Electrocoat Finishes: How Low Can You Go?
E-coat is widely recognized as one of the most efficient coating processes. However, in today’s ultra-competitive environment, the quest for improved efficiencies is relentless. Recent increases in energy costs, the desire to process more parts through the same system, and concerns for the environment have led to an interest in electrocoat materials with lower cure temperatures. Fortunately, new developments are meeting the market demand for a lower-temperature cure with a high-performance cathodic epoxy electrocoat finish.
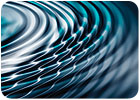
For decades, cathodic epoxy electrocoat primers have been a major tool in preventing the corrosion of metal surfaces. The combination of modern e-coat paint formulations and application equipment provides an efficient, environmentally friendly, cost-effective coating solution for many applications. E-coat is widely recognized as one of the most efficient coating processes. However, in today’s ultra-competitive environment, the quest for improved efficiencies is relentless. Recent increases in energy costs, the desire to process more parts through the same system, and concerns for the environment have led to an interest in electrocoat materials with lower cure temperatures. Fortunately, new developments are meeting the market demand for a lower-temperature cure with a high-performance cathodic epoxy electrocoat finish.
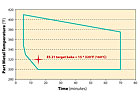
DuPont has developed a new mixed metal oxide catalyst chemistry that allows the alcohol to unblock more efficiently at lower temperatures. This new catalyst system* allows cure temperatures required in typical electrocoat processes to be lowered by 20-40°F while maintaining excellent film properties. The new electrocoat primer expands the lower end operating bake window compared to currently available commercial products. Target bake conditions for the low-cure coating are 15 minutes with the part temperature at 320°F (160°C), and low-end cure temperatures as low as 300°F (150°C) are possible. Figure 1 shows the cure window for the new coating.
The cure response of a coating can be verified by measuring the gel fraction of the polymer system - the percentage of polymer chains that have reacted and are crosslinked to form the coating film. The higher the gel fraction, the better the film is cured. The low-cure cathodic epoxy reaches a >90% gel fraction after 15 minutes at 300°F compared to standard e-coat primers, which reach about 66% gel fraction at that time and temperature. Figure 2 shows gel fraction test results for the new coating and a commonly used control material.
The development of this new e-coat was a global effort. Research chemists and engineers working at laboratories in Wuppertal, Germany, Sao Paulo, Brazil and Mt. Clemens, MI, collaborated on this technology, with the goal of ensuring that this new product would meet the needs of finishing professionals on a worldwide basis. Except for the lower cure temperature, the process operating targets and e-coat bath chemistry operating targets of the new coating are consistent with the existing DuPont cathodic epoxy formulation,** so few or no modifications are required to use the new coating in existing systems. Film properties meet or exceed targeted film properties. The new e-coat is heavy-metal-free, and its volatile organic compound (VOC) content is low, at less than 0.4 lb/gal. Finally, the new coating is “pour-over” capable with all existing cathodic epoxy electrocoat materials.
The new product meets automotive original equipment manufacturer (OEM) specifications, and two automotive OEMs are currently using the coating in North American electrocoat tanks.

The potential for energy savings is obvious. Simple energy consumption models show that lowering oven setpoint temperatures by 30°F (17°C) in a typical e-coat cure oven should yield a reduction in natural gas or electrical energy consumption of about 8%. Exact energy savings will vary depending on many factors, including oven design, part mass and part geometry.
Another advantage of lower-temperature-cure coatings is the potential to increase the mass of parts processed through the e-coat cure oven while using about the same amount of energy. This ability allows the potential for increased rack density or increased line speed. Simple models show that an oven set at 400°F (204°C) with part mass of 100% will consume about the same amount of energy as an oven set at 370°F (188°C) with part mass of 110%. Again, precise oven capacity and energy consumption will vary depending on many factors. Careful consideration should be given to all areas of the e-coat system prior to increasing rack density or increasing line speed.
Finally, lower-cure-temperature coatings can allow parts with heavy metal areas to be processed through a typical system without having to raise the target setpoint of the oven or slow down the line speed. An under-cured e-coat can cause poor corrosion or other key physical property performance on the part. The new low-cure cathodic epoxy e-coat has a broader low end cure window, which can help provide better cure on heavy metal areas of parts that take longer to heat.
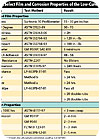
For more information about low-cure cathodic epoxy e-coats and other automotive coatings, visit www.performancecoatings.dupont.com.
*This new product is available from DuPont as ElectroShield™21.
**CorMax® VI.
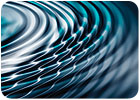
For decades, cathodic epoxy electrocoat primers have been a major tool in preventing the corrosion of metal surfaces. The combination of modern e-coat paint formulations and application equipment provides an efficient, environmentally friendly, cost-effective coating solution for many applications. E-coat is widely recognized as one of the most efficient coating processes. However, in today’s ultra-competitive environment, the quest for improved efficiencies is relentless. Recent increases in energy costs, the desire to process more parts through the same system, and concerns for the environment have led to an interest in electrocoat materials with lower cure temperatures. Fortunately, new developments are meeting the market demand for a lower-temperature cure with a high-performance cathodic epoxy electrocoat finish.
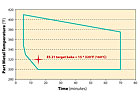
Figure 1. The cure window for the low-cure-temperature cathodic epoxy e-coat.
Coating Development and Performance
The chemistry of cathodic epoxy electrocoat crosslinking involves unblocking or removing alcohol from the isocyanate crosslinker, allowing it to react with functional sites on the backbone resins to form a fully crosslinked film. This unblocking mechanism plays an important factor in determining the temperature required to cure the film. For most commercially available cathodic epoxy electrocoat products used in typically designed processes, part temperatures of 350-400°F (177-204°C) for 10 to 20 minutes are required to cure the film sufficiently.DuPont has developed a new mixed metal oxide catalyst chemistry that allows the alcohol to unblock more efficiently at lower temperatures. This new catalyst system* allows cure temperatures required in typical electrocoat processes to be lowered by 20-40°F while maintaining excellent film properties. The new electrocoat primer expands the lower end operating bake window compared to currently available commercial products. Target bake conditions for the low-cure coating are 15 minutes with the part temperature at 320°F (160°C), and low-end cure temperatures as low as 300°F (150°C) are possible. Figure 1 shows the cure window for the new coating.
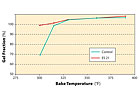
Figure 2. Gel fraction test results for the new e-coat compared to a commonly used control material.
The development of this new e-coat was a global effort. Research chemists and engineers working at laboratories in Wuppertal, Germany, Sao Paulo, Brazil and Mt. Clemens, MI, collaborated on this technology, with the goal of ensuring that this new product would meet the needs of finishing professionals on a worldwide basis. Except for the lower cure temperature, the process operating targets and e-coat bath chemistry operating targets of the new coating are consistent with the existing DuPont cathodic epoxy formulation,** so few or no modifications are required to use the new coating in existing systems. Film properties meet or exceed targeted film properties. The new e-coat is heavy-metal-free, and its volatile organic compound (VOC) content is low, at less than 0.4 lb/gal. Finally, the new coating is “pour-over” capable with all existing cathodic epoxy electrocoat materials.
The new product meets automotive original equipment manufacturer (OEM) specifications, and two automotive OEMs are currently using the coating in North American electrocoat tanks.

Recent increases in energy costs, the desire to process more parts through the same system, and concerns for the environment have led to interest in electrocoat materials with lower cure temperatures. Photo courtesy of Burkard Industries.
Potential Benefits of Lower Cure Electrocoat
Lower-cure-temperature requirements provide several potential advantages to the e-coat finisher, including energy savings, improved process throughput and an improved ability to process parts with heavy metal areas.The potential for energy savings is obvious. Simple energy consumption models show that lowering oven setpoint temperatures by 30°F (17°C) in a typical e-coat cure oven should yield a reduction in natural gas or electrical energy consumption of about 8%. Exact energy savings will vary depending on many factors, including oven design, part mass and part geometry.
Another advantage of lower-temperature-cure coatings is the potential to increase the mass of parts processed through the e-coat cure oven while using about the same amount of energy. This ability allows the potential for increased rack density or increased line speed. Simple models show that an oven set at 400°F (204°C) with part mass of 100% will consume about the same amount of energy as an oven set at 370°F (188°C) with part mass of 110%. Again, precise oven capacity and energy consumption will vary depending on many factors. Careful consideration should be given to all areas of the e-coat system prior to increasing rack density or increasing line speed.
Finally, lower-cure-temperature coatings can allow parts with heavy metal areas to be processed through a typical system without having to raise the target setpoint of the oven or slow down the line speed. An under-cured e-coat can cause poor corrosion or other key physical property performance on the part. The new low-cure cathodic epoxy e-coat has a broader low end cure window, which can help provide better cure on heavy metal areas of parts that take longer to heat.
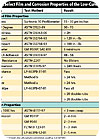
ONLINE EXCLUSIVE: Select Film and Corrosion Properties of the Low-Cure E-Coat
A Technology Advantage
Modern cathodic epoxy electrocoat coating formulations combined with well-designed application processes are widely recognized as one of the most efficient coating systems available. Competition in the electrocoat finishing business is intense. The successful coater must strive for continuous improvement to survive or thrive. Lower-cure-temperature cathodic epoxy paint formulations offer several potential areas for process improvements that can yield significant economic benefits.For more information about low-cure cathodic epoxy e-coats and other automotive coatings, visit www.performancecoatings.dupont.com.
*This new product is available from DuPont as ElectroShield™21.
**CorMax® VI.
Looking for a reprint of this article?
From high-res PDFs to custom plaques, order your copy today!