Pigment Terms and Calculations

Davizro / iStock / Getty Images Plus, via Getty Images.
Last month’s article discussed the different pigment types. In this issue I cover some of the terms and calculations related to pigments used in coatings.
Pigments in paints are often qualified by the following terms: Oil Absorption/Surface Area; Pigment Volume Concentration (PVC); and Pigment to Binder Ratio (P:B). I will go into these in detail.
Oil Absorption and Surface Area
Oil absorption is the amount of oil a pigment absorbs (ASTM D281 and ASTM D1483). It dates back to alkyd times and is determined in the lab, not theoretically. It is the amount of linseed oil needed to wet out the pigment and just fill the interstices at maximum packing. The size, shape and particle size distribution affect this important property. It will give you an idea of how much of a certain pigment can be added to a paint and still have it fully covered by resin. With the move to water-based resins that have poor wetting characteristics and resin-free dispersions, oil absorption is being replaced by surface area measurements for pigments, but it is still an important pigment characteristic.
Oil Absorption = Grams of linseed oil
100 grams of pigment
Surface area measures the amount of surface area per given mass of pigment (usually meter2/gram). It is measured by nitrogen absorption and is a modernization of the oil absorption test. Most pigment suppliers will provide both the oil absorption and surface area for their pigments. Some resin manufacturers do not list how well their resins will wet out pigments, and additive manufacturers tend to give wide ranges of use for broad pigment groups. This can limit how well this pigment property can be used.
Pigment Volume Concentration
Pigment Volume Concentration (PVC) is used to determine the pigment loading for all pigments on a volume basis in the coating, and is generally only used for architectural coatings. As you increase the PVC, more pigment by volume and less resin by volume results. You eventually reach a point where there is just enough resin to properly coat the pigment. This point is called the critical PVC (CPVC). Above CPVC, there is not enough resin to fill the voids between the pigments, air voids remain in the coating, dry hide starts and there is a significant loss of film properties. As PVC increases, gloss, stain resistance, flexibility and other physical properties decrease.
PVC = Volume of pigment x 100
Volume of pigment and resin
Since resins have variable wetting properties and pigments have different surface areas, oil absorption, properties and particle sizes, you cannot theoretically calculate CPVC, so it has to be lab determined. Unless you are developing flat paints, you will not approach CPVC, so it is not a concern. Table 1 lists a range of PVC versus gloss.
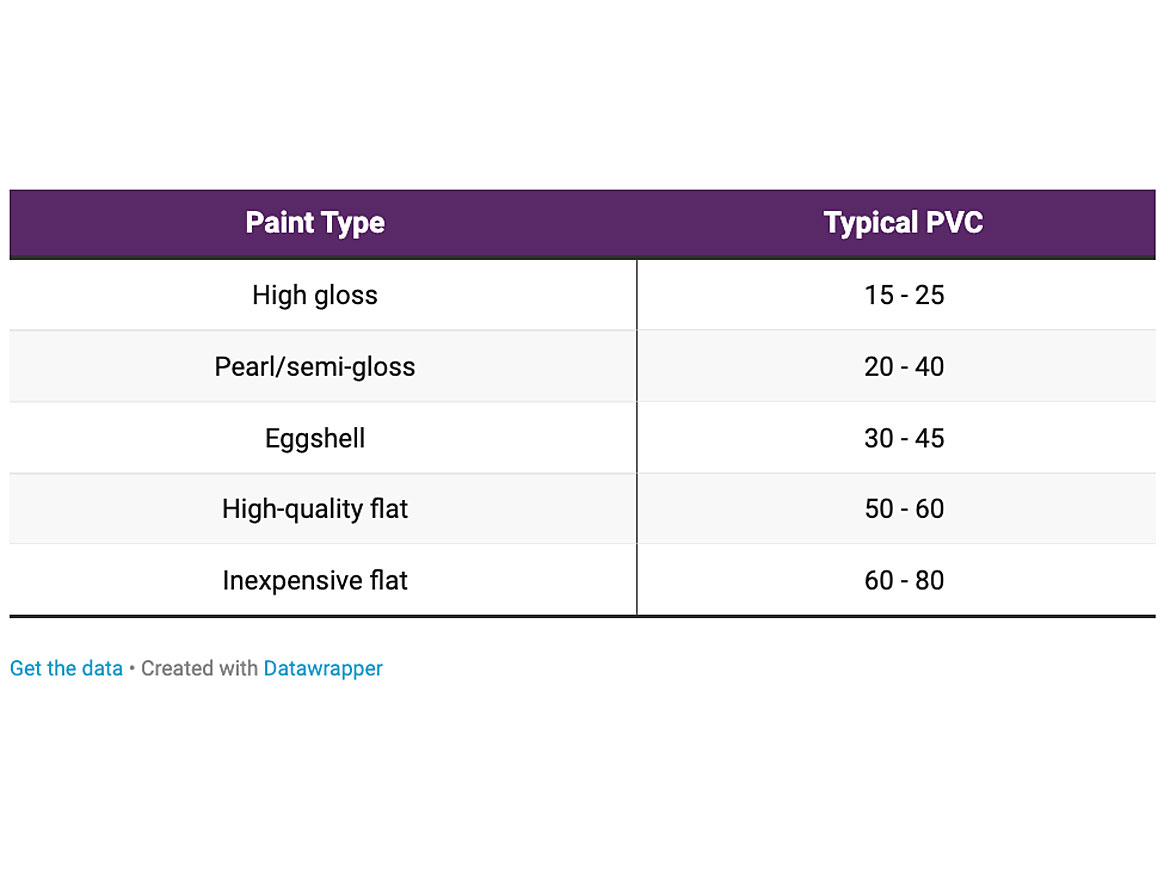
Pigment to Binder Ratio
The Pigment to Binder Ratio (P:B) is used to determine hiding and opacity. P:B is calculated with primary pigments only, and is used in industrial coatings, but is relevant to all coatings. It is used to determine the amount of primary pigment needed for hiding on a weight basis. P:B is different than PVC because it is universal across different resin systems and pigments. The ratio is calculated at a given dry film thickness, usually 1 mil (25 microns). The nice feature of P:B is changing the film thickness directly changes the P:B needed. For example, in Table 2 we see for 1 mil dry film thickness we need 1.0-1.1 lb of titanium dioxide per pound of resin solids, so at 2 mils dry film thickness we would only need half the P:B, or 0.5-0.55 lb. This is because we need a given amount of pigment in the light path — as we increase the thickness of the film, less pigment per amount of film is required.
P:B = Weight of primary pigment
Weight of resin solids
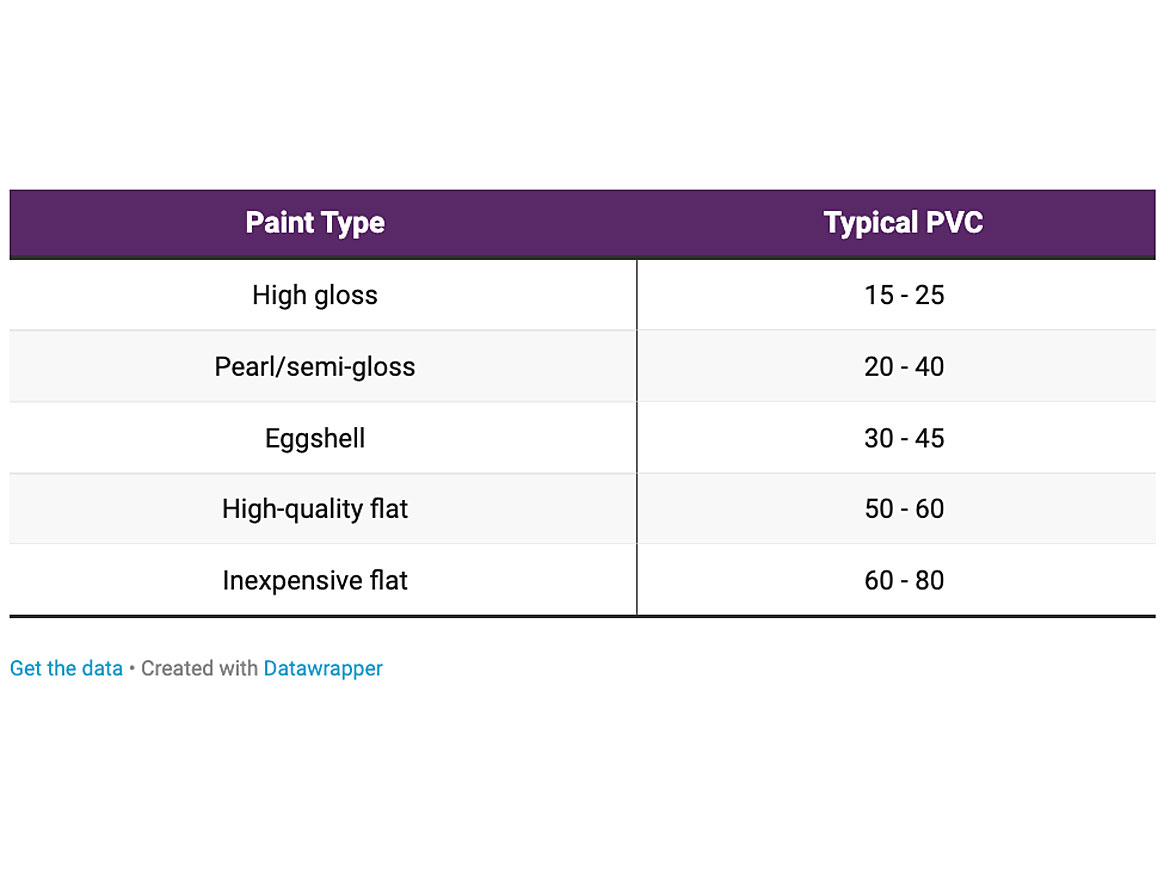
Knowing pigments will only improve your coating formulations. Stay tuned for the next article, where I will discuss the pigment dispersion process.
All information contained herein is provided "as is" without any warranties, express or implied, and under no circumstances shall the author or Indorama be liable for any damages of any nature whatsoever resulting from the use or reliance upon such information. Nothing contained in this publication should be construed as a license under any intellectual property right of any entity, or as a suggestion, recommendation, or authorization to take any action that would infringe any patent. The term "Indorama" is used herein for convenience only, and refers to Indorama Ventures Oxides LLC, its direct and indirect affiliates, and their employees, officers, and directors.
Looking for a reprint of this article?
From high-res PDFs to custom plaques, order your copy today!