Airblast Eurospray Helps Flowserve Take Control of Blast and Spray Operations
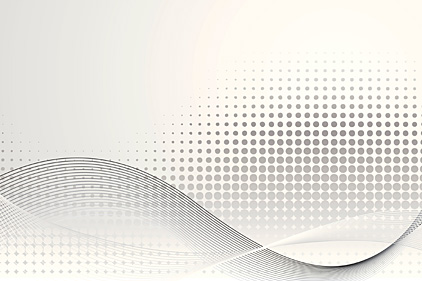
PETERBOROUGH, England – Airblast Eurospray recently completed a new blasting and spraying facility for Flowserve, a specialists in flow-control products.
Flowserve is recognized as the world’s leading supplier of pumps, valves, seals, automation and services across a range of industries including power, oil, gas and chemical. The company use blasting and spraying for the preparation of various valves and other products and wanted to be able to bring this in-house to gain more control over the process.
The project provided a number of challenges as the facility was to be situated near a residential area. Airblast Eurospray worked with Flowserve and a range of engineers to design and develop a facility that would meet all of the requirements.
Airblast Eurospray installed a modular style blast room measuring 7m (length) x 5.5m (width) x 3m (height). It was constructed with an Airflex recovery floor, which automatically recovers abrasive materials from beneath the operator’s feet giving them a virtually endless supply of media. Rails were fitted from outside the blast room to inside, close to the rear of the blast room, allowing a bogey, supplied by Airblast Eurospray, to be used for transporting heavier valves into the booth. The blast room recovery system also incorporated a bucket elevator and grit wash, which recycles the spent abrasive, feeding it back to a hopper installed above the blast machine.
The blast room was designed to ensure that dust is moved quickly and efficiently through the booth to allow for clear visibility, to decrease wear on parts and to provide a better blast quality. Airblast Eurospray work with gravity to ventilate the booths, allowing air to enter at a high level and exit at a low level. The optimum extraction rate is 50fpm, a rate that can indefinitely suspend a particle of metallic dust, preventing it from falling out of the airstream until it has been captured within the dust extractor. Capturing dust as it is generated avoids buildup and allows for blasting in a virtually dust-free environment, improving safety and efficiency
Along with the blast booth, Airblast Eurospray installed an industrial low-bake combination spray booth for the spraying of beam and lattice fabrications. The spray booth is comprised of double-skin, pre-coated, auto-bonded, insulated panels interlocked to a self-supporting structure. The panels are integrated into the booth support steel work, which forms part of the superstructure and roof inlet plenum. The booth was fitted with double-skin, galvanized, powder-coated, triple-leaf doors at one end to form a flow-through booth. It also features a smooth internal surface to help with cleaning and maintenance.
Extraction is provided via a 5000mm wide floor-mounted twin-stage dry filter extract chamber, coupled to belt driven centrifugal extract fans. A roof-mounted heated air replacement plant was provided to draw air from the atmosphere and heat and filter it prior to forcing it into the general working area. The system was completed with an inlet bend, volume control damper, 1 No belt direct driven centrifugal flow inlet fan, silencer and high level inlet filter plenum chamber complete with easily accessible drop down filter frames.
The installation ran very smoothly with Airblast Eurospray working closely with Flowserve to ensure the project stayed on track and continued to meet the company’s demands. It was finished on time and to the agreed upon budget. Airblast Eurospray engineers remained on site to provide comprehensive training for all Flowserve staff to ensure that they are able to use the equipment efficiently and safely.
Looking for a reprint of this article?
From high-res PDFs to custom plaques, order your copy today!