New Powder NiSAT Products for Architectural Paints Improve Rheology for Sustainable Manufacturing

Photos courtesy of Elementis.
Associative thickeners are standard in the formulation of modern aqueous systems, such as paints and coatings, adhesives, etc. These are either hydrophobic-modified acrylic thickeners, often called HASE, and the NiSAT group of products. The term NiSAT, which is often used for this class of associative thickeners, stands for “Non-Ionic Synthetic Associative Thickeners”.
The HASE product group contains ionic, mainly anionic thickeners, which require proper pH adjustment for activation. This product group utilizes two mechanisms, water thickening and associative.
The NiSAT product group, as mentioned, is already non-ionic and, in principle, is used over the widest range of pH values. These products represent an advanced product technology and are designed to give superior rheological characteristics so that many formulation requirements can be met. Depending on the product chosen, good levelling, spatter resistance, film build, and the flow characteristics can be achieved. The appearance of classic syneresis can even be minimized.
Furthermore, NiSAT products do not need special activation, so the majority can be added to the letdown or even at the end of processing. This product class does not adversely affect the corrosion or the water sensitivity of the resulting system, and other secondary parameters such as gloss will not be negatively influenced.
Chemistry
This class of thickeners consists mainly of non-ionic co-polymers. The structure is schematically represented in Figure 1 and can be described as a minimum of two hydrophobic groups chemically bonded to a hydrophilic backbone. The water-soluble part of the molecule takes typically ~95% of the molecule weight. The total molecule weight of NiSATs are typically in a range between 20,000 and 500,000 g/mol.
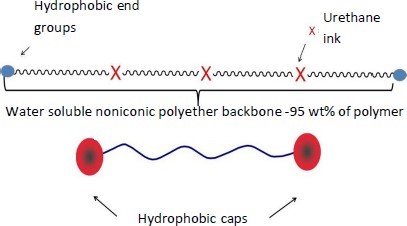
Figure 2 shows that RHEOLATE® powder NiSAT products can obtain all of the paint and coating industry-relevant rheology characteristics. This can be realized either by single or combined use of the products mentioned in Table 1.
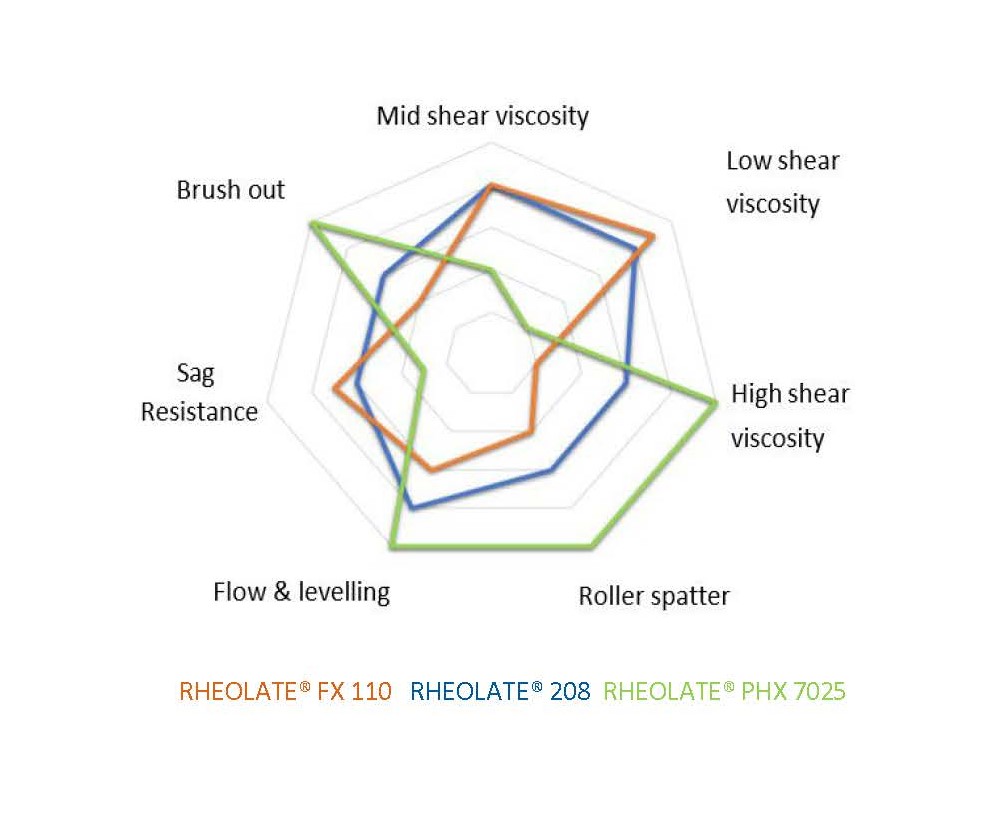
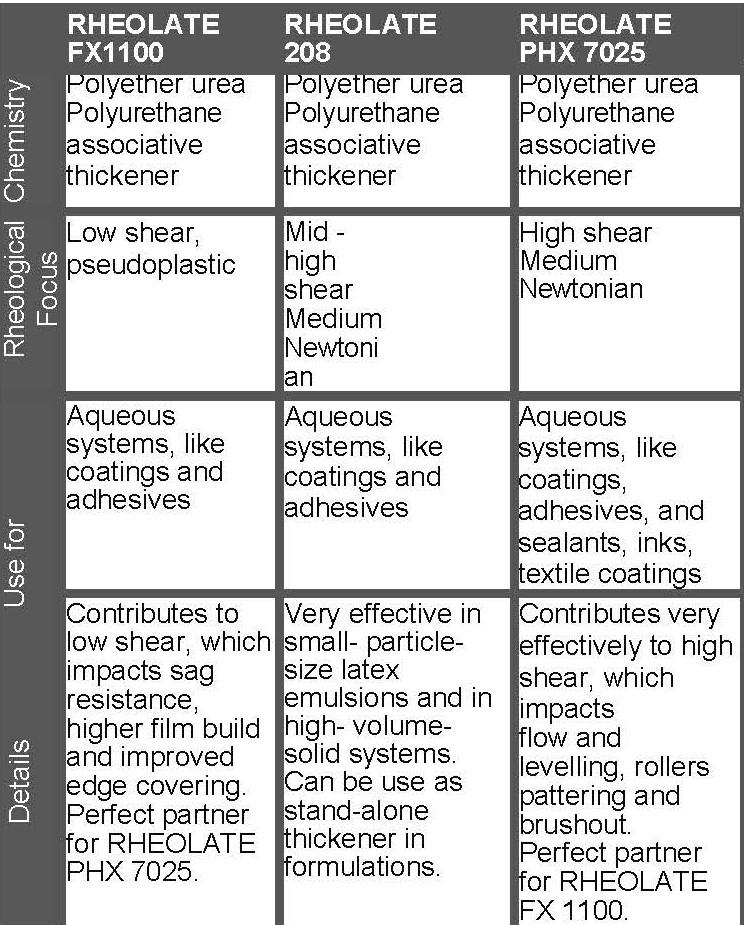
Sustainability
The use of powder in coatings formulations allow users to generate several benefits in the logistic and production process, including:
- Due to the use of only the active thickener in powder form, the transport volume can be significantly reduced.
- Approximately five times less volume has to be moved from the supplier to the manufacturer to obtain the same active thickener quantity compared to the relevant liquid product.
- Fewer trucks are needed for the required volume, which reduces carbon footprint on transportation up to 80%, according to our measurements.
- The reduced volume requires up to five times less storage area than with the liquid thickener version.
- Material transportation at the customer’s site is reduced in faster handling and logistical time savings.
- Powder thickener is generally less sensitive to low storing temperatures.
Safer Ingredients
Currently available RHEOLATE grades are only manufactured using tin-free catalysts. Further advantages from a safety perspective can be achieved since no biocides are used to the material thickener material. Emulsifier und surfactants are not needed during the incorporation process. Therefore, the VOC content of the final formulation can be lowered significantly. This leads to a very advantageous situation in terms of labeling (Table 2). Powder thickeners are free of labeling.
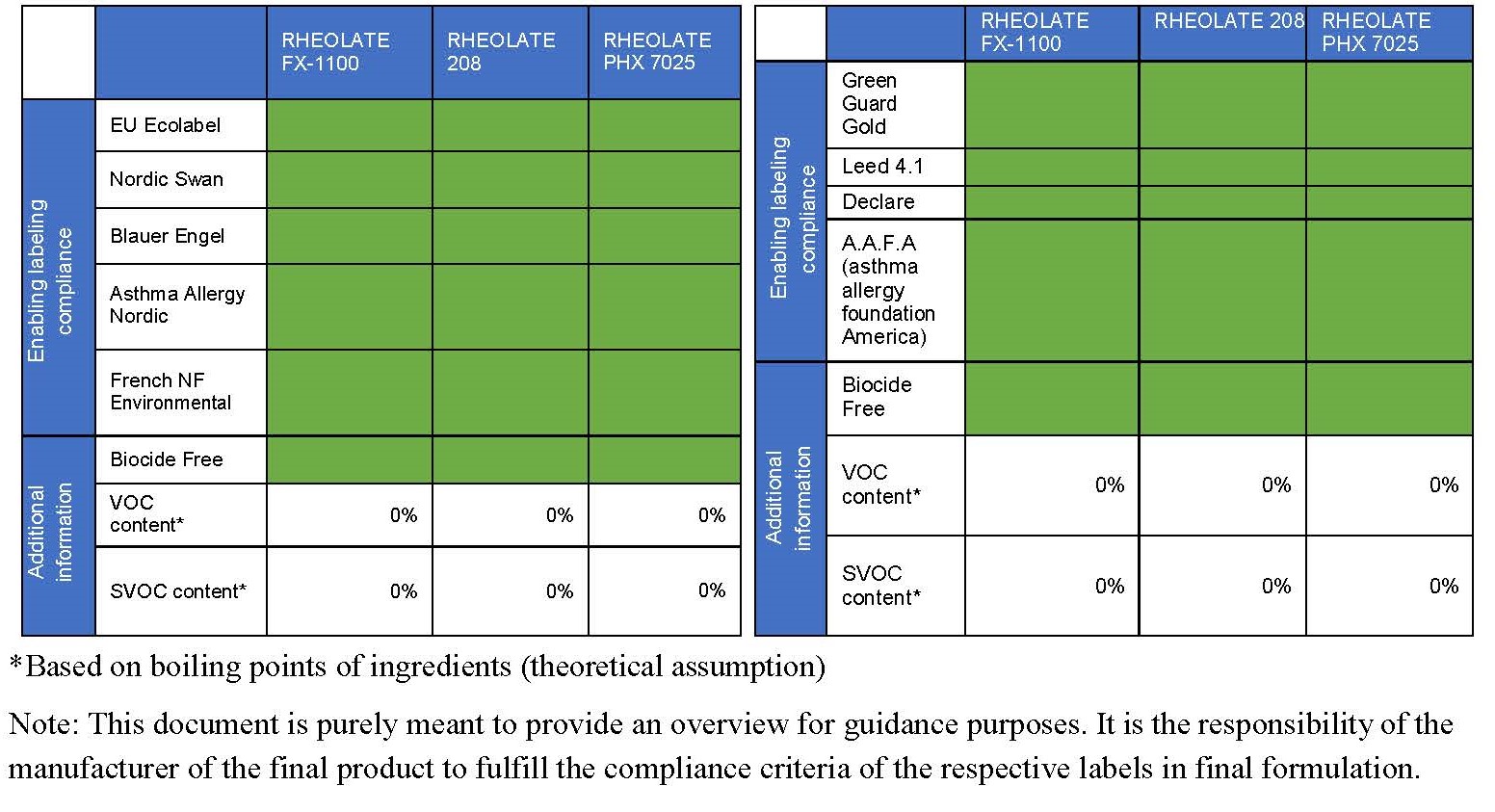
Flexible Use - Incorporation
The RHEOLATE powder NiSAT range has relatively low shear requirements for incorporation into the final system. We recommend the following processes.
Millbase Incorporation
During pigment and filler dispersion and milling, sufficient shear forces to incorporate the thickener easily and effectively are typically provided. Studies in low-PVC paint have shown that at a tip speed of 14 m/s for 30 min, e.g. by tooth bladed Cowles dissolver, is sufficient to produce particle-free end systems (Figure 3).
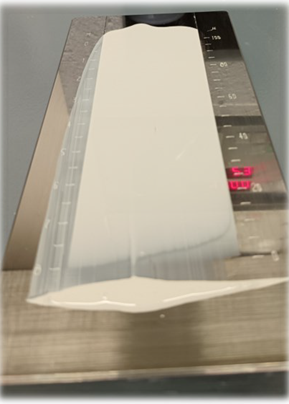
Post Addition
Post addition processes run with lower speed than mill base processes. Internal studies in low-PVC paints have revealed that 8 m/s in combination with ca. 30 min. allows formulators to incorporate the powder thickener without remaining particles.
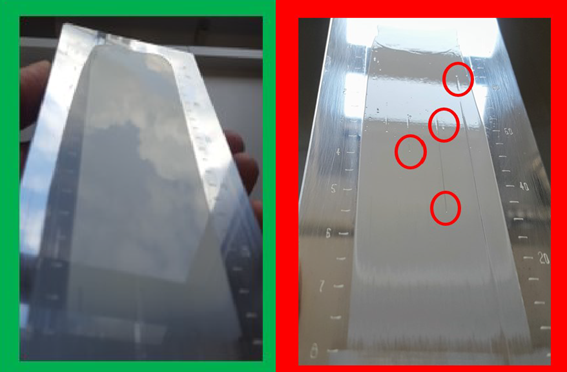
Intermediates
As a further method of incorporation, the RHEOLATE powder thickener group allows formulators to create intermediates with different solid content in water. As an example, RHEOLATE PHX 7025 pre-gels can easily be blended in ratio levels of up to 20%. Consider that typically supplied liquid NiSAT products contain in the majority up to 25%. Higher contents are generally possible but depend on handling. It is generally recommended to add biocide when the intermediate is stored for a longer period.
In the case RHEOLATE 208 and RHEOLATE FX 1100, the potential pre-gel concentrations are different. The following intermediate concentrations are recommended.
- RHEOLATE 208: 4%
- RHEOLATE FX 1100: 3%
- RHEOLATE PHX 7025: 20%
Incorporation can be done by Cowles dissolver (minimum of 20 minutes; 16 m/s) or propeller mixer at moderate shear (minimum 30 minutes).
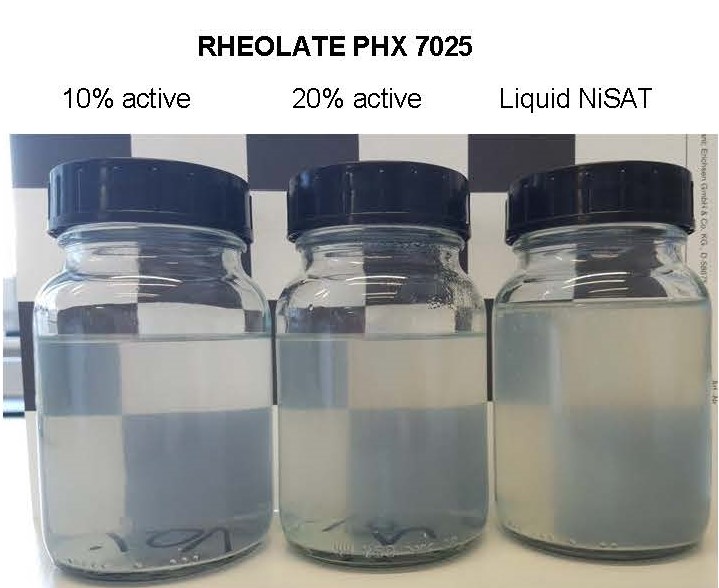
Efficiency
The NiSAT powder thickeners provide 100% rheologically active material. In the typically available liquid products, active content varies between 25-50%. Additionally to the active component, liquid NiSAT grades contain further chemicals to reduce the product viscosity to a manageable and pumpable level. These can be hydrophilic coalescents or surfactants. In the case of the powder versions, these components are missing. As a result, powder NiSAT grades provide higher effectivity compared to the liquid versions related to the active component.
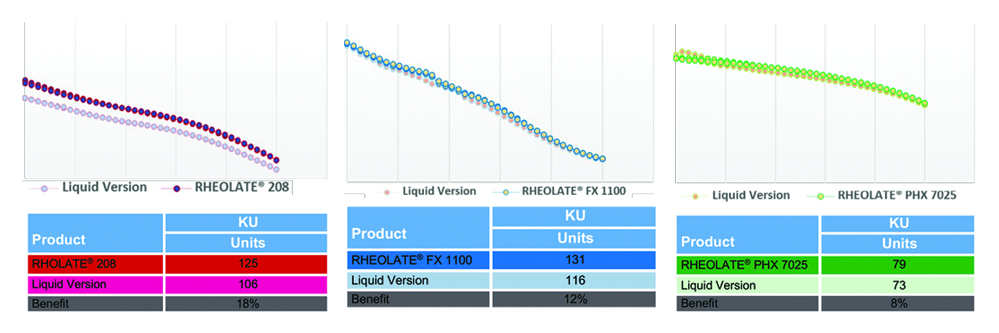
Figure 6 shows the results of an effectivity study in an aliphatic PU-alkyd dispersion. The active loading of RHEOLATE 208 and FX 1100 was 0.33%. Active loading was set to 0.86% for RHEOLATE PHX 7025. The active loading of the individually tested liquid versions was identical.
Film Properties
RHEOLATE powder NiSAT grades also generate benefits in terms of wet and dry film properties in comparison to the relevant liquid versions. This is the result of the powder thickeners not containing substances such as coalescents, emulsifiers, and surfactants as in liquid products. These substances can have an adverse influence on the resulting film properties.
Figure 7 shows a comparison of RHEOLATE PHX 7025 to various liquid Newtonian NiSAT grades in terms of their effect properties like color acceptance, rub out behavior, and viscosity stability. In the test, a colorant (1%; Chroma Chem black 7 WAB) was added to the same aliphatic PU-alkyd paint used in the efficiency testing.
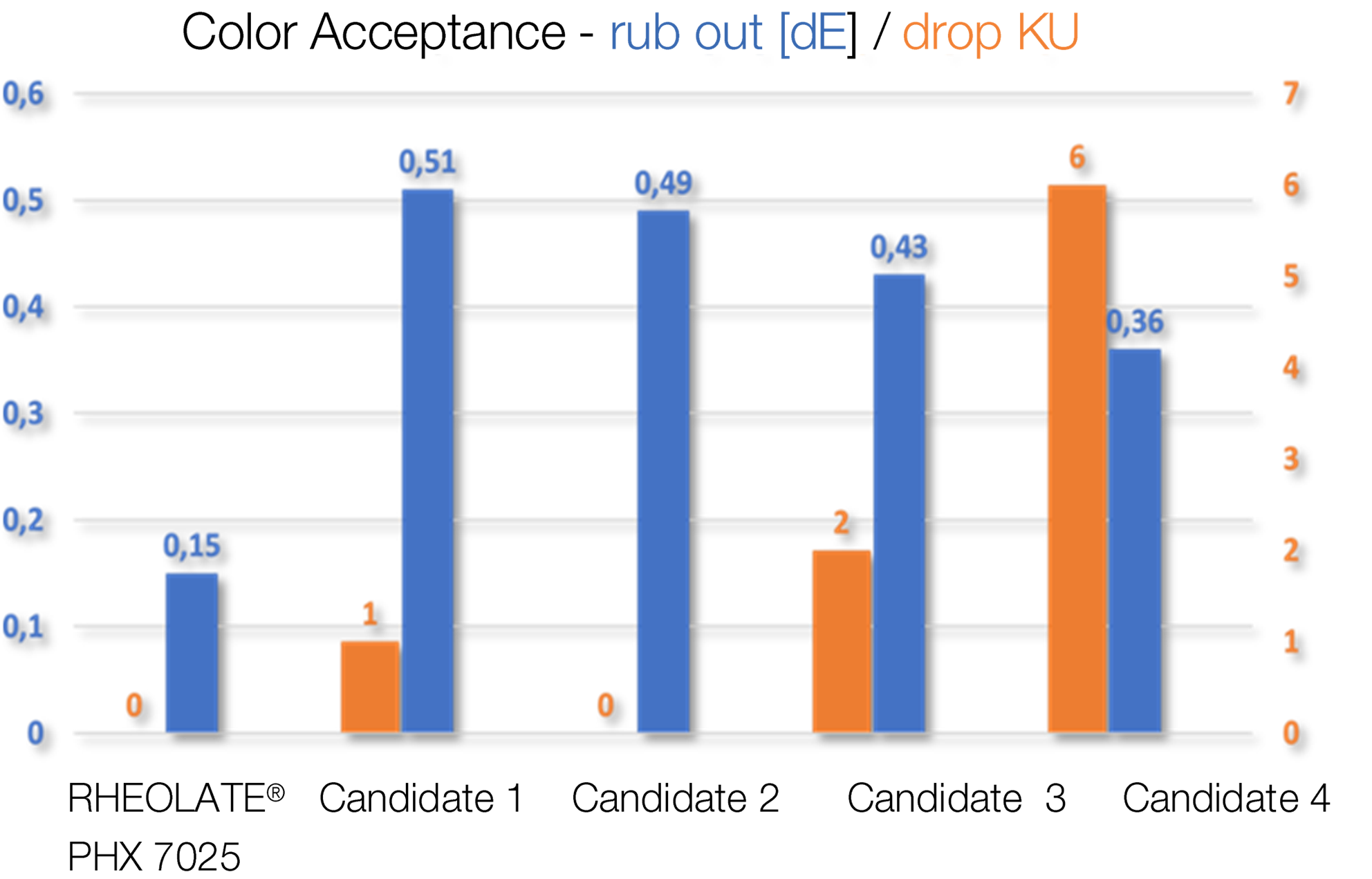
The sample formulated with PHX 7025 shows the best stability indicated by the lowest tan delta and KU differences after tinting.
Another large benefit can be achieved with the use of the powdered NiSAT grades in terms of blocking resistance. In Figure 8, the effect of the various NiSAT grades is shown on PU-alkyd-based paint. Active loading of all tested NiSAT grades was 0.86%.

It becomes obvious that the sample manufactured with RHEOLATE PHX 7025 performs excellently in terms of blocking resistance. Most of the tested liquid market reference products resulted in less block-resistant paints.
Additionally, combinations of PHX 7025 with other NiSAT grades are perfectly possible in order to create tailor-made rheological characteristics. From the powder NiSAT side it makes the most sense to combine with powdered FX 1100.
Figure 9 displays the results of the effect of RHEOLATE PHX 7025 on a styrene acrylic wall paint formulation equipped with a fixed loading of FX 1100. It can be seen, that with increasing loading of the Newtonian PHX 7025 in the thickener package, levelling and hiding power are optimized.
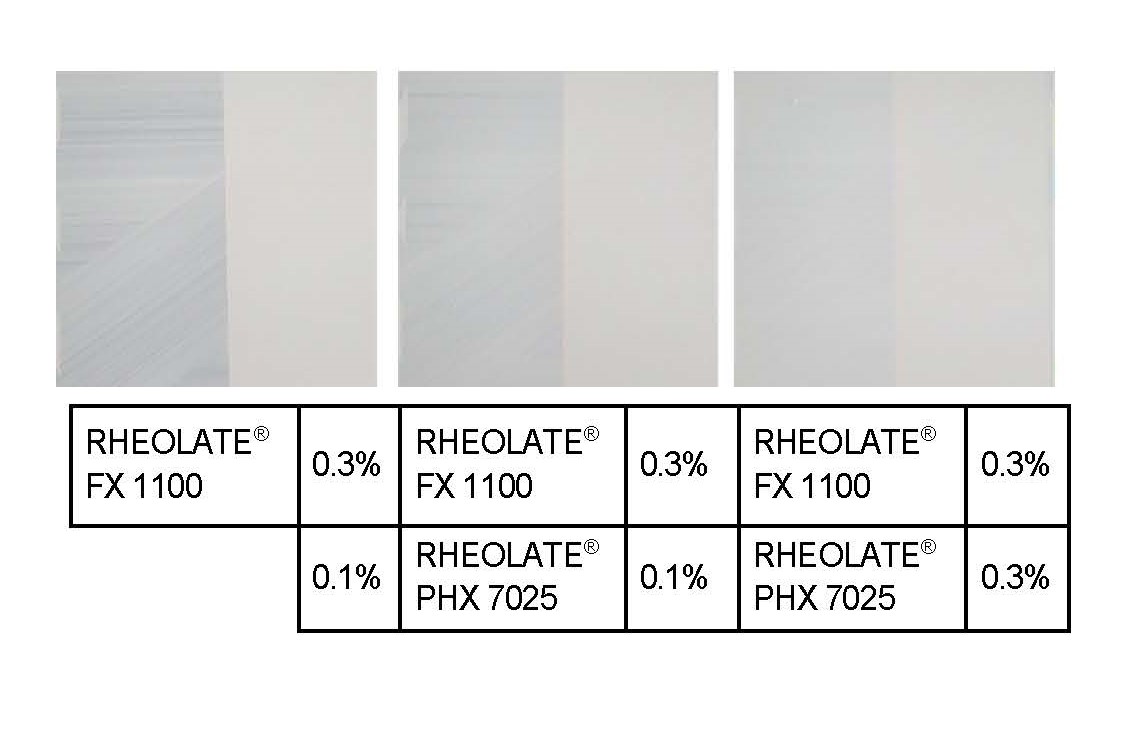
Conclusion
The powdered RHEOLATE NiSAT grades are ideal products for manufacturing sustainable paints and coatings. In terms of sustainability, powder NiSAT grades realize up to 80% CO2 reduction on transportation, and require up to six times less storage space. Powdered NiSAT's are also free from biocides and are therefore ideal products in the manufacture of anti-asthma and anti-allergy paints.
These products also add performance. Powder NiSAT grades realize higher effectivity, improved rheology, and extra dry film properties.
For more information, visit www.elementis.com.
Appendix
Test Methods
Rheology Data
Determined using the Anton-Paar MCR 302 rheometer, equipped with CP 25 measuring geometry at a gap width of 1 mm, at a temperature of 23 °C.
KU Viscosity
KU describes the Krebs-Stormer viscosity. Typically the mid-shear or appearing in-can viscosity is represented.
Brush-Out Levelling
Brush-out leveling was tested by brushing out 40 g of paint equally on a leneta chart (Measuring range: 0 = poor/5 = excellent). The higher the number, the better the performance.
Blocking Resistance
Test paint was blade applied on Leneta charts at a thickness of 250 µm and dried for 48 hours. Afterwards, the test panels were cut in pieces (5 cm x 8 cm) and placed with the coated side on top of each other. The specimen was stored for 3 hours at an elevated temperature of 50 °C with a 5 kg weight on top. After a 15-minute cool down, the panels were separated by hand and the blocking resistance judged visually.
Color Acceptance
Tested after tinting the PU-alkyd-based test paint with 1% colorant (Chroma Chem black 7 WAB Incorporation by 10-minute scandex shaker. Applied on Leneta charts by blade at a thickness of 150 µm. After 2 minutes, the rub-out test was performed. Delta E was determined by Datacolor Microflash 100.
Test Formulation
Aqueous, PU-alkyd-based test paint (Table 3).
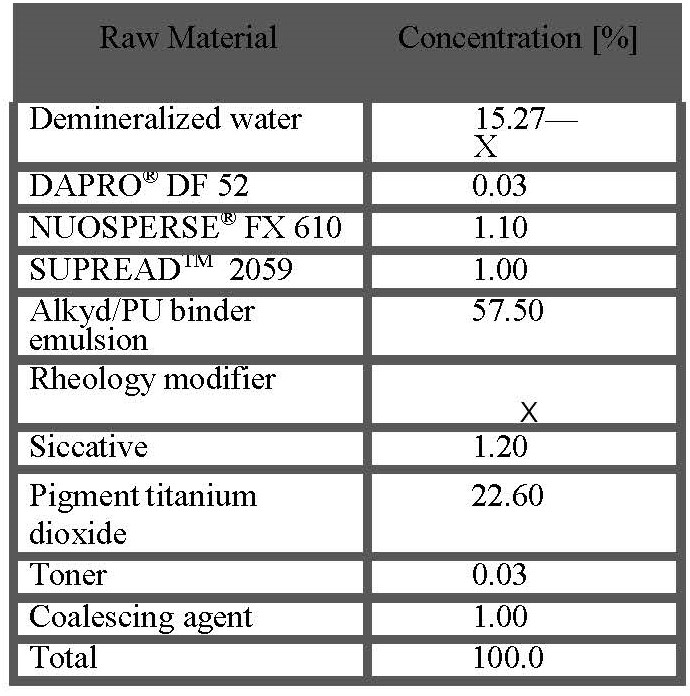
Looking for a reprint of this article?
From high-res PDFs to custom plaques, order your copy today!