Novel Curing Agent for High-Performance, Less-Yellowing, Clear Epoxy Coatings

Credit:uschools, E+, via Getty Images
For industrial protective coating applications, a two-component, epoxy-based coating has many advantages over other chemistry-based systems like acrylics or polyurethanes. Bisphenol A type epoxy coatings have an excellent adhesion to various substrates, superior chemical resistance, and improved thermal and mechanical properties. However, due to its aromatic ring structure, it results in poor UV resistance, and their amine curing agent causes increased yellowness in the system.
Driven by end-user demand, there is a strong desire to reduce the yellowness of clear epoxy coatings for many cosmetic applications. However, compromises in coating performance are unacceptable for the sake of less yellowing; epoxies are an important class of coatings, utilized in several demanding applications and environments, that are expected to provide high-performance aesthetic properties. Using a cycloaliphatic type amine, such as an IPDA or PACM-based amine, is one common route to lower yellowness for epoxy coatings.
Huntsman Advanced Materials has developed an innovative cycloaliphatic type of amine curing agent with low color, outstanding non-yellowing properties, and excellent gloss retention. It also has a unique combination of long pot life and fast-curing properties.
We report here on the use of this novel curing agent, accompanied with liquid epoxy resin, in a clear-coating formulation. Performance comparisons with another current commercially available product, specifically on their respective dry times, pot life, early water resistance, adhesion, hardness, and accelerated weathering test, will be enumerated.
Experimental
Raw Materials and Testing Panel Preparation
A commercial cycloaliphatic amine curing agent, based upon PACM, was chosen in this study as the commercial control, referred to as COM. The Huntsman novel amine curing agent is referred to as HUN. Industrial standard bisphenol A type liquid epoxy resin, designated here as BLR, was used to react with those curing agents. The physical properties of these curing agents and BLR are described in Table 1.
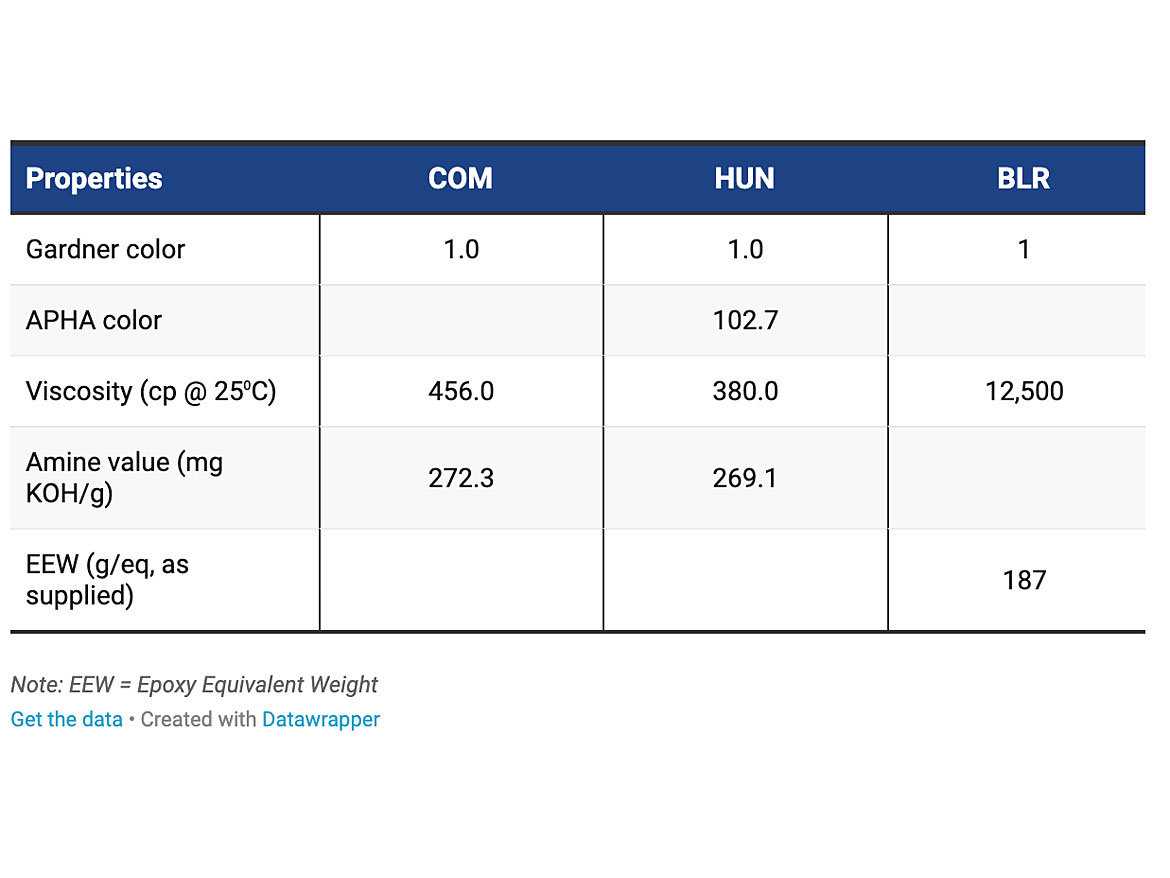
The two-component coatings were prepared by mixing liquid epoxy resins and amine curing agents on an overhead mixer on the 100-300-gram scale. The coating formulation using BLR and COM is referred to as Control, whereas the coating formulation based on BLR and HUN is referred to as Huntsman.
Testing panels were prepared by drawing down the two-component coatings over cold-roll steel panels, generally using a 12-mil gap, 3-inch draw down bar. The panels were typically allowed to cure for 7 days at 23 °C and 50% relative humidity before testing, unless otherwise noted. The dry film thickness of testing panel is about 10 mil.
Testing Procedures
Viscosity
The viscosities of the paints were measured using a Brookfield viscometer and 4-oz, wide-mouth plastic jars. Mixed viscosity was recorded immediately after mixing the liquid epoxy resin and amine curing agent.
Gel Time
Gel time was measured using Gel Timer with 150-gram total mass, according to ASTM D2471.
Gloss
Gloss was measured using a BYK-micro-TRI-gloss instrument. Gloss is a measure of light reflectance of a coating at defined angles, according to ASTM D523. Gloss was measured at 60o.
Dry Time
Coatings were drawn down onto glass substrates with a wet film thickness of 150 µm and set on a B.K. Linear Drying Time Recorder. The dry-to-touch and dry-through times were visually assessed after dragging a needle through the coating over the course of 24 hours, according to ASTM D5895.
Cross-Hatch Adhesion
Adhesion of the coatings on the metal substrates was measured according to ASTM D4541. A comb-like metal template was put on the surface of the testing panel and a utility knife was passed through each slit, thus inscribing 11 parallel cuts in the paint film. The template was then rotated 90o and placed over the same area, and a second set of 11 cuts were made. One-inch-wide tape with a 4” overlap at one end to form a pull tab was applied over the test area. The tape was rubbed with an eraser to assure thorough contact over the test area. Then, using the overlap for a grip, the tape was pulled quickly at an 180o angle from the substrate. The coating was then visually inspected to determine how much coating was removed from the substrate. The scale follows.
5A No peeling or removal
4A Trace peeling or removal along incisions or at their intersection
3A Jagged removal along incision up to 1.6 mm on either side
2A Jagged removal along most of incision up to 3.2 mm on either side
1A Removal from most of the cutting area under the tape
0A Removal beyond the cutting area
Konig Hardness
Konig hardness was measured using a TQC SP0500 Pendulum Hardness Tester, according to ASTM D4366, and reported in seconds. Three measurements were taken for each testing panel and the average was recorded. The Konig hardness was measured after seven days of cure.
Shore D Hardness
Shore D hardness was measured using a Durometer according to ASTM D2240. Three measurements were taken for each testing panel and the average was recorded. Measurements were recorded at various intervals over the course of one week of cure.
Impact Resistance
The impact resistance of the coating was determined according to ASTM D2794 using a 4-lb weight. The weight was dropped from a known height, and the indenter formed a dimple in the coating panel. The test was performed by impacting the coating directly and reversely (coating facing upward and downward). Crackling or delamination on or around the dimple was examined and data were recorded in in-lb.
Taber Abrasion
Taber abrasion was tested using a Taber abrader according to ASTM D 4060. Abrasion resistance is calculated as loss in weight at a specified number of abrasion cycle. CS-17 abrasive wheels, 1-kg load and 1,000 cycle were used.
Environmental Chamber Testing
After testing panels were prepared in the manner as previously mentioned, testing panels were placed into an environmental chamber to cure. Two curing conditions were used: 10 °C, at 70% relative humidity (RH) and 5 °C, at 50% relative humidity. After 7 days of curing, testing panels were inspected for appearance and gloss.
Water Resistance
Water resistance testing panels were prepared by draw down coating on glass panel. Testing panels were allowed to cure for 24 hours at 23 °C and 50% relative humidity, followed by immersion in tap water for 24 hours at 23 °C. After 24 hours, the panels were cleaned with tap water and dried with paper towels before rating. The coatings were immediately inspected for appearance and gloss.
Coating Weatherability
Coating weatherability was tested using a QUV weathering chamber according to ASTM G 53. The weather testing schedule used was a cycle of UVA exposure for 8 hours at 50 °C and condensing humidity at 40 °C for 4 hours. Yellow index and gloss were recorded to indicate how coating progress under UVA exposure. The higher yellow index number, the yellower coating becomes.
Chemical Spot Resistance
Chemical spot resistance testing was done in accordance with ASTM D1308. A few drops of chemicals were applied to the horizontal surface by saturating a 2.3-cm grade 3 Whatman filter and covering it with a watchglass to prevent evaporation. After 24 hours, the panels were cleaned with tap water and a sponge, then dried with paper towels before rating. The coatings were immediately inspected for appearance and film damage.
Results and Discussion
The basic coating properties of the formulations for Control and Huntsman are listed in Table 2. From the data, the Huntsman formulation has lower mixed viscosity, better visual appearance, and slightly higher gloss. In addition, it has a longer gel time, indicating longer pot life, while maintaining the same dry through time as the Control. Subsequently, it is proven to have a useful combination of long pot life and fast-curing properties.
Hardness development is very similar for both formulations; however, the Huntsman formulation has better impact properties, both direct impact and reverse impact. It is because this novel curing amine contains both rigid and flexible segments in the same molecule, which provides more balanced flexibility. Both formulations have excellent crosshatch adhesion, and the Huntsman formulation has better Taber abrasion resistance than the Control.
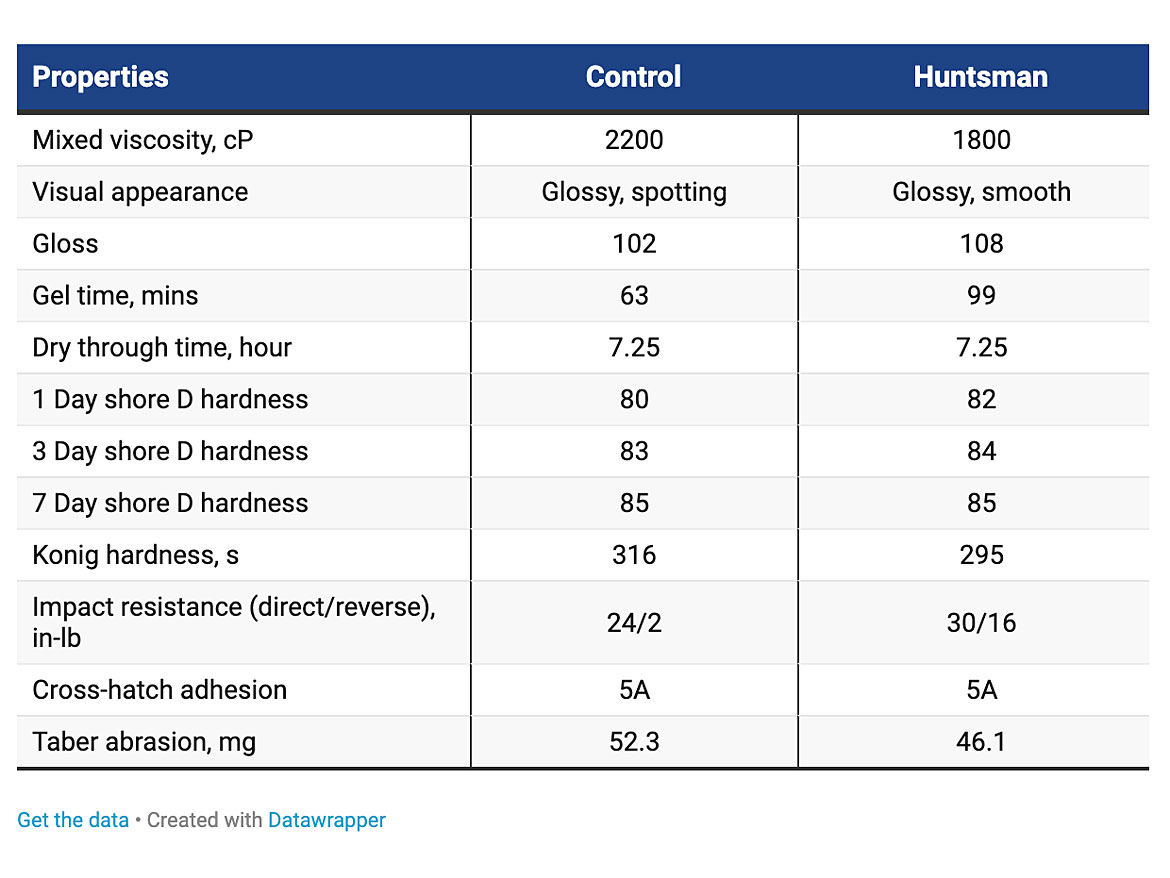
Environmental chamber testing and water resistance data are listed in Table 3. Clearly, the Huntsman formulation has a better appearance and higher gloss for both environmental chamber curing conditions. For water resistance test, the Huntsman formulation also has better appearance and gloss after 24 hours of immersion in tap water. Gloss retention results are shown in Figure 1.
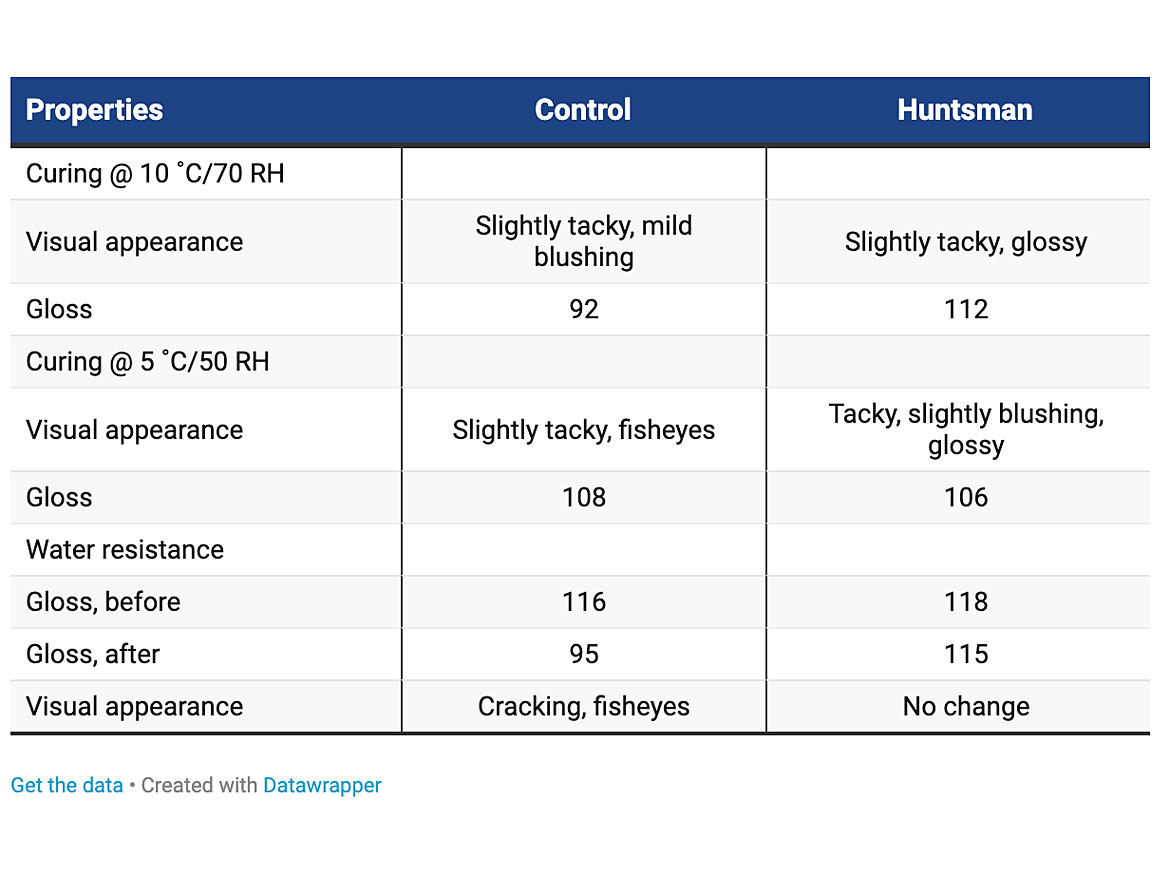
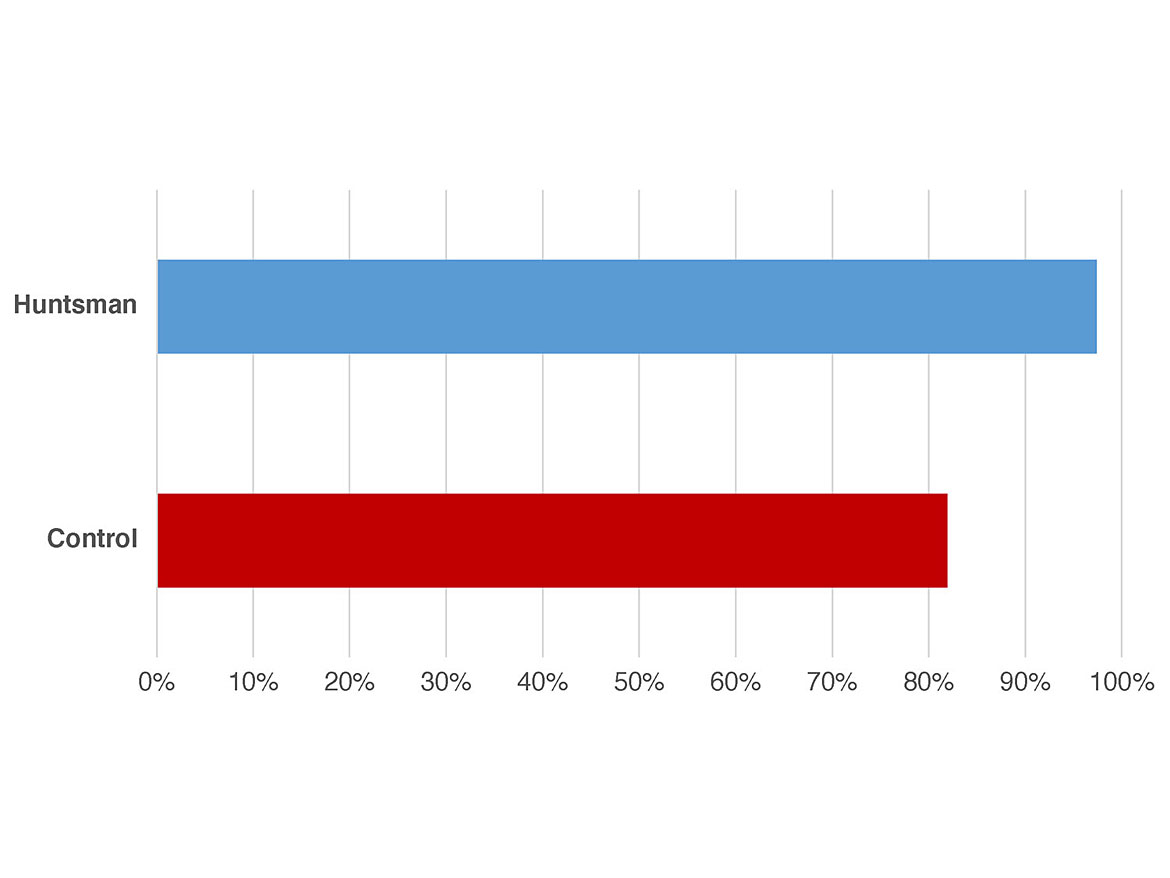
The results of UVA accelerated weather testing are shown in Table 4. The yellow index (YI) and gloss were measured for each panel after 1, 3, and 7 days of exposure.
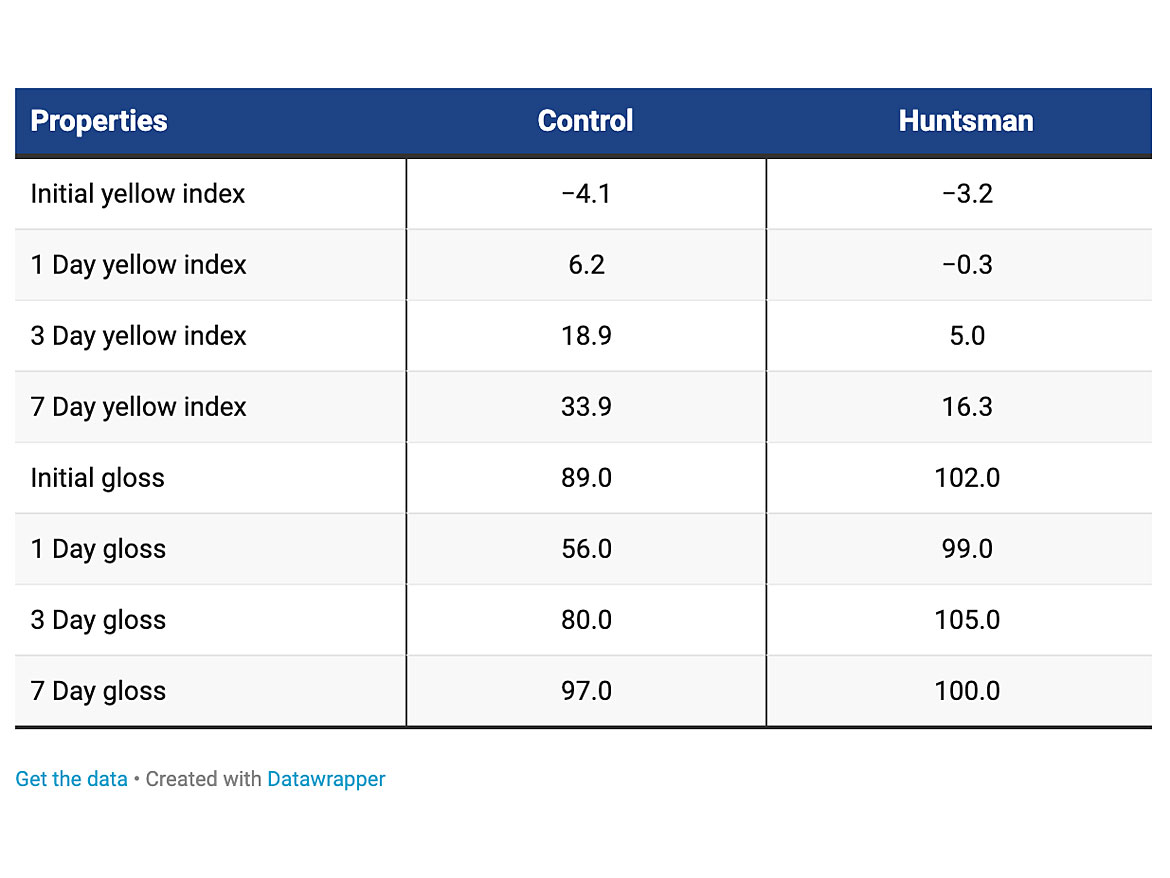
Figure 2 and Figure 3 are graphical representations of comparisons in gloss and Yellow Index of testing panels subjected to the accelerated weather tester for 1, 3, and 7 days. The Huntsman formulation has the highest gloss and the lowest yellow index in comparison with the control.
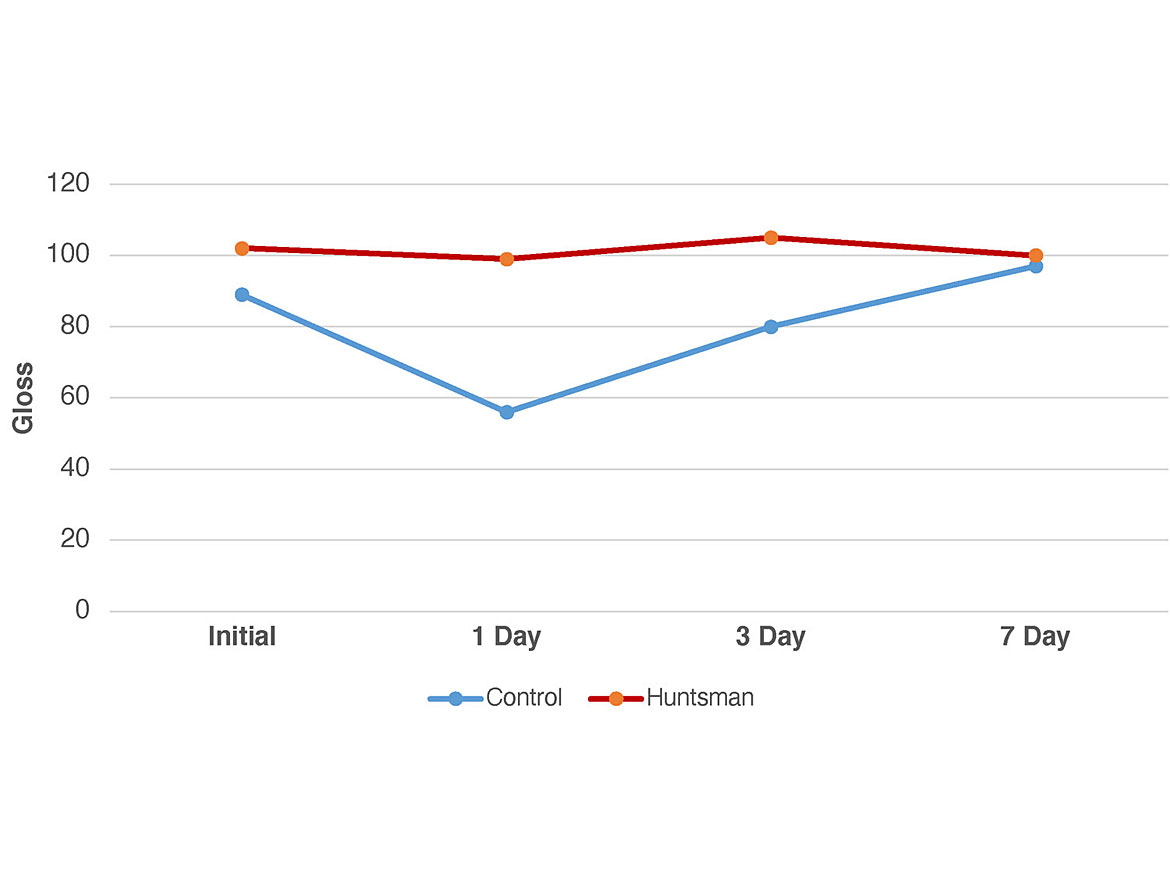
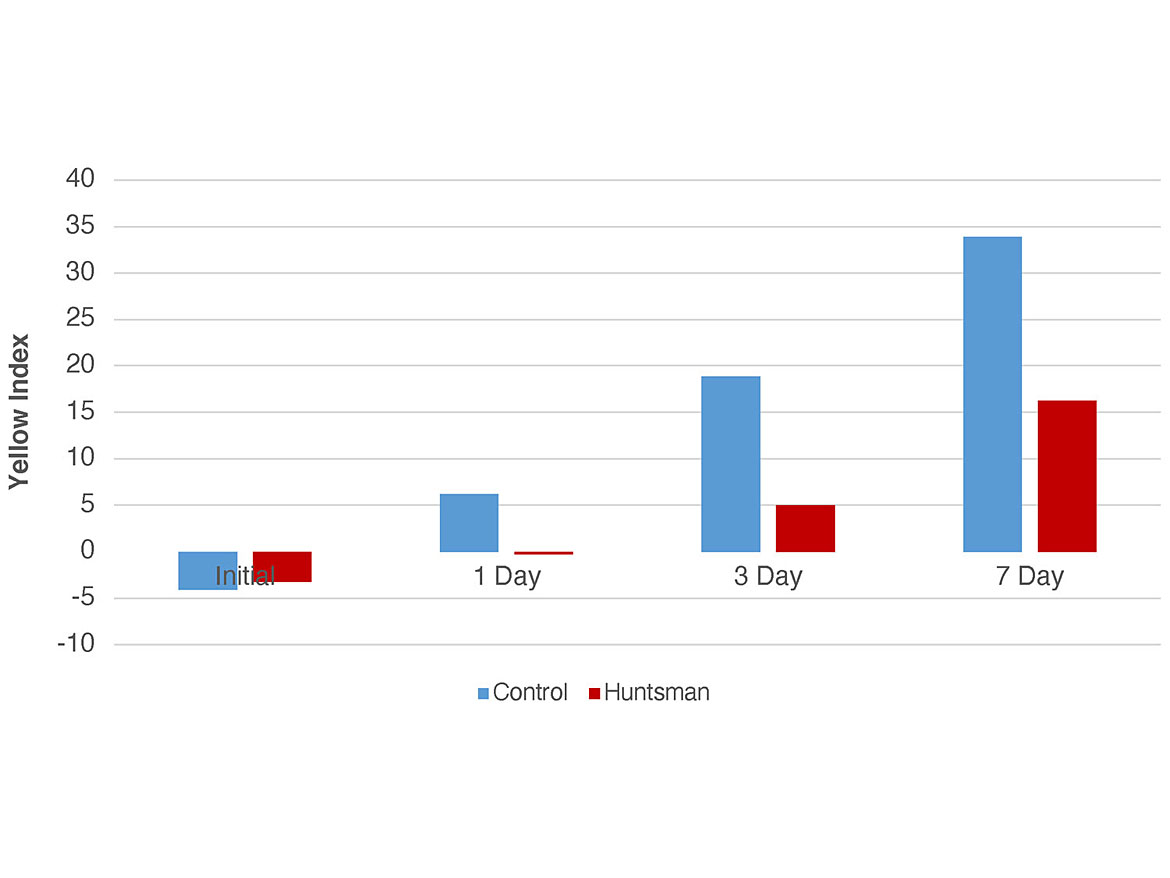
Figure 4 shows photographs of the coatings after 7-day exposure to the UVA accelerated weather tester. The yellow index is more than twice as high in the Control formulation than in the Huntsman formulation.
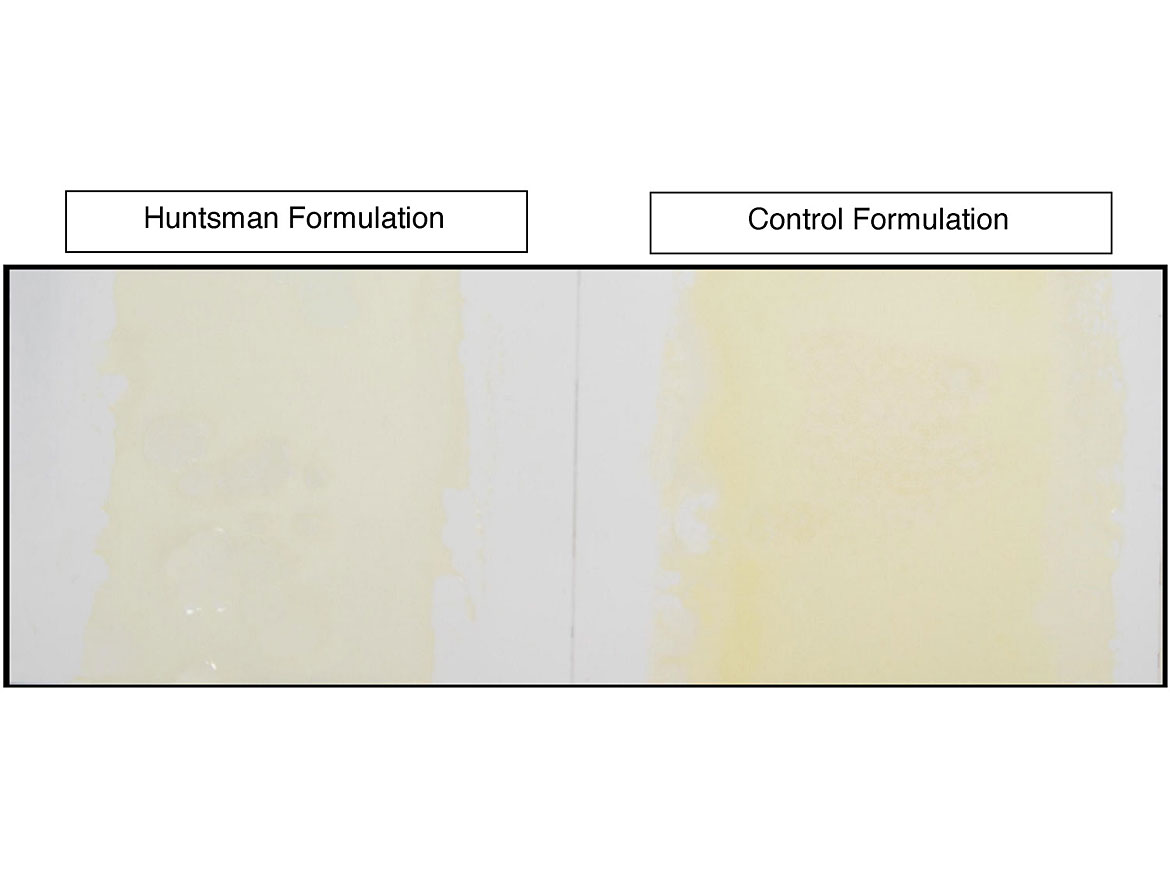
The results of the chemical spot resistance tests are shown in Table 5; the control formulation performs better than the Huntsman formulation.
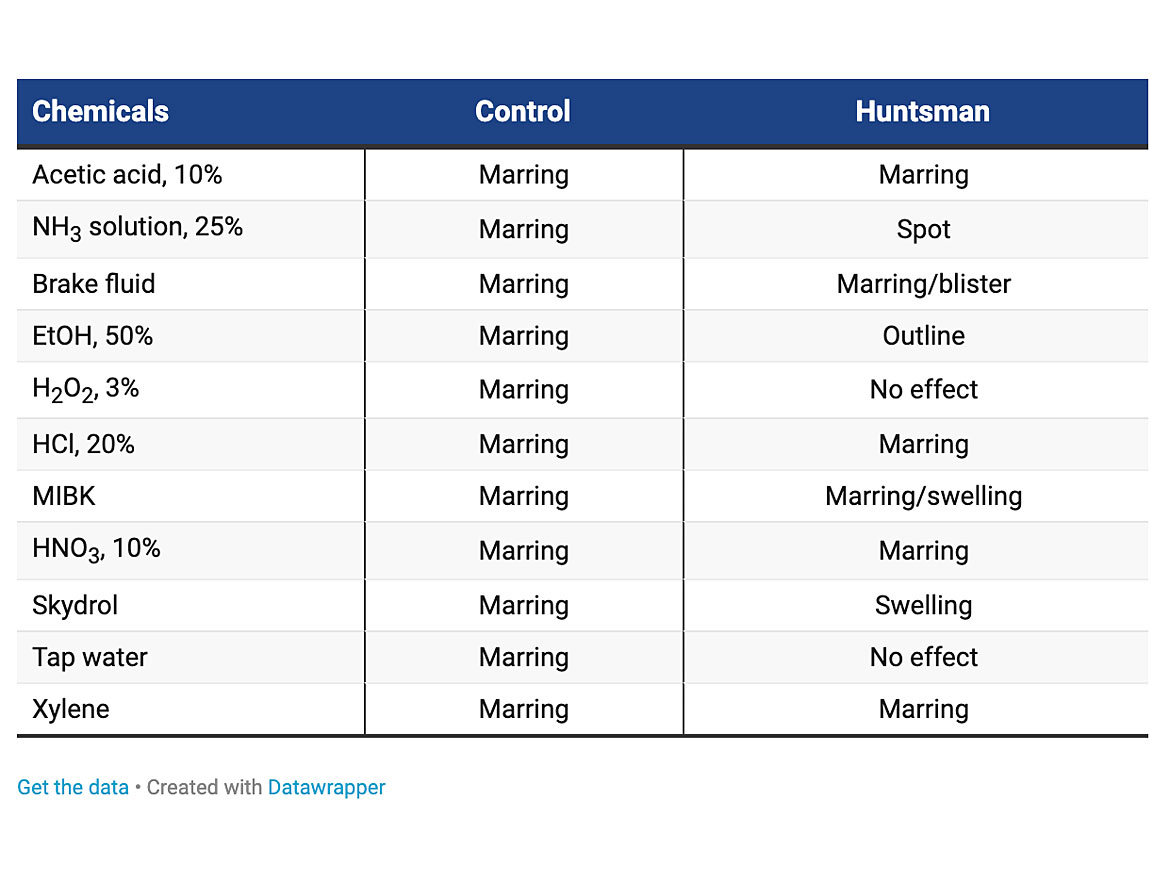
Conclusions
Examining all the data, we can see this novel curing agent performs similarly or better than the commercial reference in all but the chemical spot resistance tests. The most notable strength of this curing agent is seen in the aesthetic properties of its coating. This novel curing agent retains gloss and staves off yellowing better than commercial products. The result of the accelerated weathering test shows it gives the lowest yellowing and the highest gloss retention. The maximum yellowing index recorded for this curing agent is significant at 57% lower than the commercial reference.
When looking at the chemical spot testing results, it appears that the commercial reference outperformed our new curing agent, but there is a caveat to this observation. Despite the overall resistance to chemicals in the commercial reference, the marring in the Control formulation is more obvious than the Huntsman formulation, as it loses gloss more often. Therefore, though the Huntsman formulation is outperformed in the chemical spot tests, it is not easily discerned, as it retains a better appearance and gloss.
The summation of all the tests proves this unique curing agent offers important advantages over the commercial reference in terms of workability, gloss retention, non-yellowing and water resistance. These advantages offer potential customers the ability to formulate higher performance, less yellowing epoxy coatings.
References
1 Hare, C.H. Protective Coatings. Fundamentals of chemistry and composition. Chapter 15. Epoxy Systems. Technology Publishing Company, Pennsylvania, 1994.
Looking for a reprint of this article?
From high-res PDFs to custom plaques, order your copy today!