Improvements in Anti-Corrosion Performance
By Integrating Graphene Nano-Platelets into Coating Systems

Protection of infrastructure from corrosion is essential in preventing costly failures, with risk to both human life and the structure itself. This is frequently achieved through the use of complex, multi-layered coating systems. Current organic coating systems designed for harsh environments are typically comprised of a number of different types of coating layers, each providing a different set of properties. A basic system usually consists of three layers, which may include a primer coat, an intermediate coat and a final top coat. Primer coats are typified by epoxy-based formulations containing a relatively high loading of a more anodic metal such as zinc (zinc rich), which provides a sacrificial protection to the metal substrate. Intermediate coats are usually formulated around a solvent/epoxy base with a pigment blend containing a relatively large fraction of micaceous iron oxide. The intermediate coat or tie coat serves to promote adhesion between the primer coat and the top coat layers. The intermediate coat may also provide a barrier-type protection against corrosive species such as water, ions or oxygen, slowing their diffusion to and from the metal surface, although it is recognized that there are some limitations to these barrier properties due to the permeability of organic coatings to such corrosive species. Finally, the top coat of the system is normally composed of a polyurethane or polysiloxane. These materials usually offer UV resistance in addition to any aesthetic finish.
A key component of these systems in high-risk environments where there is significant risk of corrosion is the zinc-rich primer. These primers have been widely used since the 1930s for the protection of steel structures. Unlike regular organic paints, they provide galvanic protection at edges or the places where the coating is defective. In the FHWA-sponsored “PACE” study,1 the coatings with zinc-rich primers performed best compared to other generic types of coatings evaluated under similar conditions. Zinc-rich coatings are described in a number of industry and military specifications. SSPC Paint 202 is an industry specification that categorizes zinc primers according to vehicle types. Type II coatings are the most common, involving organic vehicles such as epoxies and moisture cure urethanes.
The protection of steel by a zinc-rich coating is achieved mainly via two effects: the barrier effect imparted by the coating itself and galvanic action. The zinc particles in the coating provide the galvanic protection. Three conditions are essential for the galvanic process to occur on steel:
- Zinc particles must be in electrical contact with each other.
- Zinc particles must be in electrical contact with the steel.
- A continuous electrolyte must exist between the zinc particles and the steel.
The first two conditions are met by zinc-rich coatings when containing a sufficiently high zinc content. The third condition is fulfilled when a steel panel bearing a zinc-rich coating is wetted by a film of electrolyte such as a salt solution. The protective action of zinc-rich coatings may be broken down to two stages. The first stage is a relatively short period in which galvanic protection of the steel by zinc particles occurs. After this period in which the zinc is consumed, the galvanic action between the steel and zinc gradually disappears. The second stage is a long-term barrier protection that is attributed to (1) greater resistance of the coating to the permeation of aggressive species such as water, oxygen and salts because the pores in the coating are blocked by the zinc corrosion products and (2) inhibition of the steel surface by the zinc corrosion products.
The properties of graphene, a single layer of graphite, have been talked about for many years. In addition to high mechanical and electrical properties, it has a high aspect ratio, endowing the ability to function as a barrier additive. When incorporated into an organic coating system or host matrix, graphene nanoplatelets (GNPs) provide a highly tortuous pathway that acts to impede the movement of corrosive species towards the metal surface,3 a passive corrosion protection mechanism. In addition, very small additions of GNPs decrease water vapor transmission rates,4 indicating a barrier-type property, while some authors also suggest an electrochemical activity provided by graphene within coatings.5
Formulating a High-Risk-Environment System Using Graphene
The use of graphene nanoplatelets in combination with zinc has been proposed and shown to have both positive and negative impacts, depending on loading6 when incorporated directly in the zinc-rich primer. The efficiency of zinc-rich primers depends on several factors: zinc loading, effect of particle size and binder type.7 For this work, we tested graphene coatings in the intermediate layer, applied over a zinc-rich primer. The graphene-enhanced intermediate layer limits water ingress, while the zinc-rich coating provides sacrificial protection for the steel substrate. Such an approach has the benefit of managing the electrolyte reaching and activating the zinc while at the same time extending the life of galvanically active zinc and providing further long-term barrier protection. Ultimately, this work seeks to determine if the operational lifetime of the zinc-rich primer layer can be extended with an intermediate layer having GNP-enhanced barrier properties, potentially reducing the amount of zinc required in the primer layer.
Three different GNP-containing variants were prepared (Table 1), substituting commercially available GNP-containing dispersion additives for epoxy in a control primer formulation. The three GNP types tested were graphene nanoplatelets, reduced graphene oxide nanoplatelets and a combination of the reduced graphene oxide with an active corrosion inhibitor. Dry film thickness of the prepared coatings was in the range of 150-160 microns for the full coating system.
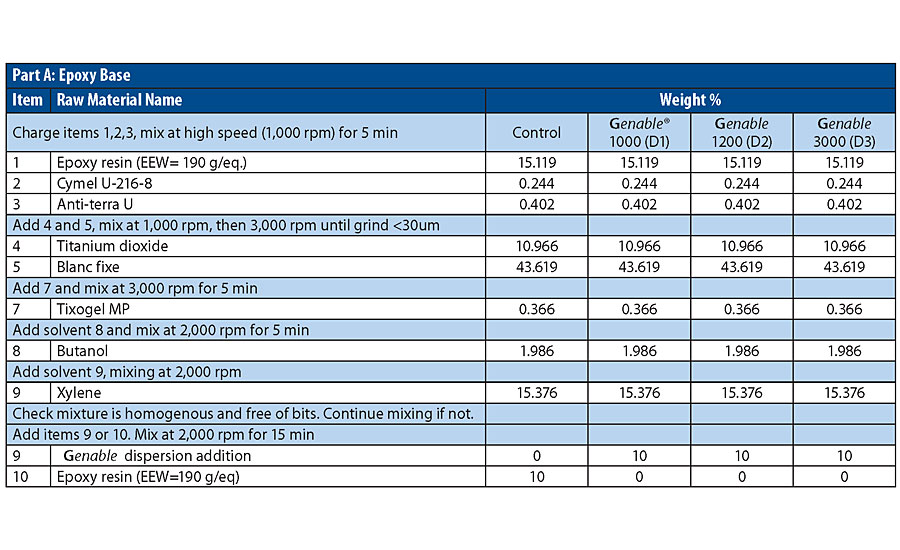
The epoxy to hardener mix-ratio can be calculated for an appropriate hardener based upon the EEW and AHEW values. In this study diethylenetriamine was used as the curing agent added at a rate of 11 parts per hundred.
Graphene Performance in Barrier System
ISO12944 forms the industry standard for corrosion protection by protective paint systems, and describes three tests – water condensation, neutral salt spray and cyclic aging – to demonstrate performance in C4 and C5 conditions. As an initial screening experiment, we chose neutral salt spray (NSS, ISO 9227) to identify systems with potential to extend performance lifetime. In combination with electrochemical impedance spectroscopy (EIS), we monitored the behavior of water within the coating at defined intervals (Figure 1). When applied to the study of organic-based protective anticorrosive coatings, impedance values, water uptake and corrosion potential provide an indication of corrosion protection.
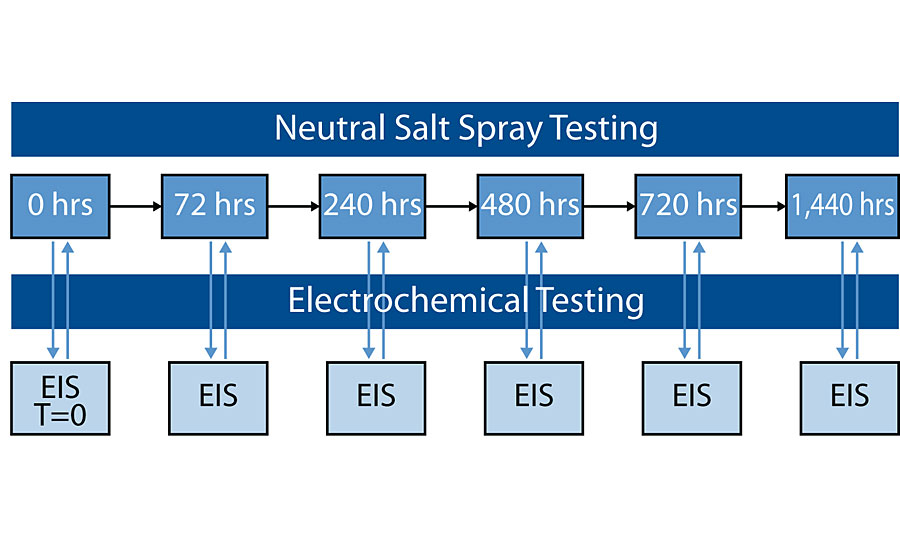
Using the combined approach has the benefit of indicating differences in coating behavior early in testing, where a visual assessment of corrosion would show no difference. In a review paper concerning the performance of fast-cure epoxies for pipe and tank linings, O’Donoghue et al8 describe the use of EIS as a screening tool, where the coating impedance measured at a frequency of 0.1 Hz can be used for screening materials. In the study, the team assigns impedance values less than 106 Ohm.cm2 to poor coatings, and impedance values of 1010 Ohm.cm2 and above to excellent coatings. Between these values, a good coating would represent an impedance value in the order of 108 Ohm. cm2, with barrier protection beginning at 106 Ohm. cm2. Here, the control sample, consisting of a zinc-rich primer coat, a layer of epoxy prototype base and polyurethane topcoat, displays the lowest overall impedance values in the order of 104 to 105 Ohm.cm2, indicating a poor performance (Figure 2). By introducing GNPs into the intermediate layer of the three-coat system, we observe maintenance of a higher level of impedance over the course of the experiment, suggesting that the inclusion of GNPs acts to increase the barrier performance properties of the system as a whole. Of the three systems tested, the graphene nanoplatelet system (D2) displays the greatest improvement in barrier properties, by five orders of magnitude over the control, indicating this system has the best performing barrier.
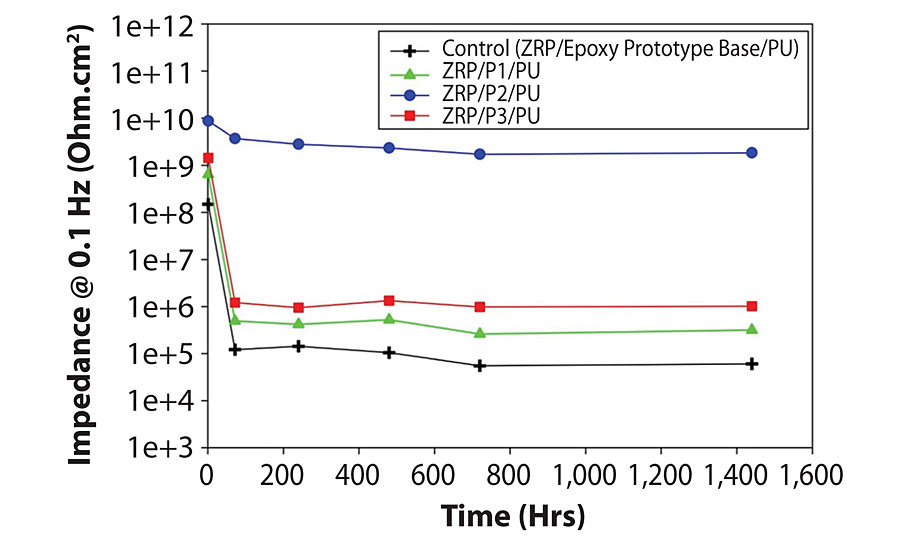
The EIS response of such high impedance coatings at the very beginning of exposure to harsh C4/C5-type environments is dominated by a capacitive behavior; the coating is essentially acting as a dielectric-type capacitor. Following exposure to these harsh environments, water may enter the coating, effecting its capacitance. Depending on the intrinsic properties, the dielectric constant of water is in the region of 30 times that of the coating, leading to an increase in capacitance as water penetrates. This change in capacitance is therefore related to water uptake by the coating, and so can be calculated.9 The water uptake (cv) data suggests that, for the control sample, an apparent water uptake level is reached before the 72-hour point and is related to the relatively low impedance values for this sample. In comparison, the graphene nanoplatelet-enhanced tie coat systems show far less water uptake and appear stable during the test period; these low water uptake values correlate with the relativity high impedance values for the graphene-enhanced samples. All water uptake profiles for the GNP-enhanced coats appear to show an increase in uptake after the initial diffusional stage (high rate), suggesting the presence of free and bound water in the GNP-enhanced coatings. For these three-coat systems, no apparent increase in water uptake is observed for all samples, suggesting major water uptake occurs in the initial 72-hour period with little change facilitating a controlled exposure and activation of the zinc flake in the primer (Figure 3).
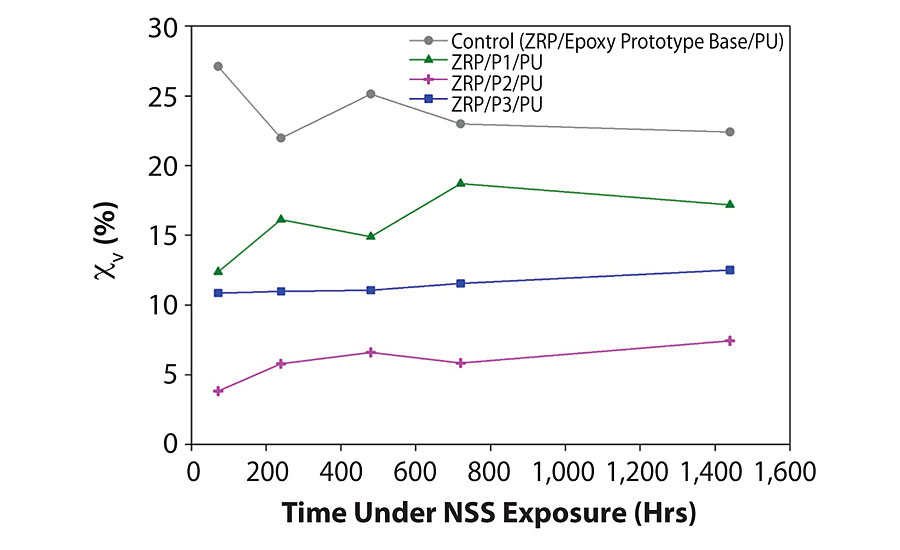
Having water uptake data shows how much water is being absorbed, but another question is how far it has penetrated. This can be interpreted from corrosion potential values for the different systems (Figure 4). The control samples show a lower potential, closer to zinc than bare steel, suggesting that water has breached both the top coat and the intermediate coat very early on in the test. A dip below the corrosion potential of bare steel is also seen for the D1-incorporated sample after 720 hrs, suggesting a lesser performance than the other two GNP-containing samples, with the D2 system performing the best.
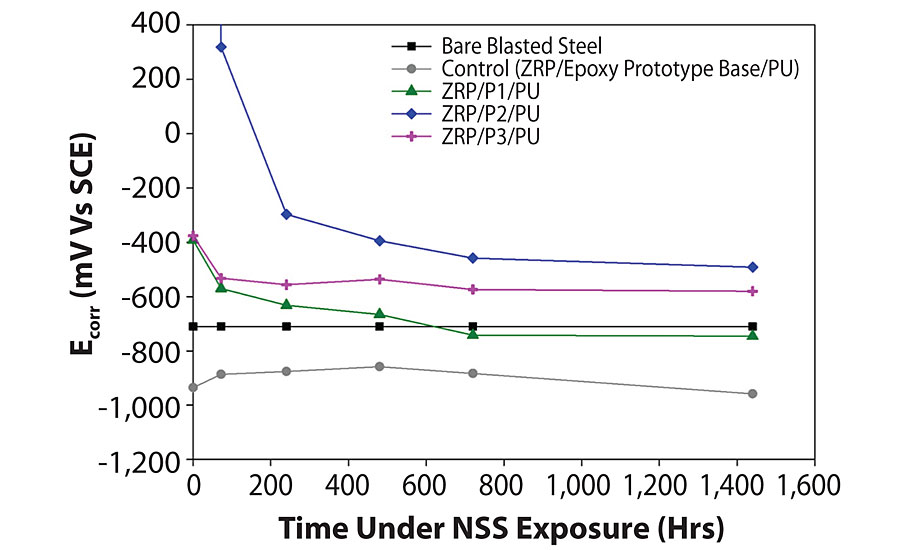
After 1,440 hrs of exposure time (the maximum exposure required under ISO12944 for C4/5 highly corrosive atmospheres) no visible corrosion was observed on any of the samples. We anticipate that subsequent visual assessments will reveal differences between the samples with more corrosion evident on the control sample. The lack of visual signs of anticorrosion performance now highlights the relevance of EIS, where clear differences in sample performance are observed.
Outlook
Graphene is a material that is at the forefront of many new technologies. It has a very high aspect ratio with respect to other inorganic barrier fillers, and is envisioned to be the next generation of barrier additives. This study demonstrates the benefit that graphene can bring to a protective coating utilizing a zinc-rich primer system to improve performance and lifetime. Life extension may have several impacts; extension of maintenance periods reducing costs, improving global warming potential and other life cycle analysis metrics through reduced-release microplastics through surface preparation and volatile organics during the coating process as a consequence of reduced maintenance activities.
References
1 Appleman, B.R.; Bruno, J.A.; and Weaver, R.W. Performance of Alternative Coatings in the Environment (PACE), Report Nos. FHWA-RD-89-127, FHWA-RD-89-235 and FHWA-RD-89-236, Federal Highway Administration, Washington, DC, September 1990.
2 SSPC PAINT 20 Zinc-Rich Coating Type I Inorganic and Type II Organic.
3 P. Okafor et al.: Progress in Organic Coatings Vol. 88 (2015), p.237-244.
4 K. Choi et al: ACS Nano Vol. 9 (2015), p. 5818-5824.
5 S. Aneja et al: FlatChem Vo1. 1 (2017), p. 11-19.
6 Hayatdavoudi, H. Journal of Alloys and Compounds Volume 727, 15 December 2017, p. 1148-1156.
7 Zhang, X.G. Chapter 12 pp 337-349 Corrosion and Electrochemistry of Zinc.
8 M. O’Donoghue et al: JPCL-PMC (1998), p. 36-51.
9 Rapid electrochemical assessment of paint, Gamry Instruments, Technical Application Note.
Looking for a reprint of this article?
From high-res PDFs to custom plaques, order your copy today!