New Polymeric Dispersants
Provide Improved Stability and Color Properties for Industrial Waterborne Coatings

The use of an adequate dispersant is necessary to achieve good stability and color properties for dispersed pigments in waterborne paint systems. Electrostatic repulsive and steric hindrance forces can be achieved by combining polyelectrolyte dispersants and traditional non-ionic surfactants. Improved stability and behavior can be achieved with new high-molecular-weight dispersants discussed in this article.
New polymeric dispersants are suitable for low-volatile organic compound (VOC) and alkyl phenol ethoxylate (APE)-free pigment dispersions for industrial and ink applications. Compared with traditional polymeric types, the properties are enhanced. These enhanced properties provide excellent color strength development, high pigment loading at low viscosity, improved stability and high gloss development.
Introduction
Over the last several decades, stricter legislation and regulation of VOCs in waterborne coatings have consistently challenged paint formulators and manufacturers in the choice and use of traditional dispersants to provide much needed long-term stability as well as application properties for a given paint. The VOC changes, together with APE-based surfactant restrictions, represent new challenges for pigment dispersion and coatings formulators. As a result, the need for high-performance dispersants has significantly increased. Newer polymeric dispersants, which represent improved alternatives to the more traditional anionic dispersants, enable formulators to achieve good stability and color properties for dispersed pigments in waterborne paint systems. They are also suitable for VOC-free and APE-free pigment dispersions for industrial and ink applications.
Factors for an Effective Dispersant
Key factors for an effective dispersant are represented by its ability to disperse and stabilize pigments. Ideally, the dispersant is adsorbed to the minimum particle size pigment, covering its entire surface. Especially in waterborne systems, the pigment-dispersant interaction should be resistant to a variety of variables like different resin chemistries, pH, cosolvents and ultimately pigment type. Inorganic pigments (metal oxides) are lower in tint strength and brightness. However, they possess high opacity, are weather resistant and are typically easy to disperse. On the other hand, organic pigments have a lower particle size and therefore higher tint strength and brightness. They are more ultraviolet and heat sensitive, and typically more challenging to disperse. A successful dispersant will need universal dispersing capabilities.
Polymeric dispersants have two major components in their structure - the functional groups that anchor onto the pigment surface and the polymeric chains that create a steric hindrance around the pigment. Dispersants could be tailored to possess single or multiple anchoring groups as well as single or multiple polymeric chains using diverse chemistries. It is important that the anchor functionality provides a strong interaction with the pigment as well as adequate particle surface coverage. A poorer anchoring ability would lead to pigment flocculation, sedimentation and inferior color development.
Another key factor for a successful dispersion is the compatibility of the polymeric chains with the solvent/water. They need to have a high degree of solubility in order to uphold steric stability.1
The benefits of an ideal dispersed system include:
Quality
- Higher color strength
- Higher gloss
- Lower haze
- No flocculation
- No phase separation
- No settling/ideal storage behavior
- No formation of paint defect like Benard cells
- Surface appearance
- Film build
- Good technological properties like:
- Water resistance
- Weathering resistance
- Corrosion resistance
Productivity
- Low viscosity
- Low/no foam creation
- Faster dispersing process
- Better mill utilization
- Low energy costs
Flexibility
- Lower/no need for dispersing resin/vehicle
Stages of Dispersion
The dispersion mechanism represented in Figure 1 consists of three distinct stages – wetting, separation/grinding and stabilization. Pigments are usually supplied in the form of dry powders. These dry powders consist of agglomerates, much larger than primary particles. In the first stage the liquid replaces air on the surface of the pigment particles by decreasing the interfacial tension. The separation stage involves pigment particle size minimization through milling. For an optimal performance, the pigment agglomerates should be broken up and disrupted into smaller units. In the stabilization stage the dispersant prevents the pigment from re-agglomeration through either electrostatic, steric or a combination of the two mechanisms.
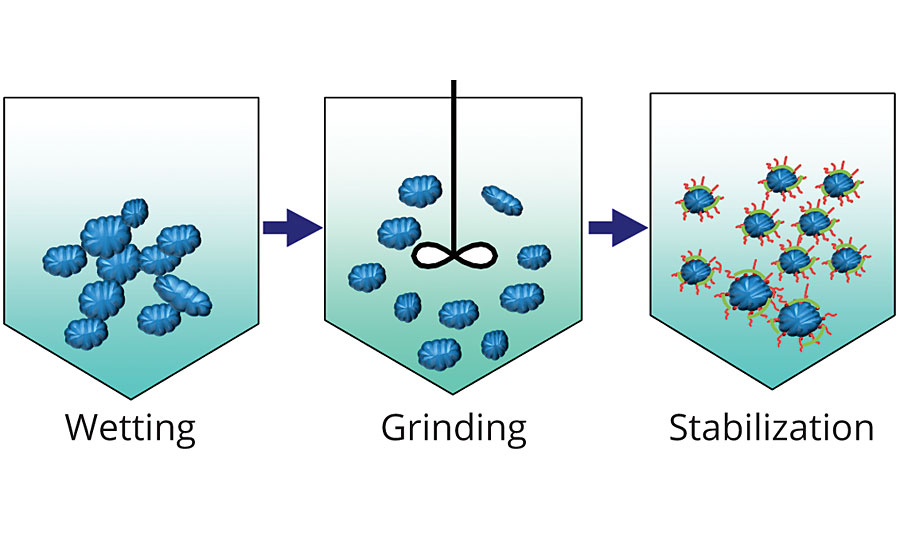
Polyelectrolyte dispersants are stabilized by electric repulsive forces. They form an electrical-charged double layer on pigment surfaces that prevents particle agglomeration. However, the polyelectrolyte dispersants do not have wetting properties, so they need to be used in combination with a wetting agent. Also, they are sensitive to the presence of other ions in the system, which can disrupt the double layer.
Non-ionic-type dispersants are stabilized by steric hindrance and provide a wetting effect. Traditional non-ionic surfactants adsorb on the pigment surface by anchoring groups and stabilize the dispersion by steric hindrance forces using solvation chains. However, smaller molecules or weaker single anchoring interaction could lead to desorption and, therefore, flocculation.
Finally, polymeric dispersants contain multiple anchoring groups and multiple solvation chains connected to the backbone (Figure 2). As a result, the departure of anchoring groups is prevented and long-term stabilization is achieved. They also provide wetting properties and are not sensitive to ionic content.2
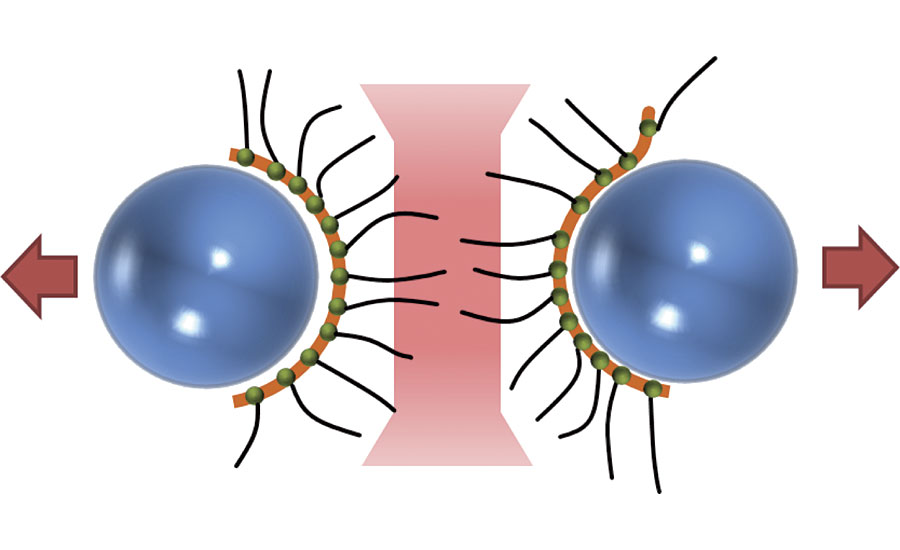
A New Type of Dispersant
New polymeric dispersants comprised of a high-molecular-weight copolymer containing multiple anchoring groups were developed in late 2018. This new type of dispersant is a wetting and dispersing agent designed especially for waterborne industrial coatings and inks. It offers efficient viscosity reduction in the grinding mill base and enhances the color intensity of pigments. The new dispersant, designated in this article as Dispersant E, was evaluated in comparison with similar competitive commercial dispersants to show its enhanced properties in a series of different pigment dispersions. It provides excellent color development, gloss, good stability and is alkylphenol ethoxylates (APEO) free.
Experiment and Results
Viscosity
Resin-free pigment concentrates were formulated with different dispersant to pigment (D/P) ratios depending on the nature of the pigments:
- Blue pigment based on phthalocyanine (Heliogenblue D 7079) – D/P 65%
- Carbon black based on MA 100 – D/P 50%
- White pigment TiO2 based on Ti-Pure R706 – D/P 15%
The viscosity of the concentrates was measured and monitored after aging 7 days at 50 °C. In all cases the viscosity of the concentrates was comparable with the viscosities of the market references. The titanium dioxide (TiO2) concentrate showed the highest viscosities – dispersant E performed with an acceptable stability, while market reference B showed borderline initial viscosity and a viscosity drop after aging.
Color and Gloss
The concentrates were incorporated into paint clear coats for different end uses. The color performance and gloss behavior before aging was determined:
- Plastic clear coat based on Albedingk AC 2524: An economic self-crosslinking multiphase acrylic dispersion.
- Metal protection clear coat based on Dow Maincoat HC 54 G: An acrylic resin for waterborne maintenance vehicle paint that is recommended for primers and gloss topcoats.
Phthalocyanine Pigment
For phthalocyanine pigment (Figure 3), Dispersant E showed similar color behavior as market references A and B. The maximum color change in B was 0.3
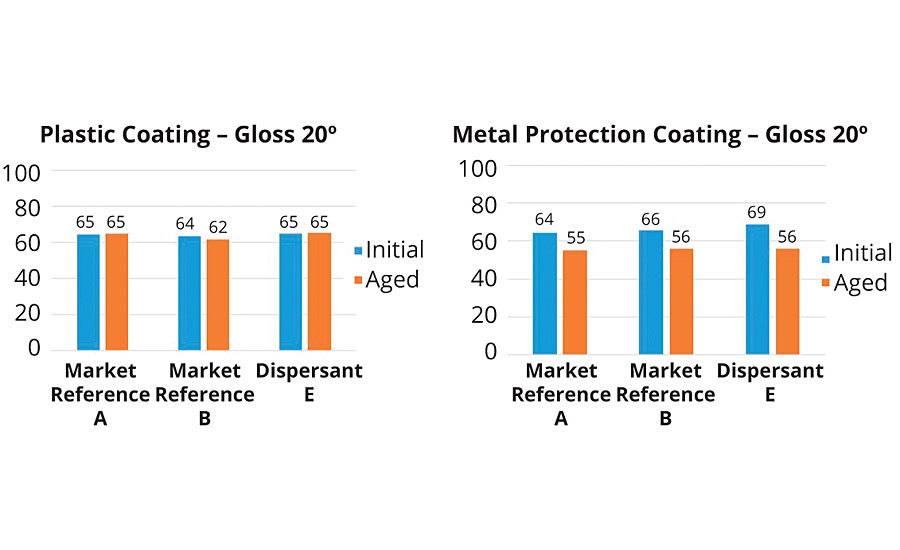
Initial gloss value was the highest in both paints when using polymeric dispersant E. In the plastic coating, dispersant E showed a very stable behavior – no change in gloss was noticed. In the metal protection coating all samples experienced a drop in gloss after aging.
Carbon Black
Using the carbon black concentrate in paint, dispersant E showed very stable values in lightness (Figure 4). In both systems the stability was very good. Significant color changes with the market references were noticed in the plastic coating, while the lowest color difference was achieved with dispersant E.
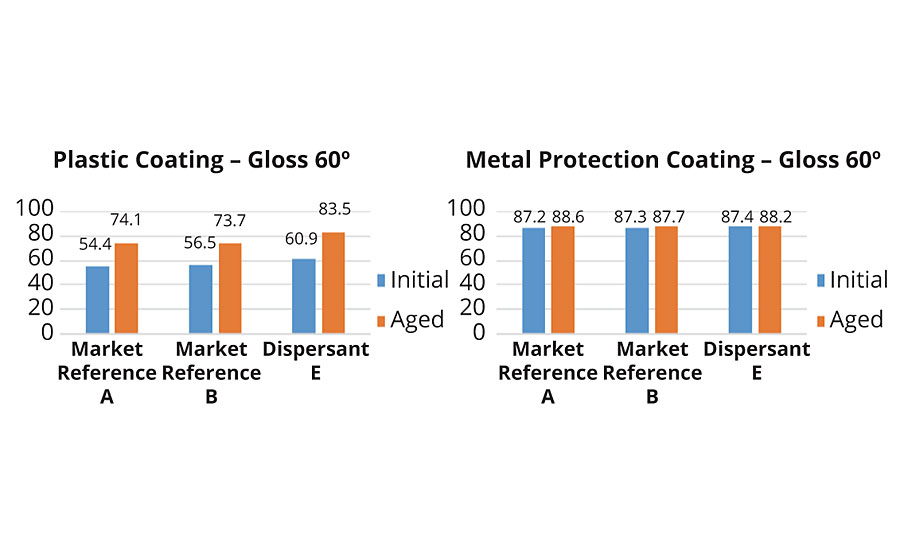
The plastic coating formula could differentiate between the different dispersant samples giving best initial gloss and aged result for dispersant E. In the metal protection coating all samples behaved very similarly, showing no significant gloss change.
Titanium Dioxide
The plastic coating showed very selective results for TiO2 as well (Figure 5). Good compatibility was shown with dispersant E, resulting in the highest lightness values. Changes after aging were small, like with the market references. The metal protection coating provided very similar lightness values with all candidates.
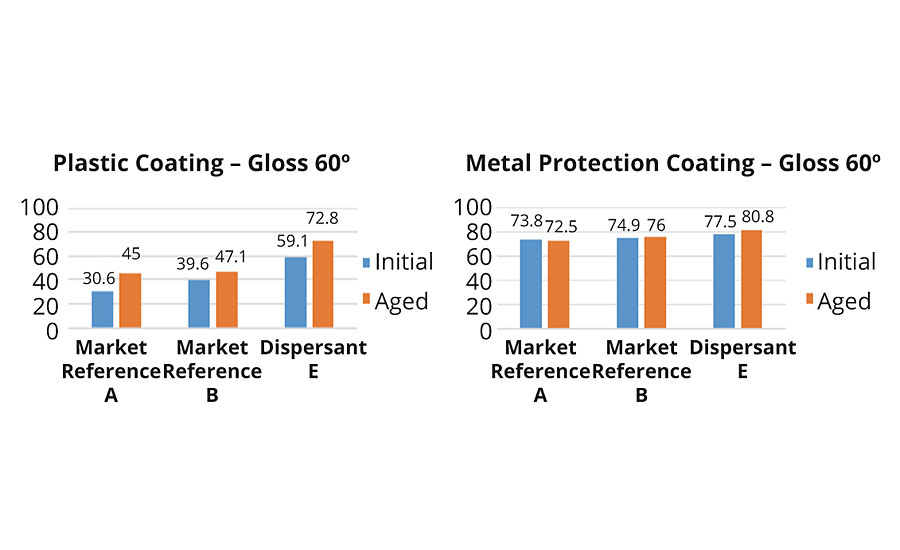
Gloss values were significantly different in the plastic coating – dispersant E provided visible differences in gloss. The metal protection coating showed the best compatibility with dispersant E, resulting in the highest gloss values.
Rub-Out
Rub-out is a basic test to describe stability with pigment mixes (Figure 6). After application of the paint, further stress is applied on the paint film by rubbing the film. Coagulation and flocculation of pigments can be made visible by comparing the rub-out area with the environmental area.
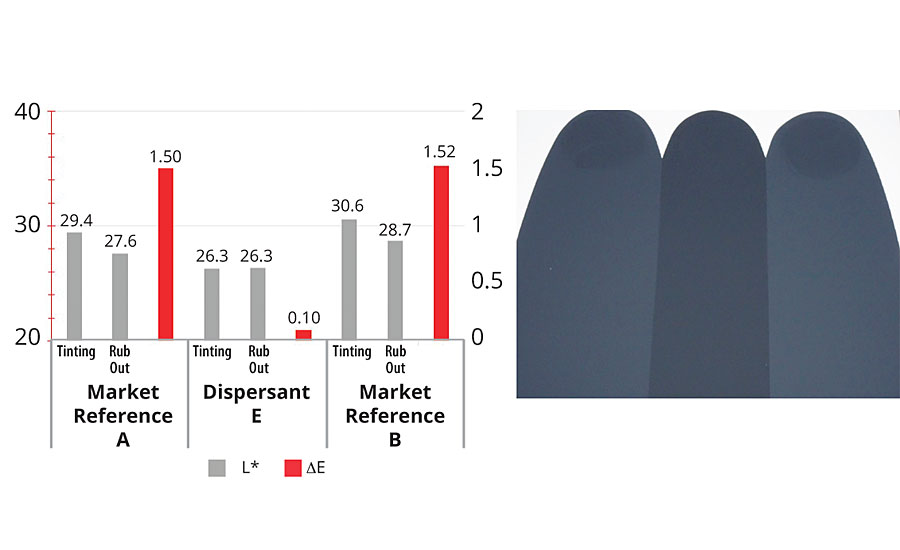
The new development showed comparable behavior to the market references when tinting a white base based on TiO2 with 3% of a pigment concentration based on phthalocyanine.
Outstanding performance was achieved when tinting with 3% of a concentrate based on carbon black. Figure 6 shows the easily visible difference in color. Color measurement of dE confirms the difference and the good performance of dispersant E. Desorption processes are depressed due to the excellent attachment of the anchor groups to the pigment surface.
A bigger study was executed with different black pigments (Figure 7). The study concentrated on difficult-to-disperse, high-jet carbon blacks. These pigments are expensive and frequently used in high-performance glossy topcoats where color and jetness are important. The jetness effect is achieved through very small particle sizes that correlate with large surface areas to be stabilized. The high level of surface area enhances cohesive forces that need to be overcome. In this respect polymeric dispersants are interesting due to having a high density of anchor groups that can prevent flocculation.
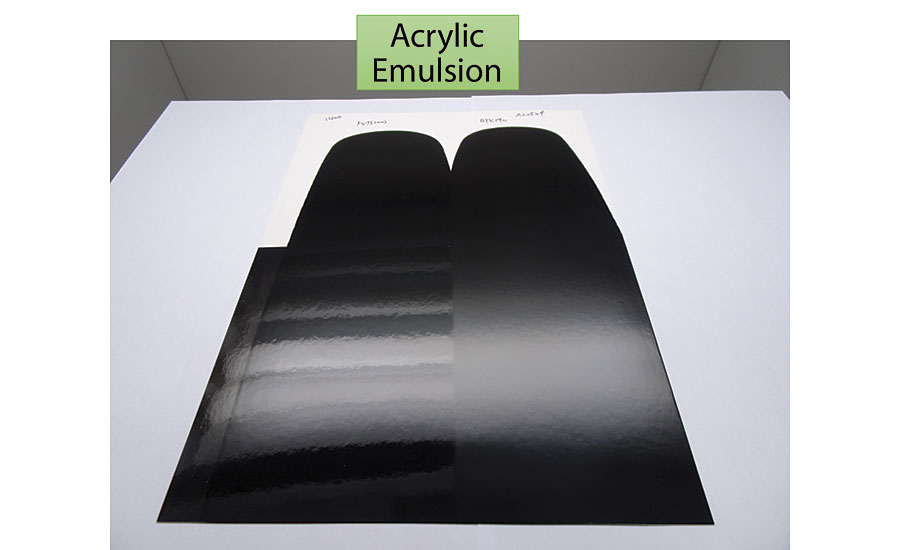
The study looked at the compatibility of four different black pigments dispersed with dispersant E and a market reference. Black pigment concentrates were introduced into paints based on acrylic emulsion and PU-dispersions. A draw down was performed initially and after 8 months aging at room temperature.
Good stability with all pigments was achieved in the PU-dispersion. A differentiation could be made with the acrylic emulsion. The market reference showed significant and visible loss of gloss after aging. A broader compatibility was achieved with dispersant E.
Conclusions
Polymeric dispersants enable formulators to develop higher-quality pigment concentrates and pigmented systems. Formulators have been used to developing concentrates with a package based on polyelectrolyte and a surfactant. Performance in terms of color development, gloss, stability and foam creation during production are improved. By using a polymeric dispersant, both functions are combined into a product, which simplifies the raw material product portfolio and the formulation for production.
These new developments have increased the performance of polymeric dispersants when compared with other commercially available materials. The studies referenced within this article showed excellent color development and stability after aging the paint materials with phthalocyanine and carbon black pigments. The gloss behavior of paints formulated with white TiO2 concentrates was improved. The new dispersants also showed very good compatibility and storage behavior with high-jetness black pigments.
The use of this technology helps to simplify formulas by replacing a traditional wetting and dispersing package. Reducing the raw material portfolio and increasing production time due to simplifying the formula can generate cost savings.
References
1 J. D. Schofield, Handbook of Coatings Additives Vol. 2, (Marcel Dekker; NY, 1992).
2 Patton, Temple C., Paint Flow and Pigment Dispersion, 2nd Ed. (John Wiley & Sons Inc., 1979).
This paper was presented in March 2019 at the European Coatings Show in Nuremberg, Germany.
Looking for a reprint of this article?
From high-res PDFs to custom plaques, order your copy today!