Challenges in Formulating Water-Based Clear Sealers for Concrete

Solvent-based acrylic sealers for concrete have been used for many years and are considered by many to be the performance standard for sealers. The primary drawback to these solvent-based sealers is that they are very high in volatile organic compounds (VOCs), and industry regulations are driving sealer manufacturers to evaluate low-VOC water-based alternatives. Because the film formation mechanisms are different, there are differences in performance between most water-based and solvent-based sealers, however. Despite the differences in film formation, novel technology in polymers for water-based sealers gives an improved balance of properties that is commercially acceptable for today’s concrete sealers. The new type of polymer is compared to conventional concrete sealers for key performance properties.
Introduction
Although water-based acrylic emulsion sealers and solvent-based acrylic sealers are based on a similar acrylic polymer backbone, the performance of water-based emulsion sealers is often not equal to that of solvent-based sealers. For instance, film hardness and water whitening resistance are key performance properties, and water-based sealers typically underperform in these areas. Hardness of the dry film is important for mar and scratch resistance and is also particularly important in garage floor applications where the sealers are subject to pressure and heat from automotive tires. The water whitening is often seen when the dry, clear film is exposed to ponding water, usually after the first rain. The white discoloration is very visible on concrete as well as darker colored surfaces like pavers. Both hardness and water whitening are usually worse for waterborne sealers because of differences in the film formation process and the polymerization process.
Solvent-based sealers are dissolved in the solvent and form a film by solvent evaporation, so the polymer can have a glass transition temperature (Tg) well above room temperature, which gives good film hardness. Water-based sealers at low VOC typically have less film hardness than solvent-based acrylic sealers because the emulsion polymer particles are dispersed in water. These discrete particles, which must be coalesced using relatively low levels of volatile coalescent to form a film, often have a lower Tg and subsequently softer film than solvent-based counterparts. To meet the current California South Coast Air Quality Management District Rule 1113 VOC regulation for concrete sealers of 100 g/L, the total volatile coalescent that can be used is limited to about 10% on polymer solids in a clear sealer formulation. This level of volatile coalescent limits the minimum film formation temperature (MFFT) of the emulsion polymer to just slightly above room temperature.
In order to design a water-based polymer with both good hardness and good low-temperature film formation at low coalescent levels, core shell emulsion polymer particle morphologies and ambient temperature self-crosslinking can be used. The core shell morphology for polymers used in low-VOC coatings will have a very small, hard core and a much larger, soft outer shell. The hard, inner core does not participate in film formation, but has the effect of restricting the mobility of the softer polymer chains in the shell. This structure has the effect of raising the modulus of elasticity and increasing hardness properties.1 The softer polymer chains in the shell intermingle and coalesce with the shell polymer chains of other particles to form the film. After the polymer chains from the shell have coalesced, additional chemical resistance and some surface hardness can be built into the polymer film by using ambient-temperature-cure self-crosslinking monomers to form covalent bonds among the polymer chains of adjacent polymer particles.2
In addition to the challenge of formulating a sealer with good hardness properties at low VOC, the water-based coating must be formulated with good water whitening resistance. Water whitening is caused by water absorption into pockets of hydrophilic material that are present in the films of most emulsion polymers.3 These pockets are created because any free hydrophilic material in the coating will migrate into residual water between the polymer particles in the drying film. Surfactants from the polymerization process may help stabilize these pockets of hydrophilic material by creating reverse micelles with the hydrophilic end toward the center and the hydrophobic end outward toward the hydrophobic polymer particles. When the film dries completely, these pockets are usually quite small and are not visible in the dry film. If the film is exposed to water, the hydrophilic pockets absorb much more water than the polymer and they swell in size. As they reach a size of about 50 nm, the hydrophilic pockets begin to scatter light since the index of refraction for the hydrophilic material in the pockets is different from that of the polymer film. This light scattering gives the milky appearance referred to as water whitening. If the film dries out again, the hydrophilic pockets become smaller as they lose water and the film often changes from milky to clear.
Solvent-based acrylic sealers have very low levels of free hydrophilic material in the dry film and they are typically very good for water whitening resistance, while emulsion polymers typically have a much higher level of free hydrophilic species.3,4 Most of these free hydrophilic species in water-based clear sealers are surfactants or salts used in the emulsion polymerization process. Often water whitening of emulsion polymers can be improved by reducing total free surfactant. This can be done without sacrificing polymer stability by using smaller polymer particle sizes5 and polymerizable surfactants6 or acid functional monomers,7 which are attached to the polymer particles and are prevented from migrating into the pockets.
While polymer design of these emulsions is a major factor in water whitening, formulation and drying conditions can also affect water whitening. The sealer formulation can play a role since added surfactants or hydrophilic amines can also collect in the hydrophilic pockets. The water whitening is also dependent on the cure time before water exposure, the length of time that the film is soaked in water, the ambient temperature during cure and the porosity of the substrate.
Several polymers with different levels of water whitening resistance were formulated into clear sealers to look at the effect of drying, soak time and formulation on the water whitening. The polymers were compared to a solvent-based acrylic sealer. The four polymers in the study were:
- WB Polymer A, a hydrophobic styrene acrylic emulsion, Tg 20 °C, MFFT 7 °C. WB Polymer A has a high level of free stabilizing surfactant and typically has poor water whitening resistance.
- WB Polymer B, a self-crosslinking, all-acrylic emulsion polymer, Tg 27 °C, MFFT 12 °C. WB Polymer B has a moderate level of free stabilizing surfactant and has moderate water whitening resistance.
- RayCryl™ 1008, a self-crosslinking, all-acrylic core shell polymer emulsion, Tg 22 °C/98 °C MFFT 16 °C. RayCryl 1008 is specifically designed for hardness at low VOC and has a very low free surfactant level, giving very good water whitening resistance.
- SB Polymer D, a solvent-based acrylic resin, Tg 50 °C.
The water-based polymers (WB Polymer A, WB Polymer B and RayCryl 1008) were formulated into 32% volume solids sealers. The coalescent used was Dowanol DPnB™ (dipropylene glycol n-butyl ether), and the coalescent level was adjusted to give good film formation at 33 °C. The solvent-based acrylic polymer was evaluated as a 30% solids solution in xylene.
Test Methods
Gloss was tested using a Rhopoint Novogloss gloss meter. Measurements were taken by drawing down the clears at three wet mils on sealed Leneta cards, then allowing the clears to age overnight.
MFFT was tested using a Rhopoint WP Unit MFFT Bar 90. MFFT was read as the point where 75% of the film is not cracked.
A chemical spot test was run by coating the clears on concrete tiles, allowing them to dry for 24 hrs, then running a 1-hr spot test with gasoline, Formula 409 cleaner, grape juice, 10% sodium hydroxide and power steering fluid. Spots were rated for softening, discoloration and blistering on a 1-5 scale (5 best).
Block resistance was evaluated by drawing the sealers down at three mils wet film thickness on sealed Leneta cards. The drawdowns were dried for 1 day or 1 week, and 1.5-inch squares were cut from the card. The squares were stacked face to face and either placed in a 50° oven or at room temperature. Stacked squares were placed under a 1-kg weight on top of a #8 stopper to generate 1.8 pounds per square inch of pressure. The high-temperature block test was run for 30 min, and the room temperature block test was run for 16 hrs. Panels were pulled apart and rated on a scale from 1-10 (10 best) for film tearing or (in the case of no film tearing) by rating the noise in pulling them apart.
Sward hardness was read using a 5-mil drawdown on glass. Drawdowns were aged for 96 hrs before testing with a Gardco Model GS3 Sward Hardness Rocker.
Hot tire pick up resistance was run by etching concrete test tiles with Muriatic acid, then applying two coats of clear and allowing the tiles to dry for 1 week. After the cure time, a car was driven for 30 min at highway speed, then immediately parked on the test tiles. After 1 hr the car was driven off the tiles and the coatings were rated for darkness of tire marking, tire marking after cleaning with a damp paper towel and film tearing.
Water whitening resistance was tested by applying sealers either at .003 wet mils on black vinyl charts or by brushing on concrete test tiles. Test panels were dried either for 24 or 72 hrs, then soaked in deionized water. At specified time intervals, the Delta E color difference between the initial or soaked areas was recorded for the black vinyl charts. On the concrete tiles, the degree of water whitening was rated using a visual rating of 1-10 (10: no water whitening).
Results – Gloss and Chemical Resistance
Gloss and chemical resistance for sealers made with the four polymers are given in Table 1.
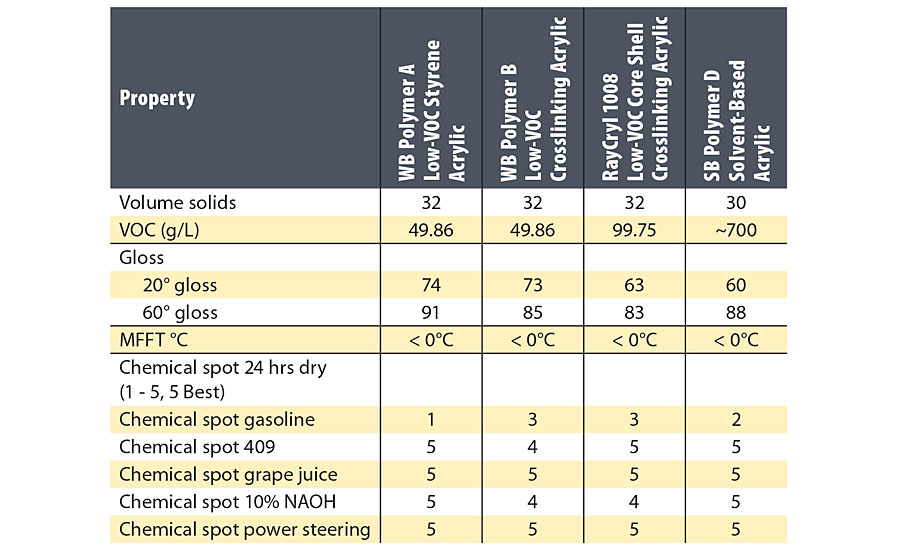
WB Polymers A and B were formulated at 50 g/L VOC, and RayCryl 1008 was formulated at 100 g/L VOC. The SB Polymer D had a VOC of 700 g/L. All four clear sealers had very good film formation down to 0 °C. Gloss of the RayCryl 1008 was slightly lower than the other polymers, possibly due to the core shell structure. The gasoline resistance of WB Polymers B and the RayCryl 1008 was slightly better than WB Polymer A. This improvement in gasoline resistance may be partly due to the ambient temperature crosslinking in WB Polymers B and the Raycryl 1008.
Results – Hardness
Hardness data for the four sealers is given in Table 2, and hot tire pick up resistance is shown in Figure 1.
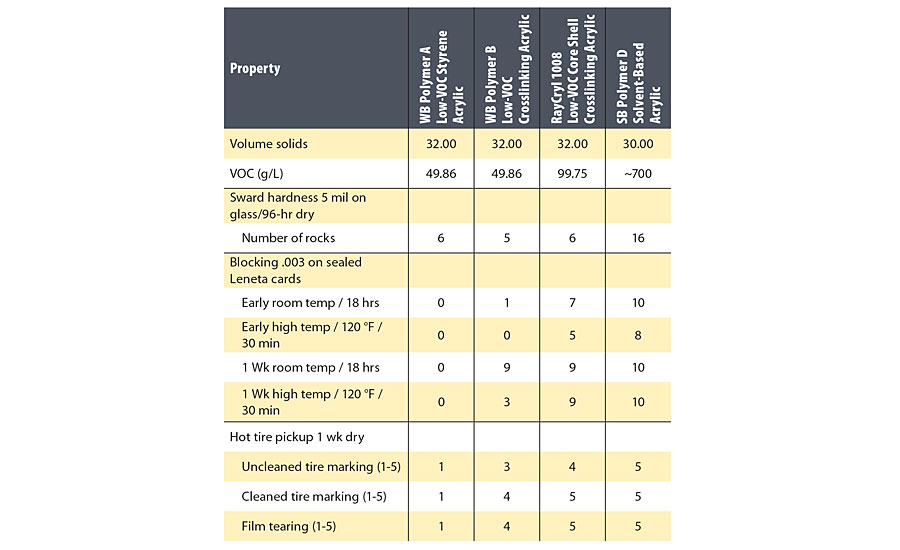
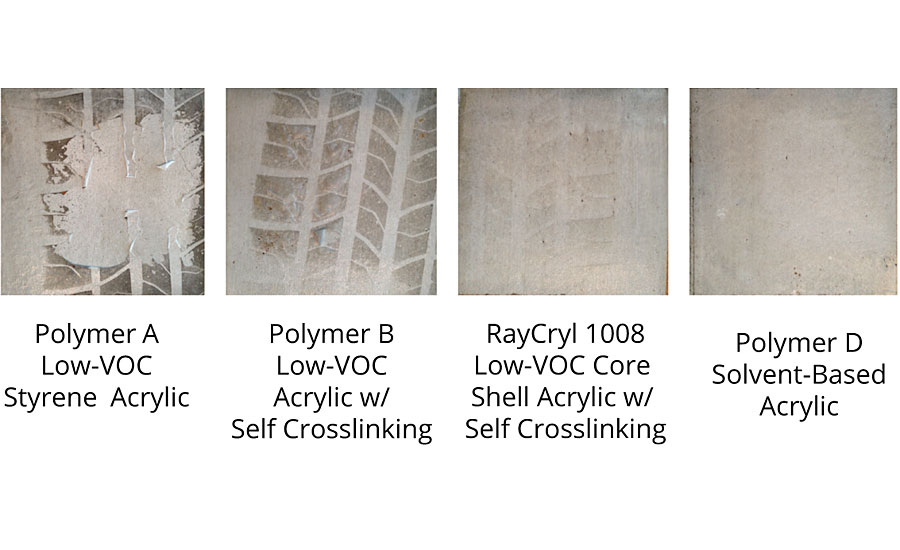
The Sward hardness of the three water-based sealers did not vary significantly and was lower than the solvent-based acrylic sealer, but the blocking and hot tire pick up test suggested that there were significant differences in surface hardness between the water-based polymers. The block resistance and hot tire pick up resistance of WB Polymer B was better at 1 week age than WB Polymer A, although the glass transition temperatures of the two polymers were similar. This may indicate that the ambient temperature crosslinking improved the surface hardness of WB Polymer B. Possibly because of the core shell morphology, RayCryl 1008 was better than WB Polymer B, and the early blocking and hot tire pick up resistance of RayCryl 1008 was just slightly worse than the solvent-based acrylic sealer based on SB Polymer D.
Results – Water Whitening Resistance
The water whitening of the sealers after 24 hrs dry is given in Table 3, and the water whitening at 96 hrs soak is shown in Figure 2.
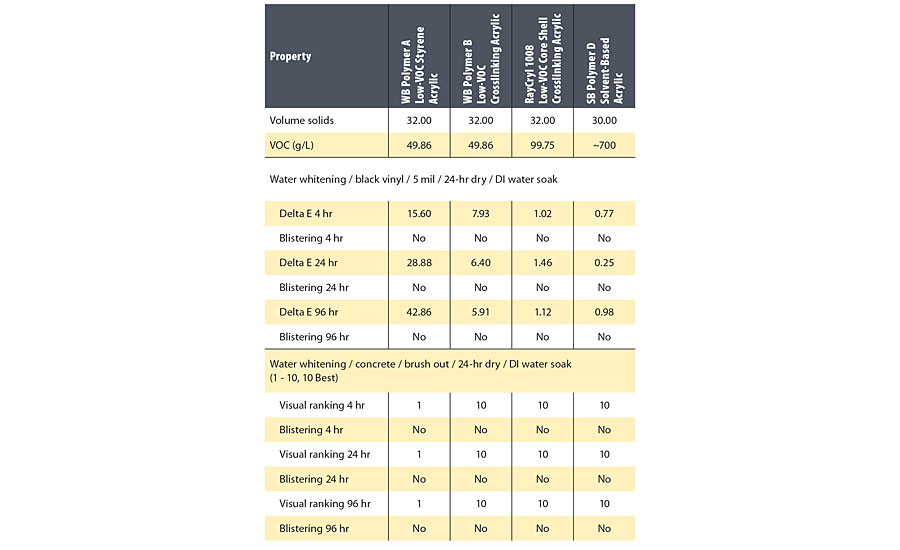
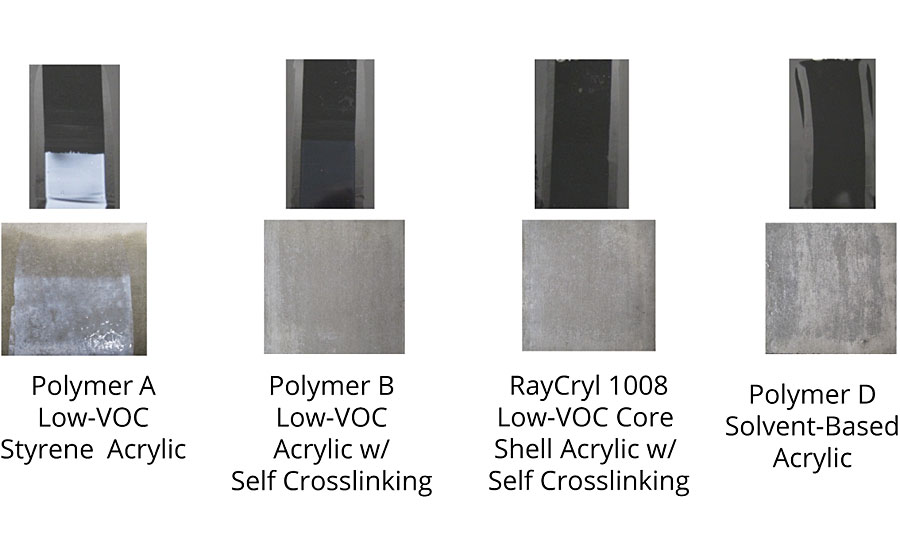
The hydrophobic styrene acrylic WB Polymer A was poor for water whitening resistance, indicating that water whitening resistance is not a function of the hydrophobicity of the polymer. The hydrophobicity of the film may have affected the water whitening in one important way, however. Possibly because of the hydrophobic backbone, the hydrophilic material was not able to leach from the film even on extended soak times, so water whitening did not improve on extended soaking. WB Polymer B had slight water whitening on black vinyl but no water whitening on concrete. The difference in water whitening between the two substrates may indicate that water and free hydrophilic material is being leached from the drying film and into the more porous concrete. RayCryl 1008 was very good for water whitening resistance at any dry time or soak time, possibly due to the polymer emulsion stabilizing system and ambient temperature crosslinking. The water whitening of RayCryl 1008 approached the water whitening resistance of the solvent-based acrylic sealer based on SB Polymer D.
While WB Polymer A was poor for water whitening at any cure time and RayCryl 1008 was good at any cure time, WB Polymer B had water whitening that changed depending on the length of time that the film cured before being exposed to water. Drawdowns of the sealer based on WB Polymer B were dried for either 24 hrs or 72 hrs and then tested for water whitening resistance at extended soak times on black vinyl charts (Figure 3).
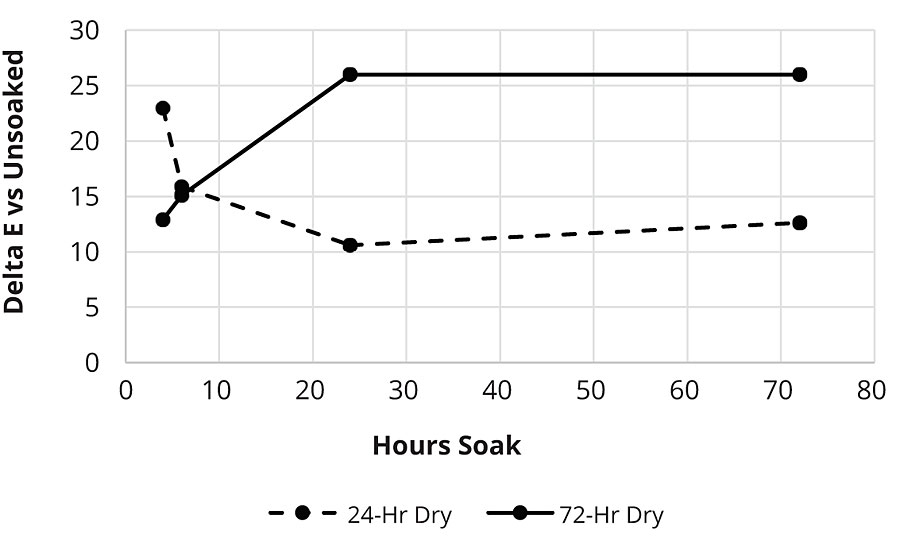
On black vinyl charts, WB Polymer B after 24 hrs cure was relatively poor for water whitening at 4 hrs soak but then improved on longer soak times. One possible mechanism for improved water whitening at longer soak times is if the hydrophilic material is being leached from the film. At 72 hrs dry time the water whitening was initially much better but then became worse than 24 hrs dry time and did not improve even with prolonged soaking. This may indicate that the film was much more water resistant on initial exposure to water, but that once water penetrated the film, the hydrophilic material was not able to be leached from the film. In the case of WB Polymer B, the loss of coalescent and completion of ambient temperature crosslinking after 72 hrs dry may have had the effect of trapping the hydrophilic material in the film, making the water whitening resistance worse.
The worse water whitening resistance in more highly coalesced films can be seen in a coalescent level study with WB Polymer B. The water whitening resistance of a sealer based on WB Polymer B at varying levels of -Texanol™ (2,2,4-trimethyl-1,3-pentanediol monoisobutyrate) or Glycol Ether DB™ (diethylene glycol monobutyl ether) coalescents (1 and 7 days dry time and 24 hrs soak) is shown in Figure 4.
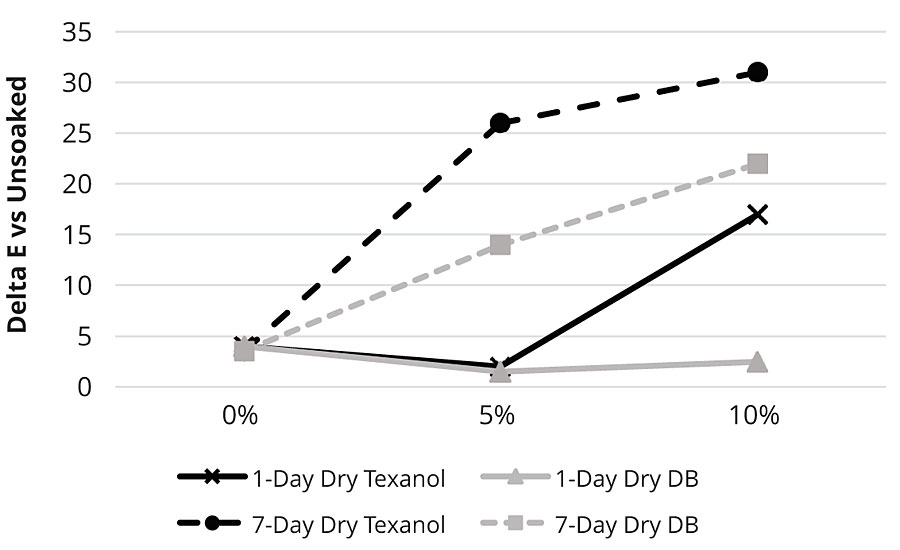
For WB Polymer B, higher coalescent was worse for water whitening, and longer dry times were also worse. The more hydrophobic coalescent (Texanol) had worse water whitening resistance than the more hydrophilic Glycol Ether DB. This may indicate that for some polymers, more coalesced films prevent water from leaching hydrophilic material from the film. At short dry times when the coalescent would be expected to still be present in the film, higher levels of Glycol Ether DB may be facilitating the loss of the hydrophilic material from the film.
Conclusion
Although it had a hydrophobic polymer backbone, WB Polymer A had poor hardness (block and hot tire pick up resistance) and poor water whitening resistance.
The self-crosslinking acrylic, WB Polymer B had improved block and hot tire pick up resistance compared to WB Polymer A, however it had water whitening resistance that varied, depending on the amount of cure time before soaking as well as the level of coalescent used. For WB Polymer B, the worse water whitening resistance at long cure times and high coalescent levels may be related to reduced levels of hydrophilic material being leached from the more coalesced film.
The performance of RayCryl 1008 was very good for hardness at 100 g/L VOC and showed excellent water whitening resistance under all drying conditions, and was nearly equal to that of the benchmark solvent-based acrylic film, SB Polymer D. The performance of RayCryl 1008 is thought to be due at least in part, to the core shell morphology and ambient temperature crosslinking, which gives good hardness at low VOC, and to the polymer stabilization, which reduced the free surfactant in the dry film to a minimum.
This paper was presented at the 2019 Waterborne Symposium in New Orleans.
References
1 Overbeek, A. Journal of Coatings Technology and Research 2009, 7, 1-21.
2 González, I.; Asua, J.; Leiza, J. Macromolecular Symposia 2006, 243, 53-62.
3 Liu, Y.; Gajewicz, A.; Rodin, V.; Soer, W.; Scheerder, J.; Satgurunathan, G.; McDonald, P.; Keddie, J. Journal of Polymer Science Part B: Polymer Physics 2016, 54, 1658-1674.
4 Jiang, B.; Tsavalas, J.; Sundberg, D. Progress in Organic Coatings 2017, 105, 56-66.
5 Starostin, N.; Harvey, S.; Carlson, G. Scanning 2008, 30, 78-86.
6 Aramendia, E.; Barandiaran, M.; Grade, J.; Blease, T.; Asua, J. Langmuir 2005, 21, 1428-1435.
7 Feng, J.; Winnik, M. Macromolecules 1997, 30, 4324-4331.
Looking for a reprint of this article?
From high-res PDFs to custom plaques, order your copy today!