations is striking. MFC effectively prevents viscosity loss after tinting. The high viscosity at rest, combined with high yield stress, results in stable formulations and allows homogenous formulations even in the presence of heavy particles or low-density fillers. In addition, the high viscosity at rest enables increased applied film thickness, thereby reducing the number of applied film layers required, without comprising the final coating properties. The relatively fast viscosity recovery leads to excellent sag resistance without sacrificing the levelling of the coating.
In addition, MFC helps to reduce the color float of the coating. Depending on the dosage of MFC, effects on the gloss of the coating can be seen. This opens up possibilities to formulate smooth-surface flat paints. MFC is a sustainable, renewable and VOC-free multi-functional additive, which cannot only replace synthetic additives in formulation, but also contribute added value to the end products.
References
1 Moosavifar, A.; Holtan, S. European Coatings Congress proceedings, 2015.
2 Falkenberg Olsen, A.M.; Holtan, S.; Moosavifar, A. European Coatings Journal , 2015 , 07/08, 30.
3 Ooi, Y.; Hanasaki, I.; Mizumura, D.; Matsuda, Y. Science and Technology of Advanced Materials , 2017 , 1, 316.
4 Turbak, A.F.; Snyder, F.W.; and Sandberg, K.R. US Patent 4,500,546, 1982.
5 Klemm, D.; Kramer, F.; Moritz, S.; Lindström, T.; Ankerfors, M.; Gray, D.; and Dorris, A. Angewandte Chemie Int. Ed . 2011 , 24, 5438.
6 www.exilva.com
This paper was originally presented at the 2019 European Coatings Conference in Nuremberg, Germany.
For more information, email otto.soidinsalo@borregaard.com.
Looking for a reprint of this article?
From high-res PDFs to custom plaques, order your copy today!