Faster, More Reliable and More Efficient Filling

Pictured in front of the fully automated filling system AFS 22 from Fricke (left to right): Dirk Novak, sales engineer at Fricke; Jochen Weghorn, head of production UV, Nino Sandner, head of production WB at WEILBURGER Graphics; Michael Krietemeier, project engineer at Fricke; and Günter Korbacher, managing director of WEILBURGER Graphics GmbH.
Speed, efficiency, flexibility, and reliability play a key role in industrial production. This also applies at WEILBURGER Graphics GmbH, a company belonging to the Weilburger Group, with headquarters in the northern Bavarian town of Gerhardshofen. As one of the world’s leading suppliers of coatings, adhesives, and flexographic inks for the printing and packaging industries, the company develops and produces its innovative products on two of the world’s most state-of-the-art production systems in this market segment. To be able to fill coatings faster, more reliably, and in larger quantities, Weilburger has benefited from the use of various automated and semi-automated filling systems from Fricke Abfülltechnik since 2010. Thanks to its steadily increasing order volumes, WEILBURGER Graphics will put an additional Fricke system into operation during the course of this year.
Every day, WEILBURGER Graphics produces more than 130 tons of water-based and UV varnishes for the graphics industry; these coatings can be used, for example, in the manufacture of food packaging made of cardboard or plastic. To optimize the process of filling coatings in different batch sizes of up to 30 m3, the company has been investing in new production systems since 2010, with the family owned company Fricke, from Minden, as their preferred manufacturer. “With Fricke, we’ve found a very capable, cooperative, and trustworthy partner that has advised us competently and on equal terms since the very start. The equipment was built in line with our requirements and integrated into our production processes according to our wishes in a way that allows for a perfect workflow,” said Jochen Weghorn, head of production UV at WEILBURGER Graphics.
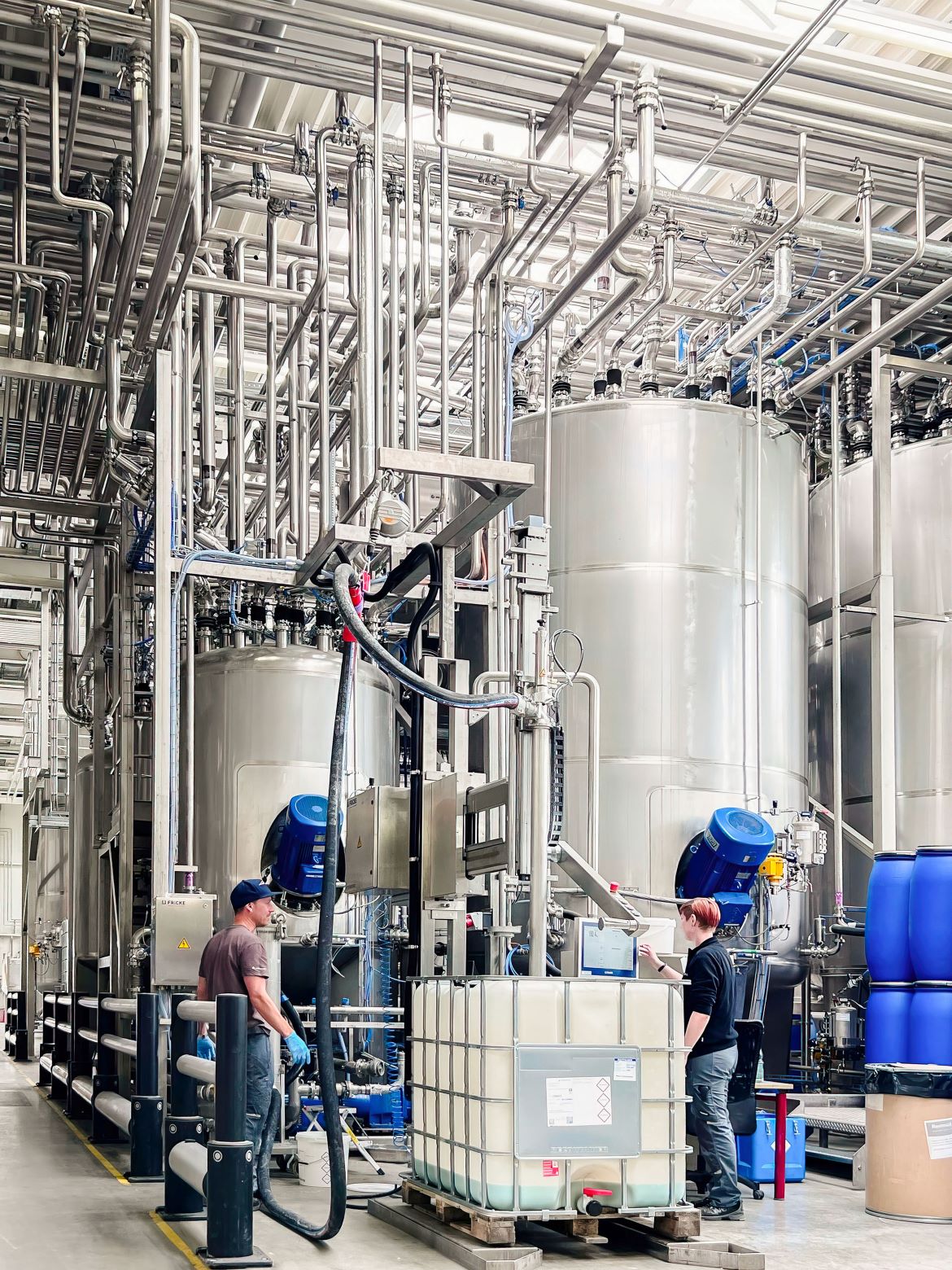
Faster Filling and Increased Reliability
Filling large quantities of coatings parallel to the production process posed a considerable challenge, since it required drums or IBCs to be filled directly from two production tanks alternately. Fricke’s filling systems for large containers handle this flawlessly, and without waiting times. “The systems were constructed in a way that allows the filling to take place directly on the pallet, and the machine operator can control it with a single hand, making the process much more ergonomic,” explains Dirk Novak, sales engineer for Filling Technology at Fricke. “In the area of WB coatings, we were able to use these systems to speed up the filling process. They also improved the reliability of the filling process, which previously required manual measurement using mobile scales,” shared Jochen Weghorn. “It’s especially convenient that we don’t need to modify the system when switching between different container types. Once the program number has been entered, the equipment automatically adjusts itself for the corresponding container size, helping reliably prevent damage to the machine and the containers, and allowing for the filling process to begin.”
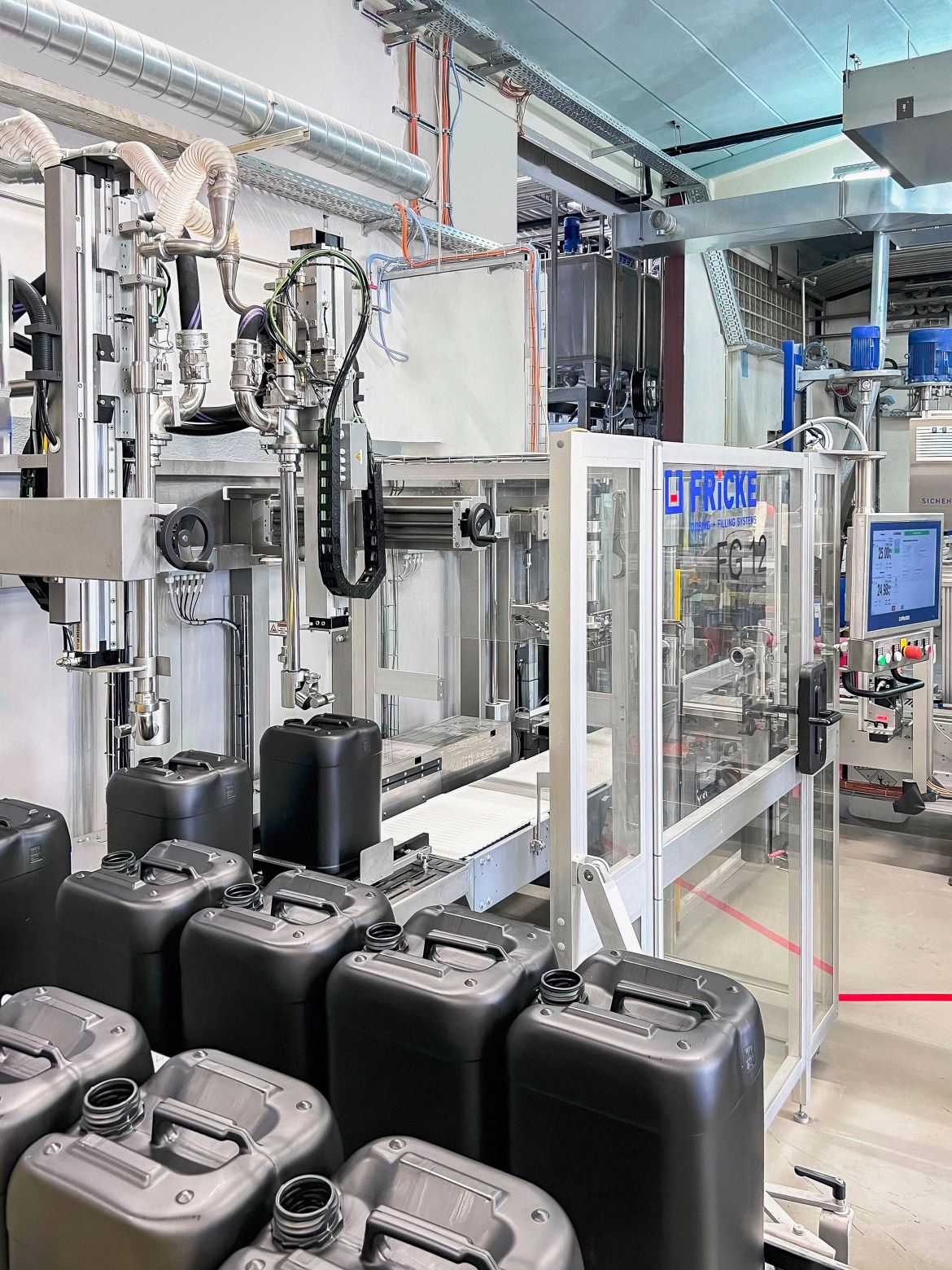
Fully Automated Filling for Different Container Sizes
Moreover, since there are customers whose coatings are supplied in a wide range of canisters, Weilburger has also been using the fully automated AFS 22 filling systems since 2013. These systems enable the company to fill 15,000 kg of coatings into canisters and close them, all in less than four hours. The various modules also allow for the containers to be labeled and palletized straight away, so that they can be transferred to the finished goods warehouse. “Besides features such as calibratable filling, fast valve cleaning and fast adjustment to different container measurements, and changing products, the equipment’s fully automated setup allows it to be easily operated by a single person,” explained Dirk Novak. Since the order volumes at WEILBURGER Graphics have grown considerably over the years, the company decided to order an additional AFS 22 with two valves. “This enables us to fill larger quantities faster, helping us cater to the continuous growth in demand,” said Nino Sandner, Head of Production WB at WEILBURGER Graphics GmbH.
“Besides Fricke’s semi-automated filling systems, which we have been using since 2010, the fully automated systems are the perfect addition to our production process. Our cooperation with Fricke has been smooth and very customer-focused, from the design through the completion of the equipment,” related Nino Sandner. “The systems were manufactured in accordance with our requirements and with Fricke’s helpful recommendations. They were integrated into our existing production space, as requested, allowing for the best possible workflow. We look forward to commissioning the next Fricke system into operation in the third quarter of this year.”
For more information, visit: www.weilburger.com.
Looking for a reprint of this article?
From high-res PDFs to custom plaques, order your copy today!