New Understanding of Oobleck-Like Fluids Contributes to Smart Material Design

rajatk, Creatas Video+ / Getty Images Plus, via Getty Images
If you mix cornstarch and water in the right proportions, you get something that seems not-quite liquid but also not-quite solid. Oobleck flows and settles like a liquid when untouched, but stiffens when you try to pick it up or stir it with a spoon. The properties of oobleck and other non-Newtonian fluids, including silly putty, quicksand, paint, and yogurt, change under stress or pressure, and scientists have long struggled to prove exactly why.
Now, researchers in the University of Chicago’s Physical Sciences Division (PSD) and Pritzker School of Molecular Engineering (PME) have used piezoelectric nanoparticles, which themselves change in response to pressure, to investigate the fundamental physics of non-Newtonian fluids. The team discovered a key role for friction between particles in causing the materials to flip from a fluid to a more solid structure.
“This not only answers long-standing basic questions about the physical origins of these materials, but opens up doors for the design of new non-Newtonian fluids with practical applications,” said Stuart Rowan, the Barry L. MacLean Professor of Molecular Engineering in PME and the Chemistry Department, and co-senior author of the paper, published in Proceedings of the National Academy of Sciences.
Among those potential applications: paint that doesn’t clump, liquids that harden into a mold when shaken, and wearable protective gear that stiffens when hit.
Piezoelectric Probes
A hallmark of non-Newtonian fluids is that their viscosity (how thick they are) changes dramatically when the materials are under stress. For some materials, this means thinning with stress. Shaking a ketchup bottle can make the condiment drastically more pourable; yogurt, mayonnaise, and toothpaste maintain their shape in a container yet become more liquid-like upon use.
But other materials like oobleck, which is a concentrated particle suspension, behave just the opposite: it can feel solid while being manipulated yet collapse into a puddle when placed down.
Scientists have formulated hypotheses about why concentrated particle suspensions change when sheared, being exposed to multiple forces acting in different directions. These hypotheses mostly relate to how the molecules and particles that make up the materials can interact with each other in different ways under different conditions, but each hypothesis is hard to prove.
“To understand these concentrated particle suspensions, we want to be able to look at the nanoscale structure, but the particles are so incredibly crowded together that imaging these structures is very hard,” explained post-doctoral scholar Hojin Kim, the first author of the new paper.
To overcome this challenge, Kim collaborated with Rowan, Aaron Esser-Kahn, also a Professor in the PME and an expert in piezochemistry, and Heinrich Jaeger, the Sewell Avery Distinguished Service Professor of Physics and the James Franck Institute. The team developed a technique that measures the change in electrical conductance based on the shear force exerted upon it. Then, they suspended the nanoparticle in a liquid at such a concentration that it exhibited non-Newtonian properties in the same way as oobleck.
The researchers applied shear force to the top and bottom of the liquid and simultaneously measured the resulting changes to both viscosity and the electrical signals. That let them determine how the particles were interacting as they changed from a more liquid to more solid-like material.
“We found that friction between particles was critical to this transition,” said Kim. “In this concentrated particle solution, there is a tipping point when the friction reaches a certain level and the viscosity abruptly increases.”
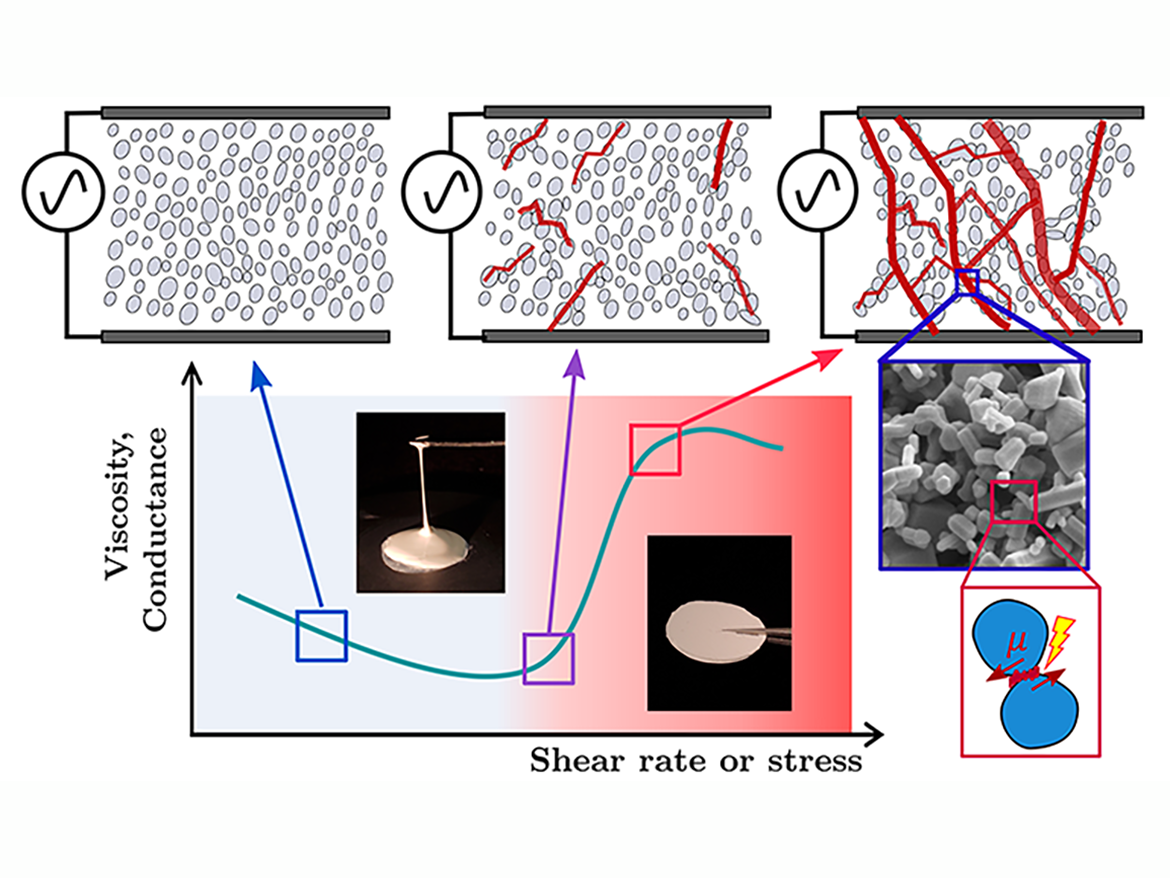
A Range of Applications
Understanding the physical forces at play in a concentrated particle solution is one step toward being able to design new non-Newtonian fluids in the lab. One day, these engineered materials could have customized properties that let scientists control their viscosity through stress. In some instances, this could translate to less clumping and clogging of liquids like paint and concrete. In other cases, it might mean a purposeful hardening of materials when desired.
“For any application, we hope we can eventually determine the ideal combination of solvents and particles and shear conditions to get the properties we want,” said Kim. “This paper might seem like very fundamental research but in reality, non-Newtonian fluids are everywhere and so this has a lot of applications.”
For now, the Pritzker Molecular Engineering and Physical Sciences Division researchers are planning to take advantage of the stress-induced piezoelectric activity of their nanoparticle suspensions to design new adaptive and responsive materials that, for example, become stiffer under mechanical force.
This article was also featured in University of Chicago’s Physical Sciences news on November 28, 2023, and was originally adapted from an article originally published by the Pritzker School of Molecular Engineering.
Looking for a reprint of this article?
From high-res PDFs to custom plaques, order your copy today!