Measuring a Variety of Car Parts

Color is just one of a myriad of factors that will influence our buying decision when it comes to automobiles. An important factor that we take into account before we even drive the car, and the first thing that we notice, is the quality of the color and appearance of the paint. Color appearance is important; manufacturer and dealer websites let us pick and choose the color combinations of the car even before we enter the showroom, while TV commercials, programs and brochures make the automobiles visually attractive to us. These are key factors in our purchase decision.
Generally, exterior body materials are made up of metal or composites, while the bumper materials are flexible plastics. Due to differences in physical wetting properties and paint processes such as baking, temperature or time, and the possible changes of color when applied to the various body parts, these materials need to be coated with different types of paint. Color tolerances between the different body parts are becoming tighter.
The ability to measure color differences on various parts of a car is now a requirement in the automotive industry. Of importance is color matching between two adjoining parts. When large areas of the automobile are painted, the paint thicknesses and color can change gradually, and noticeable color differences on adjoining car parts can become apparent. To create a more attractive color impression, automotive manufacturers have started inspecting color harmony on a wider variation of car parts that had not been checked in the past. Often these adjacent parts have some curvature for improving aerodynamic drag to reduce fuel consumption and to create a more attractive design.
Color Measurement
Some exterior car paints have metallic or pearlescent effects, which have a view angle dependency of color appearance. To control and manage the quality of these paint colors, a multi-angle spectrophotometer is used. This type of spectrophotometer has various measurement geometries.1 For the geometries, a multi-angle spectrophotometer needs to have several measurement angles for monitoring the exterior paint colors.
The angles are described in ASTM E 21942 published by the U.S. standardization committee, American Standard Test Method International. The angles are defined as an angle from specular light, aspecular angle and As 15, 25, 45, 75, 110°. ASTM E25393 also describes an angle for measuring pearlescent paints, and the angle is As-15. These angle color data can detect visual impression in metallic and pearlescent paints with color angle dependency.
Konica Minolta Sensing Inc. has released its multi-angle spectrophotometer CM-M6. The unit’s specifications are listed in Table 1. The CM-M6 can measure the following six angle geometries: As -15, 15, 25, 45, 75, 110°. When the CM-M6 measures automotive exterior paints, its As15 data, near specular light has a high L* value and as 110 far from specular light has a low L* value (Figure 1a). Also in the a*-b* diagram, color value change is observed (Figure 1b). This data is consistent with visual impression.
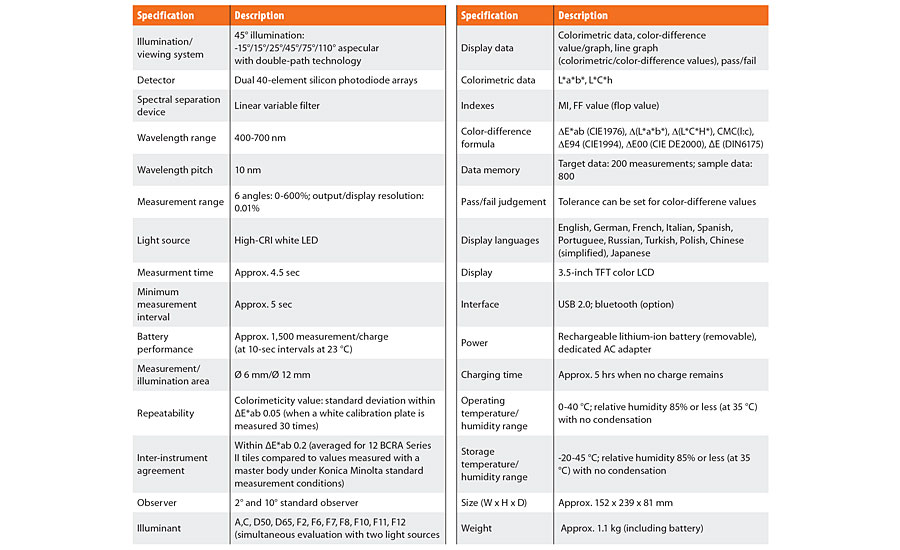
TABLE 1 » specifications of the CM-M6 spectrophotometer.
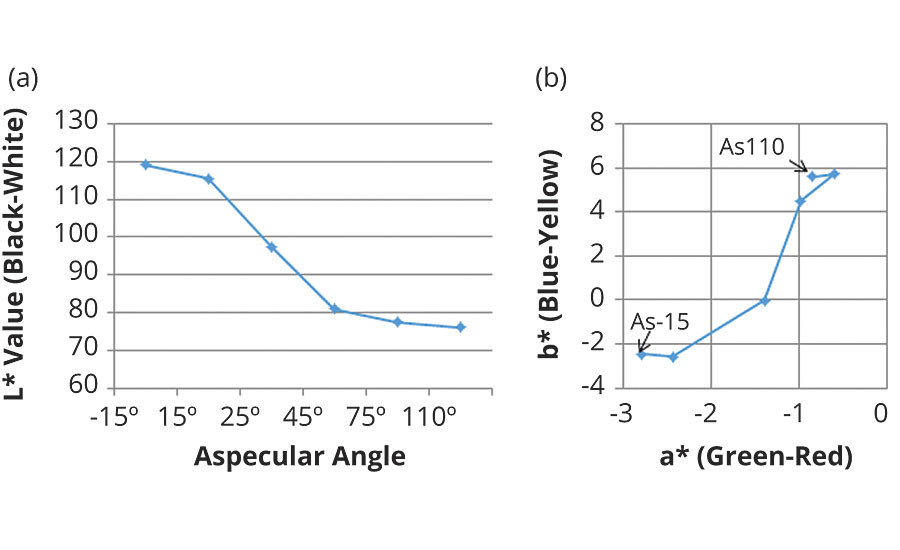
FIGURE 1 » Color change of an automotive paint (white) with geometry measured by multi-angle spectrophotometer. Left graph (a) is L* value change with aspecular angle, and right graph (b) is a* and b* data of each aspecular angle plotted in a*-b* diagram (from As -15, 15, 25, 45, 75, to 110° on a line).
Color Measurement on a Nonflat Sample
When using a multi-angle spectrophotometer to measure nonflat automotive samples (Figure 2) without a fixture for controlling the sample and instrument positions, or when measuring the car body parts with the handheld instrument after assembling, the measurement results in near specular light geometry (ex, As 15) are usually unstable because it is difficult to keep a steady, fixed position of sample and instrument under these measuring conditions. In a conventional multi-angle spectrophotometer, multiple measurements of the same sample result in about ± 3 in DE*ab (Figure 3a). This is one of the big problems in managing automotive part colors using multi-angle spectrophotometers.
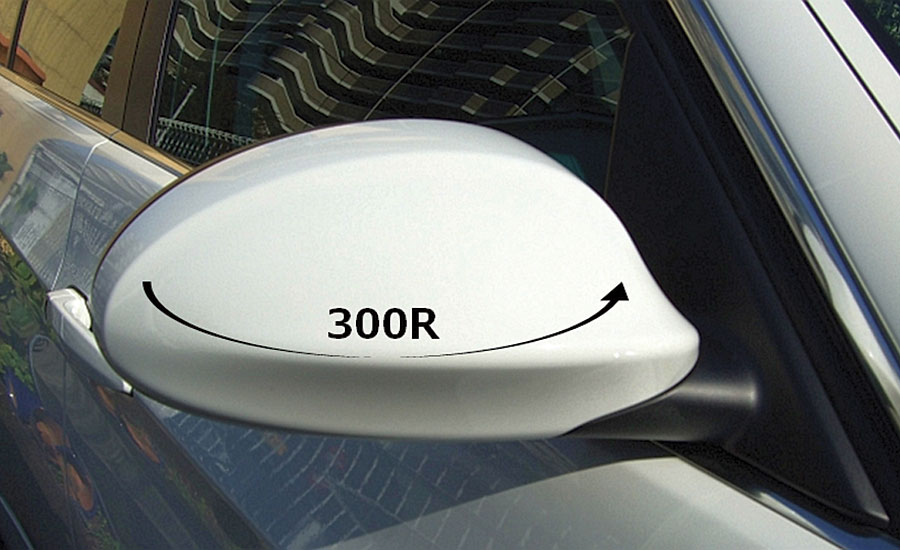
FIGURE 2 » Example of curvature on car parts. Its typical rounding shape is R 300 mm.
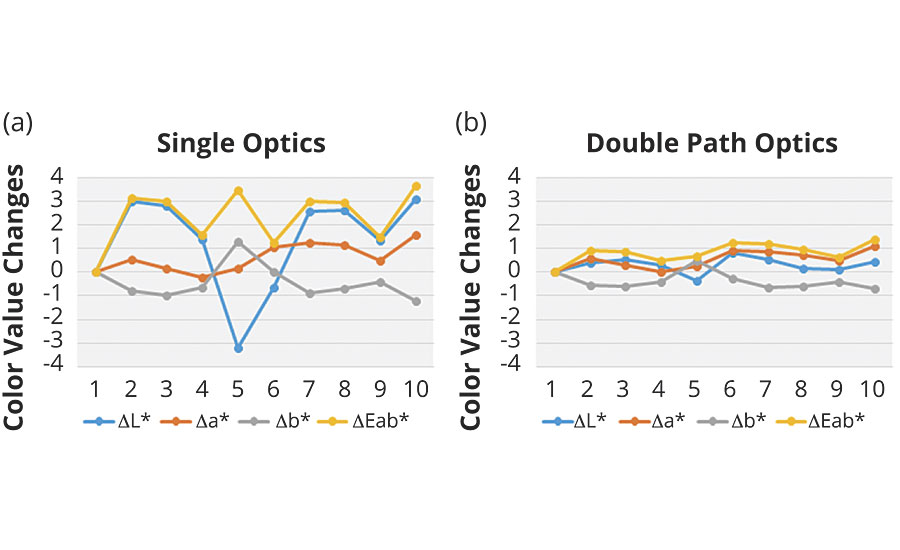
FIGURE 3 » Measurement stability of the CM-M6 in automotive curvature samples. The left graph (a) is a simulated result from a single optical system of a conventional multi-angle spectrophotometer. The right graph (b) is the CM-M6 result with a double path optical system. This is data obtained by repeatedly measuring the surface of R300 10 times. The color of the measured sample was a white pearl.
The CM-M6 spectrophotometer can overcome this issue. It has two symmetrical optical systems aligned to the measurement vertical plane (Figure 4); most conventional instruments have only one optical system. This double path measurement system can compensate two measurement results against each other (one optical result has light over the adequate light and the other one has light under the adequate light, and those lights can compensate for each other when the sample and instrument position have some incline within the incline tolerance of the instrument). As a result, the CM-M6 measurements show ± about 1 in DE*ab (Figure 3b). This technology is described in U.S. patents (Teraoka, Tsurutani, Yamanoi).4,5
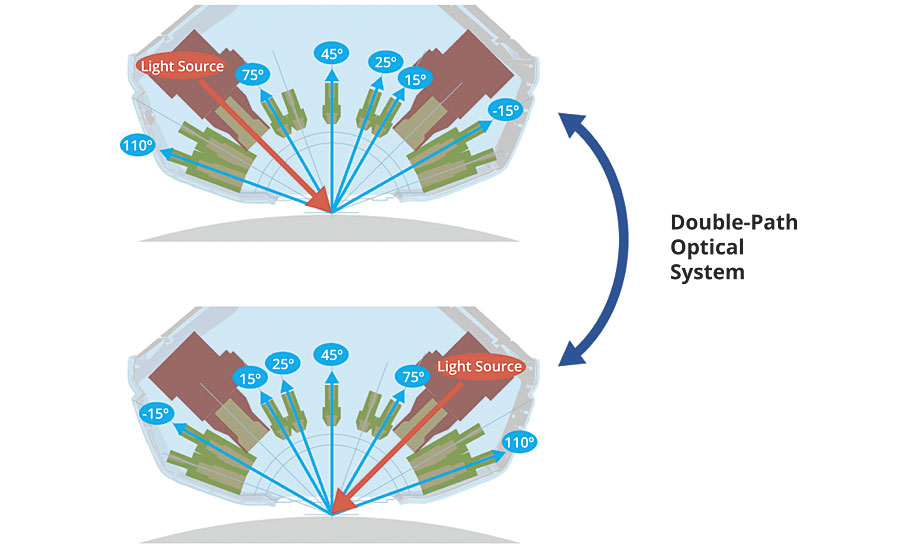
FIGURE 4 » Image of the CM-M6’s double path optical system.
Instrument shape is an important factor in obtaining repeatable, quality results. The shape of the CM-M6 was created by industrial designers and has an ergonomically designed vertical shape. The optical system inside the CM-M6 has been optimized for the small body. The unit’s shape was awarded a prize in Japan for design (Special Jury Award at the 47th Machine Design Awards, sponsored by the Nikkan Kogyo Business & Technology Daily News).
In industrial use, inter-instrument agreement is an important factor. When customers want to use an instrument in factories at different locations, the instrument needs to output similar values with acceptable tolerances. CM-M6 has been analyzed in this regard, and we have published a scientific paper of the results.6
Conclusion
The CM-M6 multi-angle spectrophotometer allows customers to measure nonflat automotive samples that in the past have been difficult or impossible to measure with excellent repeatability of color values.
References
1 Nofi, M. Understanding color measurement geometry, Paint & Coatings Industry, August 2016, 42-47.
2 ASTM E2194 (2014): Standard Test Method for Multiangle Color Measurement of Metal Flake Pigmented Materials.
3 ASTM E2539 (2014) Standard Test Method for Multiangle Color Measurement of Interference Pigments.
4 Teraoka, Y.; Tsurutani, K.; Yamanoi, Y. Multi-Angle Colorimeter, (2015) U.S.Patent 9222835.
5 Teraoka, Y.; Tsurutani, K.; Yamanoi, Y. Multi-Angle Colorimeter, (2015b) U.S.Patent 9500525.
6 Imura, K.; Teraoka, Y. Model-Based Corrections of Geometric Errors in Multi-Angle Measurements of Gonio-Apparent Coatings, Color Research & Application, Volume 41, Issue 4 August, 2016, pg. 372-383.
For more information, visit http://sensing.konicaminolta.us/products/cm-m6-spectrophotometer/.
Looking for a reprint of this article?
From high-res PDFs to custom plaques, order your copy today!