Get the Prediction of Long-Term Bonding Down to a Science
Paint the Whole Picture with Work of Adhesion and Interfacial Tension Measurements


Prefer the magazine experience? Subscribe to our digital edition here.


Identifying and developing compatible liquid-solid combinations is the key to effective wetting and adhesion. Evaluating the interaction between substrate and coating properties to see the overall picture of the wetting process will allow for the prediction of the adhesion and the long-term bonding of the coating. To do this, there must be a solid understanding of interfacial chemistry, or the physical and chemical conditions that exist when two phases interact.
Interfacial chemistry plays a significant role when working with coatings, specifically the surface tension (SFT) of liquids and the surface free energy (SFE) of solids. These parameters are often measured or calculated in order to optimize the adhesion properties and obtain long-lasting adhesion that will inhibit delamination and adhesion failures. Once these characteristics have been determined, the work of adhesion (WOA) and interfacial tension (IFT) between coatings and a substrate of interest can be deduced.
Measuring Surface Tension and Surface Free Energy
Looking at SFT of liquids first, it is important to understand its meaning and how it is determined. SFT is the result of imbalance forces due to greater attraction of the molecules at the liquid-air interface than the attraction of these same molecules to molecules in the air. There are several methods used to measure SFT of coatings, and the SFT range often dictates which method is utilized. The most common methods that have been used extensively in measuring equilibrium SFT are the Du Nouy Ring, Wilhelmy Plate and Pendant Drop methods. In addition to SFT results, the polar and disperse component of a given liquid can be calculated by measuring the contact angle of the coating liquids on a non-polar substrate such as polytetrafluoroethylene (PTFE) or polydimethylsiloxane (PDMS) substrate.
Next, the SFE of the substrate is calculated as a step in achieving optimized adhesion with the liquid of interest. Liquids that are often used in the calculation of the SFE are water (a polar liquid) and diiodomethane (a disperse liquid). This method of SFE measurement enables the polar and disperse components to be deduced and allows further critical calculations to be made. The procedure for determining SFE involves placing a drop of each liquid on the surface of the substrate, measuring the resulting contact angles of these drops in contact with the substrates, then using the contact angles to calculate the SFE of the substrate. The contact angles can then be used in different mathematical models such as the Owens, Wendt, Rabel and Kaelble (OWRK) models.
Once the SFT and SFE (polar and disperse) measure-ments are made, the WOA and IFT can be calculated. These parameters have an effect on the initial adhesion and longevity of the adhesion of coating liquids onto a given surface. Figure 1 shows a schematic diagram of two liquids (A and B) with the same SFT but with opposite polar and disperse component ratios. The polar and disperse components of both liquids and substrate are designated as the yellow and gray hands, respectively. When the liquid and solid come in contact, the liquid and the substrate with the highest interaction (liquid A) show the highest WOA and the lowest IFT. This suggests that liquid A and substrate combination will have a better initial adhesion, and over time will be more stable than liquid B, which has minimal interaction with the substrate, lower WOA and higher IFT.
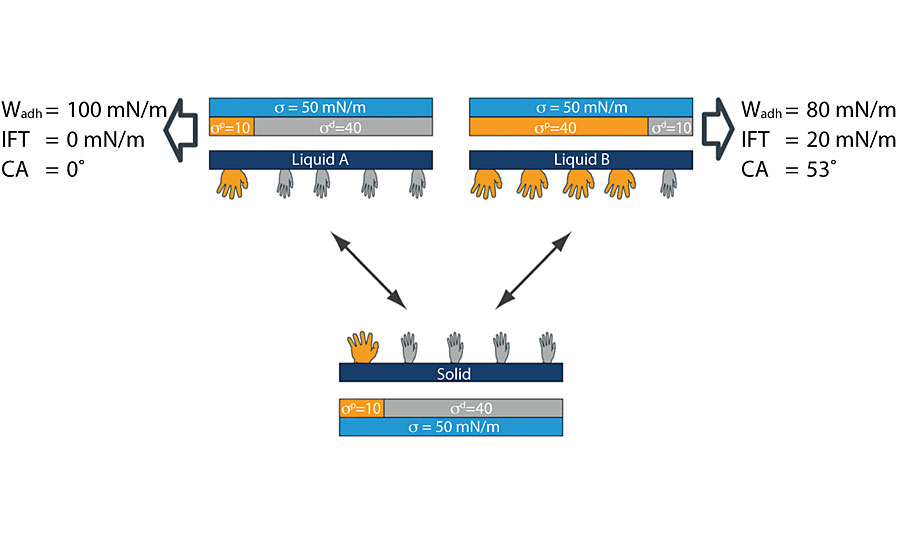
Optimizing Coatings
An example of the use of WOA and IFT to assess and optimize coatings on surfaces is coated fishing lines. One of the challenges with the use of fishing lines is delamination of coatings after multiple castings of the fishing line in the water. To evaluate the delamination cause and optimize the adhesion of the coatings onto the fishing line surface, characterization of the coating liquid, as well as the fishing line surface, needs to be performed.
To do this investigation, high-strength Kevlar fishing lines and coating liquids were obtained. The SFE and SFT, along with the polar and disperse components of the fishing line and coating liquid, were determined using water and diiodomethane contact angles and pendant drop measurement, respectively. In addition, the WOA and IFT of the coating liquid and fishing line were also calculated (Table 1). The results showed that the SFT of the coating was lower when compared to the SFE of the fishing line. This suggests that the coating will wet the surface of the fishing line. However, it also showed that the polar component of the SFE of the fishing line was very low, and the ratio of disperse and polar components was quite different from component ratios of the coating liquid. It was then decided to treat the surface using plasma.
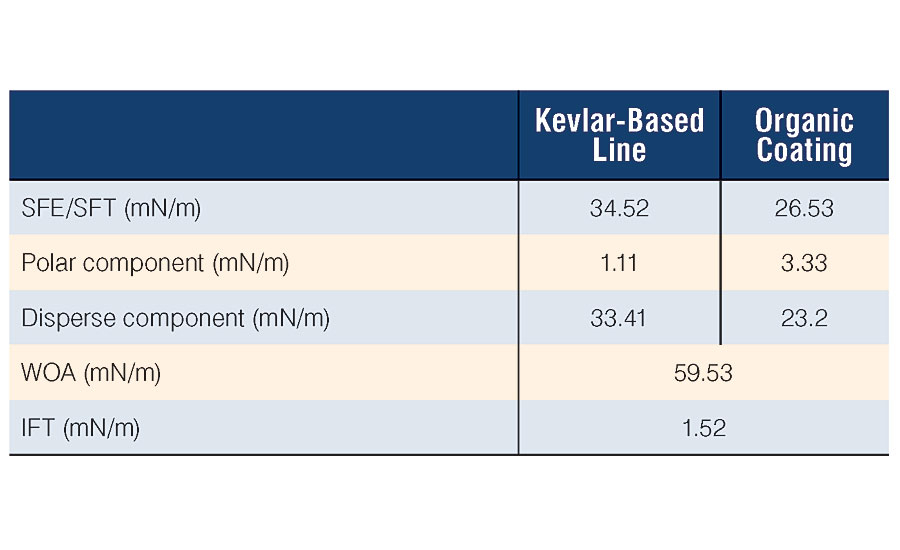
Table 2 shows the effect of plasma treatment on the fishing line surface. As expected, after plasma treatment, the polar component of the SFE of the fishing line and the WOA increased. A decrease in the IFT was also observed. At first glance, it showed that plasma treatment increased compatibility of the fishing line surface and the coating liquid with regard to surface polarity, increase in the WOA and decrease in the IFT. In application, however, it was seen that there was an increase in delamination of the coating for the fishing line that was previously plasma treated.
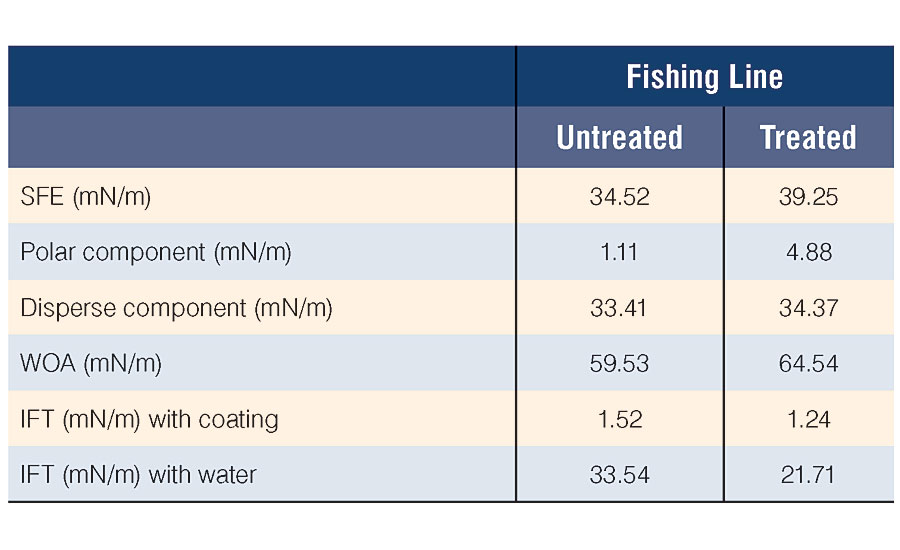
Interestingly, when the IFT between water and fishing line (before and after treatment) was calculated, it showed a decrease from 33.54 to 21.71 mN/m. This suggests that after plasma treatment, the fishing line had a greater affinity for water. This exacerbated the delamination of the coating owing to the ability of water to creep between the coating and the surface of the fishing line in the event of a crack in the coating. Casting the fishing line in the water created cracks where the water can then enter and cause peeling of the coating from the fishing line surface.
While at first glance it seems that plasma treating the fishing line surface would enhance the adhesion of the coating and longevity of the coating on the surface, it also enhanced the interaction of water with the fishing line surface and unintentionally boosted the delamination of the coating from the surface of the fishing line. In this case, plasma treatment of the fishing line was not the way to solve the problem. Instead optimization of the coating liquid achieved the desired adhesion. A reformulated coating was then made. Table 3 shows the properties of the new coating.
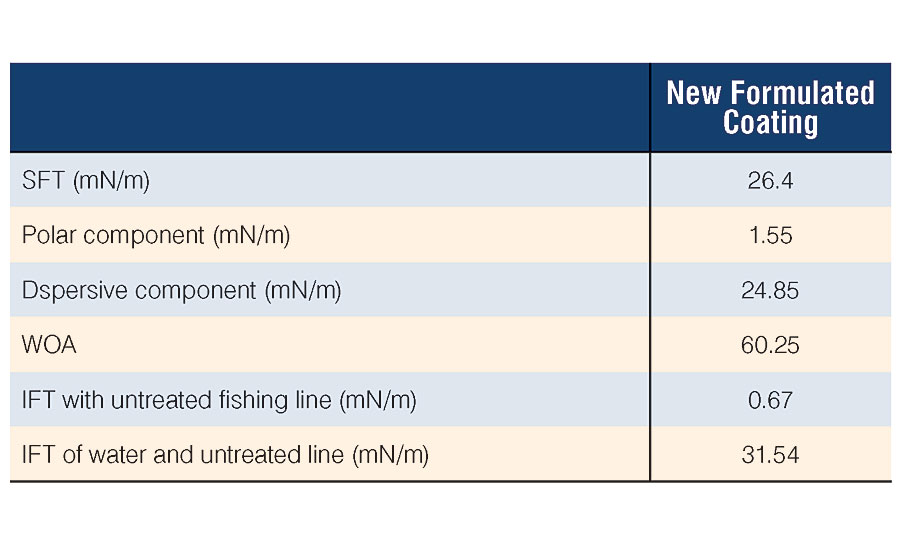
The WOA calculation in Tab. 3 showed that the new coating liquid had a high WOA and low IFT. In addition, since the new formulated coating gave better resistance to water, a decrease in coating delamination was observed even after more than 250 castings.
Conclusion
Calculating the WOA and IFT from the determination of SFT, SFE, polar and disperse components, enables prediction of good adhesion between substrate and an adhering liquid. The ADVANCE software from KRÜSS provides a single software platform to control its tensiometers, goniometers to profile liquids and solids. The ADVANCE software also calculates the WOA and IFT at the click of a mouse. The ease of adhesion calculation using a single software platform facilitates fast assessment, iteration, prediction and adhesion optimization.
References
1. KRüSS Application Report 232, Adhesion and IFT.
2. KRüSS Application Report 286, Determine How Surface Are: Quickly and On the Go.
For more information, visit www.kruss-scientific.com.
Looking for a reprint of this article?
From high-res PDFs to custom plaques, order your copy today!