Novel Nano-Dispersion for Sealers and Primers
Provides Excellent Penetration, Protection and Adhesion Promotion

Conventional emulsions are available in the market with particle sizes greater than 100 nm (140-200 nm), with several applications already consolidated in coatings. New nano-emulsions are being presented with particle diameter particularly below 70 nm.1 Below 30 nm, they are generally translucent or transparent because their particles are smaller than the wavelength of visible light.2 Nano-emulsions present a number of advantages compared to conventional systems. Some details can be found in the literature.1,3,4
One of the main advantages that we can attribute to nano-emulsions is the greater penetration and consolidation capacity, since smaller particles favor penetration and a larger number of particles increase the number of grafting sites.5
Archroma has developed a new terpolymer nano-emulsion called Mowilith® LDM 2801 with particle size distribution in the range of 35-50 nm. The product has a glass transition temperature (Tg) of 5 °C, a minimum film forming temperature (MFFT) below 5 °C, dry matter content about 33%, with viscosity below 100 cP, which facilitates its penetration. Even so, a minimum dilution is recommended to increase product penetration.
The company has followed its “Low Emission Concept” to develop this product. The concept covers seven ecological pillars: free of solvents, free of alkylphenol ethoxylates (APEO), free of toxic compounds, low odor, ammonia free, low volatile organic compounds (VOCs) and low formaldehyde. More ecological sealers and primers can be formulated with this innovative nano-dispersion without any need for coalescent additives in the formulation.
As previously mentioned, nano-emulsions present greater penetration capacity in porous substrates. In pinus wood, an analysis by optical microscopy reveals that there is penetration of about two cell layers using a conventional emulsion, whereas a 50 nm nano-emulsion reaches about three to six cell layers.
The difference is also visible in the formation of surface film. In conventional emulsions, film formation is concentrated primarily on the surface of the substrate, whereas for nano-emulsions the formation of the polymer film tends to concentrate within the surface of the substrate.
This penetration behavior is essential for the formulation and application of high-performance sealants and adhesion promoter penetration primers formulated with nano-emulsions.
Figure 1 demonstrates some of these benefits:
- Consolidation of loose particles and prevention of rupture;
- Prevents moisture migration;
- Reduction of substrate absorption for better application/coating performance (optimization of the amount used);
- Prevents efflorescence/migration of salts and alkalis. Extra protection to the substrate in coating;
- Promoter of adhesion of the coating.
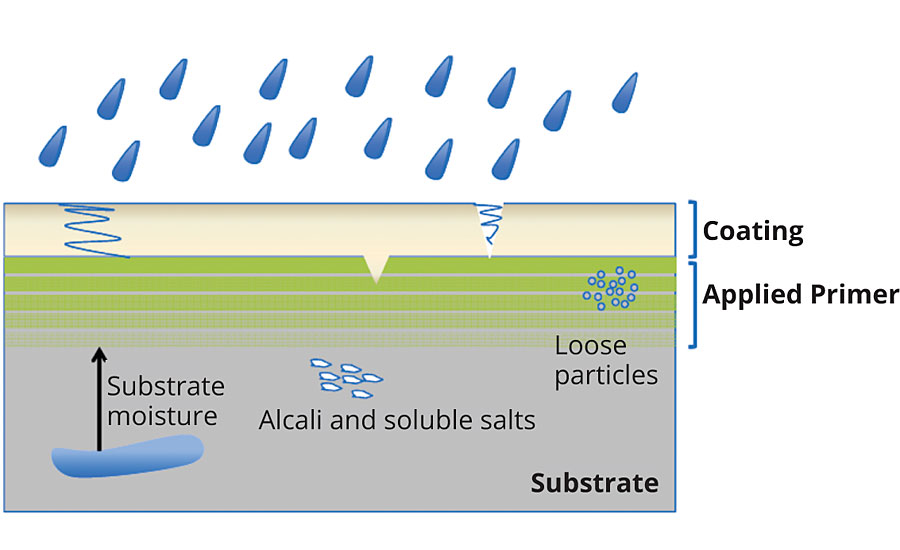
Sealers and adhesion promoter primers generally have the function of preparing the substrate to receive the top coating layers and promoting the adhesion of the final coating to the substrate in question.
The work described is focused on studies demonstrating the benefits in use of nano-particle dispersions described above, and extends to other substrates such as wood, masonry, concrete, fiber cement, tile, floors and plaster. Other materials and applications that seek these related characteristics can be exploited in order to increase product performance even with additives.
Experimental and Results
This study is divided into works that may represent the benefits described in each of the situations.
Protection Inside the Substrate (Not Only Superficially) – Absorption by Capillarity and Penetration Power
The capillary absorption test was performed with a conventional market sealer vs. Mowilith LDM 2801 in cylindrical gypsum blocks. The previously known gypsum rolls were partially immersed in a 1.5-cm layer of sealant solution of 10% solids, colored, for a period of 3 hrs.
After completion, the specimen was dried at 100 °C for 2 hrs until constant mass, and the migration of the polymer, its water repellency and the final mass of the absorbed polymer were analyzed. An interesting fact is that, after 17 min, the entire Mowilith LDM 2801 solution had already been absorbed.
Figure 2 demonstrates that there was actual capillary absorption of the nano-product by about 7 cm from the gypsum, whereas the conventional sealer formed a thin film only on the substrate on the product contacting surface.
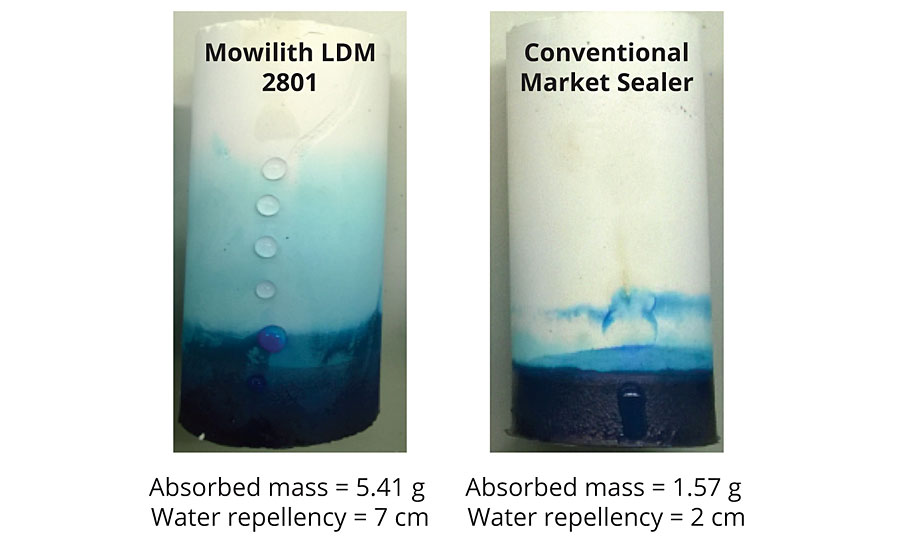
In order to evaluate the penetration difference of nano-particle products, the following test was performed. In a cylindrical block of gypsum, 1.0 g of a 10% solids content sealer was added in a 1-cm diameter tube, and the system was maintained for 2 hrs. The substrate was then dried and the penetration power was assessed by cross-section. It is seen from Figure 3 that the penetration difference of Mowilith LDM 2801 (1.1 cm) was about four times greater than the penetration of the conventional market sealer (0.3 cm).
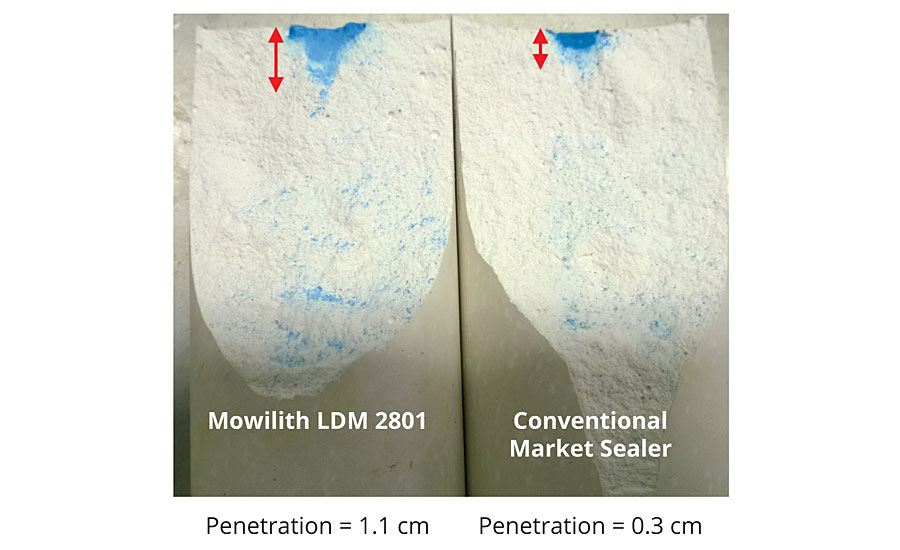
All the work done demonstrates that formulating high-performance sealants with Mowilith LDM 2801 adds values such as increased penetration and capillary absorption of the product on the substrate. There is no surface film formation, as this would be exposed to any superficial attack, and consequent failure of the coating and sealer. This penetration and formation of the film inside the substrate also favors the consolidation of loose particles and prevention of substrate rupture, favoring its mechanical strength and durability.
Potentiation of Adhesion-Promoting Effect and Water Resistance/Water Repellency
The work carried out below evaluates the adhesion-promoting effect after application of a sealer or finishing primer, Mowilith LDM 2801 (dilution 1 part product: 2 parts water) or without the presence of any treatment.
The evaluation was performed on a concrete substrate, through the adaptation of ABNT NBR 11003, Tintas - adhesion determination.6 It is important to mention that, even though it was not required, the two adhesion methodologies were performed: X-Cut and Grid Cut.
In all situations, after the application of the sealant or not on the concrete substrate, three coats of satin premium paint were applied. It was allowed to dry for 24 hrs to perform the adhesion test, from the last applied coat.
Figure 4 shows the adsorption behavior of a drop of water on untreated concrete substrate, with the treatment of a conventional sealer (Figure 6) and -Mowilith LDM 2801 (Figure 8). There is a sudden reduction of water absorption with any treatment used, however, for this purpose, the conventional sealer forms a shiny film on the surface while the nano-sealer forms a film inside the substrate, ensuring greater protection.
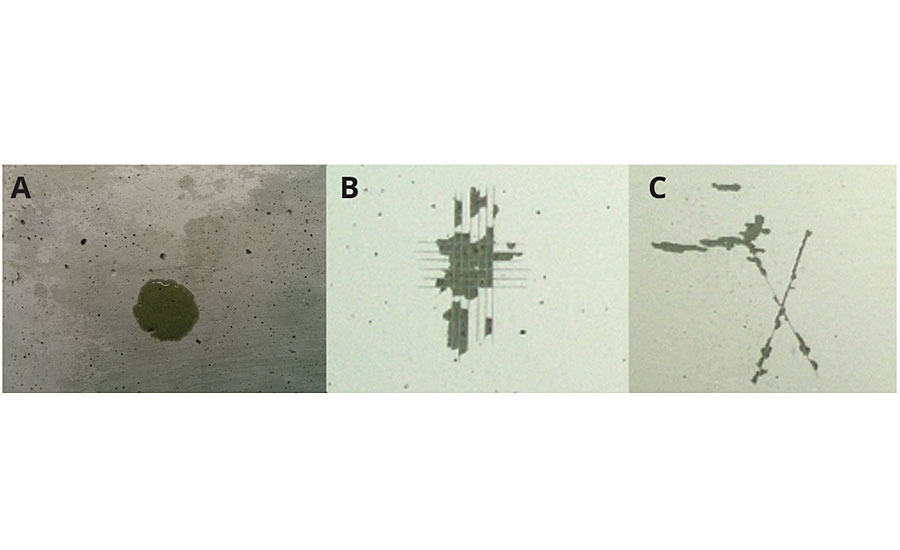
Figures 8-B and 8-C demonstrate the aggregate gripping power with the use of the nano-product. The conventional sealer (Figures 6-B and 6-C) also adds value when compared to non-pretreatment use (Figures 4-B and 4-C), but still lower than Mowilith LDM 2801.
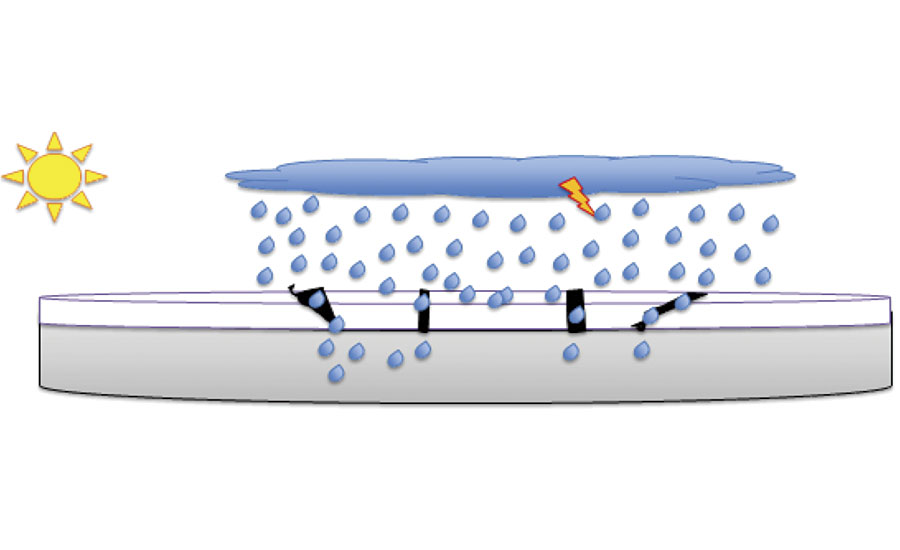
Figures 4 and 5 show that, in systems without pre-treatment, there is a deficiency in adhesion of the applied coating and substrate; the facing coating will leave the substrate vulnerable to any kind of weather.
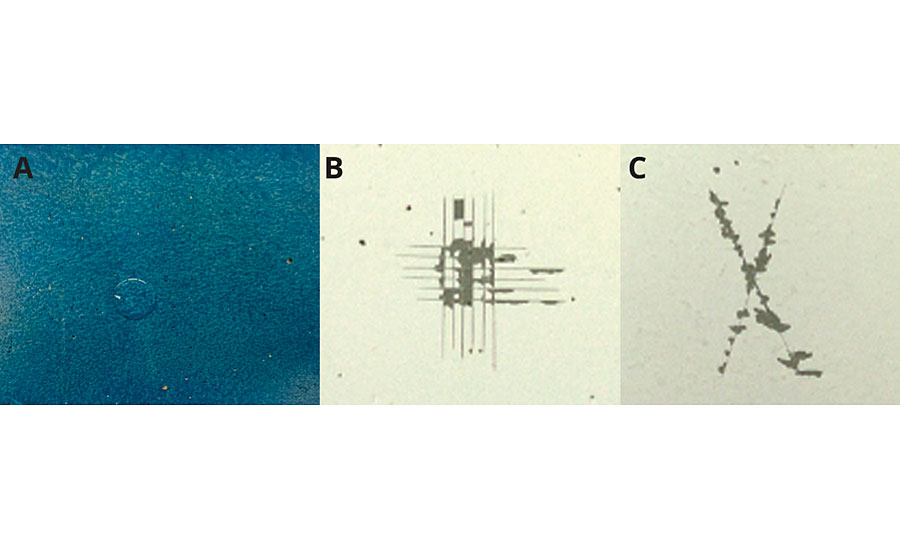
In Figures 6 and 7, the conventional sealer has the function of adhesion promoter. In this case, there is the formation of a superficial and shiny film of the sealer, which, because it is superficial, is exposed to any problem or deficiency together with the coating. If this occurs, the substrate will also be vulnerable to the weather.
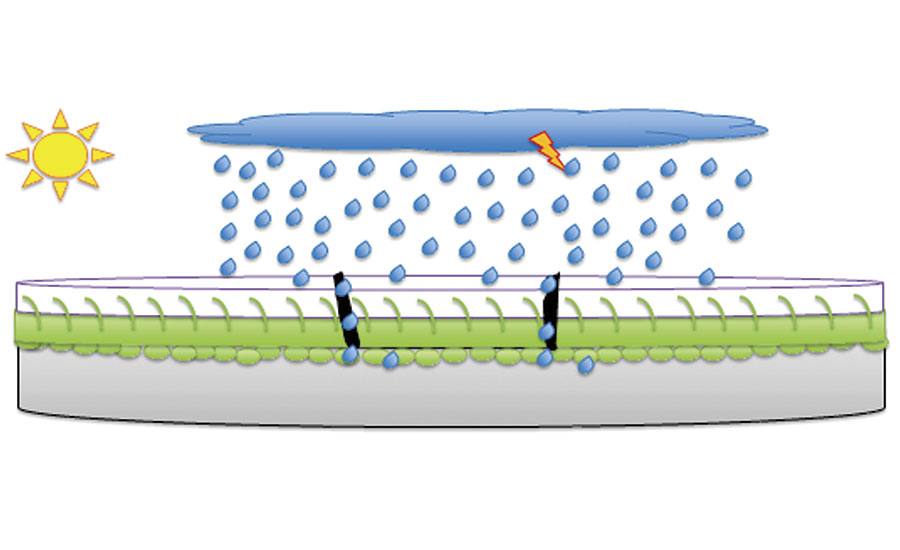
In Figures 8 and 9, it is seen that the use of the nanoparticle sealer ensures that a protective film is formed within the substrate and yet exhibits the adhesion promoter function. If there is any deficiency or problem in the coating, the film formed inside the substrate will still remain for the protection of the same. There will be greater protection and durability of the substrates.
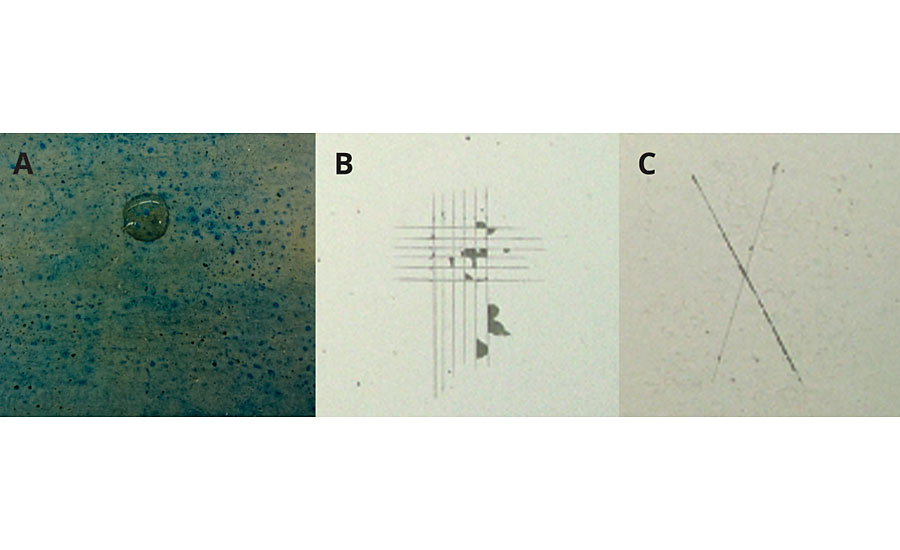
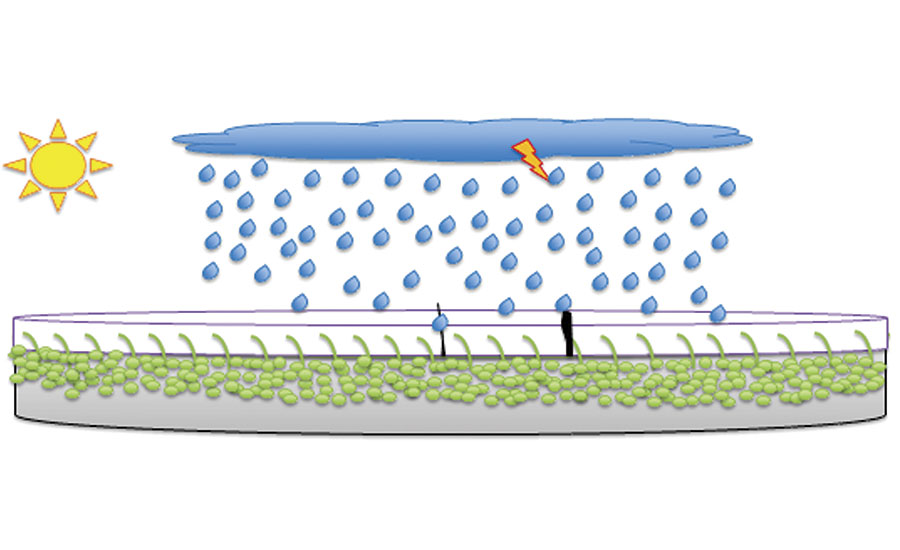
Thus, it is concluded that Mowilith LDM 2801, when applied as a primer for adhesion, confers an expressive gain of adhesion, with better performance compared to the traditional materials. Furthermore, it provides extra protection to the substrate in case of coating failure and reduces the water absorption of the substrate through water repellency.
Conclusion
Currently, the issue of durability and shelf-life of structures and surfaces is increasingly evident. In this context, this article sought to gather a series of experiments based on an advanced technology material in order to provide solutions to increase the longevity of these structures and surfaces. There are three main properties that govern the best protection for your substrates and are seen with sealers or high-performance primers formulated with the Mowilith LDM 2801 nanoemulsion: high penetration, adhesion promotion and water repellency.
References
1 Chern, C.S.; Principles and Applications of Emulsion Polymerization, Wiley, 2008; Daniel, J.C.; Pichot, C. (Eds.). Les Latex Synthétiques, Lavoisier, 2006; van Herk, A. (Ed.). Chemistry and Technology of Emulsion Polymerization, Blackwell, 2005.
2 McClamentis, D.J. Nanoemulsions Versus Microemulsions: Terminology, Differences, and Similarities; The Royal Society of Chemistry, Soft Matter, 8 (2012) 1719-1729.
3 Mader, A.; Antonietta, S. Nanolatexes: Applications in Building, Pitture and Vernici 86 (2) (2008) 31.
4 Colloidal Polymers, Elaissari, A. editor, Dekker 2003, Chapter 3, Ni, P.; Fu, S.; Preparations of Microlatexes Using Polymeric Surfactants or Mixed Surfactants; Chapter 7, Larpent, C. Microemulsion Polymerization, A Way to Synthesize Well-Defined Highly Functionalizes Nanoparticles.
5 Mader, A.; Schirò, A.; Brischetto, Pizzo, M.B. Interactions and Penetration of Ppolymers and Nanolatexes into Wood: An Ooverview, Progress in Organic Coatings 71 (2011) 123-135.
6 ABNT NBR 11003, Paints - Determination of Adhesion.
Looking for a reprint of this article?
From high-res PDFs to custom plaques, order your copy today!