Foam Protects Intumescent Coatings and Paints for Fire Protection

Steel - Unstable Above 500 ºC
Although steel does not burn, it loses its strength when exposed to temperatures above 500 °C. As a result, steel structures become unstable due to the effects of fire, and buildings can collapse completely. The terrorist attacks on the World Trade Center on September 11, 2001, dramatically demonstrated the consequences.
Steel girders can be protected against high temperatures in various ways. Common methods are shielding with concrete and/or thermal insulation panels, spraying with chopped fibers in areas that are not visible, and the use of intumescent coatings. In today's open, light-filled building designs, the latter method is by far the most elegant solution. Only a decorative finish is visible, however, the coating is really a flame-retardant intumescent coating. It protects the steel girder from the effects of heat by swelling and foaming (intumescere
If such a coating satisfies fire-resistance class F 30, for example, it will withstand the flames for 30 minutes. The critical temperature of the substrate is not reached within this fire resistance time, thus giving people in the building time to escape and fire fighters time to fight the fire.
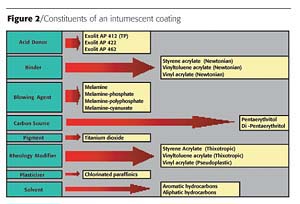
Intumescence - Complex Interaction, Highly Effective
Intumescent coatings consist of various components (Figure 2) whose effectiveness is decisively influenced by the mixing ratios chosen. The critical components are the acid source, the binder, the blowing agent, the carbonific compound and the plasticizer. These substances greatly affect the properties of the coating such as tropical- or water-resistance.The processes that occur (mainly simultaneously) in intumescent coatings during a fire are extremely complex. In the first stage, the acid source liberates polyphosphoric acid that reacts with the carbonific compound to form an ester and water. The latter, and the nitrogen from the decomposing melamine, act as blowing agents to form a foam based on the melting binder. Above 200 °C the foam must be tough enough for the substrate to remain shielded yet sufficiently flexible for the necessary thickness to be achieved. The plasticizer plays an important role in this.
The foam chars during the increasingly high temperatures of the fire but should not collapse. This is prevented, inter alia, by the glassy polyphosphoric acid liberated from the ester compound. Titanium dioxide in the outer layers forms a titanium phosphate framework that supports the foam in the final stages when the carbon has been pyrolyzed at higher temperatures. After the fire, the foam is white because of the titanium phosphate content. It is extremely important for the foam to be free of cracks to ensure complete coverage and shielding of even the most complex-shaped steel girders and supports.
The mechanism of this complex interaction is still not fully understood. The successful development of new flame-retardant systems with extended fire-resistance times thus depends largely on the experience and skill of the development chemist. The latest commercial flame-retardant systems for steel girders offer fire-resistance times in excess of 90 minutes. The quality of the basic products and the expertise of the raw material manufacturers play a significant role (e.g. Exolit AP 422, Clariant). In fire-resistance tests, panels reach the critical temperature of 500 °C only after approximately 100 minutes when these flame-retardant formulations are used (Figure 3).
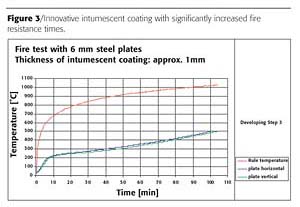
Environmentally Friendly Coatings
As in the decorative paints sector, there is a trend in intumescent coatings towards environmentally friendly, solvent-free systems. The necessary binder systems are, of course, not optimized for temperatures above 200 °C. Developers of flameproof coatings must identify the most suitable from the numerous products available. Reactive solventborne, flameproof coatings achieve up to 120 minutes fire resistance depending on the test method; waterborne systems, however, only achieve up to 90 minutes depending on the test method. The latter also exhibit disadvantages when used in damp environments. Waterborne coatings are thus currently the subject of intensive R&D efforts to improve their performance. This is particularly time-consuming since reproducible results can only be obtained if the coatings are completely dry on the test panels.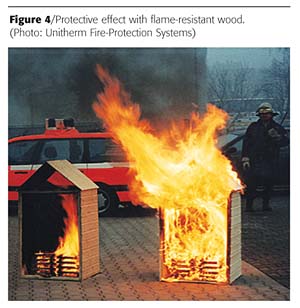
Wood - Ideal But Combustible Construction Material
The traditional construction material, wood, suffers from the disadvantage that it is a good fuel. Apart from chipboard, where flame retardants can be incorporated during manufacture, protective coatings must be used. Since wood, in contrast to steel, starts to burn at temperatures of 300 °C, coatings for this material must be effective at considerably lower temperatures.
At the same time, the coating should affect the appearance as little as possible. A clearcoat that can protect the wood from fire would be ideal. Currently available products are, unfortunately, all slightly opaque. Flame-retardant, multi-coat systems are only available as two-pack coatings that require a high level of expertise when applying. Besides the requirement for good appearance, the coating must exhibit high resistance to mechanical stresses and moisture. Nevertheless, the protection achieved is impressive, as shown in Figure 4.

Cable Protection - Self-Extinguishing and Function-Retaining
Large amounts of cable are required in buildings with extensive technical services such as power stations, industrial buildings, hospitals or offices. These cables are inherently of low flammability so that ignition is delayed. In a fire, however, they contribute significantly to the fire load and may transmit fires to other parts of the building. Particular attention is thus paid to the sealing of cableways for the purposes of fire protection. Coatings can also make an important flame-retardant contribution. Their composition resembles that of steel fire coatings but they are more flexible and do not foam up quite as strongly. They not only prevent the cable from continuing to burn but also enable it to remain functioning. Intumescent coatings are also used in wall seals for cableways. The seals must ensure, inter alia, that smoke does not penetrate other rooms.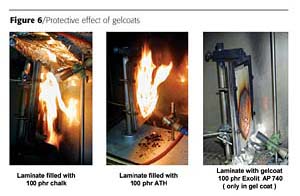
Flame-Retardant Treatment for Textiles - Handy and Wash-Resistant
Textiles are impregnated, excess solution removed, and dried rather than coated in the conventional sense. The coatings should not impair the properties of the textile. They must be invisible, and the "handle" of the material must be retained. The problem of subsequently applied flame retardants is wash resistance; binder/flame retardant combinations do not usually possess this property. Wash-resistant polyester materials are obtained only with the so-called thermofixation process in which the flame retardant diffuses into the fiber at elevated temperatures. The free choice of textile followed by the application of the flame-retardant coating are advantages of this process. Intrinsically flame-retardant textiles, such as Trevira CS, demand an extensive design portfolio based on these special fibers. However, the outstanding properties of intrinsic flame-retarded fibers cannot be achieved by thermofixation.
Unlike the coatings described above, textile coatings based on halogen-free products do not foam up, although the flame retardancy still takes place via a solid state mechanism. They consist mainly of organophosphates combined with nitrogen compounds. The impregnation formulations are generally liquid; for coatings formulations powders suspended in the binder are also used. Typical applications of textile flame-retardant treatments and coatings are shown in Table 1.
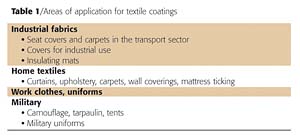
Lightweight, High-Strength Components With Gelcoats
Components based on glass fiber-reinforced unsaturated polyester (UP) or epoxy (EP) gelcoats (so-called composites) are used increasingly in the vehicle construction sector. These components must satisfy high safety standards applicable in all areas of transportation. Smoke density and freedom from corrosion play an important role. Halogen-free flame retardants can meet these requirements.Aluminum trihydrate (ATH) is widely used since it is an inexpensive filler and also meets the above requirements. However, its effectiveness is low so that up to 250 phr (parts per hundred parts resin) are necessary. This results not only in high specific weights but also limits the amount of glass fiber that impairs the mechanical properties of the component. Lightweight, high-strength components are required, particularly in transportation.
The solids content can be reduced by up to 70% by using a combination of ATH with Exolit AP 422, Exolit RP or phosphate-nitrogen combinations such as Exolit AP 740. This is, however, insufficient for some processing methods involving high glass fiber levels. Protective gelcoats can be used in such cases. In the resin-processing industry, gelcoats are generally decorative topcoats, which are the first thing to be introduced into the mold, rather than applied subsequently (Figure 5).
The gelcoat is thus an intrinsic part of the composite part. Its function resembles that of intumescent coatings, foaming up when exposed to heat and shielding the underlying resin layers. Because of the binder resin, the foam is comparatively dense and hard, resulting in a lower foam factor, generally "only" around 1:10. This is generally satisfactory for the fire rating required.
The impressive difference in fire protection is shown in the sequence of illustrations in Figure 6. The left-hand photo shows a test panel in a screening fire test with only chalk as a filler. It does not achieve any classification. The center photo shows a test panel with 100 phr ATH, which also does not achieve classification S4 SR2 ST2 to DIN 5510 Part 2. The right-hand photo shows a panel with a gelcoat based on 100 phr Exolit AP 740. This panel achieves classification S4 SR2 ST2 to DIN 5510 Part 2.
Measurements confirm that a gelcoat-protected part undergoes a considerably smaller increase in temperature over time than an unprotected specimen.
The use of protective gelcoats gives considerably more degrees of freedom in the composite and generally permits lighter parts with higher levels of reinforcement and, hence, improved mechanical properties. More elegant part design is an additional benefit, which opens the way to more sophisticated structures.
Intumescence - a Versatile Solution
The examples shown illustrate the versatility of intumescent coatings. They provide highly effective fire protection of the most diverse materials - from steel to plastics. At the same time, they permit light, elegant and sophisticated structures with these important construction materials. Non-toxic and environmentally friendly, they meet all the requirements of modern flameproofing.For more information, contact ruediger.walz@clariant.com, phone +49 6196 757 8109; or volker.thewes@clariant.com, phone +49 2233 486859.
Looking for a reprint of this article?
From high-res PDFs to custom plaques, order your copy today!