Medical Device Coatings

nopparit, iStock / Getty Images Plus, via Getty Images.
Over the past 50 years, there have been several notable developments in the medical device industry, including the incorporation of advanced tools and technologies, such as artificial intelligence (AI) and machine learning, which support the advancement within the digital health sector and led to the acceleration of the use of biomedical devices, such as medical implants, surgical instruments, and prostheses. In fact, every year, millions of individuals undergo surgeries and implantations; some of the most commonly implanted devices include cardioverter defibrillators, prosthetic hips and knees, contact lenses, and cardiac pacemakers. Notably, fixation devices and artificial joints account for about 44% of all medical devices.
However, despite the significant advancements in the design and implantation of medical devices, several challenges persist in this sector. Patients, particularly those who are immunocompromised, are at high risk of contracting healthcare-associated infections (HAIs) due to the in-dwelling nature of implanted devices and surgical tools. Other limitations include implant rejection, osseointegration, degradation and wear, and loom over the prosthetic integration. Consequently, in recent years, the medical device industry has seen a surge in medical device coatings as a method to tackle these challenges. One such example is the biomedical implant coating. These coatings are being used to enhance biological interaction between the implant and the host, mitigate joint wear, and combine the properties of several materials to enhance device performance, as well as reduce the risks associated with invasive medical devices. Medical device coatings also aid in lubrication and exhibit antifouling properties, while enhancing the durability of the device surface.
Medical Device Coatings
Production of effective, functional, and affordable medical devices, coupled with their hygienic and biocompatibility requirements, can be seen as one of the ongoing challenges of medical device developers. In order to mitigate such challenges, developers have initiated the implementation of surface coatings for biomedical devices with various types of materials, such as plastics, titanium, silicone, or apatite. Notably, these coatings can alter the physiochemical properties and functionality of the surface, depending on the intended application. It is worth highlighting that in order to accommodate the multifunctionality of novel medical devices, a broader range of coating materials with incredibly specialized design features are being produced. In fact, at times, multiple coatings are needed for the same device, as each layer of coating provides unique advantages (Figure 1).

Types of Medical Device Coatings
Different coating materials have been used to increase the biocompatibility of medical equipment. This can be attributed to the fact that each type of coating provides specific attributes to the medical device (Figure 2). Some of the common types of coatings (based on different applications) include lubricant coatings, antimicrobial coatings, and water-repellent polymer-based coatings.
- Lubricious Coatings: Medical devices that require more assistance when being placed into biological apertures or into the body, use lubricant coatings. Such coatings facilitate the interaction of the two separate surfaces by reducing the static and kinetic friction.
- Antimicrobial Coatings: The use of surface coatings that provide antibacterial or antimicrobial properties has increased over the years. In addition to preventing HAIs, antimicrobial coatings can also enable the release of pharmaceutical products, such as antibiotics, antimicrobial peptides, and silver (in case of exposure to bacterial species, such as Escherichia coli and Staphylococcus).
- Hydrophilic Coatings: Hydrophilic coatings are essential for surgical instruments, such as tubes and guide wires, which operate while constantly surrounded by physiological fluids and tissues, and need to have lower friction in order to aid the movements when inserted in the body. The mechanical design of hydrophilic coatings follows a low-friction biological format, which involves the use of polymers grafted onto polymeric materials that aid the binding of water, and provide hydrophilic surface coatings.
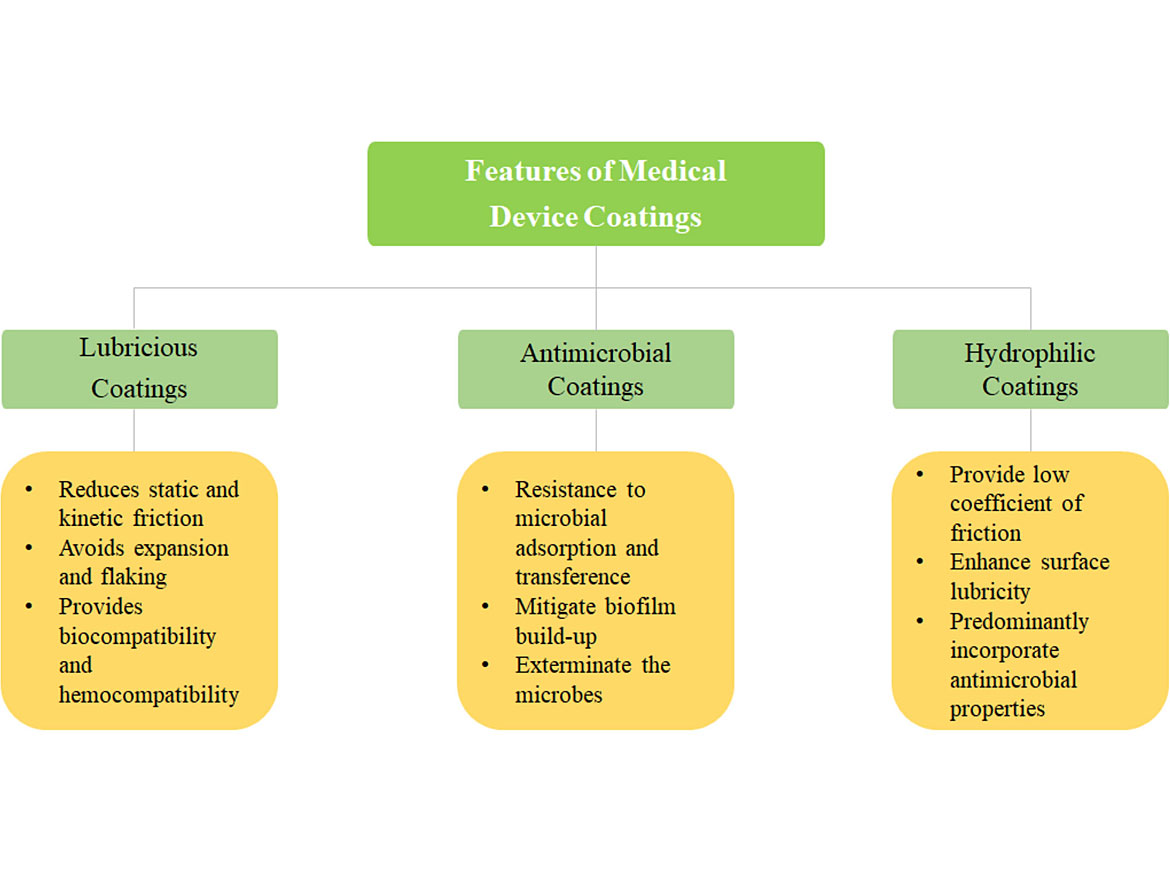
Advantages and Limitations of Medical Device Coatings
The selection of a biomaterial for a medical device depends on several factors that can affect the present as well as future potential of the device. Notably, biocompatibility remains one of the most important factors. Along with these factors, several advantages and limitations are taken into consideration for optimal device coatings (Figure 3)
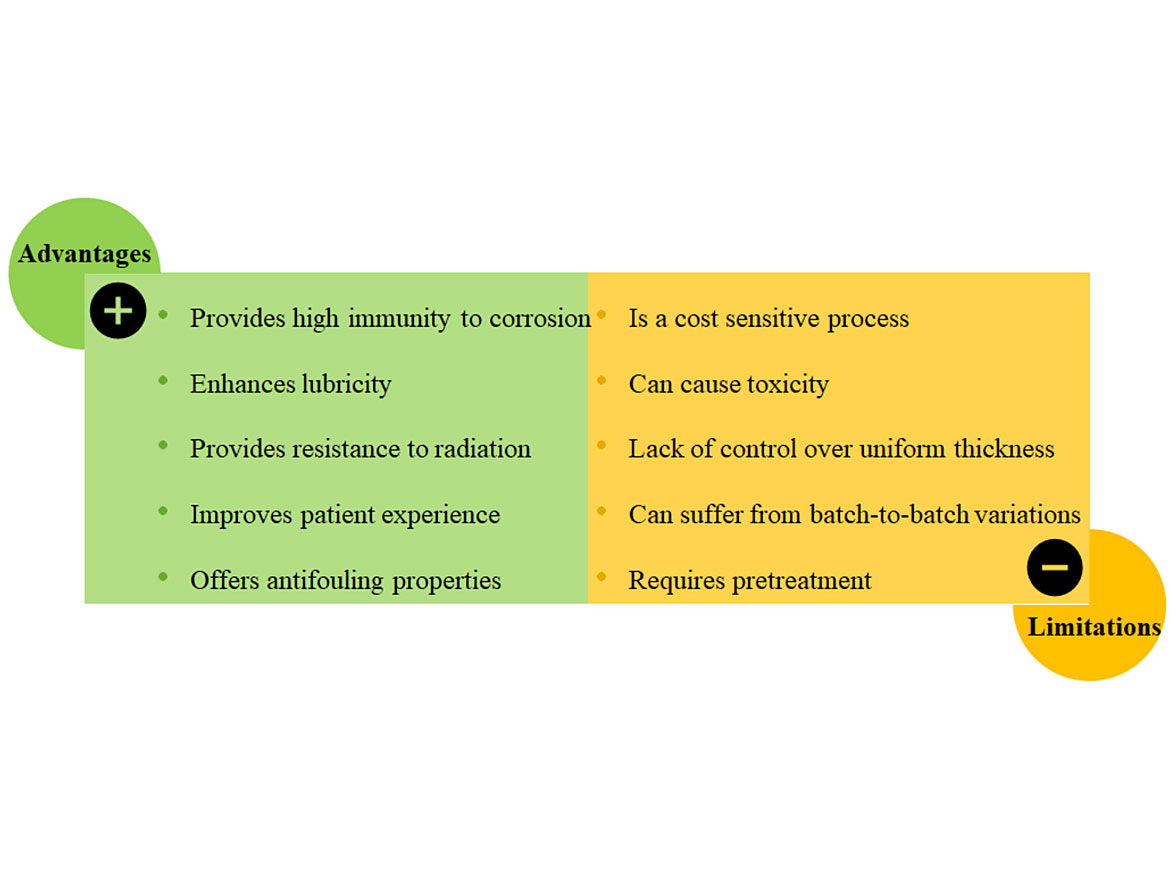
Future Perspectives
The healthcare industry has witnessed an extensive surge in the use of different types of medical devices. However, in recent years, the risk of using these medical devices (such as HAIs, infections, cytotoxicity, thrombogenesis, and immune rejection) have surfaced. In order to combat these challenges, stakeholders are levying a higher focus on the selection of suitable biomaterials and strategies for modification of the medical device surface. Some of the recent developments in this aspect include the creation of antifouling/antibacterial surfaces and development of graphene coatings, which not only elicit enhanced antimicrobial properties as compared to metal nanoparticles, but are also cost efficient. Further, it is worth mentioning that integration of new technologies (such as advanced laser processing, machine learning, and AI) drive the field towards automation, precision, and more reproducible coating/surface treatment applications, which can revolutionize the biomedical device industry. Given the rise in use of medical devices, coupled with the need for specialized coatings and innovative surface treatments, the domain is anticipated to evolve rapidly in the coming years.
Looking for a reprint of this article?
From high-res PDFs to custom plaques, order your copy today!