A Closed-Loop Recycling Program for Purge Solvents
In today’s environmentally conscious society, all finishing operations are searching for ways to minimize their environmental impact while also reducing their costs. One solution that achieves both goals is a closed-loop recycling program pioneered by Gage Products Co., headquartered in Ferndale, MI. The program allows solvents to be reclaimed and reused instead of wasted, thereby allowing more efficient use of natural and company resources.
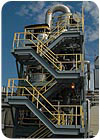
Purge solvents are used to clear paint lines between color blocks in automotive finishing operations. However, once the solvents have been flushed through the paint system, they must be disposed of as hazardous waste according to government regulations. For some plants, these used solvents account for 50 to 70% or more of their hazardous waste stream. The solvents also create air emissions, forcing some facilities to limit production or purchase control equipment to remain compliant with increasingly stringent emission rules.
Solvent formulations containing reduced volatile organic compounds (VOCs) and hazardous air pollutants (HAPs) have been developed to reduce air emissions, but the used solvent in most cases is still considered a hazardous waste. In today’s environmentally conscious society, all finishing operations are searching for ways to minimize their environmental impact while also reducing their costs.
One solution that achieves both goals is a closed-loop recycling program pioneered by Gage Products Co., headquartered in Ferndale, MI. The program allows solvents to be reclaimed and reused instead of wasted, thereby allowing more efficient use of natural and company resources.
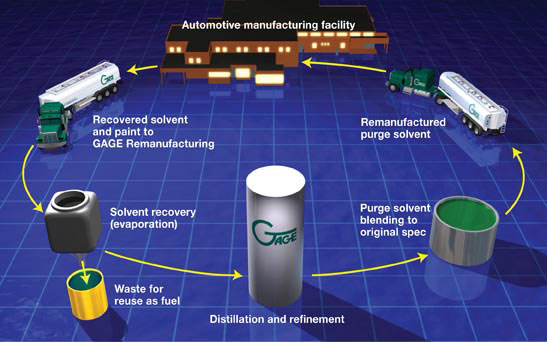
The spent purge solvent is monitored closely for solids levels, as well as other contaminants like water, and is then sent to Gage’s facility for remanufacturing. On average, 70% of the captured solvents are returned to the auto manufacturer for future purge operations. Collection systems are evaluated and improved if necessary to provide the highest possible capture rate, while eliminating potential cross contamination or dumping of incompatible wastes. By fully understanding a manufacturer’s waste stream, Gage can provide feedback and technical assistance to optimize the entire coating process.
The second phase of the program involves the use of appropriate cleanup materials and processes to ensure a clean spray booth and painting environment without the excessive use of cleaning solvents containing VOCs. Depending on the manufacturer’s needs, Gage will recommend water-based, low- or no-VOC or HAPs paint shop cleaning products and protective coatings. In many instances, the use of these coatings and cleaners allows companies to reduce air emissions, avoid compliance issues or increase production based on the reduction of cleanup air emissions.
The closed-loop recycling program has been implemented by Ford Motor Co., DaimlerChrysler, General Motors and other major vehicle manufacturers. Gage supplies a variety of purge solvents to meet the specifications established by each vehicle manufacturer and its paint supplier. The purge solvent is shipped to the vehicle manufacturer’s assembly plant, and Gage’s on-site personnel manage product usage at the plant. When the purge solvent has been used, the on-site Gage personnel assist the vehicle manufacturer in returning the spent material to Gage’s facility for remanufacturing.
The process exemplifies sustainable product stewardship from “cradle-to-cradle,” with an emphasis on managing materials, not wastes.
When recovered purge solvents arrive at Gage’s facility, the paint solids are removed using thin film evaporation. The recovered solvents are then separated into the original constituents using fractional distillation, and any water or liquid impurities are removed. The remaining high-purity materials are blended back into purge solvents and returned to the auto manufacturer. A state-of-the-art on-site laboratory ensures that quality specifications are met for both inbound and outbound materials. The purified solvent is equivalent to virgin material and is consistent from batch to batch. The remaining paint byproduct is sold as a fuel used for making cement.
In an era when all manufacturers are searching for ways to become more competitive and more environmentally friendly, a sustainable product stewardship program based on the closed-loop recycling of purge solvents can be a cost-effective solution.
For more information about Gage Products Co., visit www.gageproducts.com.
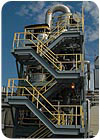
Gage operates and maintains a facility in Ferndale, MI, dedicated to developing, storing, processing and remanufacturing chemical products from used materials.
Purge solvents are used to clear paint lines between color blocks in automotive finishing operations. However, once the solvents have been flushed through the paint system, they must be disposed of as hazardous waste according to government regulations. For some plants, these used solvents account for 50 to 70% or more of their hazardous waste stream. The solvents also create air emissions, forcing some facilities to limit production or purchase control equipment to remain compliant with increasingly stringent emission rules.
Solvent formulations containing reduced volatile organic compounds (VOCs) and hazardous air pollutants (HAPs) have been developed to reduce air emissions, but the used solvent in most cases is still considered a hazardous waste. In today’s environmentally conscious society, all finishing operations are searching for ways to minimize their environmental impact while also reducing their costs.
One solution that achieves both goals is a closed-loop recycling program pioneered by Gage Products Co., headquartered in Ferndale, MI. The program allows solvents to be reclaimed and reused instead of wasted, thereby allowing more efficient use of natural and company resources.
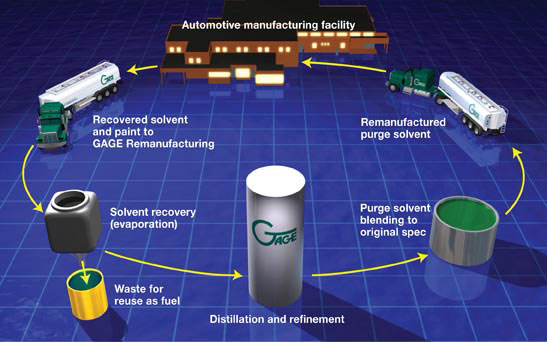
Program Basics
The program is based on a two-pronged approach that addresses both solvent recovery and emissions reductions. Depending on the paint technology, Gage recommends or creates an appropriate purge formulation to minimize material use and timing required to change colors. VOC and HAP compliance is considered, along with permit requirements and the type of application equipment used (automated or manual). The company conducts a purge audit by measuring the exact consumption of solvents and paints during color change cycles, as well as the corresponding programming and timing. By optimizing both the chemistry and purge cycle programming, a more efficient color change becomes possible. The benefits include fewer quality defects such as color carryover, spits and dirt, along with increased throughput through faster line speed or closer job spacing, and a reduction in paint and solvent use through a higher first time through (FTT).The spent purge solvent is monitored closely for solids levels, as well as other contaminants like water, and is then sent to Gage’s facility for remanufacturing. On average, 70% of the captured solvents are returned to the auto manufacturer for future purge operations. Collection systems are evaluated and improved if necessary to provide the highest possible capture rate, while eliminating potential cross contamination or dumping of incompatible wastes. By fully understanding a manufacturer’s waste stream, Gage can provide feedback and technical assistance to optimize the entire coating process.
The second phase of the program involves the use of appropriate cleanup materials and processes to ensure a clean spray booth and painting environment without the excessive use of cleaning solvents containing VOCs. Depending on the manufacturer’s needs, Gage will recommend water-based, low- or no-VOC or HAPs paint shop cleaning products and protective coatings. In many instances, the use of these coatings and cleaners allows companies to reduce air emissions, avoid compliance issues or increase production based on the reduction of cleanup air emissions.
The closed-loop recycling program has been implemented by Ford Motor Co., DaimlerChrysler, General Motors and other major vehicle manufacturers. Gage supplies a variety of purge solvents to meet the specifications established by each vehicle manufacturer and its paint supplier. The purge solvent is shipped to the vehicle manufacturer’s assembly plant, and Gage’s on-site personnel manage product usage at the plant. When the purge solvent has been used, the on-site Gage personnel assist the vehicle manufacturer in returning the spent material to Gage’s facility for remanufacturing.
The process exemplifies sustainable product stewardship from “cradle-to-cradle,” with an emphasis on managing materials, not wastes.
Efficient Recovery
Gage operates and maintains a facility dedicated to developing, storing, processing and remanufacturing chemical products from used materials. The site is located on 11 acres in Ferndale and includes 100 tanks for storage, processing and blending of materials.When recovered purge solvents arrive at Gage’s facility, the paint solids are removed using thin film evaporation. The recovered solvents are then separated into the original constituents using fractional distillation, and any water or liquid impurities are removed. The remaining high-purity materials are blended back into purge solvents and returned to the auto manufacturer. A state-of-the-art on-site laboratory ensures that quality specifications are met for both inbound and outbound materials. The purified solvent is equivalent to virgin material and is consistent from batch to batch. The remaining paint byproduct is sold as a fuel used for making cement.
A Cost-Effective Solution
Finishing operations that have implemented the closed-loop recycling program have substantially reduced both the amount of waste generated and their solvent costs. For example, Ford Motor Co., one of the earliest adopters of the program, has reduced its paint solvent waste by more than 38 million gallons and has saved more than $75 million on solvents since starting the program 23 years ago at a single plant. All of Ford’s assembly plants in the U.S. and Canada use a closed-loop recycling program to recover used paint solvent, along with sludge that’s used as fuel. Numerous other facilities have also reaped substantial cost-saving and waste-reduction benefits through the program.In an era when all manufacturers are searching for ways to become more competitive and more environmentally friendly, a sustainable product stewardship program based on the closed-loop recycling of purge solvents can be a cost-effective solution.
For more information about Gage Products Co., visit www.gageproducts.com.
SIDEBAR: How Much Can You Save with Solvent Recovery?
Determining the bottom line benefits of solvent recovery and reuse for your company depends on several factors, including:- The monthly volume of solvent that you generate
- The approximate composition of the solvent
- The typical solids content range
- The typical water content range
Looking for a reprint of this article?
From high-res PDFs to custom plaques, order your copy today!