Water-Based Epoxy Technologies for Metal Coating Applications

Epoxy resins are well known as high-performance materials in various construction and metal coating applications, providing the combined properties of chemical resistance, adhesion, corrosion resistance, mechanical strength and also high flexibility in some cases. Figure 1 illustrates how these favorable properties can be directly related to the resin chemical structure, which is available most commonly in the form of bisphenol A diglycdidyl ether (BADGE). BADGE is formed from the reaction of bisphenol A and epichlorohydrin, which when further reacted with an appropriate curing agent will eventually form a thermoset polymer, with aromatic groups from the bisphenol A component evenly distributed throughout the entire structure. They are one of the best materials available when comparing performance against relative cost, and this has in turn led to epoxies being the substance of choice for use in many high-performance polymeric applications. It is only their disadvantage of poor UV stability that prevents them from having a more dominant position.
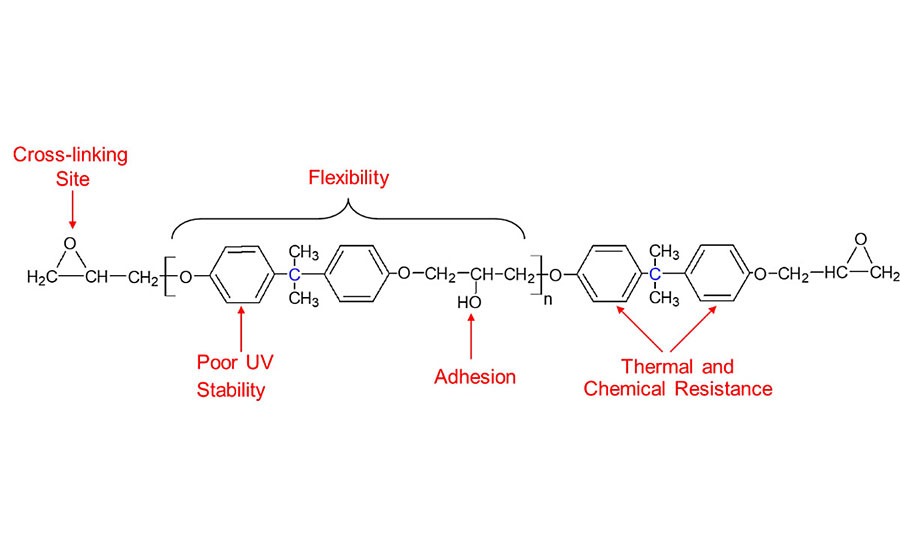
Epoxy resins can be reacted with a range of different curing agents, and a particular resin and curing agent combination is often referred to as a system. Figure 2 shows the two different points of reactivity in a typical resin molecule, namely the end epoxy ring and the side hydroxyl group. Both of these functional groups can react at either ambient or elevated temperature, thus allowing the formulation of both one-pack and two-pack curing systems from the majority of epoxy resins available commercially. For a one-pack system the resin and curing agent can be combined together well in advance of its actual application, as the system will either not react at all or react very slowly at ambient temperature. After application of these one-pack systems, when heat is applied, the curing reactions occur much faster and the final polymer is formed. For a two-pack epoxy system, the resin and curing agent have to be kept apart until just prior to their application, where they are combined together, leading to an initiation of chemical reactions that form the final polymer. Therefore, the applicator has a finite time period after mixing the resin and curing agent to use and apply the material before the growing molecular weight of the system becomes too high that it cannot be used anymore. This time period is commonly referred to as the pot life, and two-pack epoxy systems are often further formulated by adding pigments, fillers, additives, etc. for use in coating and civil applications.
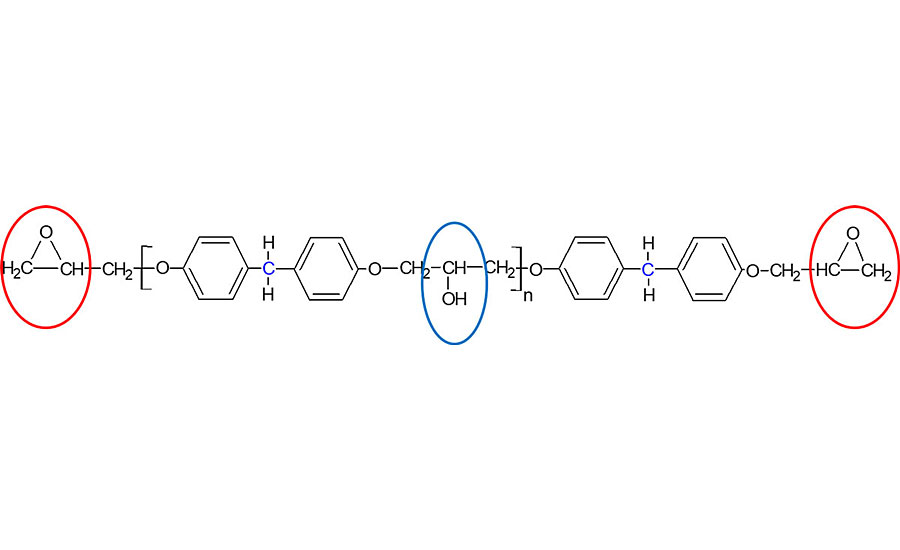
This article is mainly concerned with coating applications of epoxy resins, and by their very nature most polymeric coating applications require the resin be applied as a thin film onto another material substrate. For coatings applied in liquid form, the viscosity has to be relatively low to allow a consistent thin film to be achieved on the substrate surface. In the case of ambient-cured, two-pack epoxy systems, the low viscosity is generally achieved by dissolving the resin and curing agent monomers into a type of solvent, which will evaporate over time after application, allowing a liquid film to form and subsequently be converted into a solid thin film. Figure 3 gives an overview of the main stages that occur during the film-forming mechanism of an applied liquid coating. For liquid epoxy systems, the mixed resin and curing agent, either dissolved or dispersed in a liquid, is applied onto the substrate. The solvent gradually evaporates, forcing the monomers to move closer together. When most of the solvent has left the system, the monomers start to coalesce together as the growing polymer chains start to intertwine with one another. The solvent has completely left the coating, and curing reactions continue in the solid film, forming a high-molecular-weight thermoset polymer.
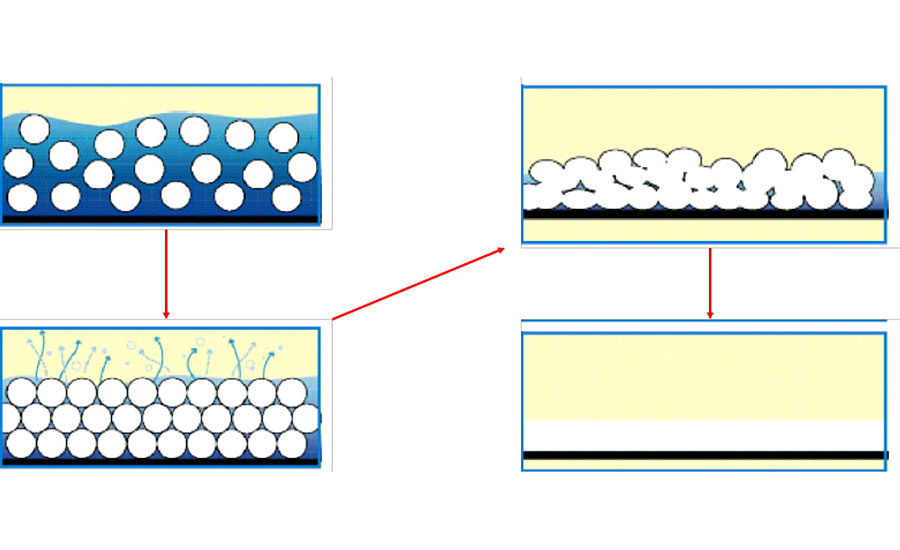
The solvent used during this process is effectively emitted into the atmosphere and is classed as a volatile organic compound (VOC), thus creating a degree of air pollution during the coating process. Increasing environmental concerns over the past decades have resulted in limits being imposed worldwide on the amount of emissions allowed during various industrial and commercial coating applications. Consequently these limits have led many industries to experience a gradual shift away from these traditional solvent-based coatings towards water-based technologies. In its simplest definition, water-based coating technology involves using water as the main carrier medium of a liquid-applied coating instead of an organic solvent, thus effectively reducing the amount of VOCs that are emitted during application, as water is not classed as a VOC. Epoxy resins by their very nature are fundamentally incompatible with water, and this is one aspect of what makes them very useful as protective coatings in particular for corrosion protection. If an organic solvent is replaced with water, careful design of the monomer structure is crucial, be it a curing agent or an epoxy resin, in order to deliver a high-performance coating. The liquid coating has to be delivered in aqueous media, but when fully dried and cured it must give the same high performance as conventional epoxy-based materials. One solution for this is to supply the epoxy resin in emulsion form, having the epoxy resin located within a dispersed phase surround by an aqueous continuous phase. As with most emulsion technologies, the dispersed phase is created using surfactants that form micelles in water above a specific concentration. Since the base epoxy resin is essentially separate from water there is no need to drastically modify its chemical structure, and it exists in essentially the same form as a conventional epoxy resin with its chemical structure unaltered. Moreover, the two-phase nature of aqueous emulsions enables them to exist as relatively low-viscosity liquids.
The use of surfactants, however, does form a ‘weak link’ in the final dried coating in terms of performance. Since surfactants are required to have part of their chemical structure as compatible with water, the presence of a surfactant in the final solid coating will lead to some water sensitivity. Moreover, if the molecule is small it can migrate to the coating surface, leading to increased water sensitivity of the coating as a whole, in addition to affecting inter-coat adhesion. To counteract this effect, the products described in this article employ a non-ionic surfactant at a minimal concentration. Moreover, the surfactant structure contains reactive epoxy groups, allowing the surfactant to cure alongside the base resin and effectively ‘lock’ the surfactant in place, preventing any migration to the coating surface. This is illustrated in Figure 4.
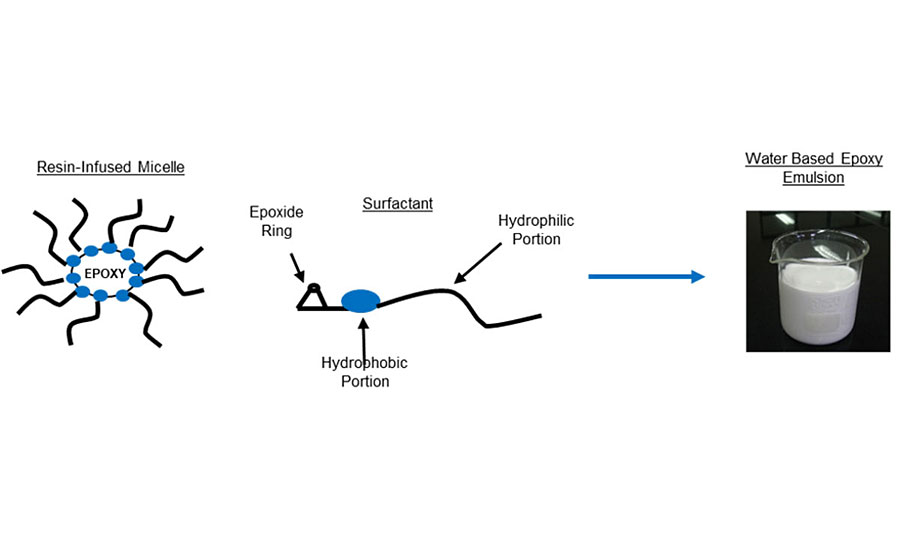
The two-phase nature of emulsions as already explained means that their final viscosity at a fixed solids level remains independent of the molecular weight of the epoxy resin within each micelle. Therefore it is possible to supply a wide range of epoxy resins in emulsion form at relatively high solids level (>50%) but still at a useable viscosity. This is not the case with solvent-based technologies where the solution viscosity increases significantly with the molecular weight of the epoxy resin being solubilized. Two-pack ambient-cured water-based epoxy systems generally exist in two main categories: liquid epoxy resin (100% solids) with water-based curing agent; and water-based epoxy resins with water-based curing agents. When liquid epoxy resin is used, the water-based curing agent serves two main functions. It chemically reacts with the epoxy resin, as a curing agent should, to form the final polymer. However, it also acts like an emulsifier so that when the parts A and B of the system are mixed together, a homogenous emulsion is formed, with the resin and curing agent reacting together within micelles, which will eventually coalesce and form a solid polymer as the water evaporates. When both a water-based epoxy resin and water-based curing agent are used, the curing agent molecules diffuse into the epoxy-containing micelles to allow reaction and creation of the final polymer. In this case it is important that the epoxy micelles are as small as possible so that full cure is achieved in the final coating. In both situations there are two end results possible. The mixed emulsion can either eventually break down, leading to a significant increase in viscosity, or it may stay as a stable emulsion and the mixed viscosity can remain relatively unchanged. The first scenario is described as exhibiting an ‘end of pot life’ indication.
For coating applications, epoxy resins with higher molecular weight and consequently higher epoxy equivalent weight (EEW) are generally preferred to standard liquid epoxy resins. Their increased molecular weight provides many advantages for coating applications, specifically longer pot lives coupled with faster drying times. These differences are illustrated in Figures 5 and 6, which show respectively the pot life and drying time measurements for two water-based epoxy systems cured with liquid epoxy resin (EEW = 190 grams per equivalent) and water-based Type 1 epoxy resin (EEW of 475 grams per equivalent). The curing agent is the same in both systems. The longer pot life observed with the water-based epoxy is very apparent by its very slow viscosity rise, which is almost constant for the first three hours. The liquid epoxy resin on the other hand shows a very rapid increase in viscosity within the first 30-40 min. The water-based epoxy system consequently does not have an end of pot life indication, and the pot life is determined by measuring the gloss retention of the dried coating when applied over time. In this case, Figure 4 clearly shows that the gloss level is maintained for nearly three hours before its starts to drop significantly, and hence the useable pot life of this particular system is three hours.
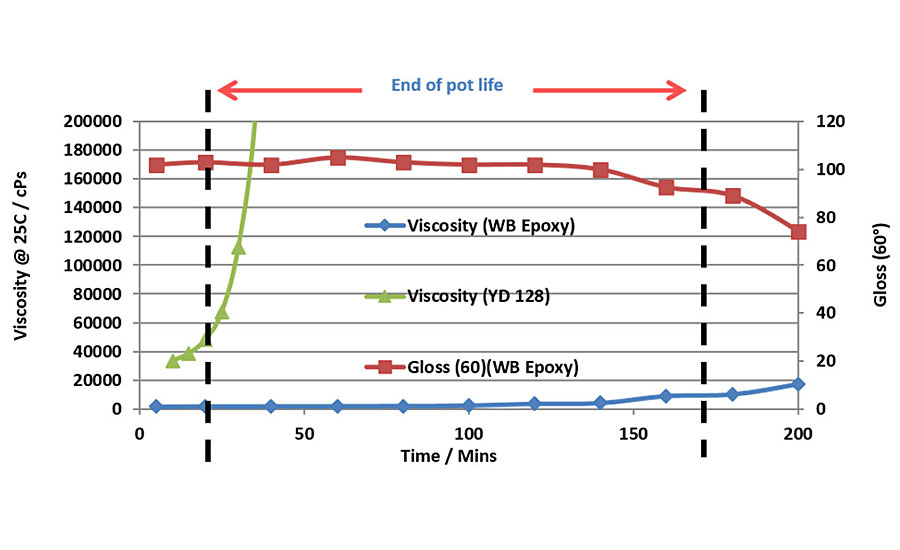
Figure 6 shows the other main advantage of using higher molecular weight epoxy resin in coating applications. When you apply a liquid coating that contains monomers that themselves already have higher molecular weight, then an ultra-high molecular weight polymer is formed much more quickly and the coating has an overall much faster drying time. Figure 6 shows how the water-based epoxy coating dries at less than half of the time of the liquid epoxy resin-based coating, thus providing additional favorable properties, such as fast ‘tack-free’ and shorter overcoat times.

The curing agents used in ambient-cured, two-pack water-based epoxy systems are predominantly based on either aliphatic or cycloaliphatic amines, with high coating performance being heavily influenced by the compatibility between the resin and curing agent. For all two-pack systems, the components should be used in the correct mixing ratio, and a thorough mixing for both parts should be achieved prior to application. Since the A+B mixed emulsion ultimately determines the final performance, the amines used in curing agents are often chemically modified to make them more compatible with epoxy resin. Modification can take several forms, including reacting with fatty acid to produce an amidoamine or polyamidoamine, or pre-reaction with an epoxy resin to form an epoxy-amine adduct. The epoxy section of the adduct thus aids resin compatibility.
With water-based curing agent technology, the design of the epoxy-amine adduct structure gets more complicated since good compatibility is required between the molecule and water, and between the molecule and epoxy resin, which are two opposing forces. Therefore, a high-performing water-based curing agent would have a molecular structure that behaves similar to a surfactant in that it is a block co-polymer consisting of very hydrophilic segments, very hydrophobic segments and some partially hydrophilic/hydrophobic segments to allow the molecule to be compatible with all species. The hydrophilic blocks mainly come from the amines used (AM), while the hydrophobic portions come from pure epoxy used in the adduction (EP). There are many additional di-epoxide species available commercially that can be used in the molecular synthesis to influence a partial hydrophilic interaction (HP) in the end product. A generic description of the overall curing agent molecule is shown in Figure 7.
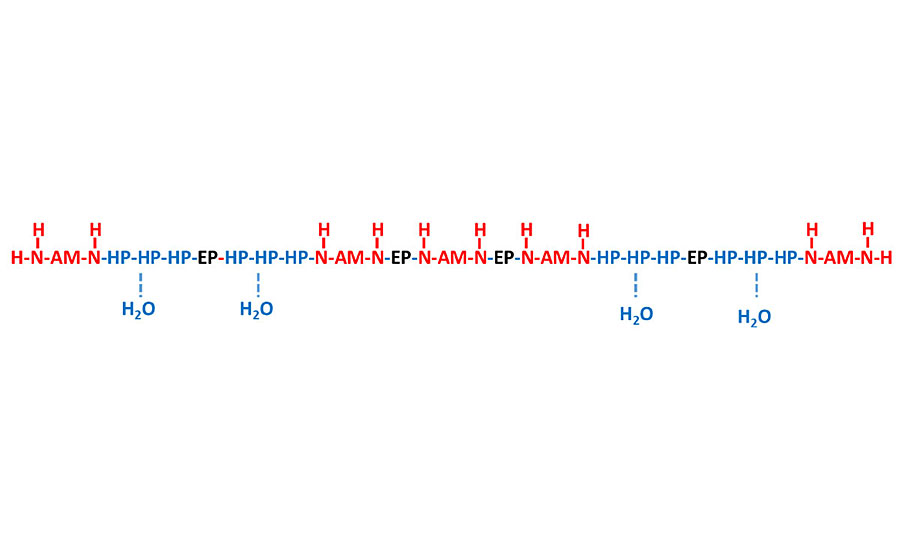
Tables 1a and 1b show the physical specifications of the water-based resin and curing agent products used to make a corrosion protection coating for this article. Cetepox 484 R is a water-based emulsion of Type 1 epoxy resin supplied at 53% solids level in mainly water, plus a small content of methoxy propanol. Being an emulsion, the viscosity of the product is very low at less than 1,500 Centipoise at 25 °C, making it easy to incorporate pigment and fillers or to develop a sprayable water-based coating without having too low a solids level. The mean particle size is also less than 1.1 microns to allow good penetration and through-cure of the curing agent within the epoxy micelles. Epotec THW 4510 is a water-based curing agent based on a relatively high-molecular-weight epoxy-amine adduct. It is supplied in solution form at 60% solids level and contains no added solvent.

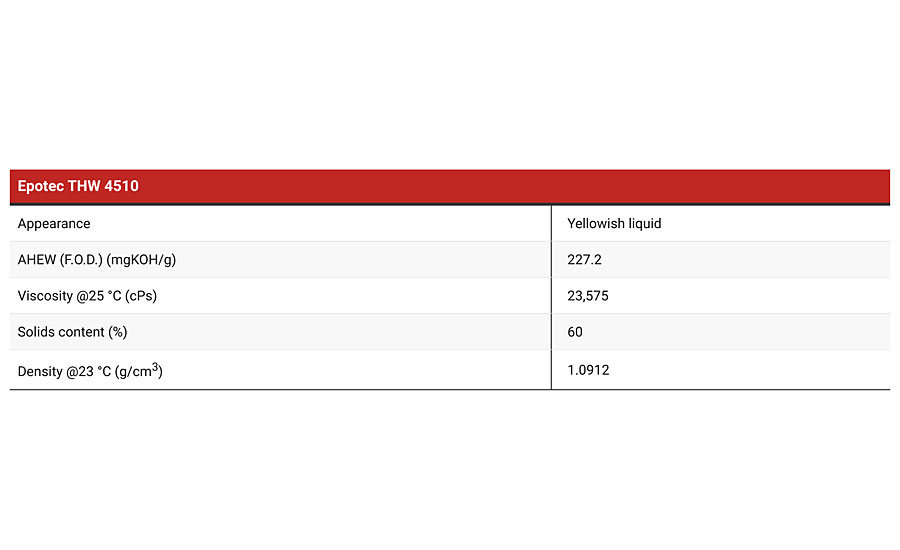
Water-Based Epoxy Coating Development
These water-based epoxy and curing agents are fully compatible when used in combination and employed in a variety of coating applications. The minimal solvent content in both the resin and the curing agent allows the formulation of coatings with a very low VOC level. When the epoxy and curing agent are mixed together, a stable homogenous emulsion is formed, where the curing agent molecules can penetrate the micelles of the epoxy resin emulsion and polymerization reactions commence. The chain extension and crosslinking reactions ultimately form the final thermoset polymer within the micelles, but there is no breakdown of the micelle structure, and hence this system does not have a visible end of pot life. This is illustrated in Figure 8, which shows the viscosity profile over time of the mixed system and is virtually constant over several hours, and since the pot life does not visibly end then the actual useable pot life of the system has to be determined by measuring other coating properties. The growing thermoset polymer will eventually attain a molecular weight high enough so that coalescence is not possible after the liquid emulsion has been applied, resulting in a poor final coating appearance and very poor protective properties. Figure 8 shows the coalescing behavior of the system when applied as a clear film over time after the initial mixing. It is evident from the pictures that the clarity of the film starts to decrease around the four-hour mark, and a cloudiness becomes more evident as the clear film dries. This signals a restriction in coalescence of the coating and thus the end of the usable pot life for this system.
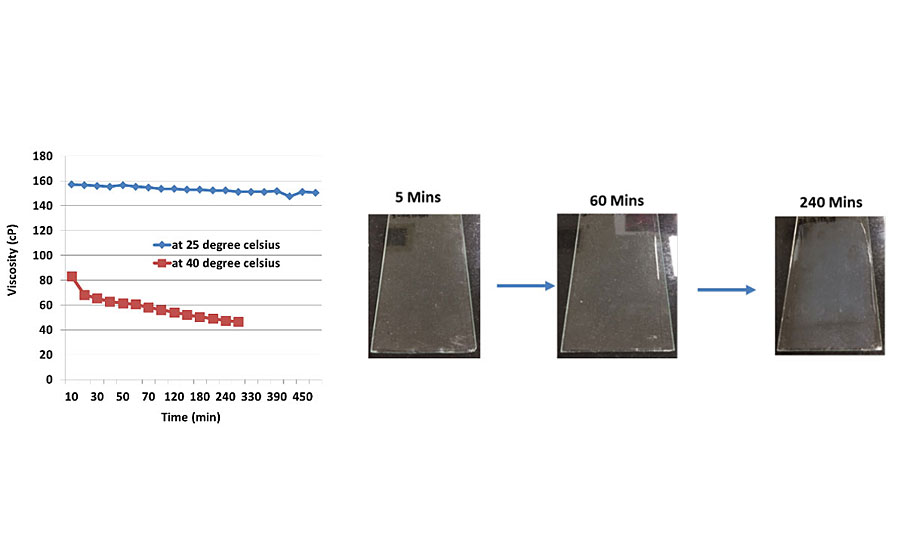
For use as a viable corrosion protection coating, the water-based system based on Cetepox 484 R and Epotec THW 4510 has to be further formulated to give the desired overall performance. This generally involves incorporating pigments and fillers into either the resin or the curing agent component. It is more advantageous to formulate into the resin component since its low viscosity allows the incorporation of many pigments and fillers without the viscosity of this part becoming excessively high. To avoid affecting the emulsion stability of the water-based epoxy by applying excessive shear, the formulated part A is prepared by first making an aqueous pigment dispersion and adding the epoxy as one of the last components. The water-based system is best formulated with a pigment volume content (PVC) in the range 30-35%, and it is typically formulated using zinc phosphate-based anti-corrosive pigments. Appendix A describes the formulation used for generating the performance data described in the remainder of this article. The formulation itself has a pigment volume content of 30% by weight, offers a VOC level of less than 100 grams per liter and provides a range of other favorable coating properties that are described in the table in Appendix B.
Again, for an absolute determination of the useable pot life of this coating formulation, it is necessary to check the overall performance of the coating over time after the initial mixing of Parts A and B. Figure 9 shows the results of one such test, where the adhesion of the fully formulated coating applied onto mild steel panels was measured with time. Strong adhesion to the substrate is just one of the important properties a coating must have if it is to exhibit good protective properties. Figure 9 illustrates the results of a cross-hatch adhesion test following the standard method ISO2409:1992. The figure shows how there is no adhesion loss of coating even after four hours.
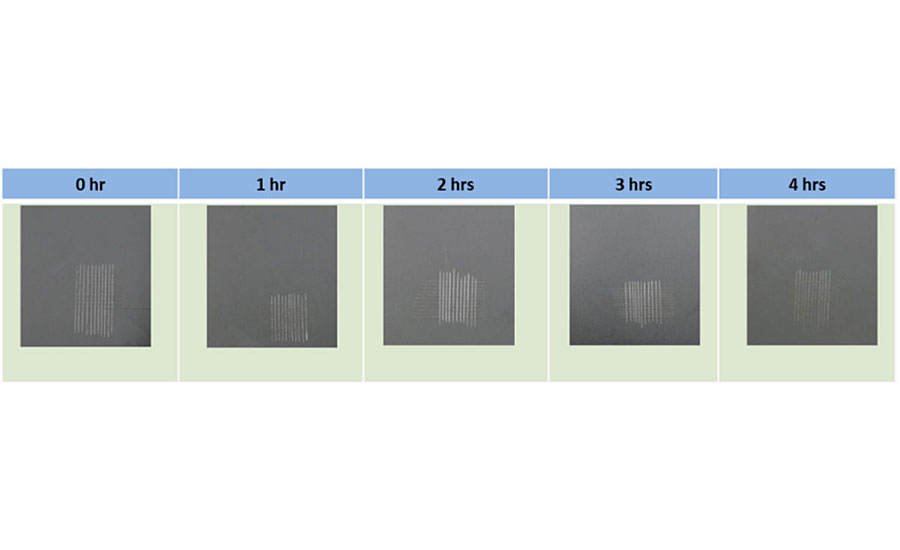
Performance Testing
The main purpose of this type of coating is for corrosion protection of metals, and the performance is typically evaluated with the aid of a salt spray chamber that provides accelerated corrosive conditions for evaluating coated test panels. Figure 10 shows the appearance of mild steel panels coated with the water-based coating described in Appendix A at a dry film thickness of 50 microns. These panels underwent salt spray exposure for 2,000 hours in line with the standards ASTM B117-16 and ISO 9227:2006, and the two pictures show both the fully coated panel after removal from the salt spray chamber (slight clean-up of the surface) and the panel with the coating around the scribe mark deliberately removed. The panels are evaluated after exposure in terms of blisters on the surface of the coating, the creepage of the rusting from the center of the scribe mark and the degree of rusting on the metal surface underneath the coating after it has been removed. Figure 10 shows how the creepage from the center of the scribe line is no greater than 0.5 millimeters in length, there is minimal blistering on the surface of the coating and also on the exposed metal underneath the coating. Adhesion testing after salt spray exposure also shows that no loss of adhesion occurs over time, thus confirming the formulation as a high-performance corrosion protection coating even when applied at relatively low film thickness.
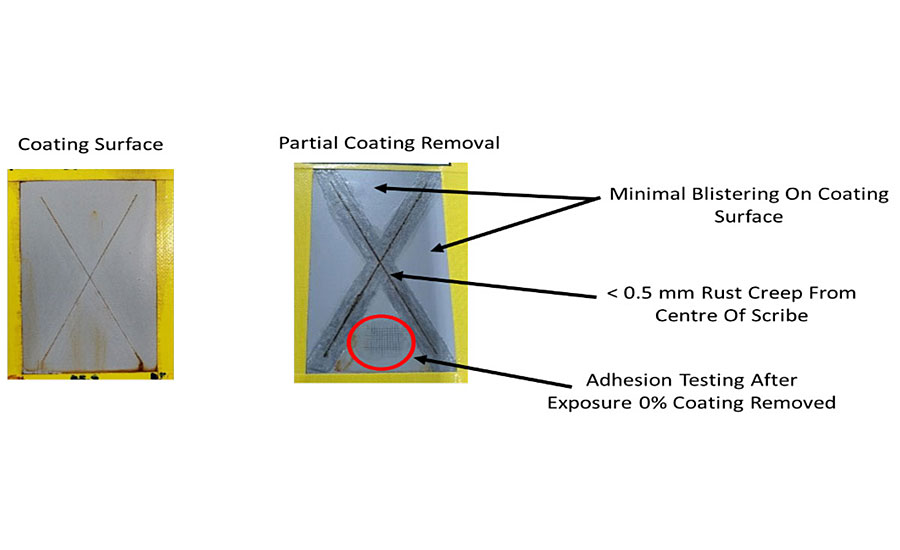
Since water-based corrosion protection coatings are increasingly being used in marine environments such as for the protection of shipping containers, another common performance test is the salt-water resistance test. This involves immersing a coated panel in a 5% sodium chloride aqueous solution. Once removed, the panel is evaluated in a similar fashion to salt spray exposure. Figure 11 shows the data and appearance of the coated panels after 168 hours of salt water immersion. As with the salt spray exposure result, the coating formulation exhibits no blistering, minimal rust creepage from the center of the scribe, and coating adhesion is not affected by the immersion.
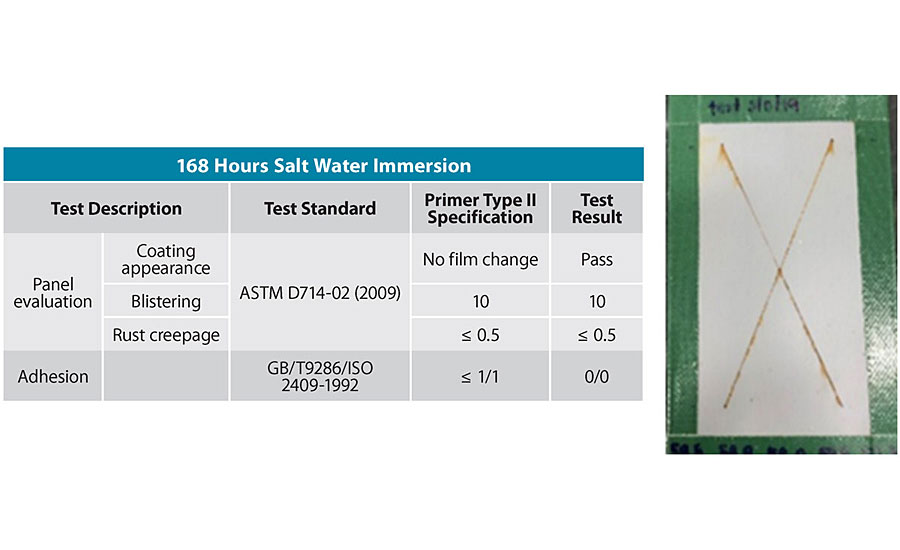
For many years, the main technology for corrosion protection has been two-component solvent-based epoxy coatings. The epoxy portion would typically be based on a Type 1 solid epoxy resin that had been dissolved in solvent, and the hardener portion would typically be polyamidoamine based. Figure 12 compares the coated panel appearance of both technologies when tested for corrosion resistance under the same accelerated conditions. For both panels, blistering on the surface of the coating is completely absent, and the adhesion of both coatings has not been diminished. The length of the rust creepage from the center of the scribed areas on the metal panel is also generally the same, with some localized areas on the solvent-based panel being in excess of 1 mm. The actual formulation for the solvent-based coating is shown in Appendix C. Thus, when considering the overall data it can be concluded that this water-based technology can deliver performance equal to that of standard solvent-based in corrosion protection applications.
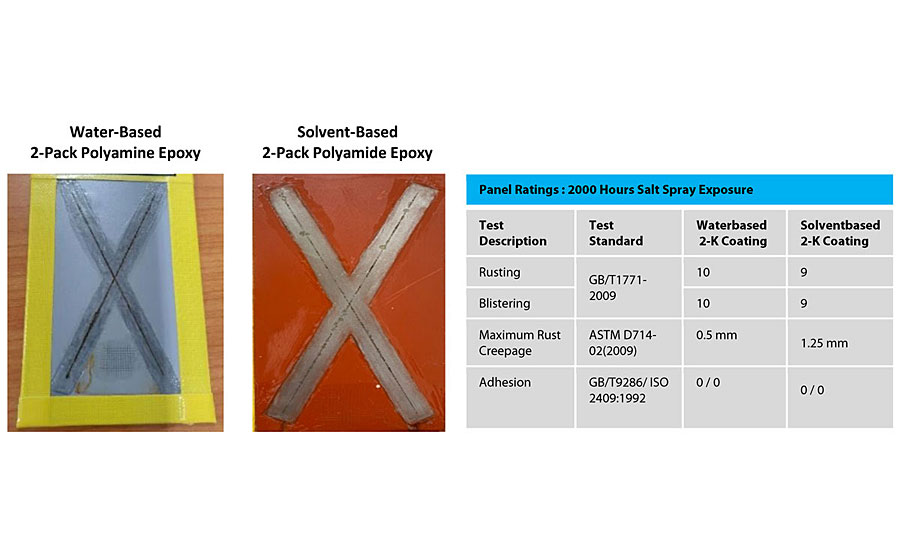
Summary
Water-based epoxy resin and curing agents have been developed that can be used together as a system to provide corrosion protection coatings with low VOC content, less than 100 grams per liter. The epoxy resin is an emulsion with higher molecular weight, which produces coatings with longer pot lives and fast drying times, especially when compared to coatings based on liquid epoxy resins. The resin and curing agent combination does not provide an end of pot life indication but can still be applied up to three hours after the initial mixing as a clear coating and up to four hours as a fully formulated coating without the loss in performance. The system can be formulated with intermediate PVC in the range 30-35% to give high corrosion resistance even at low coating thickness. Salt spray resistance in excess of 2,000 hours is achievable without any detrimental effect to the coating or significant loss of performance. The water-based metal coating was also compared against a typical solvent-based epoxy coating, and no significant difference was observed.
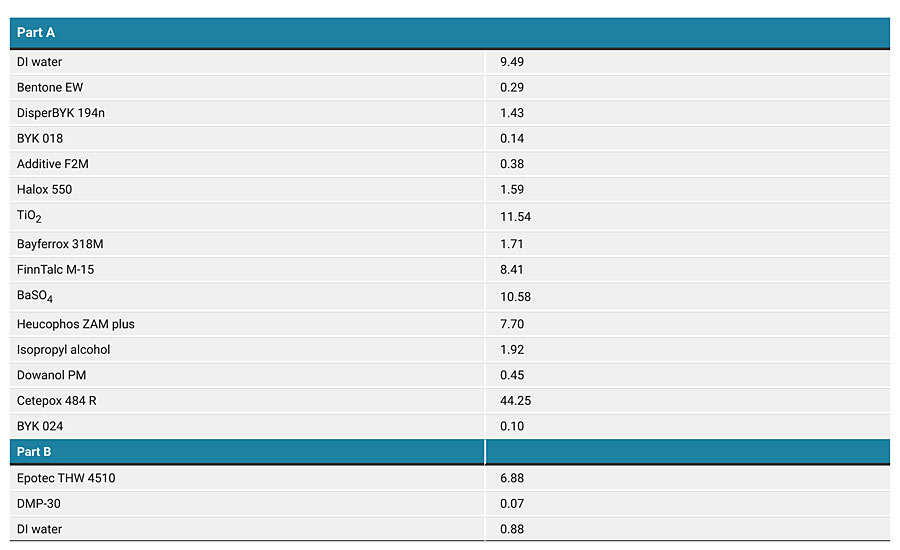
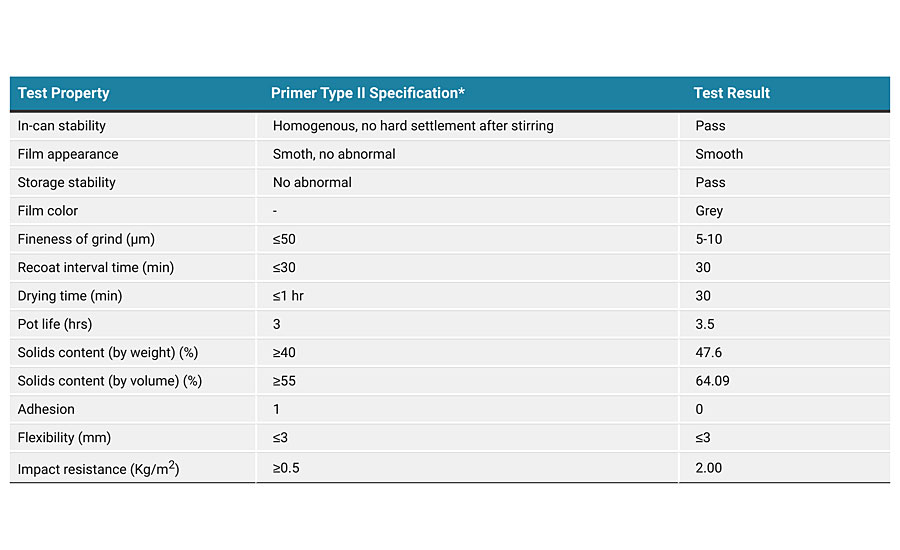
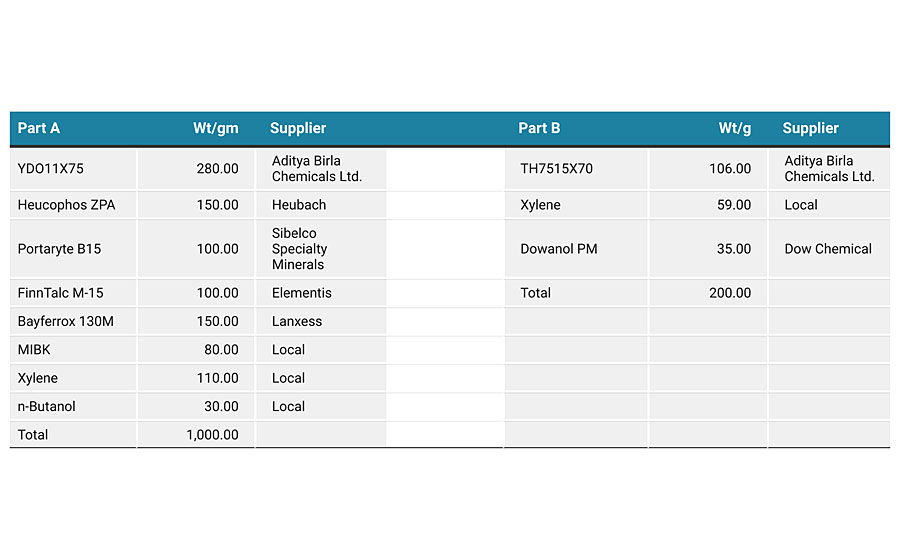
Looking for a reprint of this article?
From high-res PDFs to custom plaques, order your copy today!