New Radiation-Curable Polyester Acrylate Oligomers

Polyester acrylate oligomers have gained wide acceptance within the coatings industry and are used where superior physical properties are required. They offer enhanced performance when compared to epoxy acrylate oligomers and are cost-effective alternatives to urethane acrylates if a high degree of yellowing resistance is not essential. This paper examines the performance properties of several unique polyester-based oligomers, comparing and contrasting each to commonly used urethane and epoxy acrylates in terms of abrasion resistance, physical properties and ease of handling. Adhesion characteristics on a wood substrate (maple) are also reported.
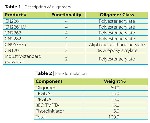
Polyester acrylate oligomers are becoming the material of choice when high performance and sound economics are important, as they are with most UV/EB industrial applications. While urethane oligomers offer a greater degree of yellowing resistance in most cases, the raw material cost may be prohibitive or unwarranted if the end product will not be exposed to harsh outdoor exposure. Epoxy acrylate oligomers, while lower in cost, may not provide the durability and quality of performance needed for many applications. Polyester oligomers can bridge the gap in cost without sacrificing critical end-use properties. In fact, they offer an added benefit of better ease of handling, as most polyesters are lower in viscosity than either a urethane or an epoxy acrylate without monomeric diluents. This allows for more contribution of physical properties from the oligomer and makes formulation changes more predictable.
The new polyester acrylate oligomers being investigated exhibit superior abrasion resistance properties. One, in fact, is low enough in viscosity to make it suitable for spray or vacuum coating application and has been shown to have a zero Primary Irritation Index (PII). For comparison purposes, a polyester oligomer considered by many to be the "industry standard" for wood coating applications has also been added to this study, along with two other basic oligomers of differing backbone structure. One is an epoxy diacrylate and the other is a urethane diacrylate. The control oligomers will be referred to as industry-standard polyester, epoxy and urethane. This study consists of an analysis of several physical properties of the oligomers, most of which are based on cured films made from the oligomers formulated with monomers and photoinitiator. Some experiments are on the neat, uncured oligomer. Table 1 offers a listing of the oligomers to be tested along with a brief description of backbone type and functionality.
Formulations Tested
The base formulation used in this study is shown in Table 2. A "master batch" of the monomer components and photoinitiator was made for each oligomer tested. The monomers selected for this study consist of tripropylene glycol diacrylate (TPGDA), dipropylene glycol diacrylate (DPGDA) and 3-mole ethoxylated trimethylolpropane triacrylate (3EO TMPTA). TPGDA was selected as a low-volatility and low-viscosity monomer that is commonly used for cost reasons in free radical polymerization. DPGDA is also an economical reactive monomer that can replace hexanediol diacrylate (HDDA). It has good viscosity-reducing properties and is more user friendly, having a PPI of 2 compared to 5 for HDDA. Ethoxylated TMPTA was also selected for its low skin irritancy, but offers the added benefits of higher crosslinking and enhanced surface cure. The photoinitiator used for these formulations is a polymeric alpha-hydroxyl phenyl ketone blended with 2-hydroxy-2-methyl-1-phenyl-1-propanone. The oligomer type was varied, but the level was held constant in the base formulation.
Application and Cure Conditions
Each formulation containing a different oligomer variation was applied to chromate-treated aluminum test panel, using a number 40 wire wound rod to yield a film thickness of 4.0 mils. The coated panel was then cured at a line speed of 50 fpm on a standard conveyor system equipped with two 300 w/in medium-pressure mercury vapor lamps. These conditions were selected, as they are commonly used to cure sealers and topcoats on wood. The measured integrated energy was 250 mJ/sq. cm using an Illuminations Industry IL390 radiometer. All panels were prepared in this fashion and conditioned for 24 hours in a controlled temperature and humidity area before testing. These conditions were used for all scratch and abrasion testing unless otherwise specified.
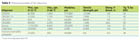
Viscosity of the "neat" oligomers was measured using a Brookfield RTV viscometer at 25 °C and 60 °C. The spindle used was different for each oligomer because the viscosities varied. The appropriate spindle was selected to maintain a mid-range reading on the dial indicator. It is worthy to note that CN2262 has a viscosity of 420 cps at room temperature without the addition of monomers. This property makes this oligomer quite useful for spray or vacuum coating applications. CN2262 has an added benefit of low skin irritancy, having a PII value of zero.
The glass transition temperature (Tg) was determined using Differential Scanning Calorimetry (DSC), with temperatures ramped from -100 °C to 250 °C at a rate of 20 °C per minute. The Tg is defined as the thermal point at which the polymer transitions from a glassy state to a rubbery state. Although not the complete answer, the Tg can sometimes be used to relate hardness. The higher the Tg, the harder the polymer.
For a more complete understanding of film strength properties the tensile pull test was also conducted. This is done by stretching one-half inch wide by four-inch long strips of the polymer on an Instron, Model 5543. The film thickness of each strip was approximately 5.0 mils. Tensile strength at break and Young's modulus were measured, as well as flexibility quantified by the maximum percent of elongation at break. Twenty samples of each coating were tested to ensure accurate results. The results of the aforementioned tests are related in Table 3.
As indicated by the tensile and modulus properties, the epoxy and urethane acrylates are the strongest and hardest. They also have the highest glass transition temperatures of the oligomers tested. However, subsequent abrasion testing has shown that it is important for the oligomers to have a balance of toughness and flexibility for the cured film to have the required resiliency to exhibit the desired abrasion resistant properties.
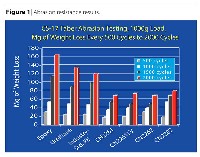
The bulk of the testing conducted in this study concentrated on abrasion resistant properties. Using a Taber abrader, weight loss of the cured coating was performed every 500 cycles through 2000 cycles with CS-17 abrasive wheels, with 1000 grams total weight. The formulations were applied onto chromate-pretreated aluminum panels and were cured using two 300 watt per inch medium-pressure mercury vapor lamps using one pass at 50 fpm. The panels were then cut into a size appropriate for the Taber machine. By weighing the panels before beginning, and after every 500 cycles, the weight loss due to abrasion can be calculated. The test panels were cleaned with a cloth before being weighed each time to ensure that all foreign matter was removed. Three panels were tested for each formulation, and the average of the panels is reported as the final result in Figure 1.
Each vertical bar on the graph represents the cumulative weight loss every 500 cycles to 2000 cycles for a given oligomer. The greater the weight loss, the poorer the abrasion resistance. When comparing the abrasion resistance of the three chemistry types of oligomers, the urethane is better than the epoxy, and the polyester outperforms the urethane. All of the new polyester oligomers are far better than the material identified as the "Industry Standard".
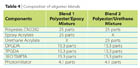
When examining the three oligomer families from a cost/performance standpoint, epoxy acrylates, although low in cost, may become too brittle and will yellow with time. Aliphatic urethane acrylates are typically used when optimum performance is essential to the final application. These oligomers exhibit superior yellowing resistance and enhanced scratch and abrasion properties, especially when compared to an epoxy. However, they are quite a bit more expensive. The polyester acrylate chemistry tends to fall in the middle of these two cost extremes. It can be added to an epoxy-based formulation to improve the performance without having a significant impact on cost, or it can be blended with a urethane-type formulation to reduce cost while maintaining physical properties, such as scratch and abrasion resistance.
Two formulated oligomer blends were made. In one case the polyester acrylate oligomer was blended with an epoxy and in another example the polyester oligomer was added to a urethane-based composition. Table 4 relates the components used in Blends 1 and 2.
The formulated oligomer blends (1 and 2), along with the formulations containing an epoxy, urethane or polyester acrylate, were applied and cured. Again CS-17 Taber testing was conducted using the method described in the previous section. Weight loss for each sample was measured every 500 cycles and the cumulative results were calculated. The results are reported in Figure 2.
When the data is examined, the poor performance results are replicated for the epoxy system. An improvement is demonstrated when the epoxy and polyester acrylate oligomers are tested in a blend. Based on weight loss measurements, the overall wear properties are improved by about 27% without significantly increasing the cost.
The results are even more impressive when the polyester acrylate oligomer is added to the urethane-based formulation. The total cost of the formulation can be reduced, while the abrasion-resistant properties are improved by about 27%.
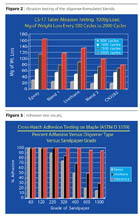
Adhesion of the coating to the substrate is another important criterion. If the coating will not adhere, then abrasion resistance is of little importance. One of the major market segments for these oligomers is coatings for wood flooring, cabinets and furniture. Maple was selected for adhesion testing, as it is one of the more difficult types of wood to adhere to. Adhesion relates to hardness, density and cell structure of the wood. Generally speaking, the higher the density of the wood, the more difficult the adhesion. Balsa wood is quite soft with a large cellulose structure. Thus, the density is relatively low at 170 kg/cubic meter, making the adhesion very easy. Pine is somewhat higher in density, ranging between 360-560 kg/cubic meter depending on the type of pine. But it is still relatively soft and porous, so good adhesion can still be realized without much difficulty. Maple, in contrast, is one of the hardest woods available and has a very small cell structure. Typical densities range to 755 kg/cubic meter, making it almost 4.5 times denser than balsa and 1.5 -2 times harder than pine, depending on the grade. Due to the adhesion challenge, maple was selected as the substrate for adhesion testing.
Another important point influencing the appearance of the coating is the preparation of the wood prior to coating application. Generally, wood is sanded before coating to impart a smooth finished texture. This can also influence adhesion, if finer sandpaper is used as opposed to a coarse one. The finer the sandpaper, the smoother the surface, the more difficult the adhesion becomes.
Grades of sandpaper used in the study ranged from 60 (very coarse) up to 1500 (extremely fine). Before coating, the surface of the maple was sanded using the different grades of sandpaper. Approximately 1.0 mil of coating was applied then cured using two 300 watt/in. medium-pressure mercury lamps at a line speed of 50 fpm. The adhesion was evaluated using cross-hatch adhesion (ASTM D 3359) as a function of coating type and grade of sandpaper used.
The results of the adhesion testing are related in Figure 3. When the different oligomer types are compared, the urethane acrylates adhere better than the epoxy acrylate, with the polyester acrylate oligomers having the best overall adhesion properties. With both the urethane and epoxy, as long as the surface of the wood is very coarse, adhesion is good. However, as the surface becomes smoother, adhesion loss is noted until the adhesion is very poor. The polyester oligomer adhesion is quite good regardless of the surface condition. CN2261LV typifies the adhesion performance of all of the new polyester oligomers tested.
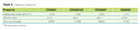
For informational purposes the refractive index, color and density of each oligomer was measured. This data is reported in Table 5.
Refractive index (RI) and color of the oligomer are important properties when making raw material selection for any formulation or application. Generally speaking, the higher the RI the higher the surface gloss. These values are considered relatively high and would equate to high surface reflectance.
Color is also important, especially when coating over a pigmented substrate or basecoat. If the APHA value is high, it may result in an unwanted color change. The values reported here are considered quite low and would have no negative impact.
Conclusion/Observations
The main advantage of these new polyesters is their abrasion resistance and adhesion characteristics. This aspect is apparent in all of the new polyesters, outperforming the "industry-standard polyester" in every case.
When comparing the polyesters to epoxies, the viscosity is significantly lower, allowing for greater formulation latitude, improved yellowing resistance and better flexibility. Being moderately priced, these polyesters can be added to an epoxy-based system to improve the performance properties without severely impacting cost.
In relation to urethanes these new oligomers equal, or somewhat improve, abrasion and adhesion properties. They can be used in situations where weathering resistance is not essential to the final application, while lowering the cost of the final formulation.
Benefits specific to this family of polyesters include:
- excellent adhesion to a wide range of substrates;
- high refractive index, resulting in high gloss;
- low APHA color, minimizing color change when used over inks or pigmented basecoats; and
- wide viscosity range available, enabling the viscosity of the oligomer to be tailored for a given application or formulation.
This paper was presented at RadTech's biennial e|5: UV & EB Technology Expo & Conference, April 2006, Chicago, IL.
For more information, visit www.sartomer.com.
Looking for a reprint of this article?
From high-res PDFs to custom plaques, order your copy today!