Novel CNSL-Based Epoxy Curing Agents for Zero-VOC Floor Coatings and Underwater Cure Applications

Concrete Coating Challenges
Concrete is a cost-effective, easy-to-handle material that is widely used to provide high compressive strength, excellent durability and good fire resistance, amongst other properties.1 As a result, concrete is a common first choice as a construction material for large infrastructures, such as dams, bridges and roads, and for residential and commercial buildings, garages and basement floors. However, due to its porous structure, water, vapors and chemicals can easily penetrate and stain the concrete. Furthermore, the low tensile strength and rigid nature of concrete make it susceptible to cracks and creeps that progress over time.
Coating systems are necessary to protect and extend the durability of concrete substrates, especially in very harsh environments; coating systems can also deliver desired aesthetic finishes to concrete buildings and floors. Floor coating is a major segment of concrete coatings with different types of coating technologies being employed, such as acrylic, epoxy and polyurethane, to meet increasing high-performance requirements. In recent years, stricter regulations and increasing health and environmental concerns, especially for indoor floor applications, have driven demands for new low- and zero-volatile organic compound (VOC) coating systems that are preferably high in bio-content and offer safer labeling.
What is CNSL Technology?
For over 30 years, Cashew Nutshell Liquid (CNSL) technology has been broadly used in the coatings industry as a starting material for epoxy curing agents, epoxy diluents, phenolic resins and polyols. CNSL is an annually renewable and non-food-chain biomaterial that can be obtained as a by-product of the cashew production.2 CNSL is contained in the honeycomb structure of the cashew nutshell (Figure 1), and it is primarily composed of 60-70% anacardic acid, 10-20% cardols, 3-10% cardanols, and 2-5% 2-methylcardols.3
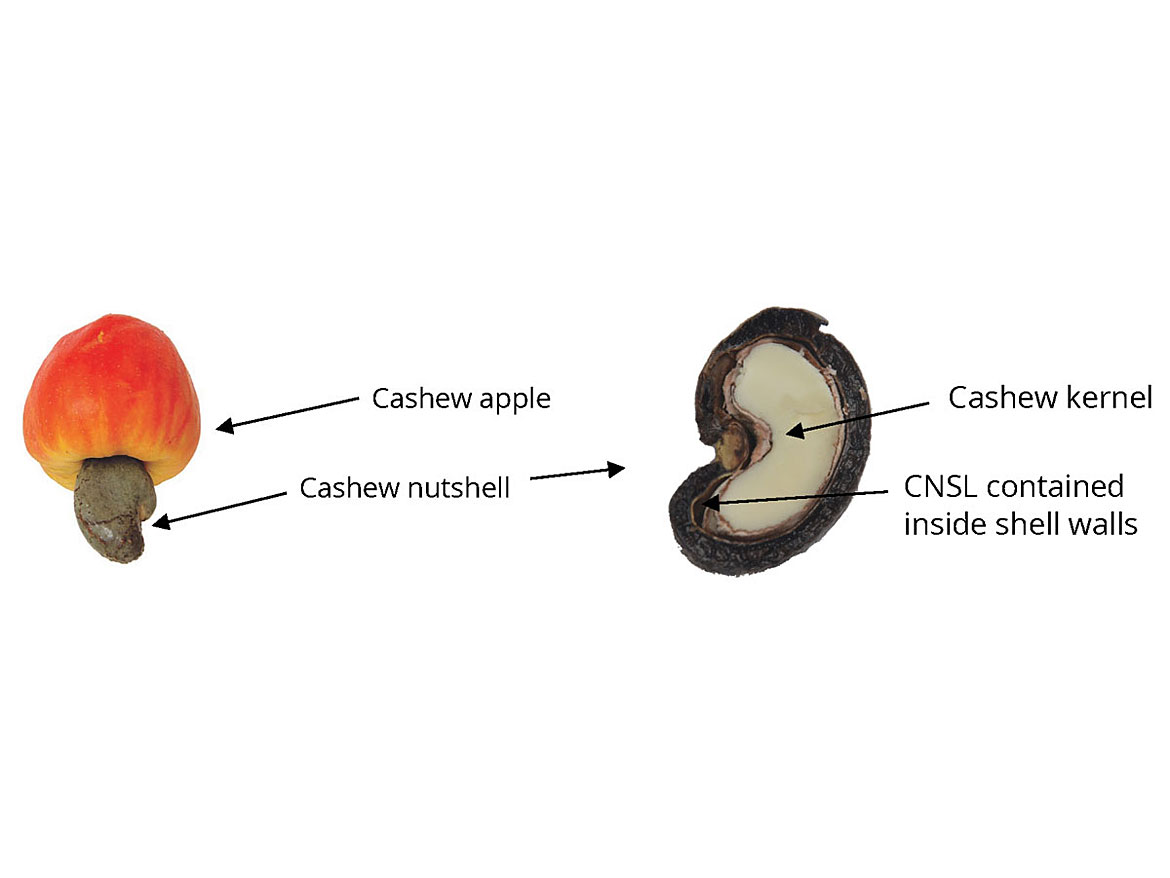
Cardanol is the main component derived from CNSL via decarboxylation and distillation.3 The average chemical structure of cardanol (Figure 2) shows a phenolic ring and a long aliphatic side chain that consists of a mixture of one, two and three double bonds. The aromatic ring provides thermal and chemical resistance, while the side chain provides hydrophobicity, flexibility and reduces surface tension. In addition, the phenolic hydroxyl group increases adhesion to surfaces and accelerates epoxy-amine reactions.5 Those unique properties are inherited by curing agents based on CNSL and enable high-performing epoxy systems that are suitable for protective and floor coatings.
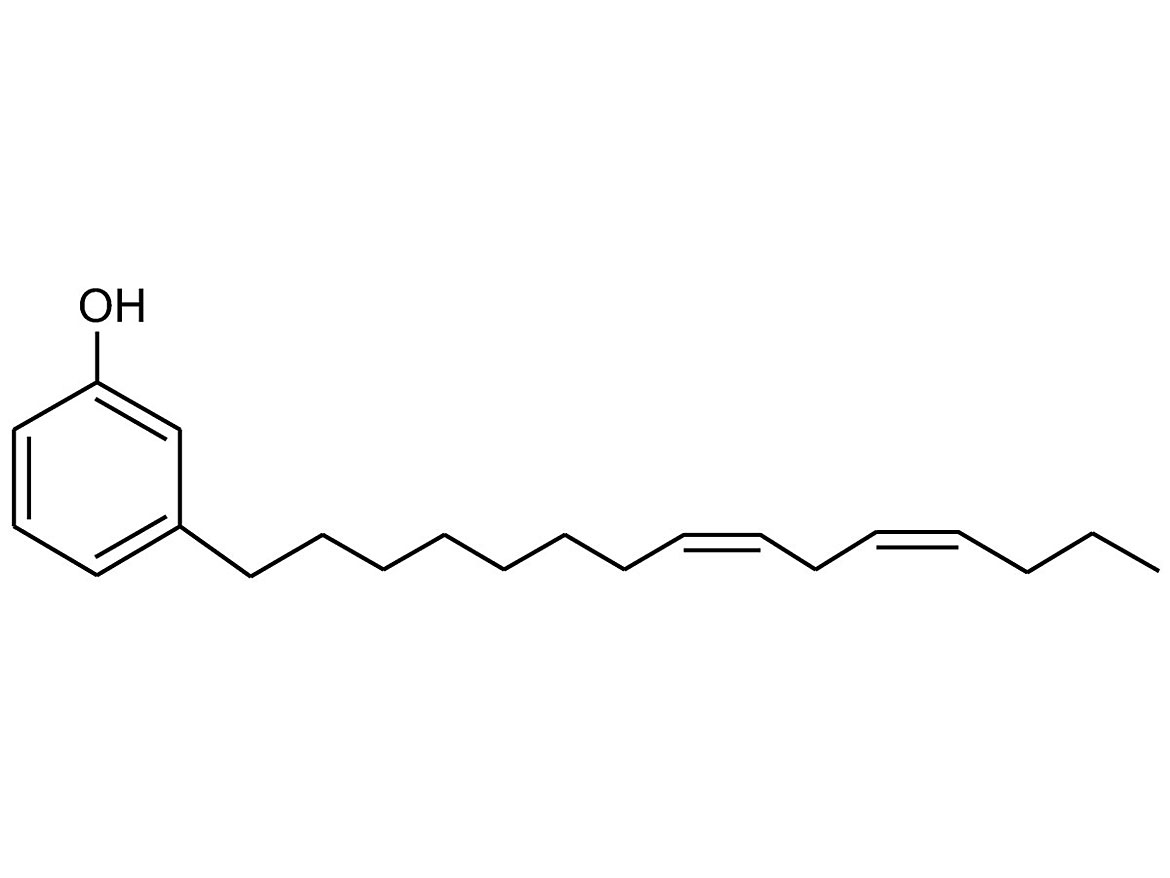
In Table 1, the typical properties of CNSL-based solvent-free (SF) epoxy curing agents, NX-5454, NX-5653 and NX-6654, are listed. It can be seen that all three curing agents have high bio-content (>60%) and low viscosities, and none of them contains any solvent or benzyl alcohol. NX-5653 and NX-6654 do not contain any phenol, which is considered as a hazardous material and not allowed in certain applications. Furthermore, the wide-ranging use level of NX-5653 and NX-6654 reduces the failure risks that can result from improper mixing at the application site and gives coatings manufacturers greater formulation latitude.
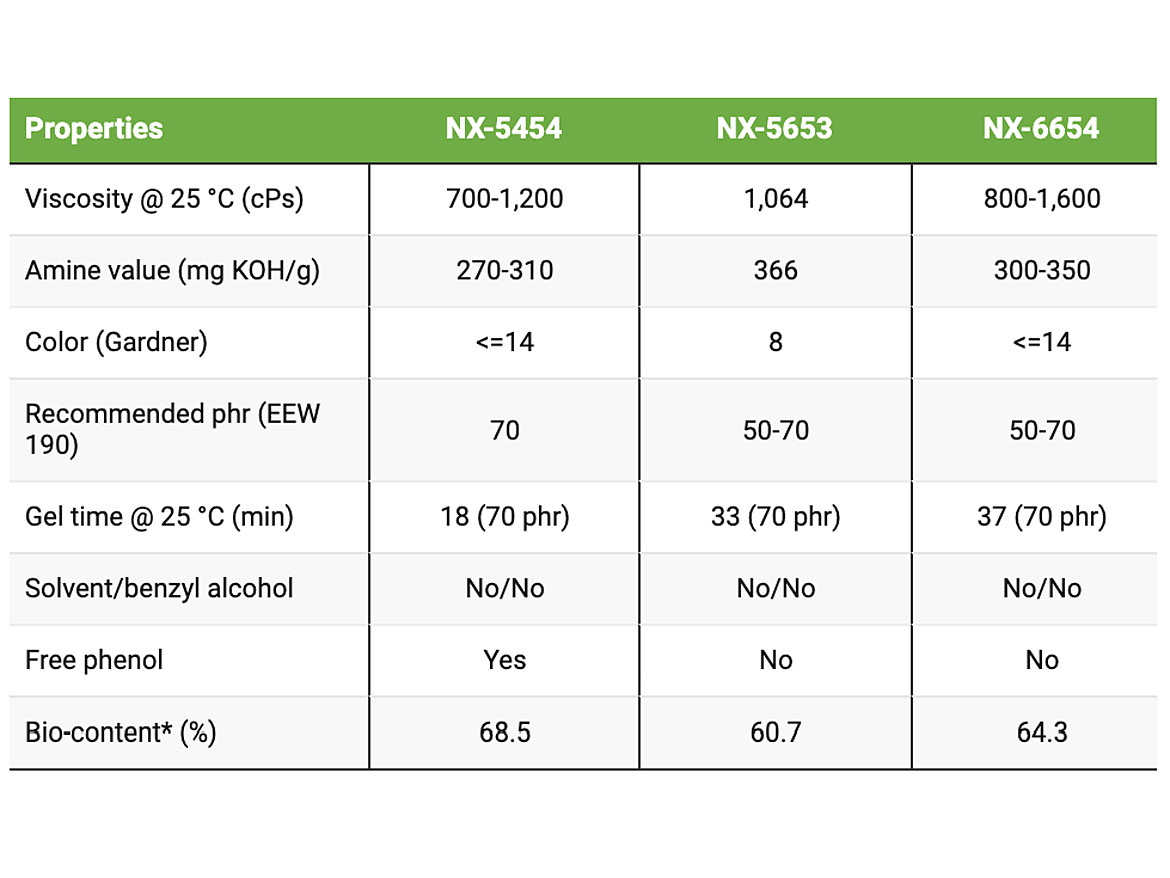
* Calculated values are estimated based on the amount of renewable raw materials used and processing conditions. They should be considered as approximate values. Cardolite cannot guarantee the accuracy of these calculations.
This article will demonstrate how those three CNSL-based SF epoxy curing agents deliver desirable properties to floor coating systems even under challenging cure conditions. Some of the performance results highlighted in this study include fast cure at low temperatures, excellent blush resistance and early water resistance, and superb adhesion to damp and/or contaminated concrete substrates.
Quick Return-to-Service
In most cases, asset owners would like to minimize the asset downtime required for floor coating applications. One important benefit that CNSL-based epoxy curing agents can bring to floor coating systems is their fast cure, especially at low temperatures. The phenolic -OH group from cardanol acts as an accelerator for epoxy-amine reactions, and the long aliphatic side chain provides good molecular mobility that facilitates cure at low temperatures. From Figure 3, it can be seen that NX-5454, NX-5653 and NX-6654 could deliver less than 3 hours of dry hard time at 25 °C cure condition. At 5 °C and 0 °C cure conditions, those epoxy primers could achieve dry hard times of less than 19 hours with no need for external accelerators, which is fast compared to many commercially available epoxy primers.

Moreover, fast cure property also allows for quick re-coatability. For instance, the three primers above were successfully recoated by an epoxy topcoat based on Ultra LITE 2009 curing agent after 5 hours cure at room temperature (RT) and 24 hours cure at 10 °C and 70% RH. After the topcoat cured for 7 days, pull-off adhesion strength was tested. The test results listed in Table 2 show that all three CNSL-based epoxy systems provided high pull-off adhesion strength, higher than 850 psi, regardless of the short cure time or low cure temperatures; the concrete cohesion failures also revealed that these primers had excellent adhesion to both concrete substrate and topcoat layer.
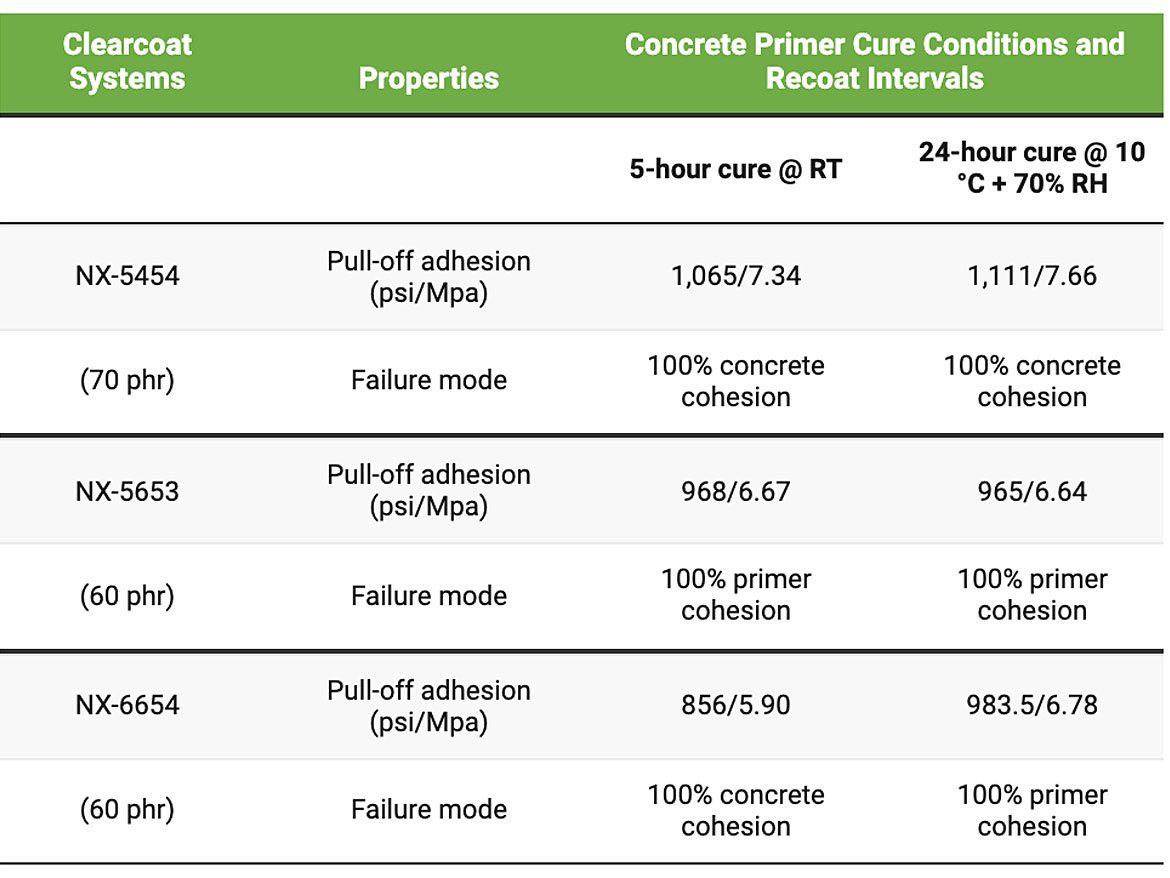
High Tolerance to Harsh Environments
Epoxy floor coatings usually struggle with blush and water spotting due to the uncontrolled weather conditions at the application site. However, CNSL-based epoxy primers are less affected by harsh environments given the hydrophobic aliphatic side chains in polymer structure. For example, when the three primers based on NX-5454, NX-5653 and NX-6654 were cured at low-temperature and high-humidity conditions (10 °C and 92% RH), their films still exhibited high glosses without any blushing or blooming issues. Furthermore, an early water resistance test was conducted on the same primers by placing a water droplet on the primer films every hour after application while keeping temperature at 25 °C. Figure 4 shows the test panels after testing. The results demonstrated there was no water stain after a cure time of 3 hours, 5 hours and 4 hours for NX-5454, NX-5653 and NX-6654 systems, respectively. The excellent blush resistance and early water resistance provided by CNSL-based epoxy curing agents suggested that their fast cure and hydrophobicity could protect floor coatings from failures due to poor application environments.
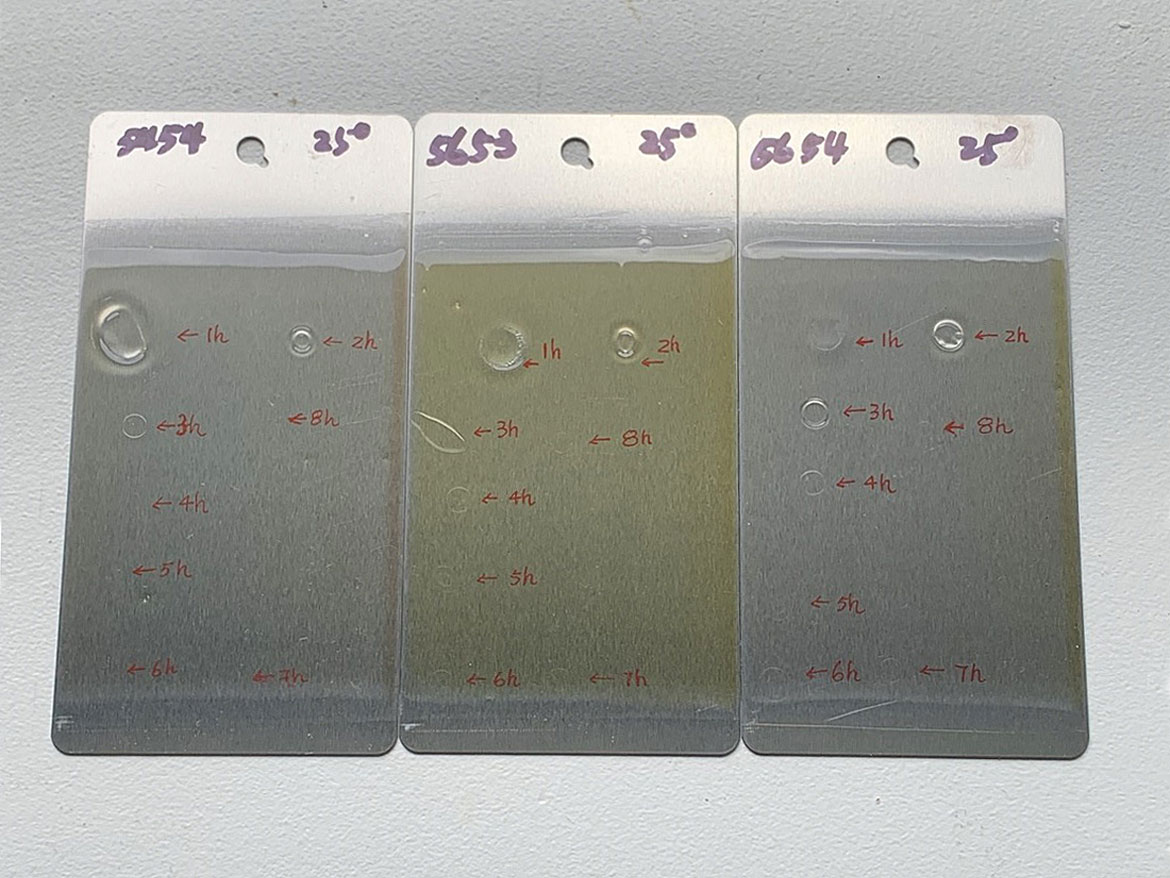
Excellent Adhesion to Poorly Prepared Concrete
One of the biggest challenges faced by floor coatings is to secure good adhesion to concrete floors that are poorly conditioned for application. For instance, basement concrete floors usually suffer continuous water and moisture attacks from underground; the floors in garages, maintenance rooms or chemical warehouses tend to be contaminated with various oils and chemicals. The porous nature of concrete allows the penetration of moisture and contaminants, which hurts the adhesion between the coating and the concrete floor. In order to minimize adhesion failures, old concrete should be deeply cleaned to remove any surface contaminations, and a sealant coat should be applied over damp concrete floors prior to primer application. Those steps increase cost and floor installation time. CNSL-based curing agents can lower cost and provide quick return-to-service by possibly removing those extra steps. The long aliphatic side chain helps reduce viscosity and increase the wetting ability of the coating, while the phenolic -OH provides anchor-like sites to improve adhesion.
As an example, NX-5454, NX-5653 and NX-6654 systems were applied over dry and damp concrete substrates. The damp concrete was prepared by fully immersing the concrete block in tap water for more than 24 hours and then keeping it half immersed during the test. The pull-off adhesion data of NX-5454, NX-5653 and NX-6654 primers over dry concrete and damp concrete substrates are listed in Table 3. It can be seen that the CNSL-based epoxy primers exhibited excellent adhesion to concrete substrates under both conditions. In addition, the lower pull-off adhesion results for damp concrete were due to concrete cohesion failure, which suggested that long-term exposure to water and moisture did reduce the concrete strength but did not weaken the adhesion between the primer and the concrete surfaces.
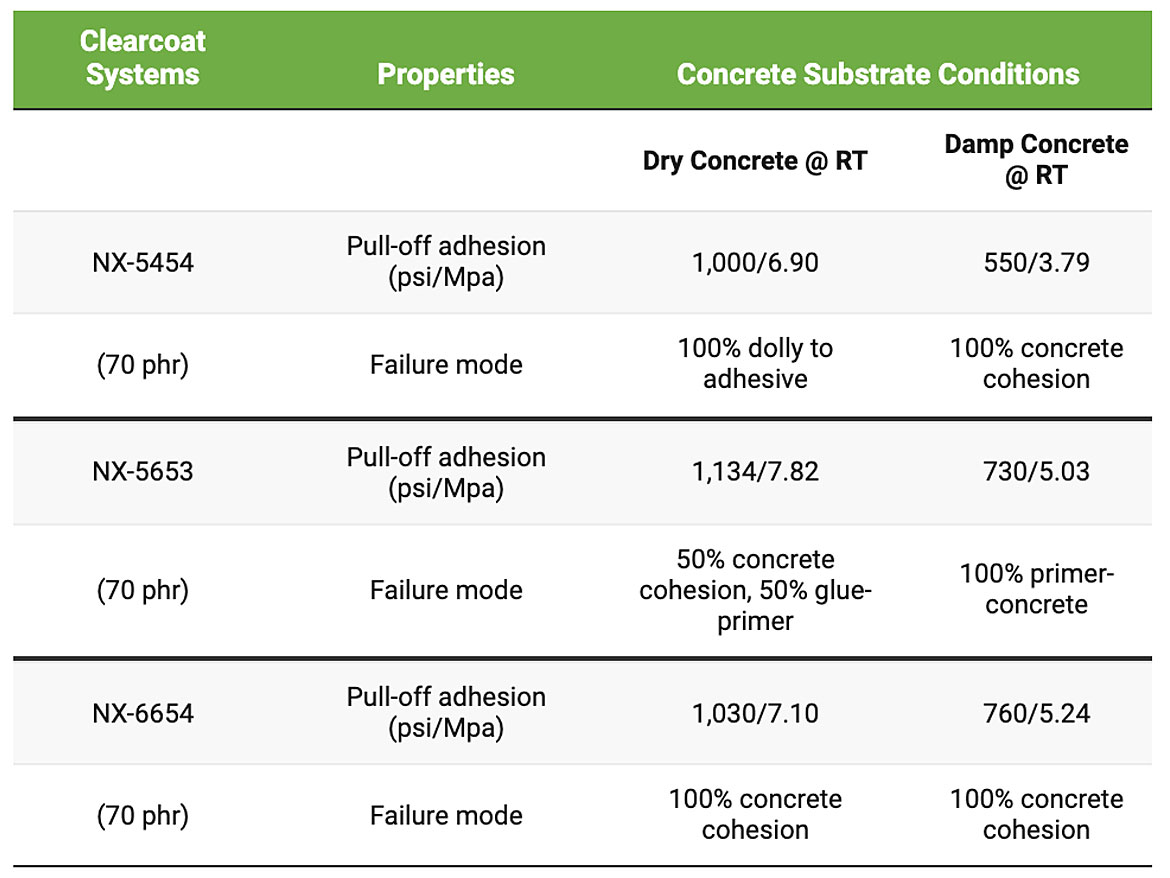
Furthermore, the adhesion property of CNSL-based primers over engine oil contaminated concrete substrate was investigated. Two different types of engine oil, SAE 15W-40 and SAE 5W-20, were poured over concrete surfaces and then spread evenly with paper towels. Once the engine oil was totally absorbed by the concrete, the CNSL-based primers were applied over the oil-contaminated surfaces. Pull-off adhesion tests were conducted after the epoxy primers cured at 15 °C for 6 days. Results listed in Table 4 confirm that CNSL-based epoxy primers give high pull-off adhesion values (>700 psi) even to oil contaminated concrete substrates.
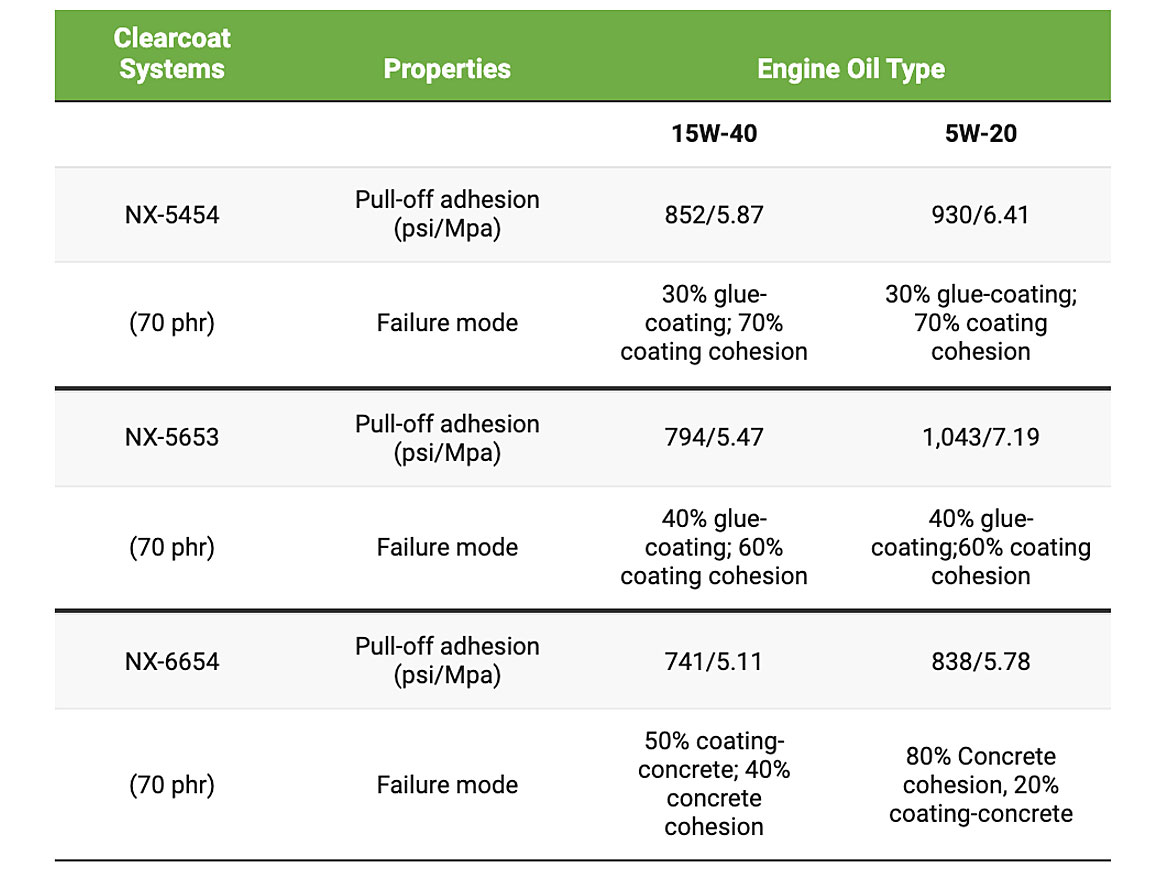
Underwater Cure
Beyond floor coatings, CNSL-based epoxy curing agents can also provide the desired performance in specialty concrete applications such as coatings cured under water (e.g., bridge piles). The video below shows two epoxy systems being applied over a concrete surface that was totally immersed in a 15 °C tap water bath. The systems were based on NX-5653 (on the left) and NX-6654 (on the right) combined with standard liquid epoxy resin, common fillers (silica, talc and wollastonite), and a CNSL-based non-reactive diluent to reduce viscosity. After only 18 hours of cure at 15 °C, a chisel was used to check the adhesion between the coating system and the concrete. It can be observed that the chisel was not able to damage or lift the coating films. This indicates that both epoxy systems cured very well underwater. Additionally, after the concrete block was taken out of the water bath and dried at RT for three days, the pull-off adhesion between the concrete and the NX-5653 and NX-6654 coatings reached 804 psi and 689 psi, respectively, with no coating failure (Figure 5). Those results corroborate that NX-5653 and NX-6654 systems can cure properly underwater and provide good adhesion to the concrete surface. Likewise, NX-5454 exhibited similar good underwater cure performance.
Underwater cure of CNSL-based epoxy primers in 15 ˚C water bath.
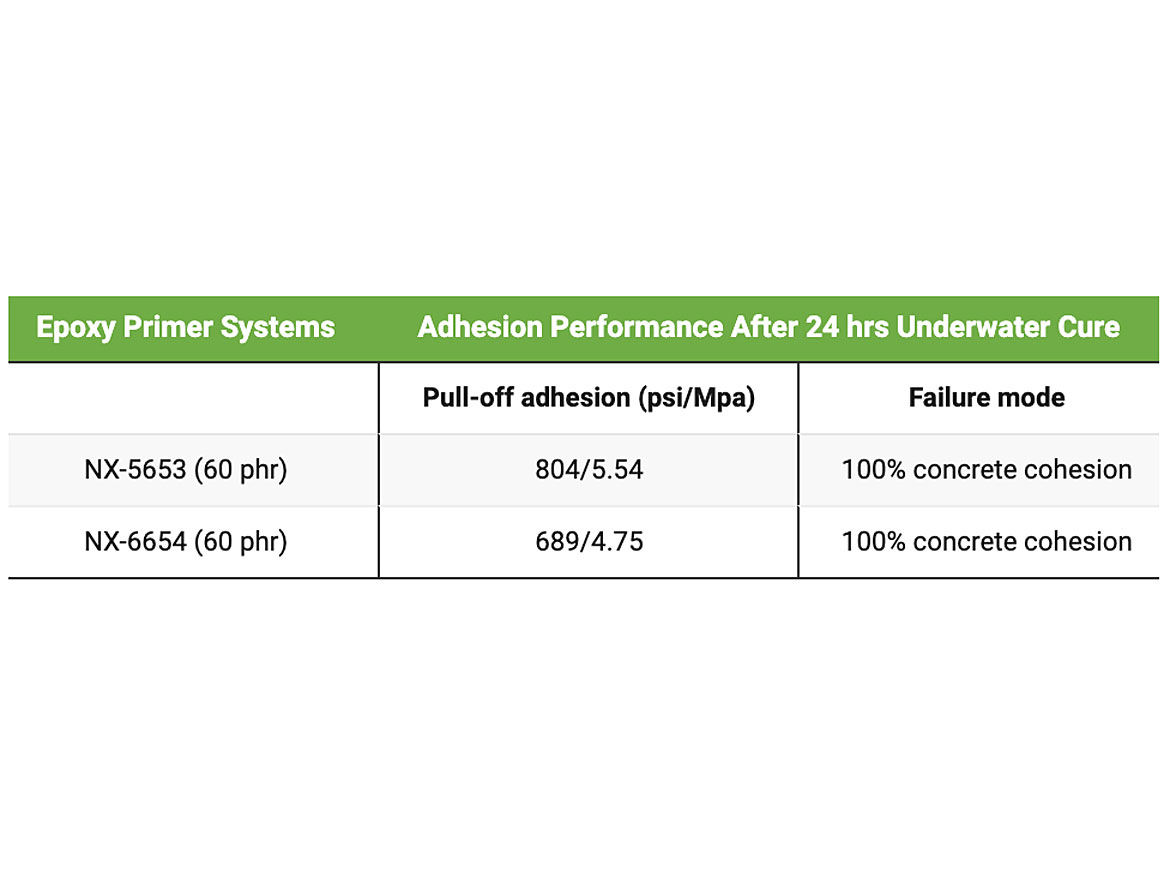
Conclusion
In summary, novel, high bio-content, CNSL-based epoxy curing agents can help formulators achieve zero-VOC floor coatings while also delivering high performances, such as excellent adhesion to poorly prepared concrete, good water resistance and fast return-to-service. Moreover, these curing agents are also suitable for specialty applications that require cure under water.
Acknowledgment
The author would like to show her gratitude to Cardolite R&D chemists, Emre Kinaci, Ph.D. (Bristol, PA, USA), Xiaoping Ding and Chuang Zeng (Zhuhai, Guangdong, China) for the new product development.
For more information, please visit https://www.cardolite.com/.
References
¹ "What is the development impact of concrete?" Cement Trust. 24 October 2010. Archived from the original on 17 September 2012. Retrieved 10 January 2013.
2 Lomonaco, D.; Mele, G.; Mazzetto, S.E. Cashew Nutshell Liquid (CNSL): From An Agro-Industrial Waste to a Sustainable Alternative to Petrochemical Resources, Springer International Publishing AG 2017, P. Anilkumar (ed.), Cashew Nut Shell Liquid.
3 Gedam, P.H.; Sampathkumaran, P.S. Cashew Nut Shell Liquid: Extraction, Chemistry and Applications. Prog Org Coat, (1986) 14:115-157.
4 Gaba, E. Wikimedia Commons user: Sting https://commons.wikimedia.org/wiki/File: Cashew_Brazil_fruit_3.png accessed: Nov 8, 2015 https://commons.wikimedia.org/wiki/File:Cashew_Brazil_nut_cut.jpg accessed: Nov 8, 2015.
5 Dai, Z.; Constantinescu, A.; Dalal, A.; Ford, C. Phenalkamine Multipurpose Epoxy Resin Curing Agents, Cardolite Corporation, Newark, NJ, reprinted from EPI-ERF Conference, Sept. 1994.
Looking for a reprint of this article?
From high-res PDFs to custom plaques, order your copy today!