Waterborne UV-Curable Resins for Industrial Wood Applications

Waterborne (WB) UV chemistry has shown significant growth in interior industrial wood markets because the technology provides excellent performance, low solvent emissions and increased production efficiency. UV coatings systems offer the end user the benefits of outstanding chemical and scratch resistance, excellent block resistance, very low VOCs and a small equipment footprint with less storage space required. These systems have properties that compare favorably with two-component urethane systems without the complications of hazardous crosslinkers and pot life concerns. The overall system is cost effective because of increased production speeds and lower energy costs. These same advantages can be beneficial for factory-applied exterior applications including window and door frames, siding and other millwork. These market segments conventionally utilize acrylic emulsions and polyurethane dispersions because they have excellent gloss and color retention, and demonstrate superior durability. In this study, polyurethane-acrylic resins with UV functionality have been evaluated according to industry specifications for both interior and exterior industrial wood applications.
Three types of solvent-based coatings are commonly used in industrial wood applications. Nitrocellulose lacquer is typically a low-solids blend of nitrocellulose and oils or oil-based alkyds. These coatings are fast drying and have high gloss potential. They are typically used in residential furniture applications. They have the disadvantage of yellowing with time and can become brittle. They also have poor chemical resistance. Nitrocellulose lacquers have very high VOCs, usually at 500 g/L or higher. Pre-catalyzed lacquers are blends of nitrocellulose, oils or oil-based alkyds, plasticizers and urea-formaldehyde. They use a weak acid catalyst such as butyl acid phosphate. These coatings have a shelf life of approximately four months. They are used in office, institutional and residential furniture. Pre-catalyzed lacquers have better chemical resistances than nitrocellulose lacquers. They also have very high VOCs. Conversion varnishes are blends of oil-based alkyds, urea formaldehyde and melamine. They use a strong acid catalyst such as p-toluene sulfonic acid. They have a pot life of 24 to 48 hrs. They are used in kitchen cabinet, office furniture and residential furniture applications. Conversion varnishes have the best properties of the three types of solvent-based coatings typically used for industrial wood. They have very high VOCs and formaldehyde emissions.
Water-based self-crosslinking acrylic emulsions and polyurethane dispersions can be excellent alternatives to solvent-based products for industrial wood applications. Acrylic emulsions offer very good chemical and block resistance, superior hardness values, outstanding durability and weatherability, and improved adhesion to non-porous surfaces. They have fast dry times, enabling the cabinet, furniture or building products manufacturer to handle the parts soon after application. PUDs offer excellent abrasion resistance, flexibility, and scratch and mar resistance. They are good blending partners with acrylic emulsions to improve mechanical properties. Both acrylic emulsions and PUDs can react with crosslinking chemistries such as polyisocyanates, polyaziridine or carbodiimides to form 2K coatings with improved properties.
Waterborne UV-curable coatings have become popular choices for industrial wood applications. Kitchen cabinet and furniture manufacturers choose these coatings because they have excellent resistance and mechanical properties, excellent application properties and very low solvent emissions. WB UV coatings have excellent block resistance immediately after cure, which allows the coated parts to be stacked, packaged and shipped right off the production line with no dwell time for hardness development. The hardness development in the WB UV coating is dramatic and occurs in seconds. The chemical and stain resistance of WB UV coatings is superior to that of solvent-based conversion varnishes.
WB UV coatings have many inherent advantages. While 100%-solid UV oligomers are typically high in viscosity and must be diluted with reactive diluents, WB UV PUDs are low in viscosity, and the viscosity can be adjusted with traditional WB rheology modifiers. WB UV PUDs have an initially high molecular weight and do not build molecular weight as they cure as dramatically as 100% solid UV coatings. Because they have little or no shrinkage as they cure, WB UV PUDs have excellent adhesion to many substrates. The gloss of these coatings is easily controlled with traditional matting agents. These polymers can be very hard but also extremely flexible, making them ideal candidates for exterior wood coatings.
Chemistry of WB UV PUDs
WB UV PUDs are made by incorporating UV functionality into the backbone of a PUD (Figure 1). These UV PUDs can be either polyether, polyester and/or polycarbonate based. There is a large selection of UV acrylates available with varying backbones and functionalities. The choice and amount of the UV functional material used impacts the final crosslink density of the coating. There are also multiple processing options that effect the final polymer performance.
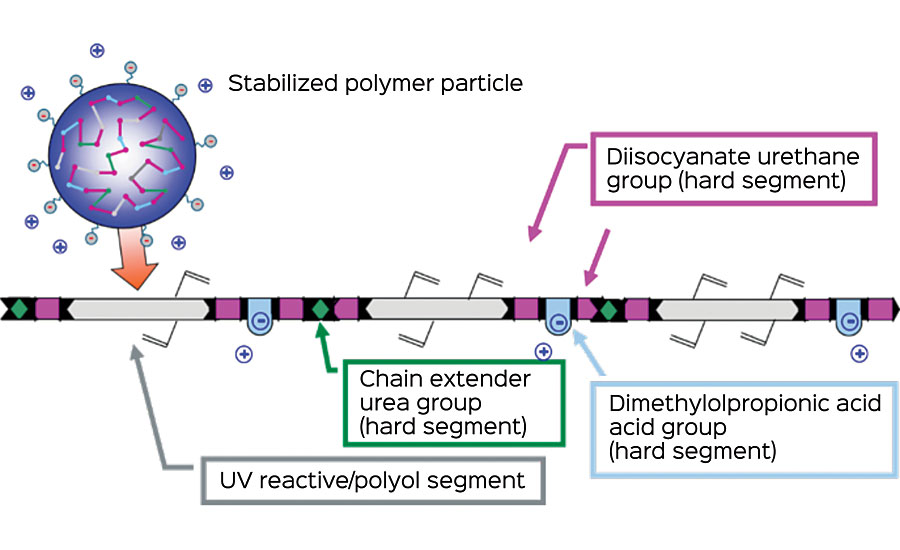
Modifications to WB UV PUDs are made for various reasons. Acrylic dispersions can be added to improve exterior durability and lower costs. Surfactants can be added to improve shelf stability. Emulsified UV acrylates can be added to adjust drying properties. Because different types of WB UV resins can provide different performance parameters, technologies can be combined to optimize the properties needed.
Experimental – WB UV Interior Wood Applications
A study was conducted to compare the properties of three WB UV coatings with commercially available solvent-based conversion varnish, water-based conversion varnish and water-based pre-catalyzed lacquer. The project plan was to develop high-performance WB UV resins and investigate their performance for industrial wood applications. These coatings were tested according to Kitchen Cabinet Manufacturers Association (KCMA), American Woodworking Standards (AWS) and individual furniture manufacturer’s specifications.
Formulations
The formulations used in this study can be seen in Table 1.
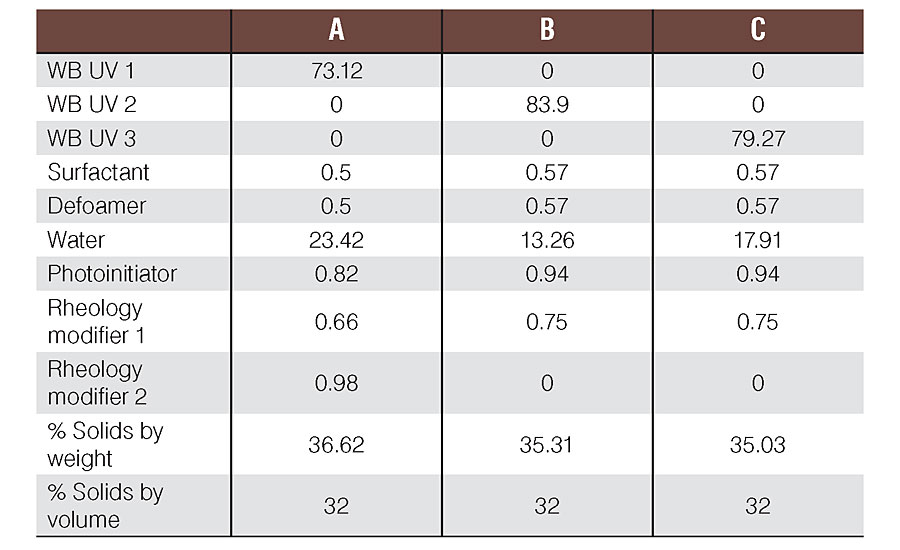
Panel Preparation
UV Coatings
Spray approximately 3 wet mils of coating over 18X18 stained birch plywood panel; air dry for 10 min; force dry for 10 min at 50 C. Cure with mercury bulb at 500 mJ/cm 2 . Sand with 3M Superfine Sanding Sponge. Apply a second coat at approximately 3 wet mils. Air dry for 10 min then force dry for 10 min at 50 C. Cure with mercury bulb at 500 mJ/cm 2 . Wait 7 days before testing unless otherwise indicated in test method. For edge soak, coat and cure all sides of a 4”X4” solid oak panel.
Other Coatings
Spray approximately 3 wet mils of coating over 18X18 stained birch plywood panel; air dry for 10 min; force dry for 30 min at 50 C. Apply a second coat at approximately 3 wet mils. Air dry for 10 min then force dry for 30 min at 50 C. Wait 7 days before testing unless otherwise indicated in test method. For edge soak, coat all sides of a 4”X4” solid oak panel.
VOC levels for the coatings used in this study can be seen in Table 2.
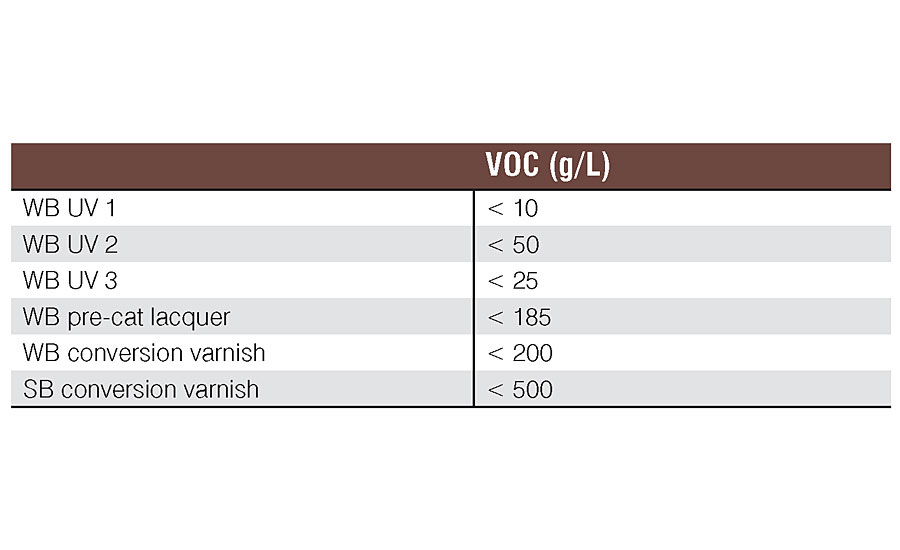
Chemical/Stain Resistance
Apply enough chemical/stain to create a 0.25- to 0.5-inch diameter spot on the test panel. Cover with watch glass. Wait 16-20 hrs. Remove chemical/stain and wash the surface of the panel with water. Rate each chemical/stain on a scale of 0 to 5, with 0 being complete destruction of the film and 5 being no effect on the film (Figure 2).
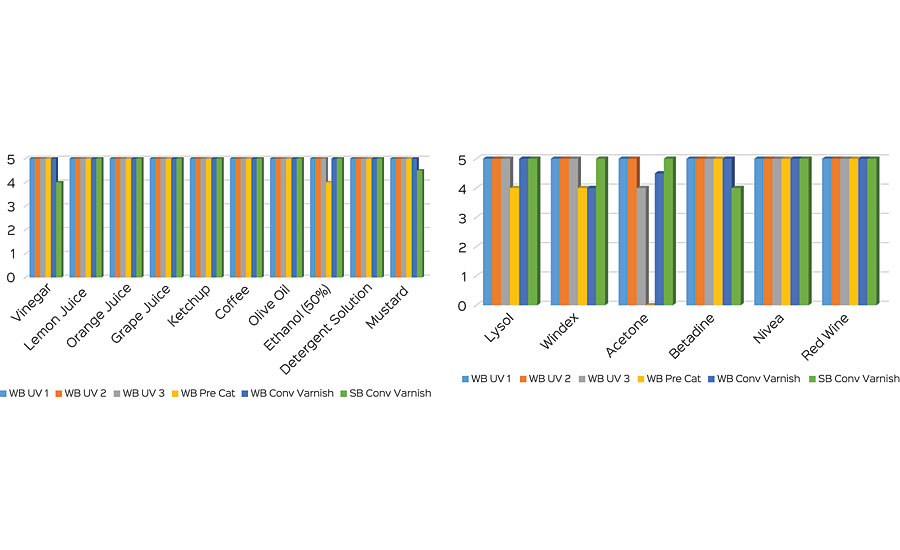
Scrape Adhesion
Cut a 4X4-inch piece from each test panel. Test adhesion with a BYK Balanced Beam Scrape Adhesion and Mar Tester with 5,000 grams of weight using the loop stylus. Rate on a scale of 0 to 5, with 0 being complete removal of the film and 5 being no effect on the film.
Ball Point Pen Indentation
Cut a 4X4-inch piece from each test panel. Test for ball point pen indentation with a BYK Balanced Beam Scrape Adhesion and Mar Tester with 300 grams of weight using the small pen #5785. Wait 1 hr before evaluating the panel. Rate on a pass/fail scale. Any indentation that can be seen from a distance of 24 inches is considered a failure. Figure 3 shows the results of both the scrape adhesion and ball point pen indentation tests.
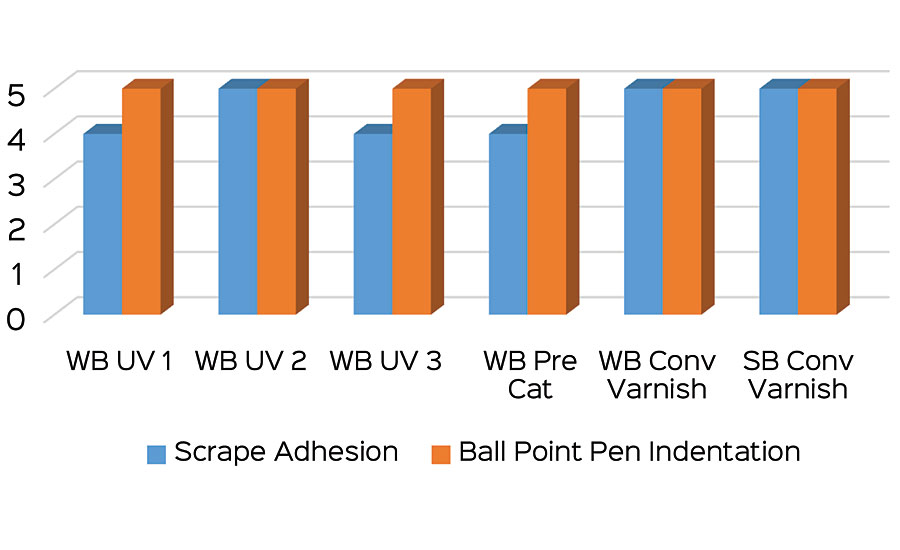
Plasticizer Resistance
Apply a 2-inch square piece of red vinyl to the test panel. Apply a force of ½ lb/in 2 . Place the specimen in an oven at 50 C for 72 hrs. After cooling at room temperature for 1 hr, remove the vinyl square. Evaluate for softening and blistering.
Green Print Resistance
After curing test panel, wait 1 hr then apply a 2-inch square piece of #10 cotton duck cloth to the finish. Apply a force of 2 lb/in 2 directly to the duck cloth. Wait 24 hrs then remove cotton duck cloth. Evaluate for printing.
Hot Print Resistance
After curing the test panel, wait 14 days then apply a 2-inch square piece of #10 cotton duck cloth to the finish. Apply a force of 1 lb/in2 directly to the duck cloth. Place the specimen in an oven at 60C for 24 hrs. Remove the duck cloth and allow the specimen to cool for one hour. Evaluate for printing. Figure 4 shows the results of the plasticizer, green print and hot print resistance tests.
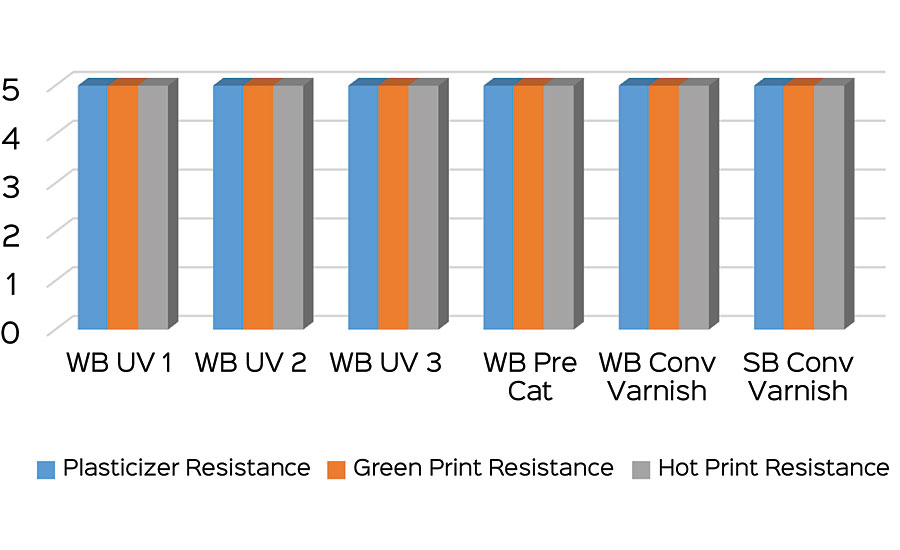
Boiling Water Resistance
Apply 10 mL boiling water to the test panel. Place a ceramic coffee cup full of boiling water on top of the 10 mL of water. Wait 1 hr. Remove the cup and wipe with paper towel. Wait 24 hrs. Evaluate for whitening (Figure 5).
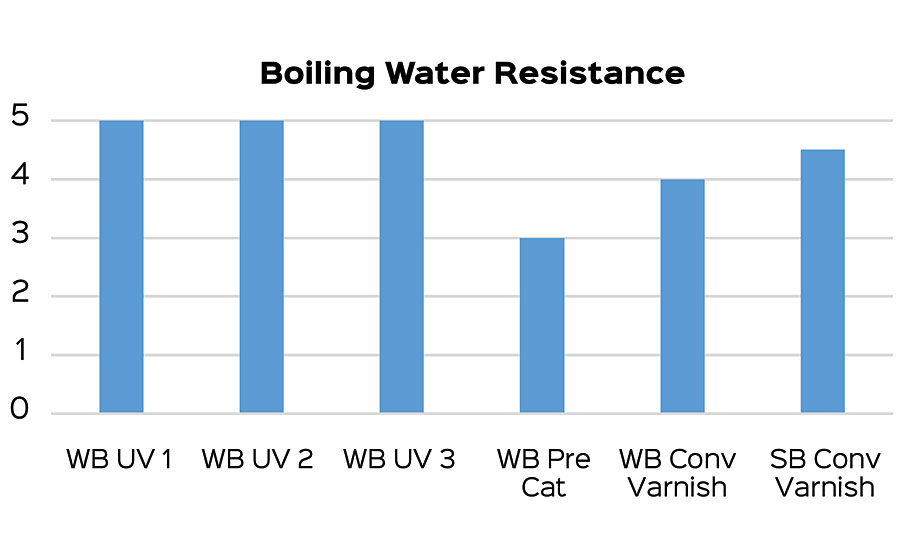
Hot and Cold Check Resistance
Cut a 4”X4” piece from each panel. Cycle as follows: Place panel in humidity cabinet at 50 C and 70% humidity for 1 hr. Remove for 30 min and allow to reach original room temperature and humidity. Place in freezer at -10 C for 1 hr. Remove and allow to reach original room temperature and humidity. Repeat for five cycles.
Edge Soak
Place a cellulose sponge in a plastic container. Level container and fill with detergent solution (1% Dawn dish soap by weight in water) to one half inch below top level of sponge. Place panel on sponge, cut side down. Permit to stand for 24 hrs. The results of the hot and cold check resistance and edge soak tests can be seen in Figure 6.
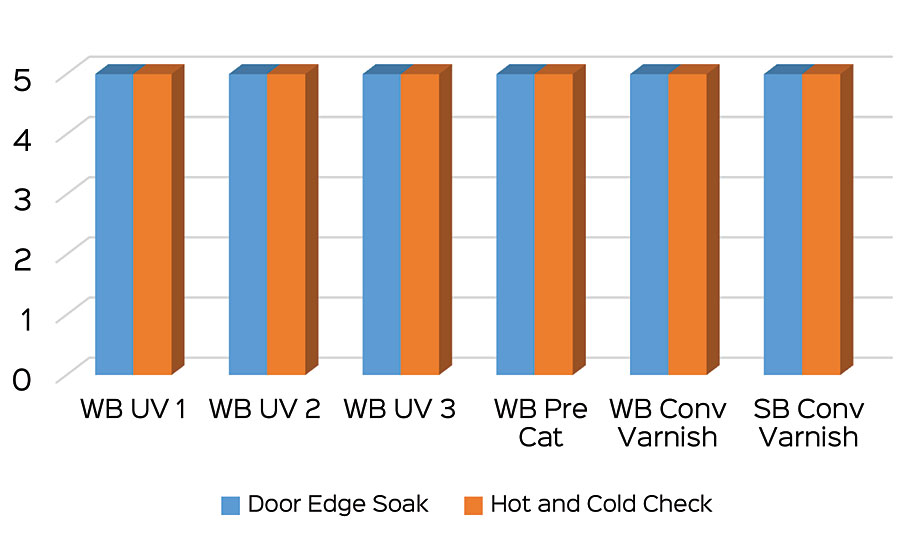
Discussion
All the WB UV coatings have excellent chemical resistance. WB conversion varnish and SB conversion varnish have very good chemical resistance. WB Pre-Cat Lacquer has adequate chemical resistance for KCMA coatings.
WB UV 2, WB conversion varnish and SB conversion varnish have the best scrape adhesion.
All the coatings have excellent ball point pen indentation, plasticizer resistance, hot print and green print resistance, hot and cold check resistance and edge soak.
All the WB UV coatings have superior boiling water resistance.
Experimental – WB UV Exterior Wood Applications, Phase 1
The first phase of this project was to identify the best UV technology in combination with other resin technologies with excellent exterior performance for exterior industrial wood applications. The resin blends were evaluated for hardness development, block resistance, water resistance, cure response and QUV resistance. Coatings were formulated using both UV absorber and hindered amine light stabilizer (HALS). All coatings were tested using two different photoinitiator combinations. All coatings were cured at 800 mJ/cm2. The coatings with only alpha hydroxy ketone photoinitiator were cured using a mercury lamp. Coatings with both alpha hydroxy ketone and acyl phosphine oxide photoinitiator were cured using both a mercury lamp and a gallium lamp. Table 3 and Table 4 show the types of UV resins used, as well as the coatings formulations that were used for this study.
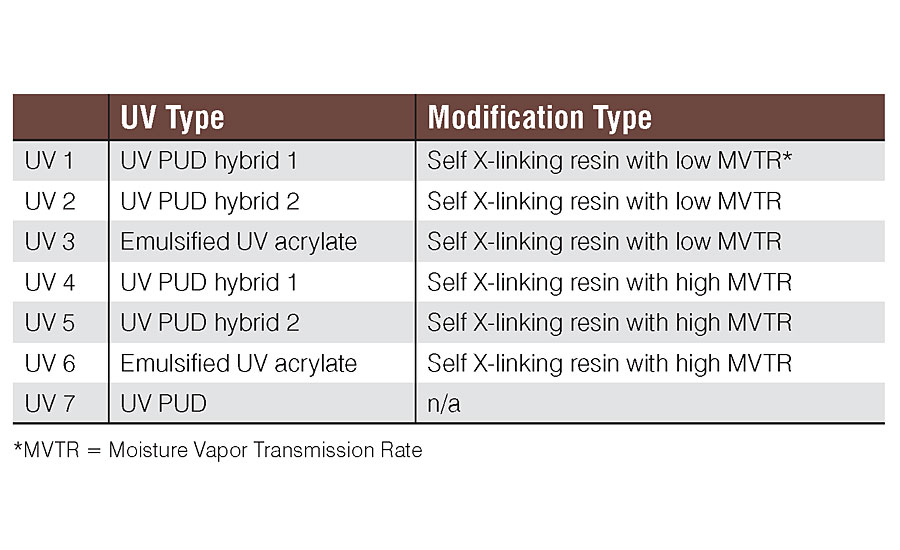
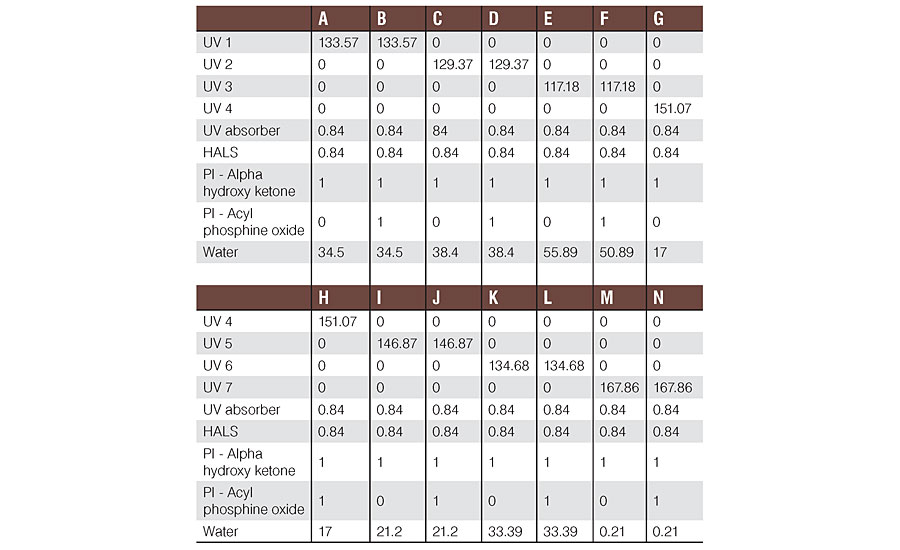
Hardness Development
We made a 150-micron draw down on a glass panel, let it air dry for 10 min and then force dried it for 10 min at 50C. Koenig hardness was measured before cure, 1 hr and 3 days after cure (Figure 7).
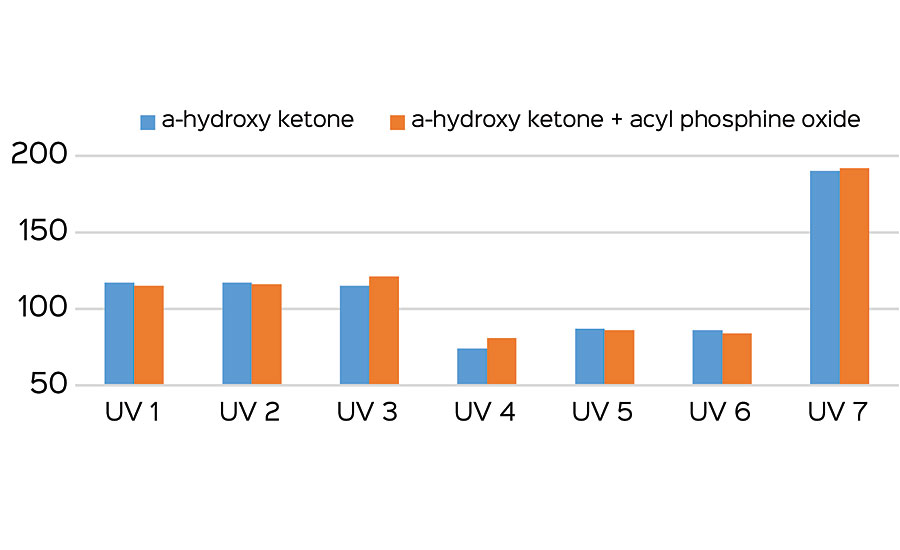
Cure Response
The cure response was measured by comparing the FTIR absorbance peaks of the C=C bond (810 cm -1 ) and C=O bond (1730 cm -1 ) before and after cure. The C=C bond reacts during UV exposure; the C=O bond does not react.
A 3-mil drawdown was made on a 3B-H Leneta chart. It was air dried for 10 min then force dried for 10 min at 50C. Using FTIR, we measured and recorded the IR absorbance at 810 cm-1 and 1,730 cm-1. The charts were cured and then we re-measured and recorded the IR absorbance at 810 cm-1 and 1,730 cm-1 and calculated the percent cure (Figure 8):
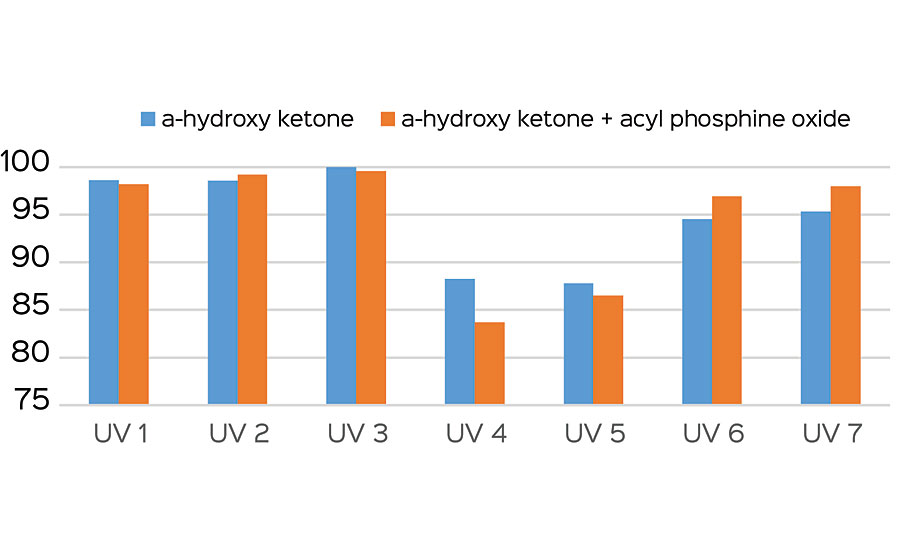
Relative concentration of UV cured group (%) =
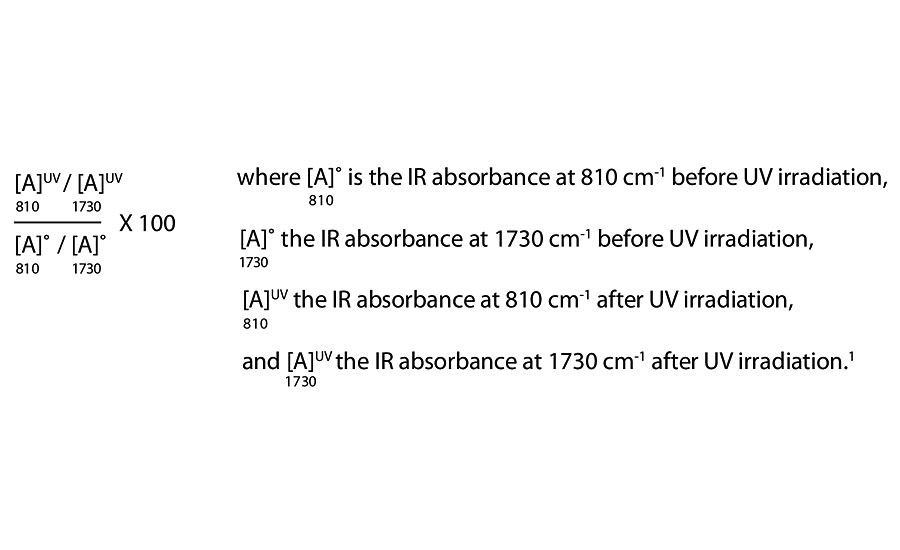
QUV Resistance
A 4-mil drawdown was made on a white ceramic tile, air dried for 10 min, then force dried for 10 min at 50 C. Cure. We waited seven days before testing. The CIELab color data was recorded for each tile using a BYK Gardener color-guide sphere. The 60 gloss was recorded for each tile using a BYK Gardener micro-TRI-gloss meter. The tiles were placed in the QUV cabinet with 340 UVA bulbs. The cabinet was set for 4 hrs of UV light followed by 4 hrs of condensation. These cycles were run for 4,000 hrs. We reported color change (delta E) and gloss loss, as can be seen in Figure 9 and Figure 10.
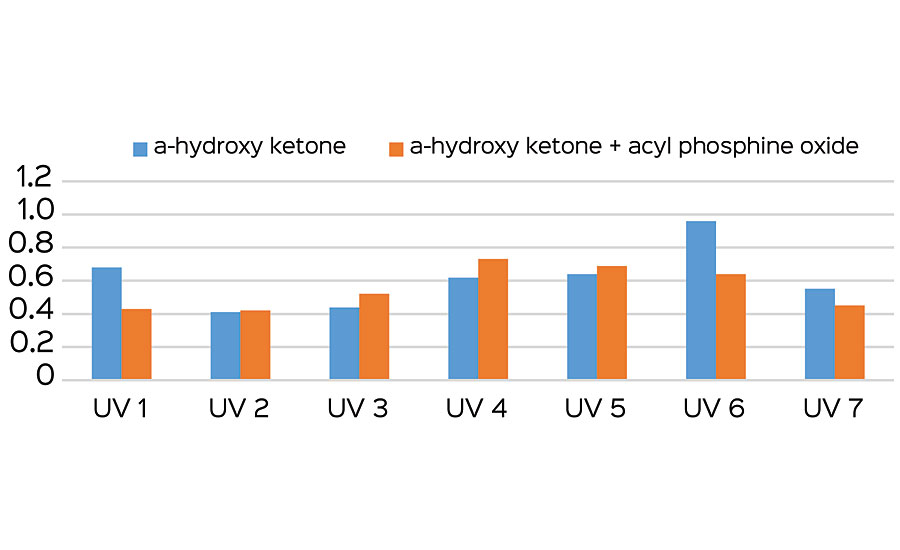
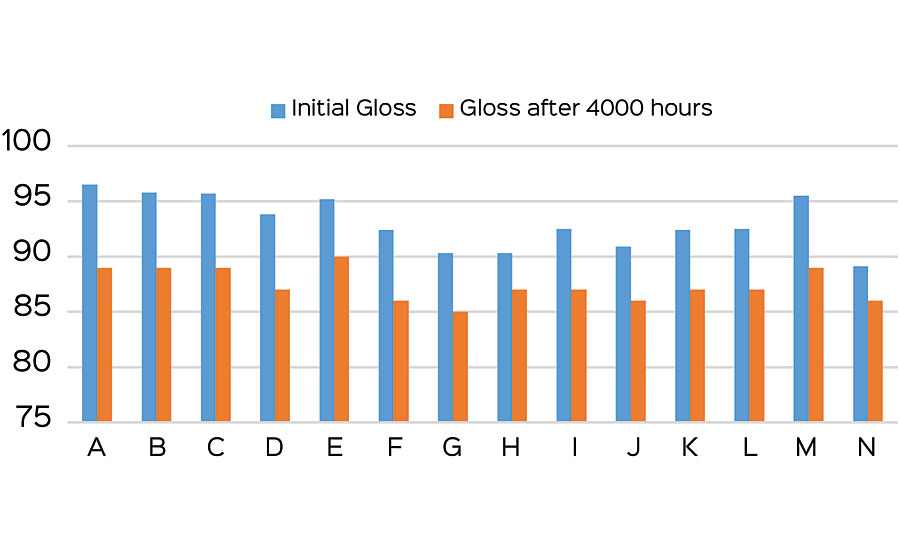
Discussion
All samples showed excellent QUV results with minimal gloss and color changes after 4,000 hours of exposure. The addition of acyl phosphine oxide photoinitiator did not impact the properties of the coatings. In Phase 2 testing, only alpha hydroxy ketone photoinitiator will be used. UV 3 was eliminated from the study due to production difficulty. UV 4, UV 5 and UV 6 were eliminated from the study due to low cure response and hardness. UV 1, UV 2 and UV 7 were included in Phase 2 testing.
WB UV Exterior Wood Applications, Phase 2
In Phase 2, coatings were evaluated according to the specifications outlined in the American Architectural Manufacturers Association AAMA 653-14 Voluntary Performance Requirements and Test Procedures for Organic Coatings on Wood and Cellulose Composite Substrates. This specification covers factory-applied coatings intended for service in exterior environments2. QUV resistance was repeated on poplar substrate. Coatings were formulated using traditional defoamers, surface tension modifiers, wax emulsion and rheology modifiers. The weight solids of the coatings was controlled with water. The formulations can be seen in Table 5.
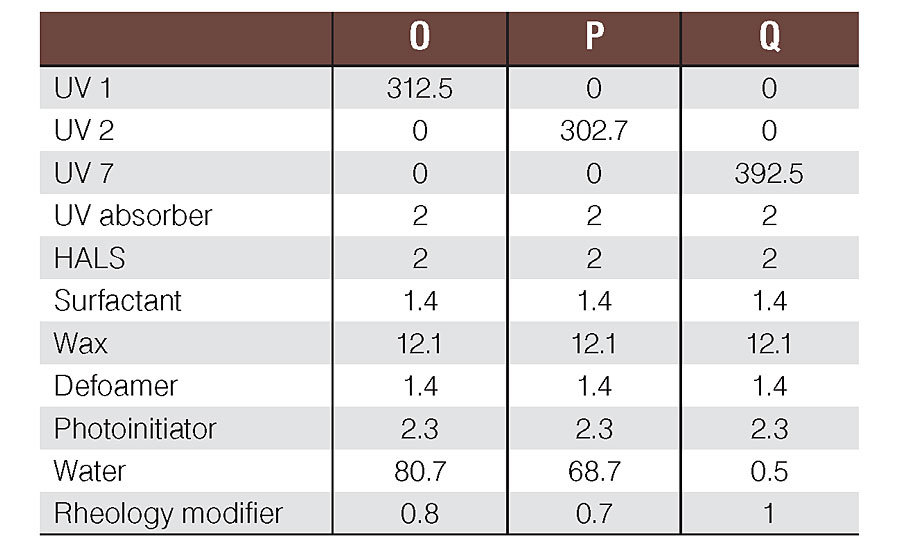
Panel Preparation
Unless otherwise stated in the AAMA 653-14 specification, all panels were prepared in the following manner:
1. Spray approximately 4 wet mils of coating over a 4 X
6-inch unstained southern yellow pine panel.
2. Air dry for 10 min.
3. Force dry for 10 min at 50 C.
4. Cure with a mercury lamp at 800 mJ/cm 2 .
5. Sand with a 3M Superfine Sanding Sponge.
6. Repeat steps 1-4.
Results
All properties were rated on a scale of 0-5, with 0 being complete film destruction and 5 being no effect on the film (Figure 11). Fifteen cycles of a cyclic humidity chamber/freezer test were performed. All coatings passed with no cracking or cold check. Figure 12 and Figure 13 show color and gloss retention for the coatings.
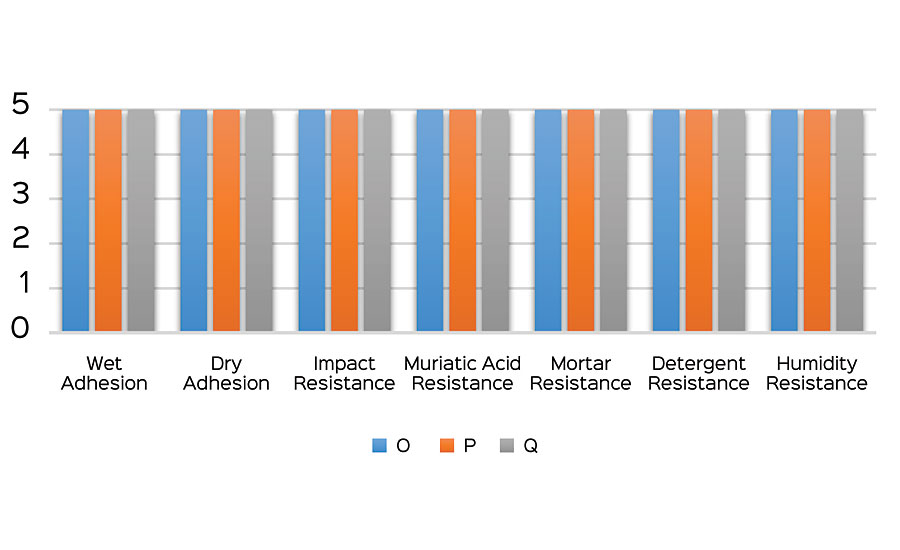
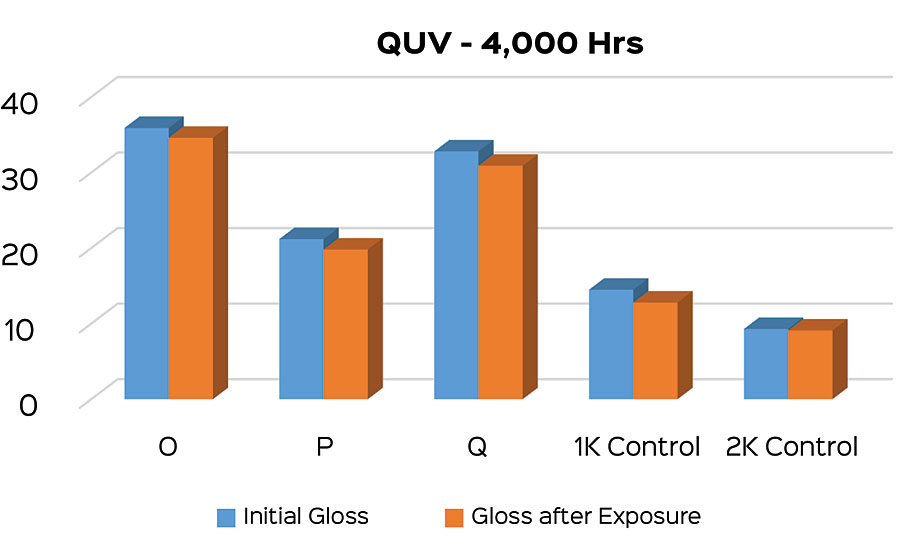
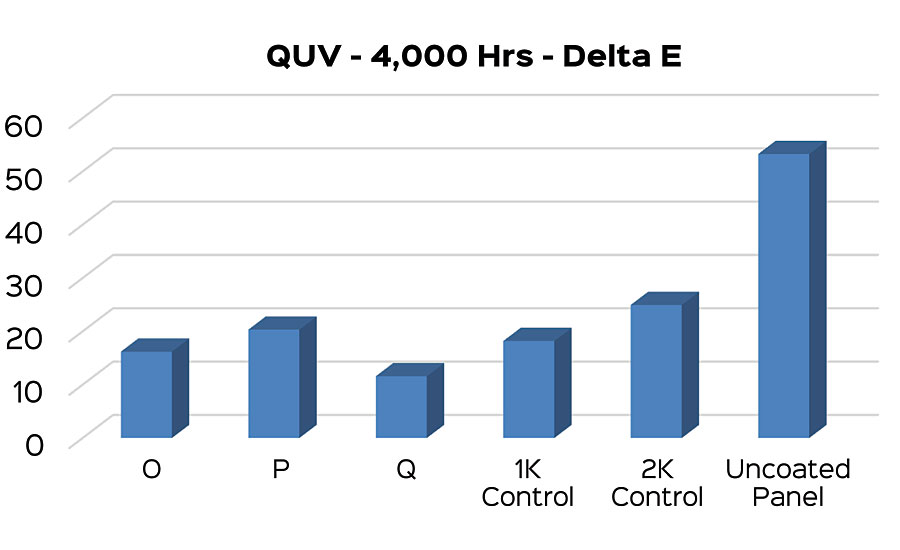
Discussion
All coatings passed the AAMA 653-14 tests. Gloss retention was excellent on all coatings.
Controls performed poorly in QUV color retention. These products are typically used as a topcoat over a stain or pigmented basecoat. The stain/basecoat provides UV protection for the wood. This study examined clear, self-sealing topcoats over a very light-colored wood. The experimental samples all had good QUV color retention.
Conclusions
Coatings made from WB UV resins are excellent candidates for industrial wood coatings for both interior and exterior applications. They have very good chemical resistance and mechanical properties. They can be formulated at low VOCs and have low toxicity. They are viable alternatives to solvent-based chemistries.
References
1 Y.-J. Park et al. Journal of Adhesion Science and Technology 22 ( 2008 ) 1401–1423
2 www.aamanet.org
Looking for a reprint of this article?
From high-res PDFs to custom plaques, order your copy today!