Field-Applied Coatings: Thinking in Layers
A 2.2-million-gallon unlined concrete reservoir in southern California, constructed in 1981, was experiencing problems with cracks in the floor and shell, and associated water leakage. Underwater epoxy patches applied to the cracks on the interior of the reservoir did not hold for more than a few years. A high-performance elastomeric urethane lining system, used in conjunction with a concentrated moisture barrier and epoxy primer, was recommended for this project.
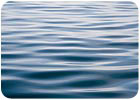
A 2.2-million-gallon unlined concrete reservoir in southern California was constructed in 1981. Over the years, the reservoir developed cracks in the floor and shell. As time went on, the cracks in the shell appeared wet, and water eventually seeped through to the exterior surfaces. Puddles were also observed around the base of the reservoir in numerous locations.
In 1996, underwater epoxy patches were applied to the cracks on the interior of the reservoir. The reservoir water level was monitored, and it was apparent that the leaks had been arrested by the epoxy patch installations.
After a few years, however, the shell leakage began to reappear. Reservoir water level monitoring was reinitiated, and leakage was again verified. KTA-Tator, Inc. was contracted to perform an assessment of the reservoir and to provide recommendations for correcting the leaks.
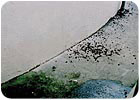
As a result of the investigation, KTA-Tator prepared recommendations that included a structural assessment of the reservoir. It was thought that the leaking water might be undermining the reservoir foundation and possibly contributing to the reservoir cracking. It was also thought that the leakage might have resulted in corrosion of the reinforcing steel embedded in the concrete shell. Fortunately, however, the assessment revealed that the reservoir was structurally sound.
The leakage problem could be corrected by repairing the existing cracks and applying a flexible lining that would expand and contract if and when new cracks formed. The lining needed to be NSF/ANSI 61 approved since the reservoir is used to store potable drinking water. A 100% solids elastomeric urethane was selected to line the reservoir and stop the water leakage.
An elastomeric urethane was ideal for the reservoir lining since 1) it is flexible and has excellent elongation to resist future cracking; 2) the reservoir can be put back into service within 24 hours of application; 3) it can be applied to both the concrete surfaces and the steel surfaces; and 4) it is applied without solvents, so explosion hazards can be avoided in an enclosed reservoir.
Steel surfaces were prepared in accordance with SSPC-SP 10/NACE No. 2, “Near-White Metal Blast Cleaning.” Existing cracks greater than hairline width were prepared by v-grooving and filling with an epoxy fortified cementitious material. The final step in the surface preparation operations was to vacuum all dust and dirt, leaving a thoroughly cleaned surface behind.
At the completion of the surface preparation process, moisture vapor emission testing was performed to determine whether moisture vapor was penetrating through the floor of the reservoir from the ground. Excessive moisture vapor emission could result in blistering of the lining once applied.
Moisture vapor emission tests were performed in accordance with ASTM F1869, “Standard Test Method for Measuring Moisture Vapor Emission Rate of Concrete Subfloor Using Anhydrous Calcium Chloride.” The test involves placing a pre-weighed quantity of hydrophilic calcium chloride on the surface of the concrete at several locations. The calcium chloride is covered with a clear plastic dome and allowed to sit for 72 hours. At the conclusion of the test, the calcium chloride is reweighed, and a moisture vapor emission rate is calculated based on the weight change and test period. Typically, concrete surfaces can be successfully coated if the moisture vapor emission rate is less than 3 lb/24 hr/1000 ft2.
The testing conducted on the concrete floor of the reservoir resulted in readings ranging from approximately 6 lb/24 hr/1000 ft2 to 9 lb/24 hr/1000 ft2. These rates dictated that a moisture vapor barrier would be needed prior to applying the elastomeric urethane system. Careful consideration is required when selecting a moisture barrier since unusually high emission rates (greater than those measured on the reservoir floor) cannot be reduced to levels acceptable for standard coating applications. Additionally, some barriers can inhibit coating adhesion, and the capabilities of the vapor barriers are often exaggerated.
The writer had good experiences in the past with the use of Xypex, which is a concentrated moisture barrier product applied as a slurry to a wetted concrete surface. The wetted surface draws the product down into the concrete. Once in the concrete, it reacts to produce a non-soluble crystalline formation within the pores and capillary tracts. Moisture vapor emission rates are subsequently reduced.
Care was taken to ensure that the barrier was applied at the correct coverage rate. Excessive applications would have resulted in puddling of the product on the surface and may have inhibited the adhesion of the elastomeric urethane.
Once the moisture barrier attained initial hardness, the surfaces were misted with water for a few days and then allowed to cure for a period of 21 days. At the conclusion of the curing period, the surfaces were lightly roughened by abrasive blast cleaning. Retesting of the concrete surfaces resulted in moisture vapor emission rates of approximately 3 lb/24 hr/1000 ft2. The concrete slab was then ready for the application of the elastomeric urethane system.
An epoxy primer was applied to a dry film thickness of 5 mils. The epoxy primer penetrated down into the concrete and promoted bonding. The elastomeric urethane was then applied by plural component airless spray in one coat using a multiple-pass technique to a dry film thickness of 60 to 70 mils on the concrete surfaces and 30 to 40 mils on the prepared steel surfaces. A reinforcing fabric was embedded into the urethane layer at joints in order to provide additional strength should there be any movement.
This innovative approach to repairing and maintaining the concrete reservoir extended the life of the structure and helped the facility owner avoid escalated costs, as well as potential water supply issues during the construction phase.
For more information about protective coatings, visit www.kta.com.
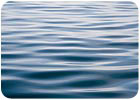
The crack locations in the reservoir floor corresponded to water puddles observed on the exterior of the tank
A 2.2-million-gallon unlined concrete reservoir in southern California was constructed in 1981. Over the years, the reservoir developed cracks in the floor and shell. As time went on, the cracks in the shell appeared wet, and water eventually seeped through to the exterior surfaces. Puddles were also observed around the base of the reservoir in numerous locations.
In 1996, underwater epoxy patches were applied to the cracks on the interior of the reservoir. The reservoir water level was monitored, and it was apparent that the leaks had been arrested by the epoxy patch installations.
After a few years, however, the shell leakage began to reappear. Reservoir water level monitoring was reinitiated, and leakage was again verified. KTA-Tator, Inc. was contracted to perform an assessment of the reservoir and to provide recommendations for correcting the leaks.
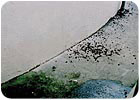
It was determined that the leakage problem could be corrected by repairing the existing cracks and applying a flexible lining that would expand and contract if and when new cracks formed.
Assessing the Damage
An underwater diver trained in coatings assessment techniques conducted the condition assessment. The assessment revealed that the epoxy repairs made in 1996 had blistered in many areas. Wet areas reappeared on the exterior shell at cracks where the patches had been applied earlier. Mild rust staining was observed along the crack repair areas, and additional cracks were observed on the floor. The crack locations in the floor corresponded to water puddles observed on the exterior of the reservoir. The internal steel pipes and appurtenances were coated but exhibited rust-through and minor pitting.As a result of the investigation, KTA-Tator prepared recommendations that included a structural assessment of the reservoir. It was thought that the leaking water might be undermining the reservoir foundation and possibly contributing to the reservoir cracking. It was also thought that the leakage might have resulted in corrosion of the reinforcing steel embedded in the concrete shell. Fortunately, however, the assessment revealed that the reservoir was structurally sound.
The leakage problem could be corrected by repairing the existing cracks and applying a flexible lining that would expand and contract if and when new cracks formed. The lining needed to be NSF/ANSI 61 approved since the reservoir is used to store potable drinking water. A 100% solids elastomeric urethane was selected to line the reservoir and stop the water leakage.
An elastomeric urethane was ideal for the reservoir lining since 1) it is flexible and has excellent elongation to resist future cracking; 2) the reservoir can be put back into service within 24 hours of application; 3) it can be applied to both the concrete surfaces and the steel surfaces; and 4) it is applied without solvents, so explosion hazards can be avoided in an enclosed reservoir.
Increasing Flexibility
The concrete surfaces were roughened by abrasive blast cleaning according to the requirements of SSPC-SP 13/NACE No. 6, “Surface Preparation of Concrete,” and the referenced ASTM D4259, “Standard Practice for Abrading Concrete.” All surfaces were cleaned of contamination, form release agents, efflorescence, curing compounds and existing coatings not known to be compatible with the new elastomeric urethane coating to be installed. Surface defects such as fins, protrusions, bulges and mortar spatter were removed by grinding or scraping. The prepared surface was to have a uniform roughened appearance similar to coarse sandpaper.Steel surfaces were prepared in accordance with SSPC-SP 10/NACE No. 2, “Near-White Metal Blast Cleaning.” Existing cracks greater than hairline width were prepared by v-grooving and filling with an epoxy fortified cementitious material. The final step in the surface preparation operations was to vacuum all dust and dirt, leaving a thoroughly cleaned surface behind.
At the completion of the surface preparation process, moisture vapor emission testing was performed to determine whether moisture vapor was penetrating through the floor of the reservoir from the ground. Excessive moisture vapor emission could result in blistering of the lining once applied.
Moisture vapor emission tests were performed in accordance with ASTM F1869, “Standard Test Method for Measuring Moisture Vapor Emission Rate of Concrete Subfloor Using Anhydrous Calcium Chloride.” The test involves placing a pre-weighed quantity of hydrophilic calcium chloride on the surface of the concrete at several locations. The calcium chloride is covered with a clear plastic dome and allowed to sit for 72 hours. At the conclusion of the test, the calcium chloride is reweighed, and a moisture vapor emission rate is calculated based on the weight change and test period. Typically, concrete surfaces can be successfully coated if the moisture vapor emission rate is less than 3 lb/24 hr/1000 ft2.
The testing conducted on the concrete floor of the reservoir resulted in readings ranging from approximately 6 lb/24 hr/1000 ft2 to 9 lb/24 hr/1000 ft2. These rates dictated that a moisture vapor barrier would be needed prior to applying the elastomeric urethane system. Careful consideration is required when selecting a moisture barrier since unusually high emission rates (greater than those measured on the reservoir floor) cannot be reduced to levels acceptable for standard coating applications. Additionally, some barriers can inhibit coating adhesion, and the capabilities of the vapor barriers are often exaggerated.
The writer had good experiences in the past with the use of Xypex, which is a concentrated moisture barrier product applied as a slurry to a wetted concrete surface. The wetted surface draws the product down into the concrete. Once in the concrete, it reacts to produce a non-soluble crystalline formation within the pores and capillary tracts. Moisture vapor emission rates are subsequently reduced.
Care was taken to ensure that the barrier was applied at the correct coverage rate. Excessive applications would have resulted in puddling of the product on the surface and may have inhibited the adhesion of the elastomeric urethane.
Once the moisture barrier attained initial hardness, the surfaces were misted with water for a few days and then allowed to cure for a period of 21 days. At the conclusion of the curing period, the surfaces were lightly roughened by abrasive blast cleaning. Retesting of the concrete surfaces resulted in moisture vapor emission rates of approximately 3 lb/24 hr/1000 ft2. The concrete slab was then ready for the application of the elastomeric urethane system.
An epoxy primer was applied to a dry film thickness of 5 mils. The epoxy primer penetrated down into the concrete and promoted bonding. The elastomeric urethane was then applied by plural component airless spray in one coat using a multiple-pass technique to a dry film thickness of 60 to 70 mils on the concrete surfaces and 30 to 40 mils on the prepared steel surfaces. A reinforcing fabric was embedded into the urethane layer at joints in order to provide additional strength should there be any movement.
Benefiting from Success
At the completion of the project, reservoir water level monitoring was performed to determine whether the leakage had been arrested. The monitoring data indicated that the leaks had stopped. The one-year anniversary inspection identified no appreciable coating failures or defects, and the reservoir inventory continued to be maintained.This innovative approach to repairing and maintaining the concrete reservoir extended the life of the structure and helped the facility owner avoid escalated costs, as well as potential water supply issues during the construction phase.
For more information about protective coatings, visit www.kta.com.
Looking for a reprint of this article?
From high-res PDFs to custom plaques, order your copy today!