UV Coatings on Plastics
Bringing Value to the Market

The use of plastics is increasing in our daily lives. In the automotive market, one third of auto components are already made of plastics as OEMs target to reduce a vehicle’s average weight by 10-15% in the coming years to enhance fuel efficiency and reduce their environmental footprint. For the beauty and skin care market, over 70% of cosmetics bottles and caps have adopted plastics (virgin, bio-based or recycle types) as the key substrates. The electronics and telecommunications markets have used plastics for decades as dominant substrates due to their ease of processing. As a result, there is a continuously growing demand for high-performance, high-efficiency and value-adding coatings for various plastic substrates. However, due to their low surface energies as well as their sensitivity to temperature and solvents, many plastics are difficult to coat, rendering the development of coating systems for such substrates challenging for formulators and raw material suppliers.
In that respect, energy-curable coating technology has already proven to overcome the limitations of conventional coatings by providing a higher overall performance of the cured coating including scratch, abrasion and stain resistance.
Energy-curable coatings are composed of acrylate functionalized resins (oligomers and monomers), which polymerize or cure instantaneously upon exposure to UV light or electron beam, thereby leading to higher production efficiency, energy cost savings and more compact, space-saving industrial lines. Energy-curable resins can be 100% solids materials or can be diluted with solvents for ease of application. Water-based UV systems exist as well, but are not the subject of this article.
Since coatings on plastic parts are mostly spray-applied, solvents are used to reduce viscosity. Since solvents contain VOCs, they should be limited as much as possible. Developments in low-viscosity, energy-curable oligomers allow the reduction or even elimination of solvents for spray applications.
This article will demonstrate how to formulate UV coatings for:
- UV solvent-based clear, matte and piano black coatings for automotive interiors;
- UV solvent-based metallic monocoat for 3C (Computer, Communication and Consumer Electronics) and cosmetic applications; and
- 100% UV clear coatings for spray applications on plastic substrates.
UV Solvent-Based Coatings for Spray Application
Radiation curing technology is increasingly used to coat a wide range of plastic substrates in automotive, cosmetic packaging, audio/video and many other applications. If the formulated product is applied directly on to the plastic substrate, adhesion to the surface is of course a key characteristic.
Coatings for the above mentioned applications are subject to very demanding tests designed to assess whether or not they are suitable to meet the industry’s demand for high-performance coatings, delivering high scratch, abrasion, chemical, stain and even boiling water resistance.
High resistance properties are obtained through high-crosslinked systems typically using oligomers and/or monomers with high acrylate functionality. However, high crosslinking density may result in poor adhesion. It is therefore key to find the best trade-off between requirements.
Solvent-Based UV Clear Coating for Automotive Interior
In the past few years, there has been a strong drive in the industry to switch from die casting metals to plastics in automotive interiors, as the latter allows, amongst other things, the reduction of the overall vehicle weight, which contributes to reducing fuel consumption and CO 2 emissions, while delivering great and different aesthetic effects. With this growing interest in plastics, automakers are looking for coatings on plastics that offer performance, robustness, good haptics and aesthetic effect, as well as better productivity. Energy-curable coatings tick all those boxes in the sense that they allow both OEMs and suppliers (Tier 1 and 2) to benefit from improved scratch, abrasion, stain and chemical resistance; as well as increased productivity thanks to an almost instantaneous cure when exposed to ultraviolet light.
allnex has recently developed a new aliphatic urethane acrylate to respond to the challenges of the automotive interior industry. To formulate a UV-curable coating, this urethane acrylate was further blended with a high-Tg monomer, hexane diol diacrylate and a hydroxy alkyl phenome as photoinitiator. For spray application, a solvent mix was used to bring the formulation to a viscosity suitable for spraying. At 70% solids, a viscosity of 40 mPa.s (25 °C) was obtained.
The formulation was applied on different plastic substrates: ABS, PC and ABS/PC. A wet film was applied such that after solvent flash off (5 min at 60 °C), a dry film thickness of 20 g/m² was obtained. For the UV curing, an energy level of about 2,000 mJ/cm² was used. Resistance properties were only tested in case the coating showed full adhesion to the substrate. Sun lotion and hand cream tests according to VW PV3964 were used as reference for testing, as these represent some of the most stringent tests to pass together with humidity resistance according to VW TL 226.
As shown in Table 1, the formulation based on the new tetra-functional urethane acrylate offers good adhesion on a variety of substrates and can pass all the chemical resistance tests including humidity resistance on PC, which is often difficult to obtain. It indicates that all the basic requirements for automotive interiors can be met.
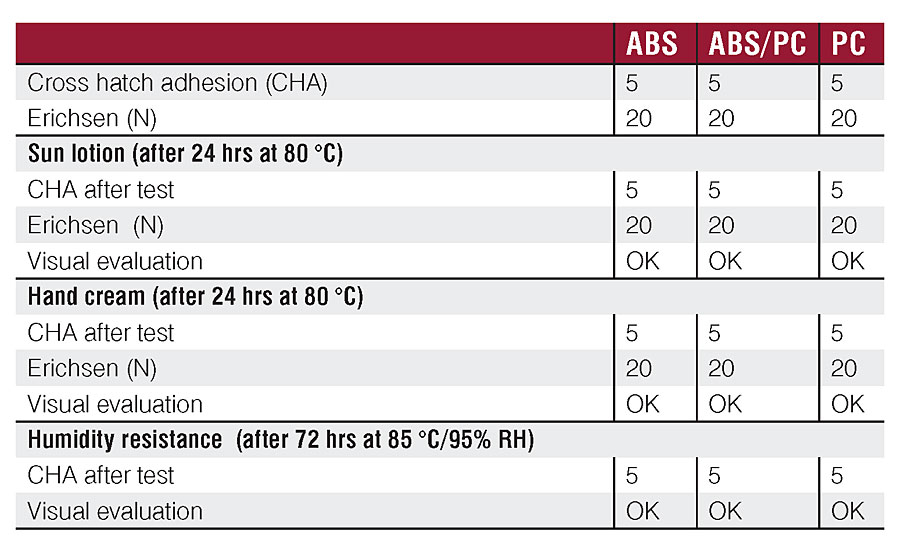
UV Solvent-Based Matte Coatings (for Automotive Interiors)
Often, for aesthetic and sometimes safety reasons, a matte surface is preferred over a high-gloss coating. The challenge for matte coatings is to keep good scratch and other resistance properties. In Table 2, formulations at 70% solids with a viscosity of 40 mPa.s (25 °C) are given. It was necessary to adapt the filler content (matting agents etc.) in function of the substrate; other and more matting agents were used for the coating on polycarbonate to reach a gloss below five at 60°.
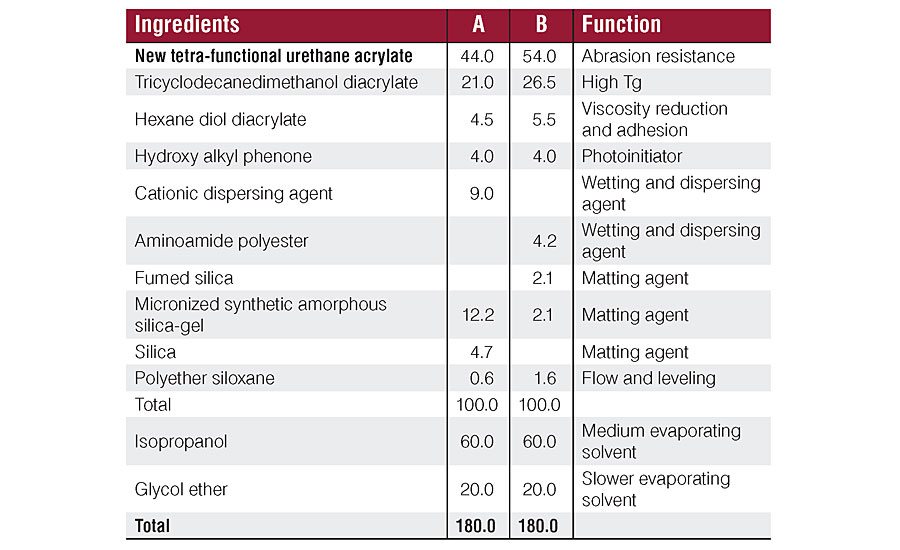
Results on chemical resistance and humidity resistance show that with a radical curable resin solution, automotive interior requirements are met without any increase of gloss or surface attack.
UV Solvent-Based Piano Black
A key surface effect for interior and exterior automotive trim components – such as trim spears on the instrument panel, central console surrounds and door trim – is glossy “piano black”, in reference to the color used on black piano keys.
While the popularity of piano black continues to increase due to its attractive appearance, it does have some disadvantages. Due to its high-gloss finish, surfaces coated in piano black often show fingerprint marks and are highly susceptible to scratches.
In the coatings industry, using oxidized fine particle carbon black pigments is the key to deep jet black coatings. The automotive industry requires the highest jetness black pigments and a bluish undertone. Small particle size carbon blacks fulfil these requirements. However, in UV-curable coatings, carbon black absorbs UV light, reducing curing. The finer the particle size, the more it will absorb UV. The challenge is therefore to find the best compromise between jetness at a given layer thickness and complete UV cure of the coating, optimizing performance. Two different pigments were evaluated: a pigment black 7 (PB 7) with a particle size of 47 nm and a relative tint strength of 88% (ASTM D 3265), and a pigment black 6 (PB 6) with a particle size of 95 nm and a relative tint strength of 26%. Finally, the best compromise could be found by using PB 6. In Table 3 a solvent-based UV formulation is given with 70% solids at spray viscosity (45 mPa.s at 25 °C). The carbon black (PB6) concentration is 3.2 % on solids.
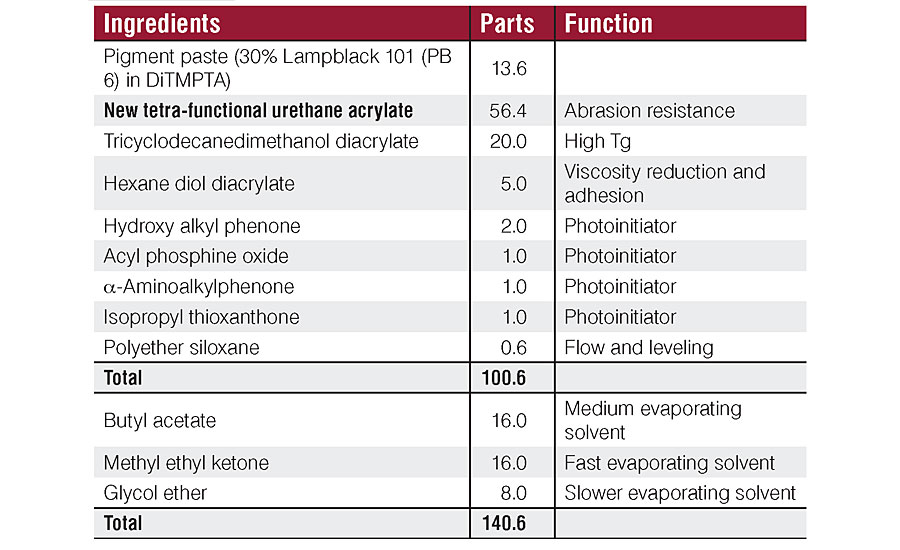
The formulation was applied on different plastic substrates: ABS, PC and ABS/PC. A wet film was applied such that after solvent flash off (5 min at 60 °C), a dry film thickness of 15 g/m² was obtained. For the UV curing, an energy level of about 2,000 mJ/cm² was used. Best results were obtained by combining a Ga lamp (deep cure) with a Hg lamp (surface cure).
The adhesion based on this formulation was good on all substrates. Erichsen (scratch/adhesion) was at the limit but increased a bit after the chemical testing, probably due to an extra thermal “treatment”. Coating surfaces were not attacked.
The formulation shows a good piano black effect and adheres to all the three type of substrates that tested. It passed also the boiling water resistance (60 min at 80 °C) and humidity resistance (72 hrs at 80 °C, 95% RH) tests.
UV Solvent-Based Metallic Monocoat
Metallic colors, especially silver, are popular, giving an added market value to plastic parts and enclosures like office and home appliances, consumer electronic (audio, video, mobile phones, cameras) and faucets, etc. Metallic paints are typically made with solvent-based conventional thermoplastic acrylic (TPA) or two-component polyurethane (2KPU) metallic basecoats (e.g. containing aluminum flakes). In some cases, a clear UV topcoat is applied in order to improve the durability, scratch and chemical resistances.
Solvent-based (SB) UV formulations were developed for this type of application to help circumvent the following challenges:
- Obtaining adhesion on the substrate, meaning also limiting the coating shrinkage upon cure by adequately selecting oligomers and monomers. The coating should be on top to have enough crosslinking density to provide chemical and mechanical resistances (e.g. mobile phone coatings).
- Ensuring complete UV curing of the bottom layer, as the metallic pigment can strongly interfere with short-wavelength UV light, by adding long-wavelength-curing photoinitiators such as mono acyl phosphine oxide (TPO). A surface-curing photoinitiator needs to be added to guarantee perfect surface cure and to reduce the oxygen inhibition.
- Metallic pigment orientation. The metallic pigment orientation effect of UV oligomers and monomers is limited due to their low molecular weight; monomers especially should be limited in quantity. Aggressive monomers should be avoided as they attack the metallic pigments and change their tone.
- Stability of metallic pigment-based formulations is low and requires good in-can stabilizers (radical scavengers).
- Metallic coatings can show limited abrasion and hot water resistance.
To obtain a good metallic pigment orientation, it is important that the solid content of the formulation is not too high. In Table 4, a solvent-based UV formulation is given with 38% solids at spray viscosity (15 mPa.s at 25 °C). The metallic pigment concentration on solids is 8.6%.
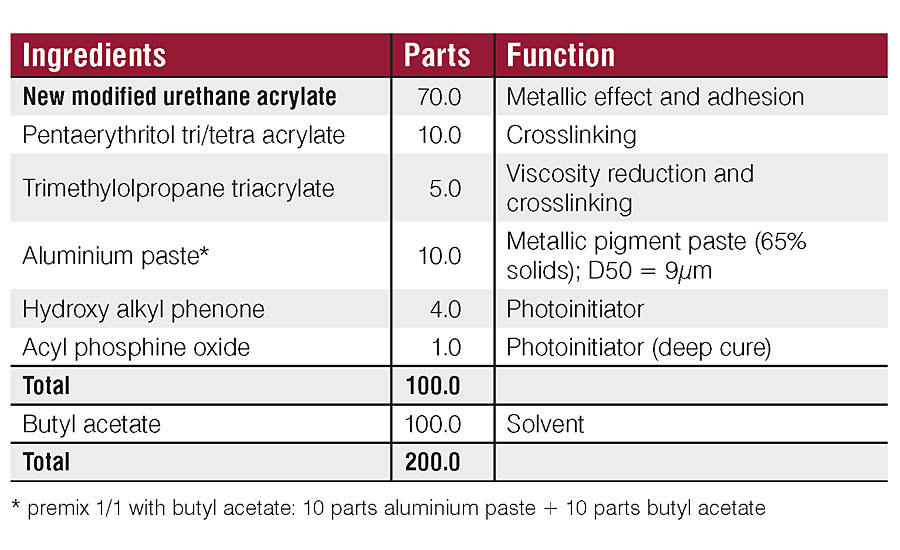
The formulation was applied on different plastic substrates: ABS, PC and ABS/PC. A wet film was applied such that after solvent flash off (3 min at 60 °C) a dry film thickness of 15 g/m² was obtained. For the UV curing, an energy level of about 500 mJ/cm² was used. The formulation showed a good metallic effect and adhered to all the three type of substrates that tested. It passed also the boiling water resistance (60 min at 80 °C) and humidity resistance (96 hrs at 80 °C, 95% RH) tests.
As mentioned earlier, abrasion resistance can be a challenge in metallic monocoats. The RCA Abrasion Wear Tester is often used as a standard to the automotive, appliance, mobile phone, plastics and coating industries. It uses an inexpensive roll of throwaway abrasion paper. Because of the small spot tested by the RCA Abrasion Tester, surfaces that are non-flat, or with small lettering or graphics can also be tested. An RCA of 300 is obtained, which represents a very good abrasion resistance.
100% UV Clear Coating for Spray Applications
In order to avoid or minimize the emission of VOCs, comply with new governmental environmental regulations and respond to the ever-stronger demand for sustainability solutions from customers in the coatings market, a low-viscosity hexa-functional urethane acrylate was developed. In Table 5, a 100% UV formulation sprayable at temperatures between 50 °C and 60 °C is given.
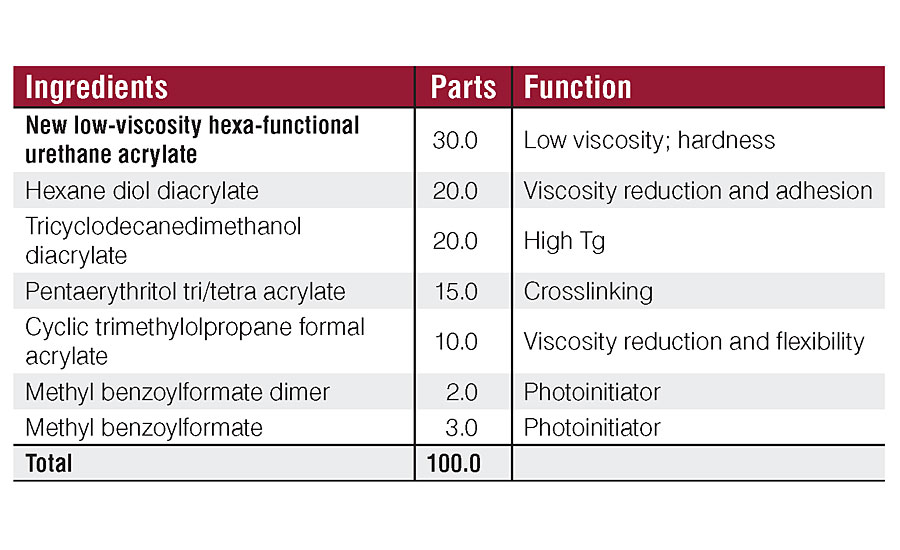
A dry film thickness of 20 g/m² was applied on different plastic substrates: ABS, PC and ABS/PC. UV curing was done using an energy level of about 1,000 mJ/cm². Resistance properties were only tested in case the coating demonstrated full adhesion to the substrate.
Adhesion was good on the different substrates used, and the formulation from Table 5 resulted in a medium hard coating (Persoz hardness of 254 seconds) with good abrasion and scratch resistance. “Boiling” water resistance (1 hr at 80 °C) and ethanol resistance were good. Only chemical resistance on polycarbonate remains a challenge, more particularly resistance to G1 solution typically used in evaluating cosmetic packaging.
Conclusions and Perspectives
allnex’s recent energy-curable resin developments respond to the increasing demand for suitable oligomers for coatings on plastics in different segments such as consumer electronics, cosmetic packaging and automotive interiors for different specifications and aesthetic requirements. Since these coatings are often spray-applied, solvents are being used to reduce viscosity. However, at allnex, development is ongoing to allow spraying at much higher solid content to lower VOC emissions for a sustainable environment. Low-viscosity oligomers are being developed for spraying 100% UV-curable coatings. Spraying at higher temperature of these 100%-solids coatings allows more formulation freedom to respond to market requirements.
Looking for a reprint of this article?
From high-res PDFs to custom plaques, order your copy today!