Improvements to the Coil-Coating Process Continue to Flow
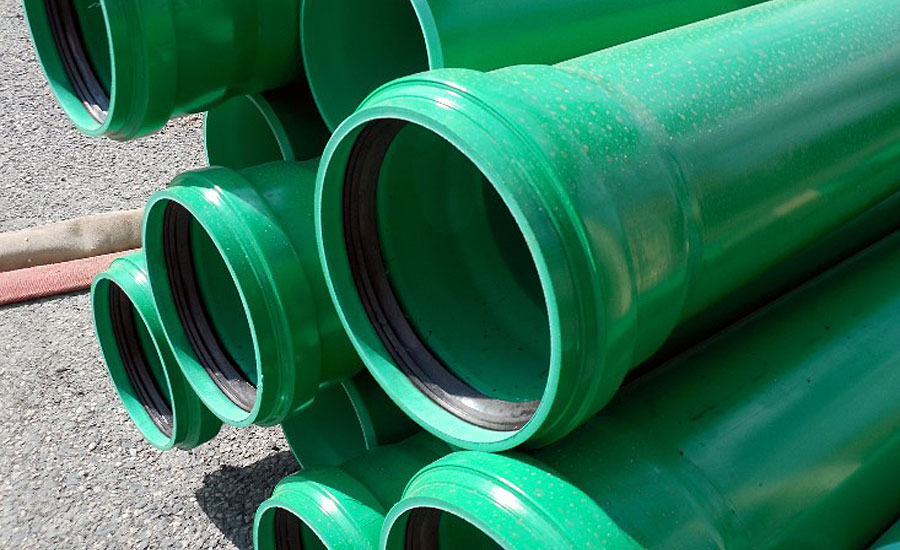
Over the past 30 years, the use of prepainted metal has expanded into every type of manufacturing. From automotive and building materials, to appliances, HVAC and more, prepainted metal now appears almost everywhere in our daily lives. Constant improvements to the coil-coating process are why prepainted metals are becoming manufacturers’ go-to method. Manufacturers have discovered that today’s prepainted metals offer more cost-savings, durability and specialized coatings than ever.
Coil Coating Benefits
Energy Savings
One of the most appreciable advantages is the energy savings the coil-coating process affords. The energy used to cure coil-coated metal is substantially less than other processes. Savings are achieved by using high-speed material processing and by recycling 90 percent or more of the painted coil’s VOCs back into the curing ovens, where they are re-used as fuel. Major improvements to the curing ovens, the most energy-intensive part of the coil coating process, enable paint to cure in just seconds, using innovative induction, infrared and near-infrared curing.
Cost Savings
Because prepainting does not require manufacturers to store paint at their facility, it also effectively eliminates all the costly labor and environmental challenges related to post-painting (e.g. waste removal, emission control and assorted EPA compliances). Modern coil-coating facilities already have approved water and air pollution equipment in place that satisfies EPA requirements. Many coil-coating lines have also substantially reduced water usage by using innovative, no-rinse pre-treatments. These savings all add up for manufacturers.
Flexibility
Since prepainting allows metals to be finished in one continuous pass, there is also flexibility in how the metal is coated and the types of coatings that can be used. Organics and inorganics, such as polyesters, epoxies, vinyls, plastisols, acrylics, waterborne emulsions, fluorocarbons, dry lubricants, treatment and primer combinations can all be applied. This allows the selection of the most appropriate coating for the application.
Prepainted coils can be printed, striped and embossed to create special visual effects. In many ways, coil coating has limitless design possibilities, most of which are virtually impossible with other systems.
Today’s coil-coated metal can also offer specialized coatings, including antimicrobial, non-skid, fingerprint-resistant, reflective, anti-graffiti and anti-static coatings, just to name a few.
Color Matching
One of the main reasons for buying prepainted product is to provide a specific color appearance. Often the customer is matching the prepainted part to other components of a building or product. Matching the color standard is critical for good appearance of the final assembled product. For repeat colors, matching the standard on each run ensures that there will be consistency of color over time. Many factors can affect color: paint formulation and quality, film thickness, substrate color, cure temperature (PMT) and dwell time in curing ovens. These can all be monitored and closely inspected during the prepaint process, assuring perfect color appearance and matching.
Performance
Long-term durability is perhaps the most critical property of any painted metal product. The processes involved in the prepaint system provide superior corrosion resistance and protection, particularly where there are cut or exposed edges. Because the prepainted sheet is uniformly cleaned, pretreated and painted as a “flat” surface; edge-to-edge and side-to-side variability are virtually eliminated. Plus prepainted parts often have two coats of paint tightly bonded to the metal, while post-painted parts generally only have one coat of paint. And prepainted parts have paint on the backside. At best, post-painted parts get a touch of overspray.
Research has proven that prepainted surfaces actually hold up better over time. The NCCA, with the help of PPG Industries, Inc. and the North American Zinc-Aluminum Coaters Association (NamZAC), compared the corrosion resistance of prepaint with three types of post-paint. Prepainted metal louvers with exposed, cut edges were field-tested alongside three sets of metal louvers; one with a post-painted electrocoat, a second with a powder finish and a third with a spray finish. The parts were made of hot-dipped galvanized steel. The louvers were exposed to the same environment in Daytona Beach, Florida. After 16 months, 44 months and 68 months of exposure to the elements, comparisons showed the corrosion resistance of the prepainted parts was significantly better in terms of the uniformity of treatment and film thickness.
How Prepainting Works
Metal coils are shipped to a continuous coil line for processing. First they are uncoiled, and then while still in flat form, the metal is uniformly (edge to edge) cleaned and pretreated. Being flat is a major advantage. A flat sheet enables excellent control of coating weights of both the pretreatment and the paint to within a tenth of a mil or less, depending upon the equipment and the paint system being applied. Post-painted metal is a batch process where several formed parts are hung on racks for processing together. These parts often contain forming lubricants, mill oils, dirt and metal filings. Because they are hanging on racks, it is hard for cleaners and rinses to reach all the surfaces and clean the parts uniformly. As a result, contaminants become trapped in bends and crevices. This results in non-uniform pretreatment and variability in corrosion resistance.
In the flat prepaint system, cleaning and pretreating are accomplished using a multistage, high-efficiency system for the specific substrate being painted. First, a high-temperature alkaline cleaner removes any oils, oxides, dirt and other contaminants. This cleaning increases the surface reactivity of the metal so that it bonds tightly when the pretreatment is being applied. The tight adhesion to the pretreatment further optimizes corrosion resistance. The pretreatment, like the cleaner, is substrate-specific and promotes adhesion between the primer and the metal coating. This adds another layer of corrosion resistance.
Having a pretreatment that is substrate-specific is important to the final finish. In post-paint operations, because factory space is often limited, only one pretreatment is usually available and must be used for many substrates. The pretreatment is not optimized for a specific substrate. This reduces the bond strength between the metal and the pretreatment. Oxides left on the surface decrease primer adhesion.
The next step in the prepaint process is uniformly applying a high-performance primer across the strip. These primers typically contain corrosion and UV inhibitors. They also provide added protection from cuts, scratches and bends. Plus they bond tightly to the topcoat. The ability to uniformly apply the primer and topcoat is key. Spray applications of formed parts is usually non-uniform in film thickness. Bends and drawn areas typically have lower film thickness than flat areas. This is also true of powder systems where recycling of the powder can increase particle size and decrease uniformity of film thickness.
Conclusion
The conversion to prepainted metal will provide energy and labor savings, reduced environmental risks, outstanding appearance, more design options, superior color matching, and better wear and corrosion resistance. To learn more about improvements happening in the coil coating industry, visitLooking for a reprint of this article?
From high-res PDFs to custom plaques, order your copy today!