Alkylphenol Ethoxylate Alternatives for Coatings Applications

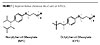
In 2006, sales of APEOs in the coatings market consisted of 22,700 metric tons octylphenol (OPEs) and 17,700 metric tons nonylphenol (NPEs) ethoxylates. These amounts were used both directly in coatings formulations and for emulsion polymerization.(2) These particular ethoxylates were preferred as wetting agents because they provided cost effectiveness while maintaining adaptable properties for many coating and non-coating applications. An example structure of each APEO is given in Figure 1.
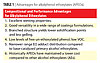
Recent Trends for Substitution of APEOs
Despite all of the aforementioned advantages for APEOs, their use in North America has started to decline. The trend, which has been dramatic over the past two years for household detergent applications, is now moving to many industrial applications. Various initiatives have led coatings manufacturers to seek out APEO alternatives.(3-6) Traditional APEO alternatives such as linear alcohol ethoxylates, secondary ethoxylates, OXO alcohol ethoxylates, etc. have been filling in the gap, but in many cases these do not have the same versatility over a wide range of applications including coating formulation and emulsion polymerization.(7)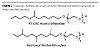
Newer APEO Alternatives
In prior work, alternatives to APEOs were evaluated for use in emulsion polymerization. Research results suggested alcohol ethoxylates derived from newer hydrophobes better match the properties of octylphenol and nonylphenol. These include isotridecyl alcohol (TDA) based on n-butene feedstock and Fischer-Tropsch (“FT”) process-based alcohols (FT-OXO) with carbon range of 12 to 13 (see Figure 2).(7)Additionally, the aforementioned work also indicated narrow range ethoxylation of these alcohols to be important in better matching the properties presented by the APEOs. The narrow range ethoxylation catalyst produced high-mole ethoxylates with an even narrower distribution than those presented by the APEOs,(8-9) which was already significantly narrower in ethoxylate distribution than traditionally catalyzed ethoxylates. When coupled with newer hydrophobes, the emulsion polymerization using these narrow-range (NR) nonionic surfactants proved to be synergistic and resulted in equal or better performance than NPE or the standard OPE.(7)
Applying Previous Knowledge
The previous work, again, centered on emulsion polymerization. Thus, by taking the knowledge from this research involving new hydrophobes and the narrow-range ethoxy-lation technology and applying this to low-mole ethoxy-lates, better APEO alternative wetting agents could be found. The industrial standard for nonionic wetting agents is OPE with 9.5 moles of EO (OPE-9.5). This surfactant, like most APEO, is very versatile in a wide range of coating formulations. Again, the narrow-range ethoxylation catalyst is used to match the peaked ethoxylate distribution of the OPE and the very low unethoxylated material (free alcohol) present in the OPE-9.5. Thus, a narrow range (NR) TDA and FT-OXO ethoxylate will again be evaluated verses the OPE.In order to better demonstrate the performance of the alcohol ethoxylates discussed above as APEO alternative wetting agents, a study was undertaken to employ these alternative ethoxylates as the surfactant in a standard coating formula. The following sections discuss the surfactants evaluated, the coating formulation, analysis methods employed, and the resulting coatings’ properties.
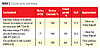
Experimental
Three surfactants were compared in the following study: the industrial standard (an octylphenol ethoxylate with 9.5 moles), a narrow-range n-butene-based isotridecyl alcohol ethoxylate with 9 moles, and a narrow-range FT-OXO alcohol ethoxylate with 7 moles. The properties of each are outlined in Table 2.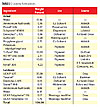
Using the method outlined in DIN EN 1772, the test compares the surfactant concentration needed to wet a small cotton disk in deionized water at 25 seconds. The lower the concentration of the surfactant, the more efficient the wetting performance. The test can also be run at a fixed surfactant concentration, and the wetting time for the cotton disk measured in seconds. Typically, surfactants with lower concentrations for wetting have improved dispersing properties for most pigments in coatings formulations. For reference, a nonylphenol ethoxylate with 9 moles (NPE-9) was also examined.
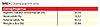
This study employed a standard outdoor trim house paint formulation, which is outlined in Tables 3 and 4. The three surfactants being evaluated were used alternatively as the “surfactant” in the grind portion of the formula. Each coating was prepared using standard practices. That is, the grind portion was sheared until a Hegmann gauge of 7+ particle size was achieved. Then, the letdown materials were added with mixing to generate the final formulated coating.
Coatings Analysis
Each coating was evaluated using the following tests.Freeze-Thaw Resistance (ASTM D 2243)
Each coating was analyzed initially and after three freeze-thaw cycles. The coatings were subjected to viscosity and pH analysis. Then, each was drawn down and allowed to dry for 24 hours. Gloss measurements were taken for every coating at 60° and 85°.
Heat-Age Stability (ASTM D 1849)
The three sample coatings were analyzed for heat storage. The sample was tested initially and after 4 weeks at 50 °C. Changes in viscosity and pH were recorded for each sample along with observations of any settling and the height of syneresis. Next, each coating was drawn down and allowed to dry for 24 hours. The gloss at 60° and 85° was measured for each sample.
Low-Temperature Coalescence (modified ASTM D 3793)
Each coating was drawn down on the unsealed and sealed panel as stated. Then, it was placed into a cold box at the ASTM required 40 °F for 24 hours, and finally, the surface appearance of the coating was visually observed and recorded instead of taking reflectance measurements.
Color Acceptance (ASTM D 4838)
Ten Colortrend® 888 series tint bases were obtained from Evonik® for the color acceptance test.
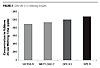
Results and Discussion
Wetting AnalysisIn Figure 3, the concentration of each surfactant to yield a 25 sec wetting time was determined. The concentration of OPE-9.5 is lower than that of NPE-9. However, the NR TDA-9 and the NR FT-OXO-7 require even lower concentrations and thus are more efficient wetting agents based on concentration. There are two possible explanations for this. First, since the NR FT-OXO-7 has only 7 moles of EO, it is actually a lower molecular weight which translates into more molecules present at a given weight percent concentration. The increased number of molecules allows for more interaction with the substrate (the cotton disk) and leads to faster wetting. Second, with NR TDA-9, the increased wetting can be attributed to the compact nature of the hydrophobe.(10) The diverse isomeric hydrophobic structure of the TDA hydrophobe leads to better packing at the interface/micelle and lowers the CMC of the surfactant. This contrasts to the single isomer present in the octylphenol hydrophobe.
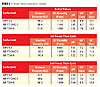
The freeze-thaw testing demonstrated little deviation for initial values both on viscosity and gloss for the OPE-9.5 (see Table 5). Similarly, each alternative surfactant performed equally well under these testing conditions. The variation seen is considered to be within the standard deviation and accuracy of the evaluation method.
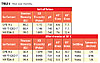
The results of the surfactant long-term stability testing can be seen in Table 6. Each coating exhibited minimum reduction in high-shear viscosity while maintaining Stormer viscosity. Additionally, the syneresis of the wetting agents was comparable; however, the APEO alternatives did display a small decrease in gloss after the four weeks at 50 °C as compared to the OPE-9.5.
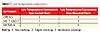
The low-temperature coalescence testing showed the coating with the OPE-9.5 had slight to moderate cracking on the over sealed chart and the unsealed chart, respectively. In contrast, the NR TDA-9 and NR FT-OXO-7 coating outperformed the control by showing no cracking. Thus, under low-temperature conditions the coalescence of the coatings is improved by employing the APEO alternatives.
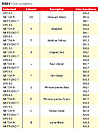
The color studies examined the interaction of the three surfactants with a wide variety of standard colors. The coating using the OPE-9.5 was set as the standard with each color (100.0). Next, the two surfactant alternatives were tested with each color and a value was calculated compared to the OPE-9.5 control. These values are in Table 8. Color acceptance values below 100 suggest the pigment color was less than the OPE control while color acceptance values above 100 indicate the pigment was more intense than the OPE control. The results indict that in all cases the color acceptance for the NR TDA-9 and the NR FT-OXO-7 was equal or better than the OPE-9.5 standard surfactant. Overall, the NR TDA-9 resulted in slightly higher values in most of the color acceptance comparisons.
Conclusions
Over the past 40 years, APEOs have been the surfactant of choice for both emulsion polymerization process and coatings formulation; however, due to various initiatives, APEO alternatives have had to be developed. By exploiting narrow-range ethoxylation and newer alcohol feedstocks, the properties of non-APEO surfactants can better match those of the APEOs. The comparison of APEO standard to the two new non-APEO wetting agents in the paper demonstrated the ability of the new surfactants to generate coatings that perform equal to or better than the APEO industrial standard.This paper was presented at The Waterborne Symposium, sponsored by The University of Southern Mississippi School of Polymers and High Performance Materials and the Southern Society for Coatings Technology, 2009, New Orleans, LA.
Acknowledgements
We would like to acknowledge the University of Southern Mississippi for help in evaluating the surfactants.Looking for a reprint of this article?
From high-res PDFs to custom plaques, order your copy today!