A Clear Winner Against Rebar Corrosion in Concrete Repairs

Corroded reinforcement is the chief cause of concrete deterioration, which prompts subsequent repairs. For repairs to be sound, contractors must ensure adequate adhesion of new patch repair materials by proper preparation of exposed reinforcing steel. ICRI’s 310.1R-2008 “Guide for Surface Preparation for Repair of Resulting from Reinforcing Steel Corrosion” states that exposed reinforcing steel should be free of any materials such as concrete, dirt and corrosion products that could interfere with repair material adhesion, although a tightly bonded light rust on the rebar surface is usually not detrimental to the bond of patch materials. When it comes to tackling reinforcement surface prep and ongoing protection, CorrVerter® MCI® Rust Primer stands out among competitor materials with clear performance and application advantages to mitigate rebar corrosion.
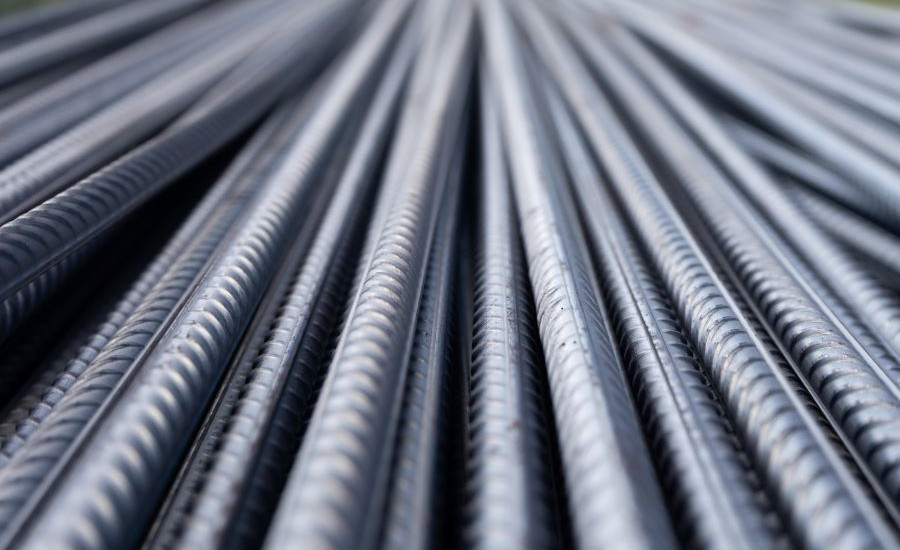
Resolving Existing Corrosion
Competitor rebar coatings containing corrosion inhibitor typically require a rust-free application surface to work properly. Abrasive or water blasting and intensive labor are usually needed to ensure corroded surfaces are completely clean. This is not necessary for CorrVerter MCI, which is recommended for application to rusty or poorly prepared steel surfaces where further corrosion protection is required and good surface preparation is difficult to achieve. The product is a unique formulation of chelating agents combined with a high-solids waterborne latex with extremely low water vapor permeability. This fast-drying, single-component primer converts surface rust into a hydrophobic passive layer and offers excellent protection against re-rusting of metal surfaces. Reinforcement coated with the rust primer has similar bond strength to concrete compared with uncoated rebar.
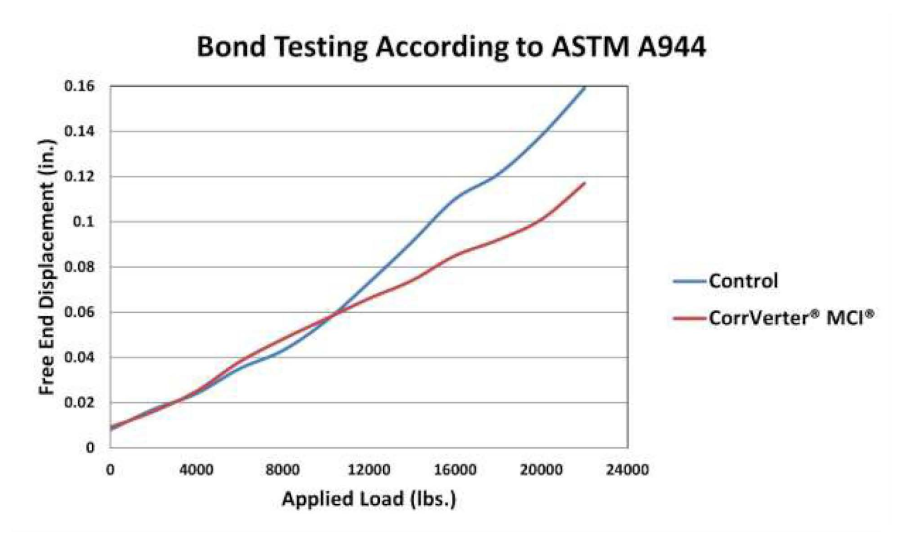
Preventing Future Corrosion
While competitor bonding agents list rebar corrosion protection as one of their benefits, actual performance is vague or reduced compared to CorrVerter MCI. One data sheet for a prominent cementitious epoxy resin states that it reduced corrosion rate by over 40% and tripled time to corrosion, without specifying a standard test method used in the study. Another bonding primer reports excellent corrosion resistance in 120 hours of salt spray testing according to ASTM B-117 (application recommended at 31 mils [787.4 µm] minimum). A third competitive bonding agent claims corrosion protection with no support data listed. In stark contrast, CorrVerter MCI Rust Primer data reports 500 hours of corrosion resistance in salt spray testing (ASTM B-117) at only 3-5 mils (75-125 µm) DFT (applied at 8.7-14.5 mils [217.5-362.5 µm] WFT).
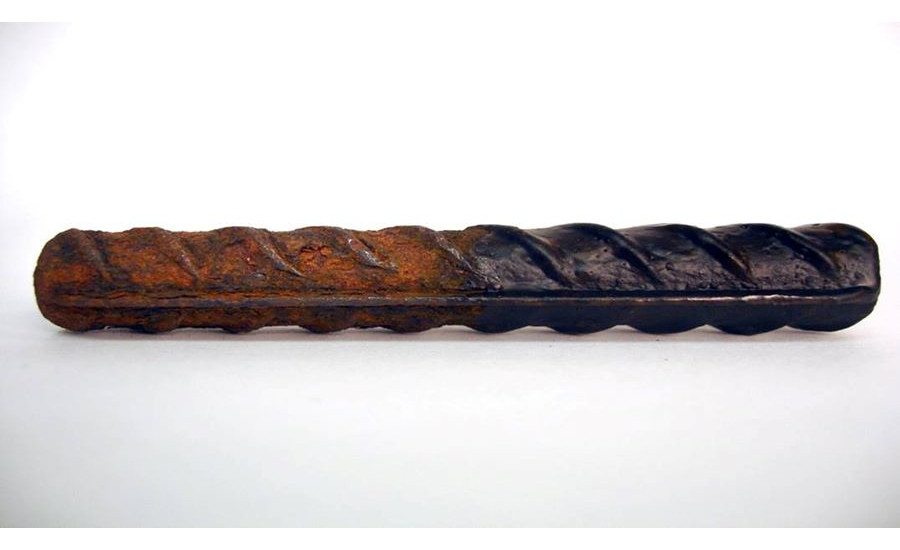
Choosing a Clear Winner for Convenience and Dependability
When it comes to dependable corrosion protection and easy surface prep, CorrVerter MCI Primer is the clear winner among competitive rebar primers and bonding agents. It offers engineers, owners, contractors, DOTs and government agencies a convenient, low-labor option when performing repairs on heavily corroded rebar and other metal surfaces. It converts rust quickly and provides ongoing protection without compromising bond strength. Contractors may rely on it as an integral part of a high-performance repair system that extends the service life of concrete structures.
To learn more, click here. All photos courtesy of Cortec® Corporation.
Looking for a reprint of this article?
From high-res PDFs to custom plaques, order your copy today!